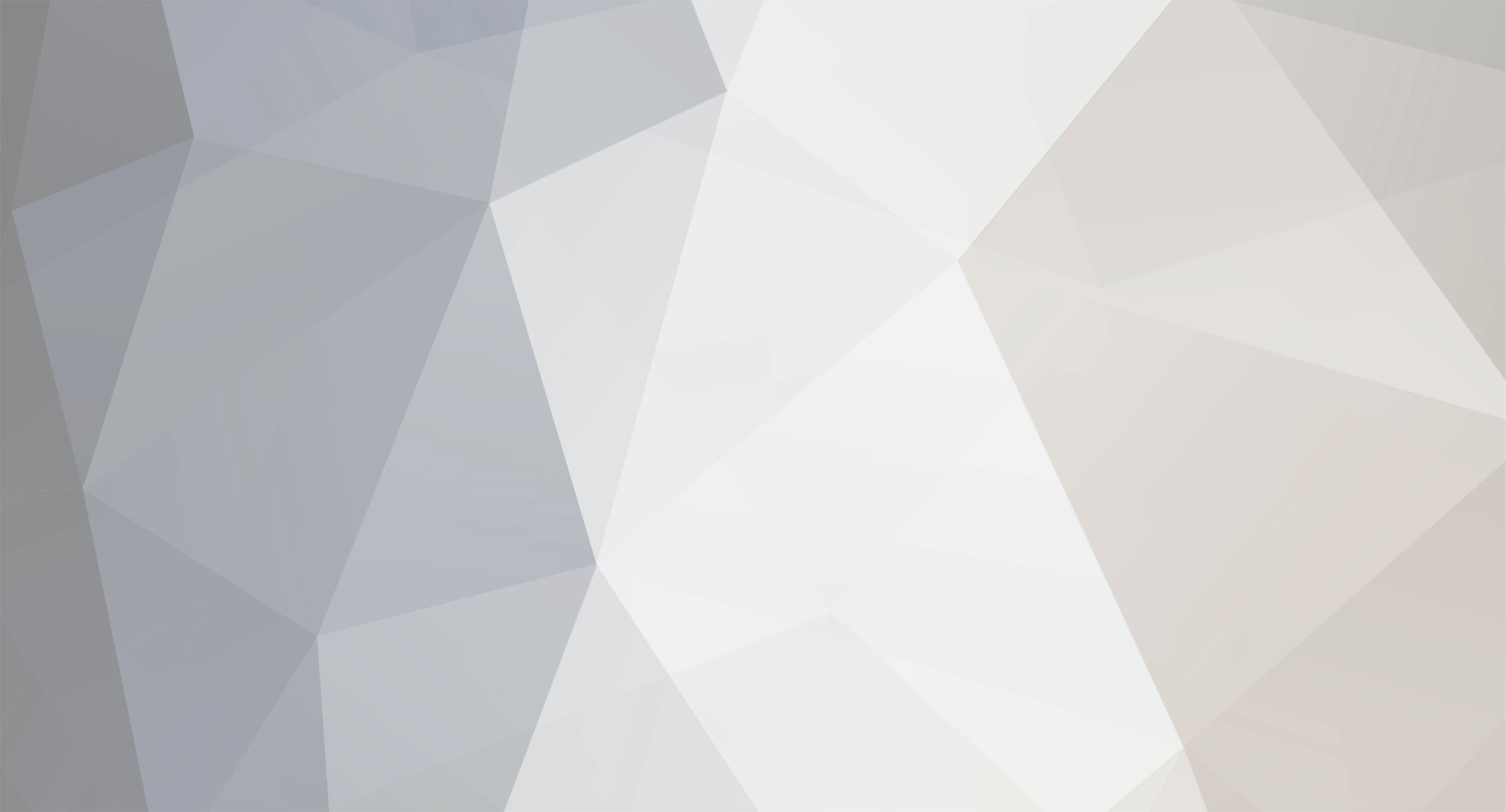
Crunchynut
Members-
Posts
88 -
Joined
-
Last visited
Recent Profile Visitors
The recent visitors block is disabled and is not being shown to other users.
Crunchynut's Achievements

Member (3/5)
11
Reputation
-
Cheap way to prevent boiler cycling
Crunchynut replied to Crunchynut's topic in Boilers & Hot Water Tanks
@Silverdee I have d m you with some details. -
Planning permission for new sewage treatment plant?
Crunchynut replied to jumbletons's topic in Waste & Sewerage
Just for those coming across this thread in the future. I’m in Staffordshire and replaced an existing septic tank with a STP and had to have planning permission. I argued the point with them but they insisted it was a requirement. Maybe different authorities have different needs. Building Control too, of course. -
Good evening, I'm after advice, hopefully I'm in the right place
Crunchynut replied to Cross's topic in Waste & Sewerage
My view : If the deeds say that access must be given to allow development at the end of your garden, that would mean whatever is necessary to meet the minimum building control standard, in connecting to the drains. Inspection chambers are usually required where there are junctions or branches. So if the builder is installing one it could well be because he has to. I doubt he would do it if it wasn’t necessary. Also, suppose it isn’t done and then there is a blockage and your garden has to be dug up to find and fix the blockage - you may be glad of an inspection chamber in this scenario. I would just check that whatever is being done is necessary from a building control perspective, ensure it is done to a good standard, and that everything is ‘made good’ when finished. Also make sure that your drainage is unaffected - eg that a branch into your pipe is not poorly designed potentially causing you problems with blockages etc. -
running soil and waste pipe in new extension
Crunchynut replied to mandrake's topic in Waste & Sewerage
A sketch would be helpful, to fully understand your situation. -
I agree gravity is best if possible. Though if there was a long power outage the sewage treatment plant would soon be in difficulty and that’s a different world of pain. In fact, being able to store for a while in a pumping station would prevent ‘not quite treated enough’ effluent flowing out of the stp if it has been without air for a while. Everything’s a compromise at the end of the day.
-
Maybe, but the risk is low. No lives are going to be lost. If there is a power outage then normal life goes on hold. No washing machine, dishwasher, shower, cooking etc etc. so our 1000L a day output would dwindle, and if it became a problem we would jump ship and squat (no pun intended) somewhere else. I’m in the countryside but not anywhere remote or exposed, and in 25 years here we’ve never been without power for more than half an hour. So not ideal but very low risk in my case.
-
I pump into my sewage treatment plant. It’s been installed 2 years and has been faultless. It is silent in operation. In theory, in England at least, the tank should be big enough to take 24 hrs of waste in the event of a power outage, but when I discussed this with our BC they were clueless and didn’t care on the issue. My tank would take 18 hrs worth of output in normal use. I have a timer that sets it to pump for 5s every 40 minutes. It doesn’t sound much but these pumps are beasts and 5s is about 30L. That means the treatment plant receives a nice rate of input throughout the day rather than heavy flow at bath time (for example). This is a benefit to the tank. Also if cleaning agents are held in this way then they have a bit of chance to neutralise / dilute in the pumping tank. So, that’s my experience. It’s better without, obviously, but don’t discount it as being too bad a thing if it simplifies the rest of the install.
-
Is it ok for builder to leave pipes like this?
Crunchynut replied to nmh's topic in Waste & Sewerage
What are the blue and red pipes/cables in the background? -
I sometimes use a small BM and they don’t have hiabs. I asked about why not and he said the trucks are hugely expensive and the drivers need special certification to operate the crane …. which means for a small BM it’s just too costly. Mine was delivered on a tale lift truck and so got wheeled into my yard on their pallet truck. Local farmer lowered it into the whole using the front loader on his tractor.
-
My Learning points in case they help (sorry - order is a bit random). -As others have said - definitely an air blower system with no moving parts to go wrong in the tank. -Take a look at building regs - Part H I believe - has some good guidance best not ignored, and good for you to know so that you know a contractor is doing it right. -Install it in the summer when the ground water is low - a flooded hole or caving sides is a headache you can do without. -Make sure concrete is semi dry - if it’s too wet it will put too much pressure on the tank walls as it slumps. I mention this because concrete suppliers are a mixed bunch and sometimes you get what they bring, regardless of what you asked for. Also they don’t like semi-dry cos it’s a heavier load for their mixer to churn and wears the gearbox out. At least that’s what my concrete delivery guy told me (in a grumpy manner). -I reckon all these systems need a bit of tlc from time to time. For that reason I chose a Vortex because the access is via a large lid, whereas some other systems seemed to have a smaller hatch. I also chose a low invert depth model which meant pipe work and adjustments were all near the surface and in easy reach. Invert depth may be dictated by site levels, of course. -Put plenty of concrete round it. The installation instructions will probably say minimum advised concrete back fill based on ground water because they want their systems installed cost to appear low, and a contractor may also want to get away with minimal concrete. But - if you have to empty it in the middle of winter when ground water is high you don’t want to be worrying about it floating out of the ground because you skimped on a couple of hundred £ worth of concrete.
-
Thanks for your replies. I’ve not go an issue with staying with 50mm pvc and solvent weld, and plenty of suppliers around. The concern I have is whether I can solvent weld onto the existing pipe. If it is pvc then no problem, but the fact that it is push fit makes me wonder whether it’s whatever push fit is made of and you can’t solvent weld that. As @ProDave says, 50mm OD is non-standard in the push fit world, it seems. I guess I can do the tap test (tap fingers on the pipe - push fit sounds soft and ductile and solvent weld more brittle sounding) to help confirm but access is tricky. A rubber sleeve adapter from push fit to pvc may be the answer in normal circumstances , though I’m space limited so might not be an option.
-
I need to do some plumbing and match into an existing installation. The existing pipe is a funny size - it is 50mm OD which made me think it is metric PVC pipe. But, it is using push fit fittings, whereas the only PVC pipe I can find is solvent weld. Any ideas as to what I’m dealing with and where to get supplies? (note 50mm push fit is 50mm ID / 54m OD as far as I know)
-
Those costs look in line with what I’d expect, in the U.K. at least. By simplify, do you mean to avoid the planning costs?
-
Leak in kitchen - is soil pipe the source?
Crunchynut replied to Bearino's topic in Waste & Sewerage
Hi @Bearino Your post has lots of views but no replies yet - I guess, like me, people don’t know where to start, because you have a right mess on your hands there. It looks to me that because the toilet soil pipe comes through the outside wall at roughly the same level as the flat roof, they have built a ‘waterproof’ box over it because the pipe spoils the ability to properly cover the roof in that location. But it looks like it has been done very badly (sorry to offend if you or yours did it) and was always destined to be problematic. I would say that anything you do to ‘patch it up’ is going to fail within a short space of time because you have nothing decent to work off. The bitumen on the pipes is probably a crude way to try and seal everything up and prevent leaks - just daub with bitumen in a ‘spray and pray’ kind of fashion. Tarps work to keep a central area dry but water always gets round the edges in my experience. And it only takes a bit of water to make everything wet. So, for example, if you were just to butt the tarp to the wall of the house, water will get behind. It will be better than nothing of course, but not a solution. In the past when I have had to do this I have used ‘flash band’ (roll of aluminium about 5” wide with tar on one side that you heat up and stick down with a blow torch) to seal between the wall and the tarp, buts it’s all quite precarious. You can re-box it but you need to properly flash the join between the box and the roof. By that, I mean the roof covering needs to lap up the sides of the box and then the box covering needs to overlap the ‘turn up’. Difficult to do with felt since you will have a lot of joins and laps and felt cracks quite easily either straight away or soon after once the weather gets to it. Buying a prefabricated box might be an option. Points 5 and 6 - I’d say you need to rip all of that area out because it will never be any good. The wood will rot and the damp smell will pervade. The mass on the pipe might be someone just having stuffed in something absorbent to stop a leak, or perhaps prop up some felt. If it were me - I would look at putting a new soil pipe on the toilet, run it through the wall and then straight down into the roof, you can get flashing collars specifically designed for sealing around pipes in this configuration so a good job can be done. Then inside, properly connect the pipe into the existing stack and make good with new stud work and plastering etc. Sorry if that’s all no help - the situation isn’t entirely clear - but I thought I would try and reply.