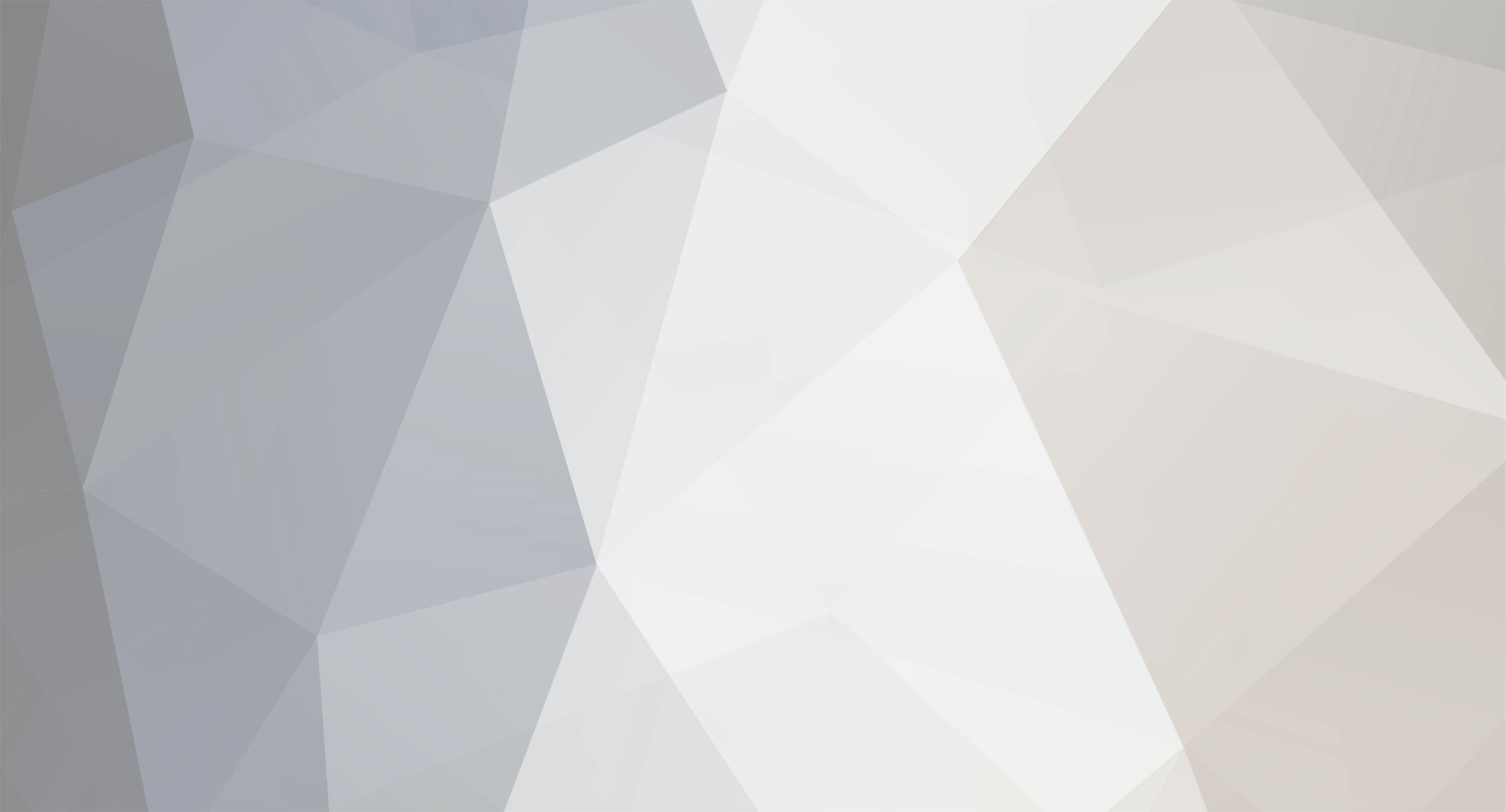
Rishard
Members-
Posts
165 -
Joined
-
Last visited
Recent Profile Visitors
The recent visitors block is disabled and is not being shown to other users.
Rishard's Achievements

Regular Member (4/5)
28
Reputation
-
Closing cavity at the top for blown beads
Rishard replied to MortarThePoint's topic in Heat Insulation
I was aware of the fire issue in clear cavities. It’s mostly the moisture issue I was concerned with, if it is a concern at all? -
Closing cavity at the top for blown beads
Rishard replied to MortarThePoint's topic in Heat Insulation
Other than preventing air movement and in some cases blown beads, is there any other reason to close of the cavity where it connects with the roof insulation? I know mineral wool is none combustible so fire spreading isn’t an issue. Is moisture travelling from the cavity wall upwards towards the roof insulation a concern at all? I’m detailing my wall junctions similar to @Mr Blobby with mineral wool. Below my rafters I will have my vcl which prevents moisture moving into the roof. I hadn’t thought about moisture moving from the cavity at eaves and the gables into the roof insulation. -
There is a ridge board above the glue lam which the rafters are all fixed to so there are no holes in the dpc. It’s also stuck down with airtightness silicone. Would have used a ‘smart’ membrane similar to the vcl which I’ll be using but didn’t have any to hand. Felt the dpc would be better than a roofing membrane out of the 2 available materials to hand.
-
It’s dpc. It will tape into my vapour control layer once the osb is attached to the ceiling. I was just going to tape the vcl to the beam but figured this would be a lot easier.
-
My longest ridge beam is only 6m. I’ve used glue lam throughout as I love the look of it. I’m actually lifting them up tomorrow so I’ll get some pictures. I also built a gluelam truss just to give a bit of a wow factor as it’s above the main enterance at full height from ground floor to the ridge. I actually joined a couple of glue lams, they join on a masonry wall. That beam is now 10m long. My supplier could supply up to 15m I think but I would struggle to lift my beam in at 10m. My engineer calculated my beams and I basically doubled the height mainly for aesthetics. I think I could have gone deeper still. Here are a few pics:
-
Likewise with mine. It’s a racking layer. Not required where I am but it only cost me £400 for the osb. If I’m able to osb the underside first, it’ll give me a great base to snug the mineral wool into. I can then tape my vcl to it from below as it’ll be a good flat surface to work with without having any bulges from the mineral wool.
-
@ProDave Did your frame therm come in slabs or on the roll? Did you need to make these shorter lengths to handle or could you put up large sections in one? Did it require any temporary support before you put the osb up? Good to know there is an alternative way if I decide to insulate from below. I’m also using Knauf as I find it much nicer to handle. I’m using 150mm Knauf batts in my cavity so I can also use up some of my remaining bits of insulation for between my rafters.
-
I would start with finding out what size your rafters need to be. Mine had been oversized by the architect to accommodate more insulation. Moving to a warm roof allowed me to reduce these and thermally break them with insulation over the top. I’d think full filling your rafter depth with a mineral or blown material will ultimately be easier to do. Mines a gable to gable with 1 small valley section. If there were dormers or hips, pir in between would become even more tricky.
-
@Crofter I will indeed nail up the osb first when I get a couple of clear dry days. I’ll then cut my rafter roll insulation to my rafter spacings and roll it in, followed by the pir over the top. Working from above as you say. Mineral wool still isn’t great but at least it won’t be flapping down in my face with reduced ventilation.
-
I’ll chime in on this as what you’re proposing is very similar to what I’m about to undertake. Robins method requires a lot of skill and accuracy. I’ve done dozens of roofs with cut PIR between. It’s horrible. Not to mention difficult to achieve the level of accuracy. Gapo tape does help with this somewhat but comes at a very high cost. Cutting 100mm pir is hard to maintain accuracy, I have the fancy festool insulation saw and even this isn’t perfect. I’ve done 70mm sheets on my table saw where I can make repeat cuts. Doubling up sheets can help achieve your thickness. Even when every rafter is meticulously fixed and spaced there always seems to be a slither of light that gets through somewhere. If you’re prepared for cutting lots of pir and buying a boat load of gapo tape then his method is great. For me, buying Pir is by far the cheapest method of insulating sadly, combined with its uvalue it’s very appealing. Using the full sheets over the top seems to be the best solution for pir, minimal cuts and thermally breaking the rafters. I have 180m2 of warm pitched roof to insulate and I’m working to a similar principle to you. It won’t be everyone’s cup of tea but I’ve researched and costed out multiple versions of insulating this roof. I’ve had advise from my phpp designer and condensation risk calcs done. They all state the most breathable material to the outside however the VCL changes everything. Obviously it needs to be bullet proof which may be hard if your contracting this work out. For me, being the builder on this, I’m very confident I can achieve an excellent vcl in my roof build up. Height is also and issue on my project as some areas already have low eves ceilings on plan and the ridge height is already decided upon on planning. (Had I known what I know now when I put in planning 6 years ago….) My build up is 120mm pir over rafters in 2 layers to stagger the joints. 145mm rafters full filled with Knauf mineral wool. 11mm osb below vcl service void. I know the risks. I’m willing to take it. The condensation risk came back ok with an effective vcl. For me, it’s mainly cost and simplicity of installation that ruled. I got a uvalue of 0.1 with the above. Also have mvhr planned. I costed out dozens of alternative blown cellulose and wood fibre options. They bother required much greater rafter depths which double my timber price. Wood fibre came in at twice the price of pir for half uvalue for thickness. I know all of the above have different characteristics and achieve varying uvalues and that uvalue isn’t only thing to consider. Everyone’s circumstances are different on their project, sometimes a bit of context may help. Who’s installing the roof? Who’s installing the insulation? What do you have on your plans? What u-value do you need? What’s your budget? If I had the money and roof height weren’t an issue I would go wood fibre over engineered rafters with blown cellulose allday.
-
Ok. My plans were submitted pre the last building regs change. Going from 0.13 to 0.11 ( from a quick google) In my phpp I have it at 0.104. Anywhere below 0.11 would feel satisfying. Although from some of your previous messages, the real terms difference of these uvalues may not have to drastic a cost implication from a heating perspective. I have had a quote for blown cellulose which is promising. It does come in as the most expensive option currently. Plus the additional cost of Ibeams or using local stock with extra additional timber screw on. My current favourite option is 170mm rafters 180mm mineral wool 100mm pir below rafter. Vcl 25mm service void plasterboard. All locally available and altogether come in cheaper than the supply/install of cellulose. I could take my rafters down to 145mm minimum if needed. I’ve been in circles with this, as you may see. Flipping the above option presents a ‘condensation risk’ in my calc. Leaving it this way does have some small thermal bridges at the ridge and the wall - roof junction where the insulation thins a little around the birds mouth connection at the wall plate. Gauging which of the 2 small compromises is better or worse is where I’m at now. No doubt there are multiple other options. I’ve priced all the cellulose/wood fibre/ mineral wool/ pir / hybrid / warm options. The more layers I add seems to add either cost and or complexity. What’s the saying, keep it simple stupid? If only 😅 My original architects plans are fairly lose but generally it shows 200mm pir between with 25mm under. I think we both knew at the time it wasn’t going to be this but gave us enough to put it through planning. The roof will all be hand cut with a gluelam ridge beam. All vaulted. There is some adjustment on wall plate heights if I need to favour a warm roof. And 145mm rafters would tick the box for my spans.
-
Also. Is the osb below the pir needed or is this for racking strength? If I wasn’t using this osb as my vcl would it need to be there? Vcl would go below mineral wool in this option.
-
Would an intelligent membrane work well as the vcl in option 2?
-
-
I’m doing a cut roof so I was going to bring vcl from ceiling down to meet internal plaster. At the ridge I’m using glue lam which are on show. I was going to drape a metre strip of vcl over the top of the glue lam sandwiched with a 6x2 timber plate which the rafters would fly over. This could then be taped into the ceiling vcl when roofing done. Im using 175mm rafters. My latest plan was to fill them with 180mm of mineral wool at 0.034 with 100mm pir boarded directly below the rafters taped, an additional vcl and then a 25mm service void. I’ve looked at the above make up and wonder if I could flip them, pir on the outside as you say. My concern is that if the vcl isn’t 100% then I may run into issues… thoughts?