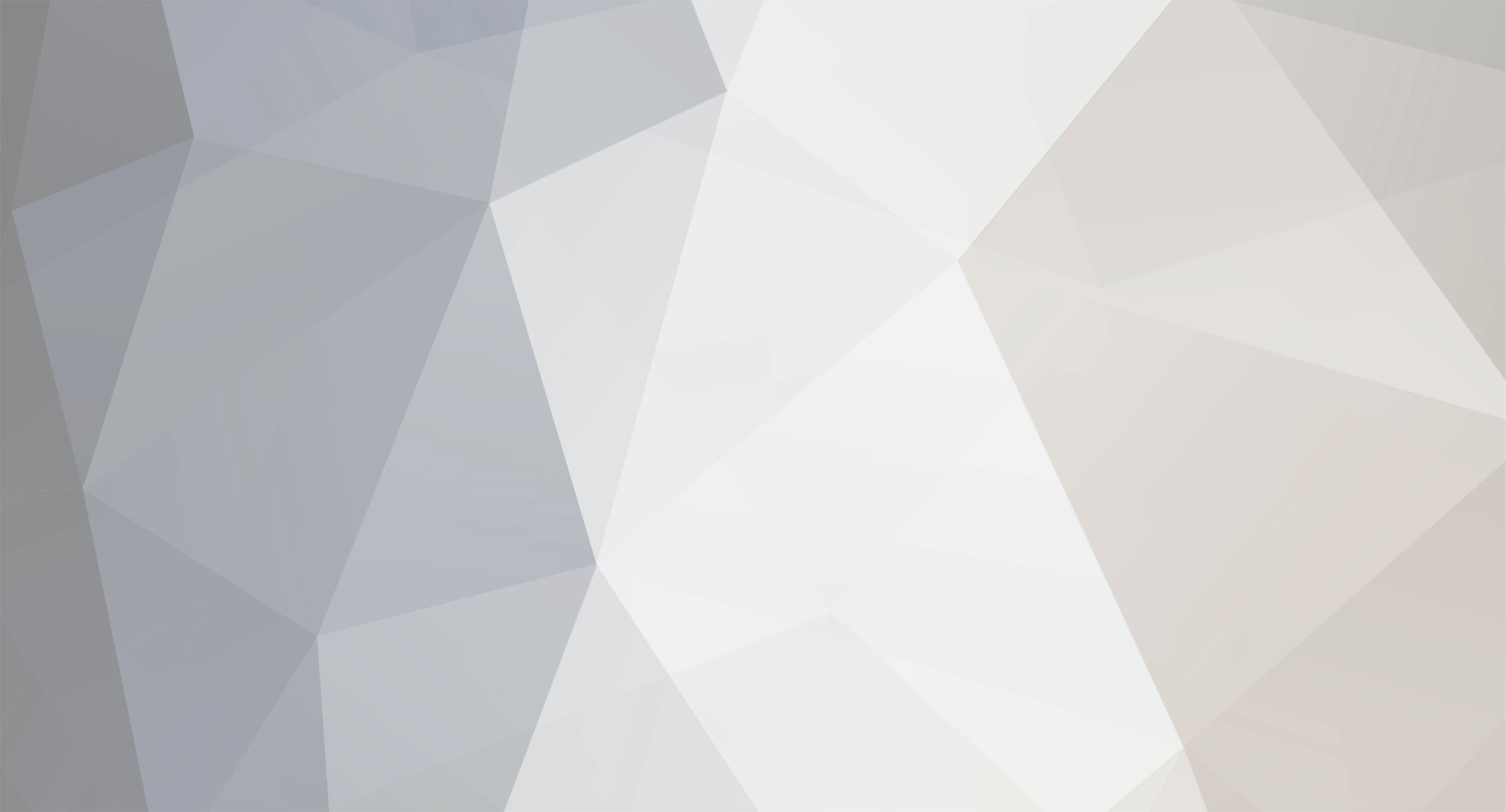
Snowbeetle
Members-
Posts
65 -
Joined
-
Last visited
Snowbeetle's Achievements

Member (3/5)
18
Reputation
-
Talk to me about dry ridge vents
Snowbeetle replied to Snowbeetle's topic in Roofing, Tiling & Slating
My ridge tiles are capped so can't re-purpose them for that particular system. But good to know that other people have done that in other cases. Has anyone else retrofitted a system like this, what pitfalls did you find or did it go smoothly (as anything ever does)? -
Talk to me about dry ridge vents
Snowbeetle replied to Snowbeetle's topic in Roofing, Tiling & Slating
Thanks for your reply. Much appreciated. -
I am converting an existing building into a house and need to have the rafter space vented to prevent condensation. I have installed eaves vents and now need to get a ridge vents in. Roof is a slate roof with hip ends (no gables) currently with clay, capped ridge tiles (local vernacular would like to keep). I've found this product which has similar ridge tiles to mine, so I am wondering if I can put the holes in mine to adapt them as substitutes.. New Redi-Ridge ventilated dry fix ridge and hip system from Forterra. Also found this one which has a ridge tile similar to mine (but was hoping to avoid unnecessary cost) Ridge Systems | Redland I'm wondering if anyone has experience of retrofitting dry ridge vent system, any recommendations, thoughts or pointers? (this is my project Bungalow Barn - update - Barn Conversions - BuildHub.org.uk) Thanks
-
Hi, We have a selfbuild mortgage with Newcastle Building Society through Buildstore. Both companies have been good to work with so far. We originally scheduled the selfbuild stage to take 3 years which was up at the end of last year (2020). Nerwcastle were happy to extend that (though it cost us another 12 months indemnity insurance) until end of 2021. As we approach end of 2021 we find that we are gpooing to need another year (we are doing this entirely self built, through pandemic, home schooling and a few other hiccups giving us delays). Does anyone have any experience how tetchy / twitchy Newcastle are likely to get? I am wondering if they will want to do a big inspection or what their reaction might be? I am clueless what to expect and though I'm happy tpo handle anything I'd like to know what attitude or difficulties this is likely to throw up for us? We are not struggling with budget it is just(!) the timeline. Any wise words?
-
Wood Fibre IWI - plaster removal or reinstate?
Snowbeetle replied to larry's topic in Heat Insulation
Thanks for the links, I haven't referred to those for my reply as not got time to look just now. I'm always interested and curious though (much like you) so I'll check them out later. If you want the details of the lime plasterer eventually let me know. -
Wood Fibre IWI - plaster removal or reinstate?
Snowbeetle replied to larry's topic in Heat Insulation
Hope you can decipher the autocorrect garble. -
Wood Fibre IWI - plaster removal or reinstate?
Snowbeetle replied to larry's topic in Heat Insulation
I think the issue is in the definition of 'breathable'. Can wet pass through it... Yes, but will it actively facilitate it's movement...no. So for instance, wool insulation will let wet go through it. But I it doesn't actively assist. Imagine a soggy tweed wool jacket. It will stay wringing wet until you hang out by the fire or get a nice breeze going over it. So it its not that it is impermeable like a sheet of plastic so much that it isn't dissipating and moving the water on and out. Wood is the same. You can use them but where you know that draughts it warmth will stop them from sitting soggy. Gypsum doesn't like water, it tends to soften the plaster and cause it to fail if it is moist often or stays moist. So it isn't like a plastic sheet but it isn't happy acting as a member of the team in a breathable system. Lime plaster acts more like blotting paper, put a drop on it and it will disperse and keep dispersing until it is down to the molecular level and easy to vaporise and disappear. This causes the line no harm. It's on the team as it were. The problem lies in the fact that this field of expertise is still going through a process of formalising and professionalising (as I mentioned up thread), so some of the terminology is used interchangeably and doesn't always have consistency of meaning. Things like wood and wool can still be used but you would need to keep in mind their properties and not put them somewhere where the hygroscopic nature is going to be an issue. There are some minerals etc you can add to lime plaster to create an insulating effect, or to buffer and manage water even more effectively than stand alone i.e hemp or certain minerals... Ty Mawr in Wales do some courses which are for folk like us which you might find interesting. It seems like a dark art, it's not, it's just that the development of a body of expertise is relatively limited and not as easy to summarise due to the historical factors. It is much better than it was though. -
Wood Fibre IWI - plaster removal or reinstate?
Snowbeetle replied to larry's topic in Heat Insulation
Incidentally, though wood fibre is breathable you still need to use it in the right way as it is also hygroscopic which will mean it doesn't dissipate the water molecules so whether it is right for your application depends on ventilation and substrates and what they are doing in the performance of your building. If you haven't checked I would be tempted look into it if I was you. -
Wood Fibre IWI - plaster removal or reinstate?
Snowbeetle replied to larry's topic in Heat Insulation
Breathable alternative to plasterboard.. Wood Wool Board | Savolit Plus | Natural Plasterboard (mikewye.co.uk) -
Wood Fibre IWI - plaster removal or reinstate?
Snowbeetle replied to larry's topic in Heat Insulation
Much better place to acquire information/knowledge Search our Knowledgebase | www.spab.org.uk -
Wood Fibre IWI - plaster removal or reinstate?
Snowbeetle replied to larry's topic in Heat Insulation
sorry that wasn't the video I thought it was...not actually that educational at all... -
Wood Fibre IWI - plaster removal or reinstate?
Snowbeetle replied to larry's topic in Heat Insulation
Good video Problems With Cement in Traditional Buildings - Video | Unity Lime Yes, lime+wood fibre will be breathable. The cement render isn't of course which may or may not be an issue - any moisture getting into your brick can only escape inward but if the volume and rate is low that isn't necessarily going to cause problems. You could consider altering that, but costs / benefits etc all need to work and some bod like me on the internet can't tell you that. All I'm trying to do is flag up potential pitfalls for you. My previous house had an unsuitable insulation applied, sadly I didn't have the knowledge then and the advice I was given was ill-informed (I now know). Unfortunately the people who bought it will be suffering the symptoms of that for years (I didn't know when I sold it). It is common unfortunately. -
Wood Fibre IWI - plaster removal or reinstate?
Snowbeetle replied to larry's topic in Heat Insulation
Plasterboard/gypsum plaster is not breathable. Likely the paint isn't too. So yes your bricks are currently sandwiched between two non permeable layers. Whether this actually gives you problems or not will depend on whether water is reaching the bricks. Which as you can imagine could depend on many things. But the fact is that you can't argue with water, so you either need to very effectively keep it from ever getting to your build fabric in the first place (this is the modern build system. So wall cavities, damp proof courses etc) or, you have a building which works with the water and you provide it with a non-damaging escape route (this is the older building method, so materials buffer the moisture variation and expirate it without harm so ultimately the building is dry for the inhabitants because the fabric does the job of buffering and expirating correctly. Because the older building methods were skills handed down verbally father to son or apprentice the country lost a huge body of knowledge in the world wars and the massive build programme post WWII meant concrete and pre-fab with it's ease of setting was the go-to choice. So now the building trades and modern buildings are much more familiar with the modern systems. Add to that that modern methods have been applied to old buildings often leading to problems as people unwittingly mashed together water exclusion versus water management systems meant that the traditional methods got a really bad name and you will often find builders who won't touch it with a 10' barge pole. But although lime/gypsum plaster have the same job as a finish surface, they function and are applied differently so they are kind of apples and pears. There are a lot of people now formally re-developing the body of knowledge and products are becoming better known, but it can be hard to find the information for the DIY builder. In a nutshell if you try to mix the systems, you could cause problems unless you know what you are doing (i.e in that particular situation what result the relationships between the systems will create - I have a stone barn conversion and the roof has a non-breathable membrane which I have to keep for bat preservation so I have adjusted my methods to account for the interplay between the two), whether you get problems or not will often be down to the luck of the draw as to what water makes it as far as the building fabric. You get a lot of people trying to retrofit water exclusion methods to a building constructed with water management in mind, such as people chemically injecting sealants into single skin brick houses. but that often just pushes the water onto the next thing. I have a friend who tanked their victorian basement so they could have a games den... the water it was providing an escape route for then just started creeping up their lounge walls instead so now they have to tackle that. They would have been better putting in excellent ventilation. You can't argue with water as anyone who has been to the grand canyon knows, so if your building can't keep it out (no foundations / DPC) then you have to let it escape. Or just cross your fingers and hope you don't have a lifetime adressing damp symptoms. It can be dismaying to find you are trying to bolt on unsuitable methods to an old house, modern materials are often cheaper up front and people are familiar with them. But, if the house is to be your home for years and you want to do it right and do it once, you should educate yourself what you're tackling to make the decision. -
Wood Fibre IWI - plaster removal or reinstate?
Snowbeetle replied to larry's topic in Heat Insulation
The external concrete render will mean any moisture in the walls, (possibly coming up from the ground - depends on foundations and DPC, if there is one; or weather getting behind the external render - render varies in how well it keeps the wet out - age, how well the joints are done etc) won't escape outward and will only escape inward. Wuth lime plaster on the inside it can escape that way and not be forced on to appear elsewhere. At that age your building is likely to be single skin brickwork not double with a cavity, so how dry the fabric of the building is will depend on it 'breathing' in line with buildings of it's age. So your lime plaster will buffer moisture (take it in when there is an excess and expirate it when humidty drops) and allow water to escape. If you put gypsum on, that doesn't 'breathe' so any moisture in the brickwork will not escape and could lead to damp problems. JFB has a point that in a small area the effect will be minimal, so your choice if you want to worry about that or not, for 1 sqaure metre you are unlikely to see issues but moisture finding itself behind the gypsum will have to go sideways/up/down to escape. For the reasons I mention: a) You could do, it isn't 'ideal' but it isn't likely to bite you on the bum too hard. b) I agree with JFB the wood fibre on the walls would not be a good idea, it could end up slwoly getting wet and wood does not dry readily without good ventilation. c) no d) You could lime plaster the patch, it isn't that hard but the technique does differ to gypsum and it is a more skilled managing the going off process than gypsum, so you'd need to look it up, or I know an excellent lime plasterer who travels and isn't stupid money, so if you PM me I could give you their details. I only go into the explanation cos you wondered about the whys. But since you are plasterboarding you are making the walls non-breathable anyway. I wonder if the building will cope with that (deoends on whe way it was constructed and how it stays dry, how it is used, ventilated, affected by external weather etc. If you want to look at that sort fo thing more this guy is knowledgeable on older buildings and what helps/doesn't help Energy Retrofitting - why it doesn't work and why it's causing damp. - YouTube This email is about a slightly different question but the forces at work are the same.