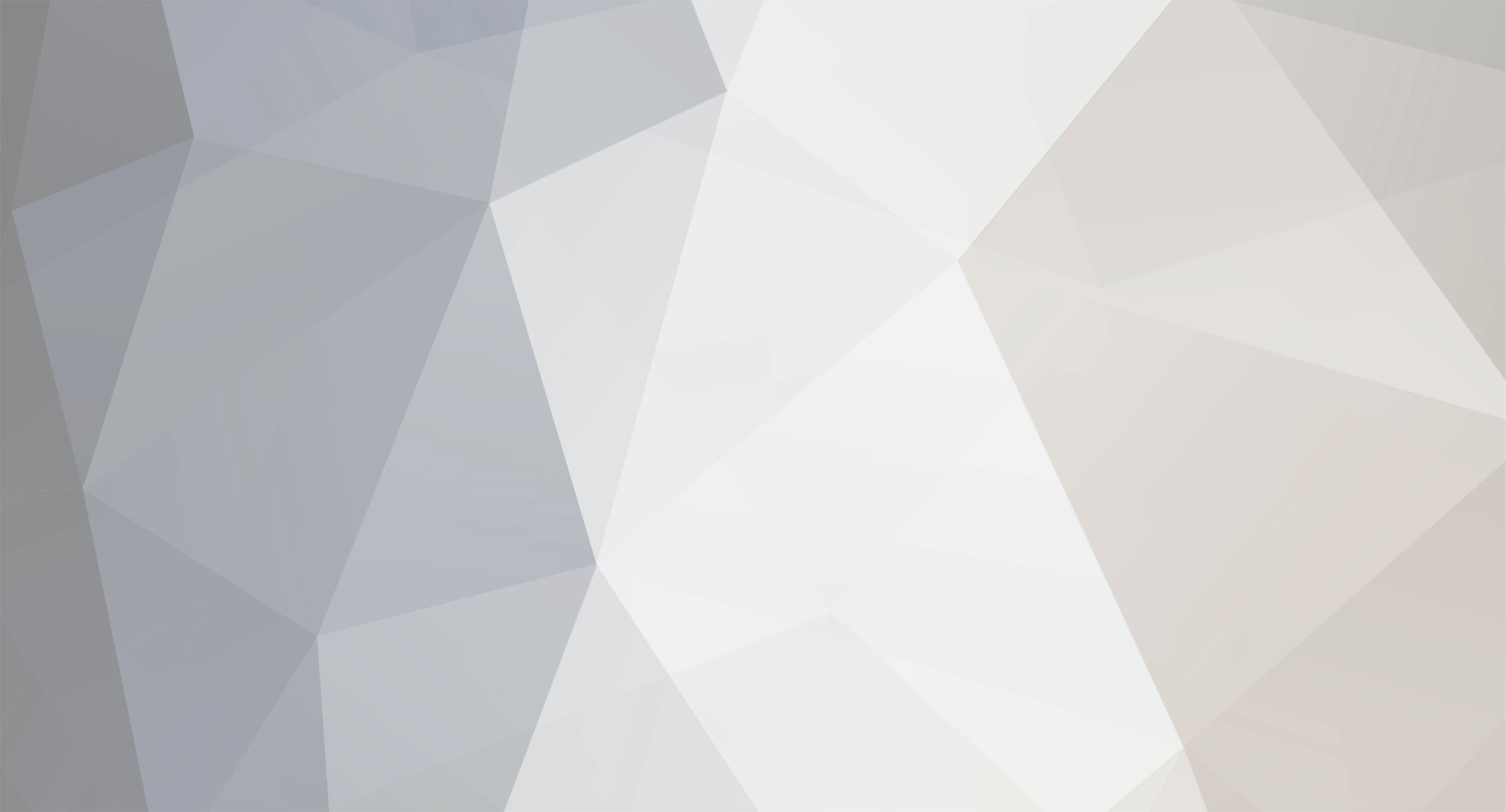
sgt_woulds
Members-
Posts
104 -
Joined
-
Last visited
Recent Profile Visitors
The recent visitors block is disabled and is not being shown to other users.
sgt_woulds's Achievements

Regular Member (4/5)
35
Reputation
-
Also, PIR shrinks over time and when exposed to the high temperatures typical under a roof. Even if by some miracle you get a perfect fit when installed, as it shrinks, you will get thermal bypass. I agree that flexible insulation is better in this situation. Flexible woodfibre would be better still as the decrement delay will help with overheating issues we are likely to experience ever more often. On my retrofit, I used woodfibre between cut rafters (allowing minimum 40mm ventilated airspace) and PIR underneath, fully taped and sealed, and acting as the VCL and airtightness. This was a compromise to meet the U-value requirements and stay within the structural capacity of the existing timbers. Has worked very well through the heatwaves so far, and no sign of PIR shrinkage as it is protected by the woodfibre above.
-
Sorry, I missed your reply... It depends on the specification of the woodfibre sheathing. Some are available with a hydrophobic coating that allows any moisture that gets behind a properly ventilated rainscreen to run off and additional membranes would not be required in most parts of the UK. If you are in an exposed location where rain could force its way into the cavity, or if the rainscreen has less ventilation (due to firestops, or behind a brick or stone skin) then it will require a waterproof breathable membrane fitted, before the battens and rainscreen go on. Ideally, a nail-sealing tape should be used between the battens and the membrane to ensure that no water can run down the wall and find its way into the insulation zone. At least one manufacturer makes a woodfibre board that is pre-bonded with membrane to make this task easier and quicker (although slightly more expensive in material terms, you save on labour costs and install time, and reach a weather-tight stage, sooner) REI60 should be possible with the correct cavity closers and detailing. The aluminium skin would reduce the spread of flame, and woodfibre - although a class E product - smoulders and self-extinguishes (unlike plastic insulations which melt and ignite, spreading fire), so you are unlikely to have a Grenfell situation. The woodfibre manufacturer should be able to advise on this, and it is better to have e-mail evidence from a manufacturer to show building control if needed.
-
3 to 5mm. Just big enough to allow a dropped credit card to disappear - ask me how I know... π But thankfully, easy enough to lift and replace without the homeowner noticing any changes!
-
-
I'd ask the Architect on what basis they specified that build-up? Did they consider moisture at any stage? WUFI assessment? With a non-permeable sheathing board, your internal VCL and sealing would have to be immaculate to prevent damp issues with the frame - that is practically impossible to achieve on site with your average Great British Builder. For my own timber walls, I used a system that allows fully open moisture transport and easy sealing. Uses fewer components, zero membranes, and is less critical on detailing if Bob the Builder is having a bad day or there is a football match they need to watch... π Inside to out: Plasterboard 25mm battens (with woodfibre or hemp flex between to help moderate internal moisture levels) 15mm OSB3 such as Smartply or equivalent with air and moisture tightness. Taped and sealed, this forms both the racking and airtightness in. Easy sealing and hard to damage. TF (I-joist studs for better u-value) with Woodfibre or hemp flexible insulation - mineral wools work, but I like to maximise the decrement delay for future heatwaves T&G Woodfibre sheathing - provides additional airtightness and reduces cold bridging. Breathable render Wood fibre used in a certified system behind a render or plaster system achieves a B-s1,d0 classification for both internal and external use. This is a classification of the render system; depending on which system is used, the manufacturer can provide the relevant data. Approved document B asks for external cladding within 1m of the boundary to be Euroclass B, so rendered woodfibre is fine as long as the height of the building does not exceed 11m. If the aluminium cladding is a must, this could be used over the woodfibre (without render, but with additional breathable membrane), but you'll need to speak to the woodfibre manufacturers to confirm the build-up for ventilation and fire rating.
-
I'll bow to your knowledge with suitable evidence. PU resins (at least those I've had experience with in industrial cement repairs) generally contain solvents to liquify them to allow pouring and shaping. The solvents off-gas as it hardens. Adding warmth generally speeds up this process. Do the resins used in modern flooring use a different process?
-
I agree, using SIPs was the worst decision I ever made! If I could do it again, I would use Kithurst NIPPS or Ecocon panels or other similar products, that not have nasty PIR and have better structural flexibility than PU SIPs. Also better for the environment and internal healthy air. Also, consider accoustics - SIPs are awful for noises resonating through the drum-like skins. If you live under a flight path you'll regret SIPs. Also consider decrement delay - SIPs are good at keeping internal heat in, but are rubbish at keeping external heat out. I used woodfibre externally to counter this to some extent, but a build-up with decrement delay is probably going to be more important than ultimate u-values for the short winter months in the coming decades. MVHR - great, but expensive for what it is. Best with passiv house levels of airtightness. If you are self-building, you should always aim for Passivhouse, even if you don't plan to have it certified. Pick your builders and specifiers well to achieve this. UFH - wet underfloor any day. But if my house was passivhouse, it probably wouldn't need it except in bathrooms where it works a treat I wouldn't have PU resin in any house that I intended to breath in. Too many VoCs - especially when heated by UFH.
-
Lime only mortar? (i.e. no cement)
sgt_woulds replied to Gibdog's topic in Bricklaying, Blockwork & Mortar
No, just stating a known fact π I may have been getting the wrong end of the stick, but I felt the inference from Andehh's comment was that TF and rubble trenches were inferior. I not stating that such a building would definitely last for thousands of years, merely that it could, based on extant evidence. As could any structure built with care, and with proper design and maintenance. Not something we can apply to most mass housebuilder efforts, nor the ego-boosting glass and concrete towers littering most major cities. I suspect most of these will be torn down or require a substantial rebuild in the next 50 years. -
Lime only mortar? (i.e. no cement)
sgt_woulds replied to Gibdog's topic in Bricklaying, Blockwork & Mortar
True, and the oldest man-made structures on earth are made of mud bricks or cob on rubble trench foundations π There are also plenty of timber frame buildings in this country dating back more than 800 years. Combining the best features of all of these structures that will last the test of time is the ideal, as long-term savings in running costs and maintenance can then ameliorate any initial up-front carbon costs. So-called 'energy-efficient' monstrosities built using tonnes of concrete and bricks, but with a practical life measured in decades, is where we are at today, unfortunately. At least as a self-builder, you have the chance to build something better. Put your name on a little commemorative brick like the Victorians did, and someone can praise your efforts in 100 years... -
Lime only mortar? (i.e. no cement)
sgt_woulds replied to Gibdog's topic in Bricklaying, Blockwork & Mortar
If you really want to save upfront carbon, then changing to natural stone will save much more than the mortar alone - and it will look lovely as shown above. Changing to engineered timber rather than sawn will save more - (less timber section required for the same strength, and more of the tree can be used for structural components versus traditional sawn timber). The smaller cross-section allows more insulation and reduces cold bridging as a useful side effect. This works well with a woodfibre external sheathing board and flexible insulation between the studs - hemp flex for preference to reduce upfront carbon even more. TF can work well with a brick skin as long as you allow adequate ventilation and effective protection for the insulation. Probably the best area to save UFC is in the foundations. These don't need to be concrete - a rubble trench foundation is as green as it gets and is perfectly acceptable to building control with a structural engineer's sign-off. As a plus, it is the quickest foundation type to make, and also act like a French drain to keep your walls bone dry. -
Not necessarily large sections! Some, like 'We Build Eco' provide pre-cut and numbered timbers to allow swift build on sites with limited access for lorries/cranes. Essentially a rapid and accurate stick build with very tight tolerances. With or without all insulation and finishing boards included. House 'kit' content will vary according to manufacturer - most end with the basic shell ready for fitting out, but some include all items required for finish (e.g. Huf Haus) Essentially one step down from pre-fab
-
I briefly worked in a car insurance call centre. The line managers' commissions were based on the value of our sales so were always pushing us to upsell unnecessary extras. In most cases that involved screaming and spitting at those members of the team they could get away with, and generally being as objectionable as they could be to the rest of us without actually expecting a knuckle sandwich. The entire call staff quit on the same day, just after we got our payslips. Would have been one of my best days ever - a real 'self-respect' moment - but one of the scumbags sexually assaulted one of the girls after she went to collect something from the toilets. I was in the pub with the team when she came in crying. I never met any of them again, but I heard later week that some of the guys had tracked the scumbag down and 'sorted him out'. They all got done for GBH but he was never convicted as the poor lass was too scared of him.
-
The research evidence on security alarms
sgt_woulds replied to Adsibob's topic in Networks, AV, Security & Automation
But back to the OP's question: Alongside the alarm you should really consider a smokescreen system. If they can't see it they cant steal it -
The research evidence on security alarms
sgt_woulds replied to Adsibob's topic in Networks, AV, Security & Automation
Personally, I think introducing a little public shame back into society might work wonders - bring back the stocks and televise the rotten tomato throwing. There is so much open lawlessness on the streets we could never throw enough people in prison to curb it. There are gangs marauding pavements on stolen mopeds and people openly shooting up on the bench outside our local police training station. As the police pull out in their vehicles they deliberately look the other way. The decline in morals and public order is shocking. The increasing apathy in policing is even more so.