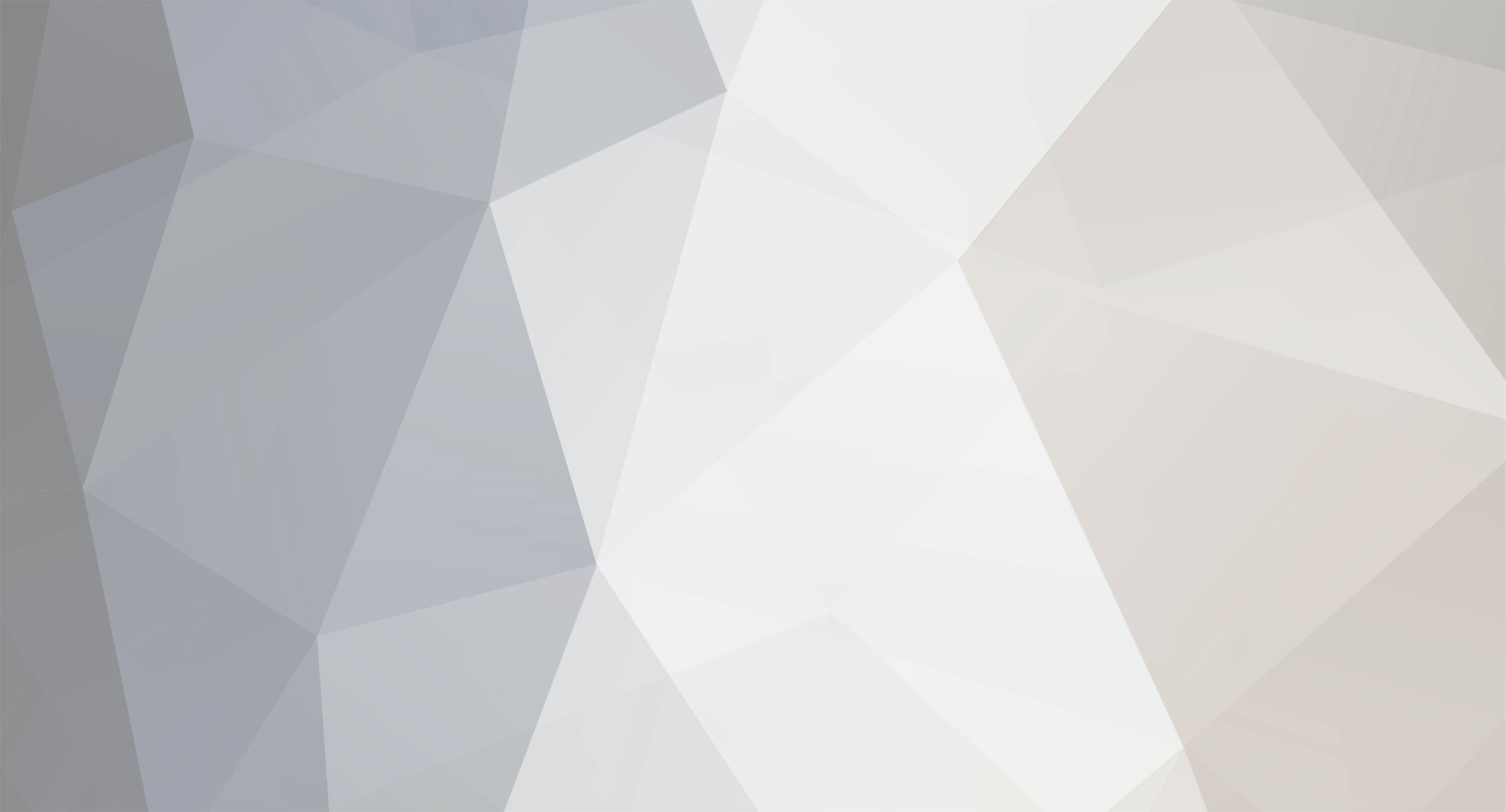
Bancroft
Members-
Posts
118 -
Joined
-
Last visited
Recent Profile Visitors
The recent visitors block is disabled and is not being shown to other users.
Bancroft's Achievements

Regular Member (4/5)
53
Reputation
-
Wet plaster or dot and dab for my self build?
Bancroft replied to Berkshire_selfbuild's topic in Plastering & Rendering
Excellent marketing! -
I'm still investigating this and haven't yet fitted so take read this with caution. Condensation drains? I think the basic answer is 'yes'. However, if thought about early enough in the planning process it shouldn't be too much of an issue. I'm planning on 4-5 fan coil heads in a single storey building and (on paper) it doesn't seem too torturous to find ways to locate the fan coil where drains will be easy to install. For example, we have two bedrooms with a bathroom in the middle - easy to mount the units on the bathroom/bedroom wall and take the drain through the wall into the bathroom plumbing. Ditto near the kitchen etc. Also, I think some units that can be ceiling mounted can pump condensate uphill to then flow down into the final drain. This means easier installation between floors or routing through loft spaces.
-
MVHR and cooling
Bancroft replied to flanagaj's topic in Mechanical Ventilation with Heat Recovery (MVHR)
After going around this circle many times over the last year this is how I'm planning on solving the issue. -
We have had a nightmare with the Conditions placed on us following approval of our planning application. So much so that I'm putting in a formal complaint about how/why they were imposed in the first place and how they have subsequently been staffed by the planning office. Too late for us now, but for anyone who is in the early stages of planning approval/discharging of Conditions, it might be worth acquainting yourself with the government guidelines on planning conditions starting with https://www.gov.uk/guidance/use-of-planning-conditions If going through this process again, the first thing I would do on being confronted with any Conditions from the planning department would be to go to that page and check each one against the six tests and other guidance shown. Armed with that information I would then go back and confront the planners. I have a strong feeling that most would crumble at the thought of being asked to explain their actions. That could save you a lot of time, money and frustration.
-
I think if we get to that stage, my wife will be putting me in the ground, not a spade!
-
Somewhat depressingly, Facebook has just sent me one of those "on this day..." memories in the hope that you'll share it again on the platform. It was this day last year that we finally got the letter saying we had been granted planning permission to build our new house. (That was after applying for planning permission the previous December but let's gloss over that...). Since then, the only physical proof we have to show as 'progress' are three lumps of earth in the garden where soil inspections were done. But, there is some good(ish) news: Only one of the thirteen conditions remains to be discharged The new architect is almost ready to submit the Section 73 notice to update/amend some changes made to the design. Hopefully, the planning department won't take another six months to approve those. I think this stage of 'building' your own home is one that is often glossed over but it does help to put into context why planners allow you three years from approval to commence the build... I've found it quite difficult to determine what I should be doing personally during this period, especially now that I'm essentially retired. When we initially got permission to build I went out at full speed and started talking to builders, organising site insurance, writing letters regarding CIL etc etc. But then the reality of discharging Conditions came in, along with a seemingly never-ending series of reports and inspections to be arranged and paid for. I took a pause, throttled back in preparation for the long haul, and put my frustrations to one side. And, although physical progress might have stuttered, I have been able to use places like this forum to increase my overall knowledge of some of the more obscure (but no less important) corners of self-building. I'm grateful to both this site and the individual contributors who have gone before and highlighted their experiences. So, onwards and (hopefully) upwards as we enter the second year of holding planning approval.
-
Is this a complete new build or are you just looking at re-hashing the internals of an existing building and are limited by the external wall size/shape? Is the garage an absolute necessity or can it be used as part of the re-design? Finally, I presume the garden is at the top of this drawing, next to the conservatory?
-
Battery Storage - Lifespan and Replacement
Bancroft replied to marmott2334's topic in Energy Storage
I'm certain I saw the ad as it appeared in the magazine month after month. But, I will acknowledge that my TB and GB might have got mixed up over time (memory not what it used to be - if you'll pardon the pun). -
Battery Storage - Lifespan and Replacement
Bancroft replied to marmott2334's topic in Energy Storage
Back in the mid-eighties, I saw an advert for a 1Tb hard drive for a computer. I remeber thinking two thoughts: Who on earth would need that amount of data on a hard drive, and Who would pay £6000 for a hard drive? -
If you're planning a modern, well-insulated and ventilated house, the likelihood of wanting/needing to open an upper floor window are pretty slim so, personally, I would see this limitation as being of minor importance. I'm actively trying to make more windows fixed closed to stop my wife from randomly opening them and ruining the MVHR efficiency!
-
I've heard/read of people having issues getting buildings insurance for self builds that are fully clad in timber. Most of the posts I've seen on this site are a few years old and so quite soon after Grenfell when the insurance market was still in flux. We're planning on building a 210sq m single storey house in ICF with a metal seamed roof. At the moment we're planning on 100% timber cladding but I am considering the option of about 40-50% seamed metal cladding on the rear of the building instead for ease of getting insurance. Has anyone got any recent experience of how insurance companies are reacting to buildings totally clad in timber?
-
And suffer the abuse of everyone telling you you're a Festool Fan Boy! I take a pragmatic approach to tools - generally speaking, the greater the accuracy required and the closer the tool is used to the final/finished product, the more I spend on it. So I have everything from Festool down to Machine Mart Clarke tools.
-
Battery Storage - Lifespan and Replacement
Bancroft replied to marmott2334's topic in Energy Storage
Car EV batteries are generally said to decay by 1% per year so I would have thought that would be a good figure to start with. Recycling? I asked this question to a friend who is in the EV car world and he said yes. There is a cascade of ways they get re-used (eg they go from car to static storage, then to less important storage facilities etc until finally broken apart for parts) and I imagine that the options for re-use and re-cycling is only going to grow. Costs generally seem to be coming down - at the same time as efficiency is going up. So the chances are in the future you'll probably pay the same cost but have something 2-3 times more efficient. -
Starting a business helping Self-Builders, advice?
Bancroft replied to LDNRennovation's topic in Surveyors & Architects
From my limited experience I think this could be a key area for you to focus on. A few wider thoughts: You will need to be clear about your niche. How are you going to differentiate yourself from a planning consultant or normal architect? Most new self-builders won't know what they don't know. Human nature makes us fell safer doing what we see others have done so they will naturally gravitate to the norm - ie an architectural firm. Perhaps a survey of Buildhub members to find out their experiences of their journey and where they felt they would have benefitted from some independent help. Have you considered working alongside an architectural firm (or firms) as their self build expert? Taking Mike's point from above you might be able to create a symbiotic relationship with a company that works for both of you. In my experience, and reading of other's experiences, architects get very excited about the design stage but interest drops at an alarming rate as the project approaches the point where a spade hits the ground. You could work alongside them in the early stages then take over as the project develops. In practical terms, although you say only 2-3 clients at any one time, will that give you sufficient income and how are you going to be able to service them? The chances are they will be spread across the UK so you will need to factor in travel and time away which will eat into profits/make you more expensive. Regardless of the route you take, running a small business is as much (if not more...) about marketing and sales - especially in the early years until you have built up a reputation. With a business such as the one you propose you will need to maintain that marketing/sales effort because the likelihood is 99% of your clients will not be repeat customers so you will always be searching out new opportunities. (An alliance with an architect(s) as suggested above might help this issue). Apologies if that all sounds a bit negative but I've worked with a lot of embryonic businesses and these are just some of the realities. Despite the negativity/realism I do like your idea and think that if you can crack the niche and find a simple, powerful way to market to your ideal clients this could be a really good business idea.