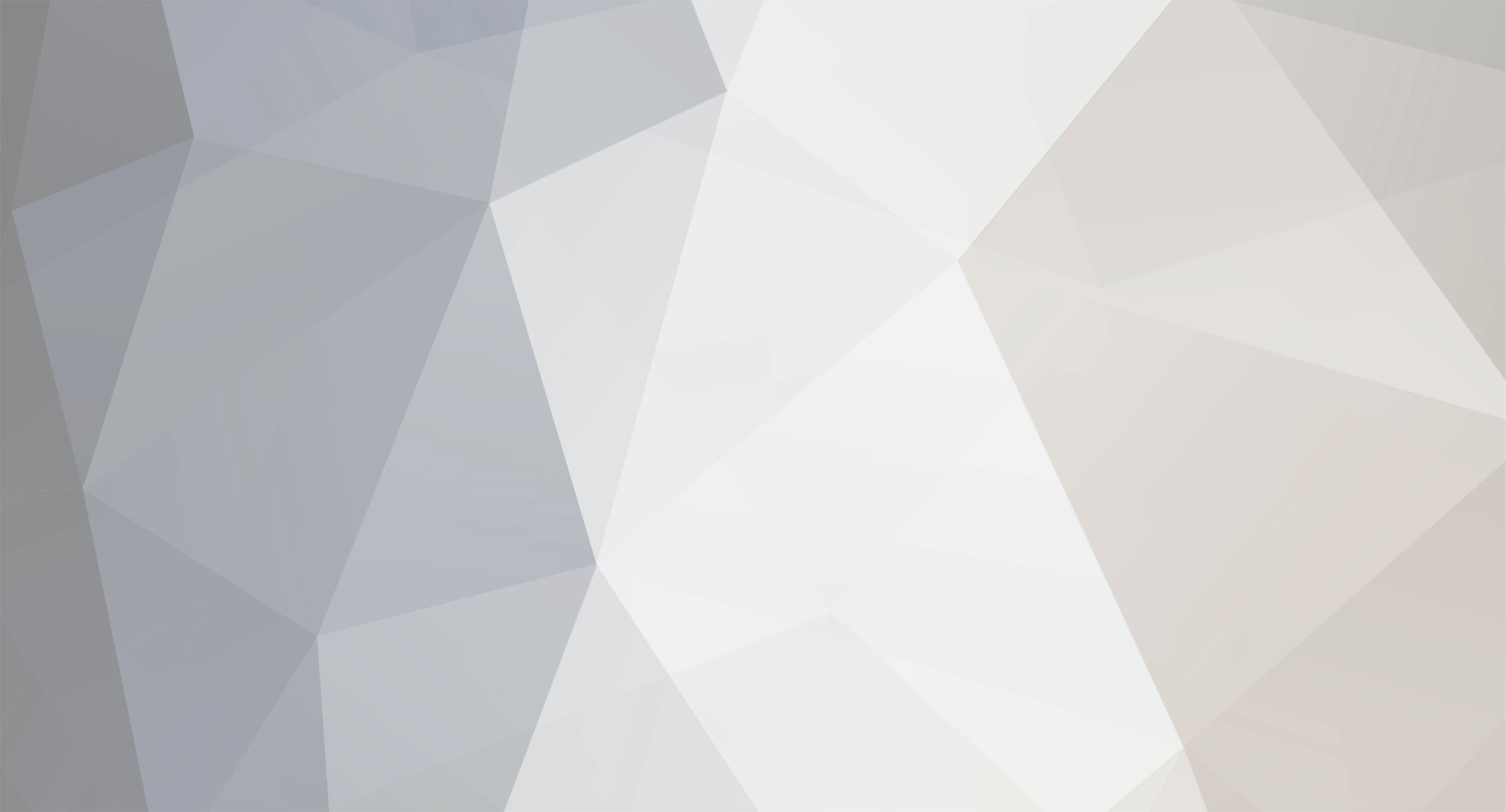
AccidentalSkydiver
Members-
Posts
21 -
Joined
-
Last visited
About AccidentalSkydiver
- Birthday March 25
Personal Information
-
About Me
Chartered Engineer with carpentry skills... just trying to find my way...
-
Location
West Midlands
Recent Profile Visitors
The recent visitors block is disabled and is not being shown to other users.
AccidentalSkydiver's Achievements

Member (3/5)
3
Reputation
-
agreed... 500mm OC with a 47x225 would give you about 455mm(ish) gap in the middle, which would allow for a roll or standard batt to fit easily. 600 centers, you could rip a cellotex 2440 x 1220 in half, throw on some gapo tape on the edges and seal that cavity shut...
-
Businesses Going Bust
AccidentalSkydiver replied to Triassic's topic in General Self Build & DIY Discussion
Its probably going to be an upward trend in construction, cost of living, supply chain issues and fuel cost sky rocketing, lots of bigger companies can absorb it because they have massive margins anyway, but the little guy hasn't. My Dad has a small company been around for about 30 years, and they're finding the pinch points, they raised their costs with the clients (they do lots of sub-contracting) and the big guys absorb it. But the direct customers are getting hit with the increase and they've seen about a 35% increase in people who pull out last minute -
I'd picked 37x37mm off top of my head without consulting my tape measure... things are always a bit bigger in your minds eye aren't they 🤣 but with the two layers, I'd expect plenty of shear strength with the cross sectional rigidity being created with the sheathing and then the actual main structure (since this would essentially be a stand off and run flat and perpendicular to the supporting wall. You're probably correct though, they'd be a bit bendy - I suppose with a 3 / 3 layout at 400mm OC you'd have more strength if you put them on alternating sides... Quickly added a 400mm OC model into a setup in fusion, going to strength model this tomorrow when I have some more time! Yeah I've noticed the flange fit windows and then the super-raving about 'European style UPVC tilt turn' conventional windows here- it is a bit boggling you'd spend the time and money insulating to stick on flange fit which are so poorly sealed in the rough opening... Did utility in 39x89 which is solid, but it was also a fairly small area and a single wall to enclose the flat roof+ an inside walls in the old coal house/pantry. I just did sill seal and a basic rock wool in that area though I understand wood and OSB especially are not cheap - just the few projects I've done in the past year for people have been a bit mad for the materials compared to even 18 months before, however, I've already got a costing sheet I'm using to add up the current expected cost of framing including joists, trusses, rim joists etc with an average of 10% over purchase and a contingency of another 3k - but that might change. Alot of my current plans I've sketched up (confusingly I've done a fair bit of it in Fusion) have an additional 18mm inboard for plasterboard + the external sheathing where needed, plus a 36mm layer in the garage dividing wall for fire insulation - however, I realised I can likely use a single fire-rated plasterboard - Cheers for the resources, I'm going to play with ubakus now
-
Assume you mean 400mm/600mm? 40mm would be a fairly small space Outer layer OSB was to add an additional air break, but offset moving any direct line of air gap off set in an event that air sealing was not properly done or broken. however, this could be easily replaced with meshing or depending on the material of outer insulation simply a good tape like gapotape to create the fit You are correct about the blockwork leaf needing to be tied in, this was a oversight on my part - boredom in a meeting I really didn't need to be at, but was forced to be in + lack of coffee = this, but I did spend some time after my original drawing here looking at a few different larsen/double stud walls, and found most sat the secondary layer in-board, using the shear outside with blocking or osb to secure the inner wall with the insulated gaps between with vapour barriers in place. regarding the marks for the vapour barrier etc - agreed, definitely through marking would help finding studs, its a common enough practice Ah Nice, I'll look into this - Some of the companies I'd looked at (and spoke to) mentioned it would work but I never really asked about how much work it would need to make it work... if that makes any sense at all 😁
-
Yep couple are, but the IBC and BS 8103-3 are physical copies, got the BS one through work (after some bribing persuading the team in purchasing with coffee and cake to let me buy it through the department and I'd pay back at the member price rather than full cost). IBC I bought online shipped to my door Some of the links: Eurocode EN1995-1: https://www.phd.eng.br/wp-content/uploads/2015/12/en.1995.1.1.2004.pdf Building Regs 2021 with Part L: https://assets.publishing.service.gov.uk/government/uploads/system/uploads/attachment_data/file/1057372/ADL1.pdf Scottish small buildings guide: https://www.gov.scot/binaries/content/documents/govscot/publications/advice-and-guidance/2020/02/the-small-buildings-structural-guidance/documents/small-buildings-structural-guidance/small-buildings-structural-guidance/govscot%3Adocument/Small%2BBuildings%2BStructural%2BGuidance%2B%2B.pdf Alot of these I was specifically looking for span calculations for flooring joists and fire bridging standards- IBC was particularly one I was super interested in since the majority of North American homes are TF, California has a specific sub section in their own local codes for fire bridging, and then Alaska / Canada etc have good local codes for Cold and thermal insulation details I've been paying attention to on my travels....
-
Ehh maybe, but if you setup a backstop and a decent jig you could easily build out the idea of a non-structural double stud setup - you just need to keep two studs parallel and equidistant and then have some slots for your spaced blocking to go- if you went with 2ft OC (600mm) from a 2400mm stud you're looking at 4 blocks, if you went side on and not down the middle, you'd 'simply' need to have them ripped down the your given size- in my image below I'd assume 180mm width, 100mm height Because I'm an awkward git? 😁 I'm 100% going to be framing traditionally, but I may add an additional non-structural semi-larsen style outer layer before the masonry - however if I did this, I was preferably looking to run our double stud layer externally of the shear walls off set from the studs in the shear wall to stop the thermal bridging and moving the offset of any air gaps. Here's a quick example I've got in my head ...35mm stone slip, 100mm thermal blocks, 45mm gap, 18mm osb3, 180mm gaps for insulation, with side-blocked 37x37mm battons which are spaced 500mm OC, then the 18mm OSB, 2x6 600mm OC on a 2x6 sill. I'd have the 'lower' one perpendicular to the axis I'm following, starting at the point of the lowest external block (If that makes sense... I've only had one coffee today and 7 meetings) With the offset there would be some places where thermal bridging can occur (the corner here for example) but with offset timbers and air gaps you'd be able to bring that down to a minimum. Then add in something like the proclima kaflex for sealing protrusions for cables, or roflex for pipes - I'd be pretty confident that it will create a very warm and comfortable home.
-
The right side actually looks very similar to my design, except I was having the insulation outboard of the OSB- however further reading, you can run into moisture retention and/our internal vapour and temps causing condensate to gather outside the vapour barrier but stuck in the outboard insulation which can lead to mould which is obviously not great. My order of sealing details are water, air, vapour, thermal... so if I can get the first 3 done- the last should be self supporting when the insulation is in, but running the vapour-open insulation before the main insulation with the service cavity is a nice touch, I'm going to revisit some of my modelling in the next coming weeks once the design of the house itself is done and signed off by an architect, then rest of the actual structural stuff comes after. On another note, I just spent a small fortune on reading materials. I picked up the IBC 2021, Building Regs 2010 (2021 edition, with Part L for energy conservation), Scottish small dwellings guide, eurocode 5 and BSI BS-8103 all stacked up for reading materials for my next few weeks 🙃
-
Strength, I've solely been focusing on the structural design. At the moment, the design has been my number one key point, calculating dead loads - material amounts etc. However I did some research into average cold-zone temperatures and the standard for insulating values in those areas such as Wainright AK. The US IRC 2015 standard for insulation the walls in Arctic Slope region (Alaska) is R35[1] - No where in the Midlands is going to see average temperatures of -29c for prolonged periods of time (Its currently -27c as we speak). According to Rockwools website[2] if you ran 2x6 at 600mm OC, to achieve a U0.028 / R35.7 you'd need to run 5.5in (140mm) then an additional 5in (130mm) outside your 9mm sheathing + vapour barrier + then your brick ties, air gap and masonry rain screen. My original plan was to fill the 2x6 with 145mm insulation batt, 18mm sheathing and then 145mm - but further reading has shown (IMPO) that I could easily drop to a 2x6 145mm batt + the external 50-100mm, with good air sealing details and still achieve the a good insulation level without being excessive. - I have been reading through the idea of a larsen truss (which my dad called a "double stud, single strength wall" for what thats worth) to encapsulate that extra layer of insulation between the rain screen and the actual interior frame and reduce breaks in the sheathing / vapour barriers. Sources and reading material [1] https://www.ahfc.us/iceimages/manuals/building_manual_ch_02_special_considerations.pdf Table 1 Thermal envalope (Page 6) [2] https://bim.rockwool.com/rvalue/ Further info https://extensionpublications.unl.edu/assets/pdf/g2233.pdf http://cchrc.org/media/ArcticWallReport.pdf
-
DIY Kitchens Fitted Office - Colours
AccidentalSkydiver replied to canalsiderenovation's topic in General Joinery
This is a 2.1m x 620mm long desk.. I'm at it 90% of my (working) day... and 70% of my non-working day, I have plenty of space for all kinds of crap on there (including the brush I used to quickly sweep all the crap off it before this photo...). Monitor is a 34" UWHD screen for reference in size... and we've still got plenty of space Had an IKEA 800mm deep desk before, it was flush with the wall on the crap legs it came with and but it was made of cardboard inside so I couldn't even drill through it for a cable tidy 🙄 - think 620mm with cable pockets is more than adequate- I personally wouldn't need 200mm more imo edit: 2nd pic shows full length of the desk while I was still decorating, filling holes in the crap wall and changing plug facia plates 😁 edit edit: Should add, this was a 38mm thick (I think) Melamine coated worktop from B&Q.. back batton is a 30x30 1.8m batton secured to the wall, then this on top.. total build was <60quid with legs, then there was some 90mm cable tidy holes 38p each off ebay. I can put coffee cups and stuff on it without worrying it will ever stain or peel with moisture -
I know lots of American homes run like HUGE insulated piping, but their homes are usually huge to boot- think 75mm radial is standard here isn't it? planned on the MHVR going in the utility at the back of the workshop with the boiler and media closet... can't be a techie without a house full of tech 😁 this would give us direct access to the ground floor through the wall to the living space and then also to the WC/utility space
-
The I-Joists planned are 97x220 mm engineered using glulam upper and lower beams, Maximum span per joist is 9m according to BS8103-3 / NHBC - my biggest span would be 6m over the garage/workshop. And 100mm hole saw isn't an issue with a good saw I did 3x 90mm in 38mm thick surface in about 70 seconds with an erbauer hole saw and arbor, clean sharp saw and a good drill does wonders (built a 2.1m long desk which is die straight, anywhere you put level is the same) Using the 0.003 x 3500 (width of the living space north south) we're expecting to see 10.5mm deflection (which is smaller) that the max of 12mm deflection, but according to JJI table the deflection would be 4.27mm and an SI of 2.40 over the 3500mm span at its maximum point on hangers. I'll be using blocking/web stiffeners across the majority of the living space to give horizontal deflection capability and share some of the load there, manufacturer I spoke to can actually put in holes in the board before delivery but it would be much more difficult using solid joists (or glulam!)
-
I was speaking to my mate who's a SE working for Manchester council on their projects, he said they recently had an issue with some council houses which are SIP built with window opening pre-formed in the panel was 40mm to the left of where it should've been, on 13 panels, and because they're not just stud walls and then sheathed they were a pain in the backside to rectify and builder ended up just scrapping them in favour of new panels all together. They also found some issue with undulation in their foundations causing gaps in some places since the edge of the pad was tapered off - he advised to go full stick frame and sheath which I think is my direction. Have architect booked for 4th April for look over and consultation on my designs, then I've got a meeting with Amit to get him to review all my calculations and load paths for my design.. paid for with a case of beer 🍻 then its all off to planning... once all this is done, I'm about to fill my dads yard/workshop with a few pallets of timber and OSB 😁
-
I've been in constant conversation with a very good friend and ex-colleague of mine who's a SE through out the design process, He has already agreed with me 2x6 with a 600mm OC, california corners at all external corners and 3-stud U-Channels for interior walls using 2x6 for all load bearing walls are more than adequate. I'll be cutting all the framing on site to account for undulation in the foundations obviously 'flat' pads can be a nightmare with undulations and waviness. Only thing I wont be doing is trusses, I can get these made relatively cheap compared to hand cutting them on site - Joists are still on the board, I'm still considering using a I-Joist over 45x220 - mainly because they have a higher load carrying weight, lighter so I can move them myself and come in longer spans than I'd usually get in 45x220 My only walls in the entire design that are 2x4 are non-load bearing partition walls between the downstairs WC/Utility and the en suite/master, everything else will be 2x6 interior and exterior. The total floor plan is less than 1780sqft not including the garage (main house 2 floors + granny flat only) I know I sound like a no-it-all kid, who's just being awkward, but I've done extensions, stairs/stringers, summer houses, porches, dormer windows with hand-cut hip rafters etc oh and a bed because I dislike Ikea I'm confident in my ability and between myself and my dad we have probably 40 years experience in carpentry and building (He's a chippy too, I'm just not one professionally anymore) - just now need to find some more cash and get cracking
-
Hello! Its a bit of here or there! New builds will be much higher insulated to conform to building regs etc - but they are all fairly small, gardens are no bigger than my drive way and some even have covenants against a bloody garden shed! unless you spend a fair whack for a bigger new build property, older houses are generally more substantial in size, but will require more work for the insulation, windows, heating etc (unless these are done but then the price goes up) already. Older houses tend to leak (air, not water - unless it is leaking water then run!) air so will need a fair amount of air sealing to ensure tight retention of conditioned air (heated, cooled whatever). Self building is a whole 'nother kettle of fish, There are a few lenders now who will do staged mortgages for building - land, foundations, walls, utilities (wiring/plumbing), roof etc but they require a 10% deposit in most cases, you need to find land with permission (or land without, then get permission with plans).
-
Yeah I've looked at SIPs, I'm on the fence- one hand they'll be quick but the other hand, I have experience/training in commercial carpentry including exposed oak frames etc and a hankering to build 😁 Recently (2020 > 2021) did a stick-frame extension (20ft x 12ft) for my parents 2x4 with double top plate, XPS in the wall, 18mm ply, 150mm PIR insulation outside, 50mm air gap, traditional brick outside - its incredibly warm, frame went up in about 2 days with 45x220 joists over the top taking another day or so to get done then it was about 2 days sealing, taping, flashing, exterior insulation etc