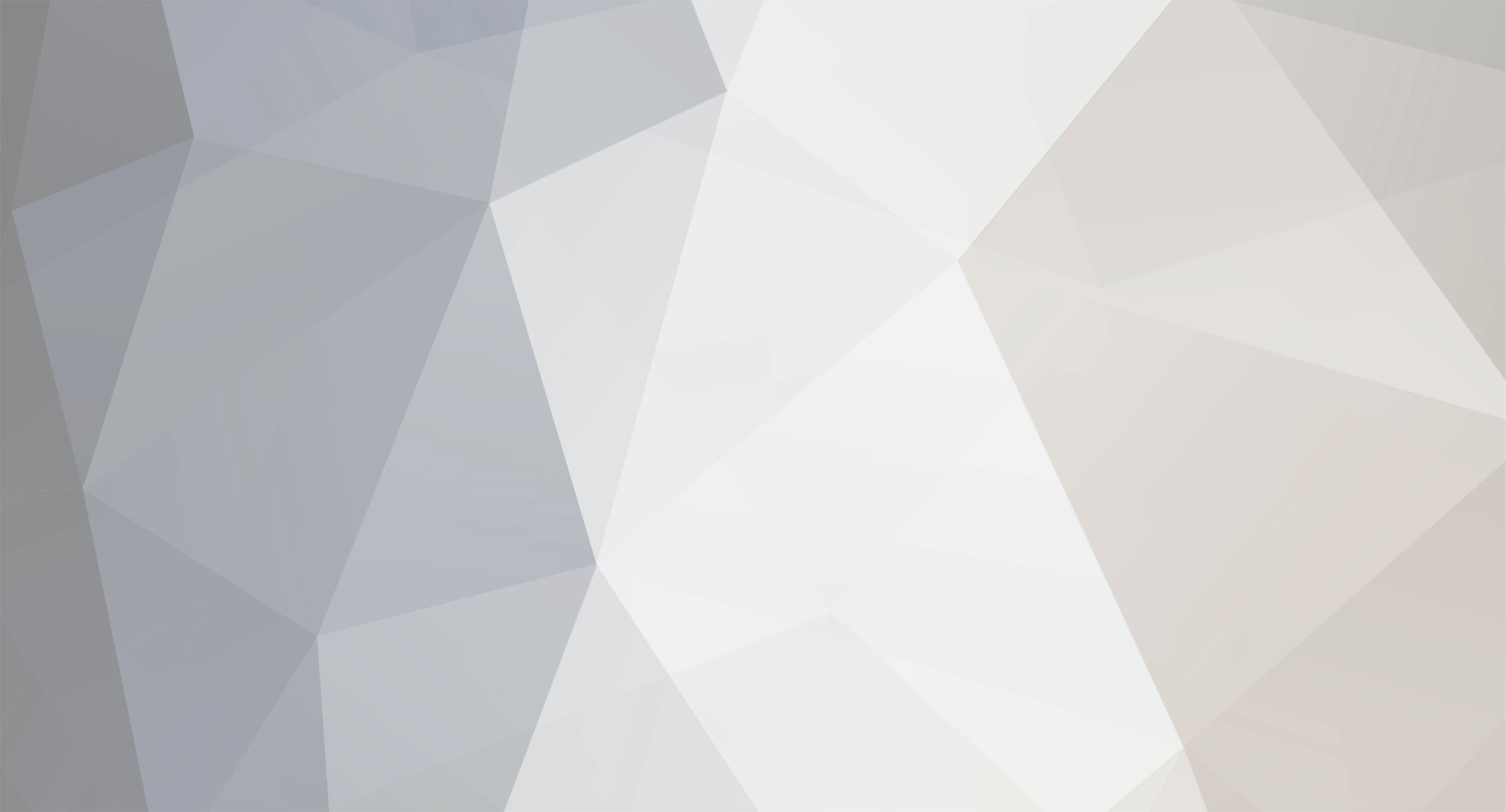
Brendan
Members-
Posts
36 -
Joined
-
Last visited
Everything posted by Brendan
-
No idea. I’m sure they would say they did all of this, and they might have done. They wouldn’t have any proof, I imagine. When I asked what preparation they had made in the stud walls for wall-hung basin/vanity units, they said they couldn’t remember. So I now have floor-standing units instead. The plumber was one of the main reasons we parted company, mainly because it became evident that the ASHP system had not been designed before installation and wasn’t correctly specified in several respects. They are probably technically competent at plumbing but I would have to learn all about plumbing to be certain (in the same way that I had to learn about central heating and ASHP system design to understand how badly they had approached this aspect of the work).
-
It is a completely new bathroom in a supposedly Enerphit standard retro fit renovation and extension. All of the bathrooms are in the new timber frame extension. The photo shows what is now behind the boxed in section.
-
Can you (or anyone else) tell me where to find this bit of the regs? I will happily get the builders (with whom I have now parted company for various reasons) to come back and sort it out at their expense and to my satisfaction if this is a mandatory requirement.
-
I have completed 2nd fix plumbing but now noticed there is a smell (soapy poo, like the smell from the local sewage treatment facility) in my downstairs wc/shower room. It is the same smell that came out of the waste pipes before they were connected up. The smell is very mild unless the toilet is flushed, thereafter it is a lot stronger. I have checked that all the traps (wc, shower, basin) contain water. There are no wet patches or other obvious signs of leaking waste pipes. The WC waste turns 90 degrees at the back of the toilet into a boxed-in section which contains an AAV. The easiest place for any smells to emerge from this cavity is behind the WC, which is where the smell is strongest. The boxed in section is tiled and would be very disruptive to remove, so I wouldn’t want to do this unless I was certain the AAV was stuck/faulty. Is there another likely cause of this smell and any easy things I can check first? I thought about buying a cheap gas detector, would this be any use?
-
Baserail and balustrades with 180 degree return
Brendan replied to Brendan's topic in General Joinery
I think I will probably clad this side with ply as well, then fix a handrail between the newel posts somehow. -
Baserail and balustrades with 180 degree return
Brendan replied to Brendan's topic in General Joinery
It’s open on both sides. There will be vertical ply floor to ceiling on the ground floor that side, 100mm wide spaced at 25mm gaps. -
Baserail and balustrades with 180 degree return
Brendan replied to Brendan's topic in General Joinery
I’ve just realised the handrail is also going to interfere with the landing in this setup. I’m going to have to think of something else, aren’t I? -
My staircase has a 180 degree return onto the landing. This means that the string on which I want to mount the baserail is tight to the landing near the top. It is the same on both sides. Is it ok to trim down the baserail and balusters for this section, or do I need to come up with another solution? Cost is an issue, so I am hoping to use square profile pine for the staircase and landing.
-
Anyway, I think I might have got round the problem by swapping the showers between the en-suite and the main bathroom. The fitting for the other shower is not as tight around the pipe and I think that the end where the compression olive will sit is round so should seal properly. We shall see... (For info the very tight fitting was a Bristan shower fitting, the looser one from Mira).
-
My arse cheek, not my rectum.
-
The wall pipe for my basin to attach to is around 20cm to the right and 20cm down from the outlet from the sink hole waste fitting. I am therefore going to have to go back, right and down (not necessarily in that order, but definitely back first), from the bottle trap to reach this. Does it matter what order this happens in?
-
Unfortunately my arse met the unnecessarily long copper pipe protruding from the wall for the shower hot feed and bent it (probably about a 20 degree bend). So the pipe is now kinked. The bathroom is already tiled. If I'm lucky I might be able to pull the pipe out far enough to cut behind the kink and then solder on a new section - but the pipe is only meant to protrude by 21mm from the finished wall surface and needs to be narrow enough to go through the close-fitting valve that has a compression fitting to attach. Is there any chance I can un-kink this pipe, or is it likely to be removing the shower screen, taking out a tile and soldering a new bit of pipe on further back into the wall cavity?
-
The shower is already tiled, so in the end I have opened the wall from the other side. They had installed a sheet of OSB (probably 18mm) with some extra noggins. I’ve taken the opportunity to add another 18mm ply securely fixed behind the OSB. The specialist disability bathroom sites I found generally recommend 36mm to fix a seat into. I could have just bought a floor standing seat, but I wanted something discreet that would fold away when not needed.
-
It’s a shame they can’t confirm whether they’ve done any preparation for the shower seat that needs to support the weight of a person. Something that we talked about several times.
-
I’ve been sent this photo by the builder. Behind the Celotex is a layer of OSB, then the timber frame with further Celotex in between the studs. I assume these panels of OSB are fixed through the Celotex and into the next layer of OSB. I’m not convinced that’s a particularly sturdy mounting for a wall hung vanity unit. Any comments?
-
Thanks.
-
The wall is insulated so it's difficult to see much - I tried poking my inspection camera in around the pipework, but all I could see was insulation. I don't think there are any sockets on this wall on the other side - which is an as yet undecorated room (bare plaster).
-
Your favourite cheap gloves for painting (and for gardening)?
Brendan replied to Adsibob's topic in Tools & Equipment
I find I can mostly grab stuff at will without worrying about it. Backs of the hands and arms are still at risk, however! -
Your favourite cheap gloves for painting (and for gardening)?
Brendan replied to Adsibob's topic in Tools & Equipment
I use Auro paints which are solvent-free and wash off with soap and water. No need for gloves. Graphenstone would be another good choice. The only time I wear gloves in the garden is when I’m handling jaggy bastards like brambles, in which case these are excellent: https://www.safetecdirect.co.uk/products/hex3092/hexarmor-thornarmor-3092-landscaping-gloves-cut-resistant-level-5-cut-f-?sku=hex3092/xl&gclid=EAIaIQobChMIua-946GJgAMVRuzVCh2ABQKIEAQYASABEgL7ifD_BwE -
When we started our building works, we had lived for two years in our house that had been largely unchanged since it was built in 1961, and were fed up with it. In retrospect I think we should have waited longer and been more thorough in finding a builder - we went for builder as main contractor route. The architect helped us with assessing the quotes and were administering the RIBA contract initially- this stopped when we couldn’t afford the monthly architect’s fees and had substantial delays for various reasons. Otherwise I would have been happy for the architect to continue in this role as they are experienced specialists in energy efficient homes - I couldn’t find a local building contractor who had any notable experience of Passivhaus/EnerPhit type projects. Thinking back, there were signs from the start that our builders weren’t going to be right for the job, but hindsight is a wonderful thing. We have now arranged an early conclusion to our contract with the builder and I am taking on the remaining work myself. I have had to spend a lot of the spare time that I don’t really have, learning how various construction jobs should be done, to understand whether or not they’ve been done correctly. If you aren’t experienced, and don’t have the time to be on site inspecting and discussing things daily, particularly if your building is in any way “non-standard” (E.g. Passivhaus/EnerPhit) where attention to detail and understanding new/different materials and techniques is important, you need a builder who is humble and intelligent enough to ask for help - or spend time looking it up - and you need someone experienced to help you. E.g. the architect or a good project manager. My feeling is that if I started again, I would seriously consider project managing myself.
-
Sorry, wrong region here so can't help you with a contractor. However: Whoever you get, make sure you watch them like a hawk! I had extraction (done properly) and then insulation with Thermabead (or similar). I had a suspicion a whole wall had not been done at all, so I decided to check with a borescope camera before my external insulation was started. Lo and behold, absolutely no insulation at all within the whole gable end wall. I got them to come back and redo it, and pay me compensation for the delays incurred.
-
Before first fix plumbing I bought all the bathroom furniture at my builder's request. This included wall-hung vanity units for all three bathrooms. The downstairs shower is also supposed to have a seat and handrail to make it suitable for elderly relatives to use should the need arise. The bathrooms are all in the timber frame extension so essentially the walls are boarded stud walls, whether internal or external. From the pre-boarding photos I have, I can't see any extra bracing/noggins/ply board that would support these things. It is possible something was put in, but in the absence of photographic evidence I would assume it hasn't been (I have asked the builder if they can supply any evidence). The bathrooms are all fully tiled now, so I have no inclination to undo all of this to find out what's there. 1) Is the Hardie backer type board within the shower enclosure able to support any load, or is it more or less the same as plasterboard in this respect? 2) If there is no evidence of any support behind the plasterboard, I assume I am right that I am going to be stupid doing anything other than buying new floorstanding furniture? Picture of the downstairs bathroom pre-boarding, for example:
-
My garage has openings front and rear, and I already have timber side hinged doors with frames to go into the openings. At the rear opening, there is brickwork either side of the opening for the timber frame to fix into and a Catnic lintel overhead. How should I be fixing the timber frame to the Catnic lintel?
-
Architraves with proud door linings/frames
Brendan replied to Brendan's topic in Doors & Door Frames
Yes, I worked that out! I've got 16 openings to do so buying one is likely to be the economical route. -
Architraves with proud door linings/frames
Brendan replied to Brendan's topic in Doors & Door Frames
I don't think 10mm of caulk would ever look good, certainly not for long. In some cases this would have the advantage of me only having to modify one side of the frame (or lining) as it's proud of the wall both sides. They are screwed in place as far as I can tell. Would a table saw not be suitable, with an appropriate fence? I am not an excellent chippy, in fact I've never done this before, but I have run out of money and enthusiasm for paying other people whose job it is, to do a poor job and be happy with it. In my favour, I am diligent, thoughtful, careful, considered, patient and thorough. I'm also reasonably practically adept. I've already learnt a lot of new skills and carpentry and bathroom fitting are just the next two on the list.