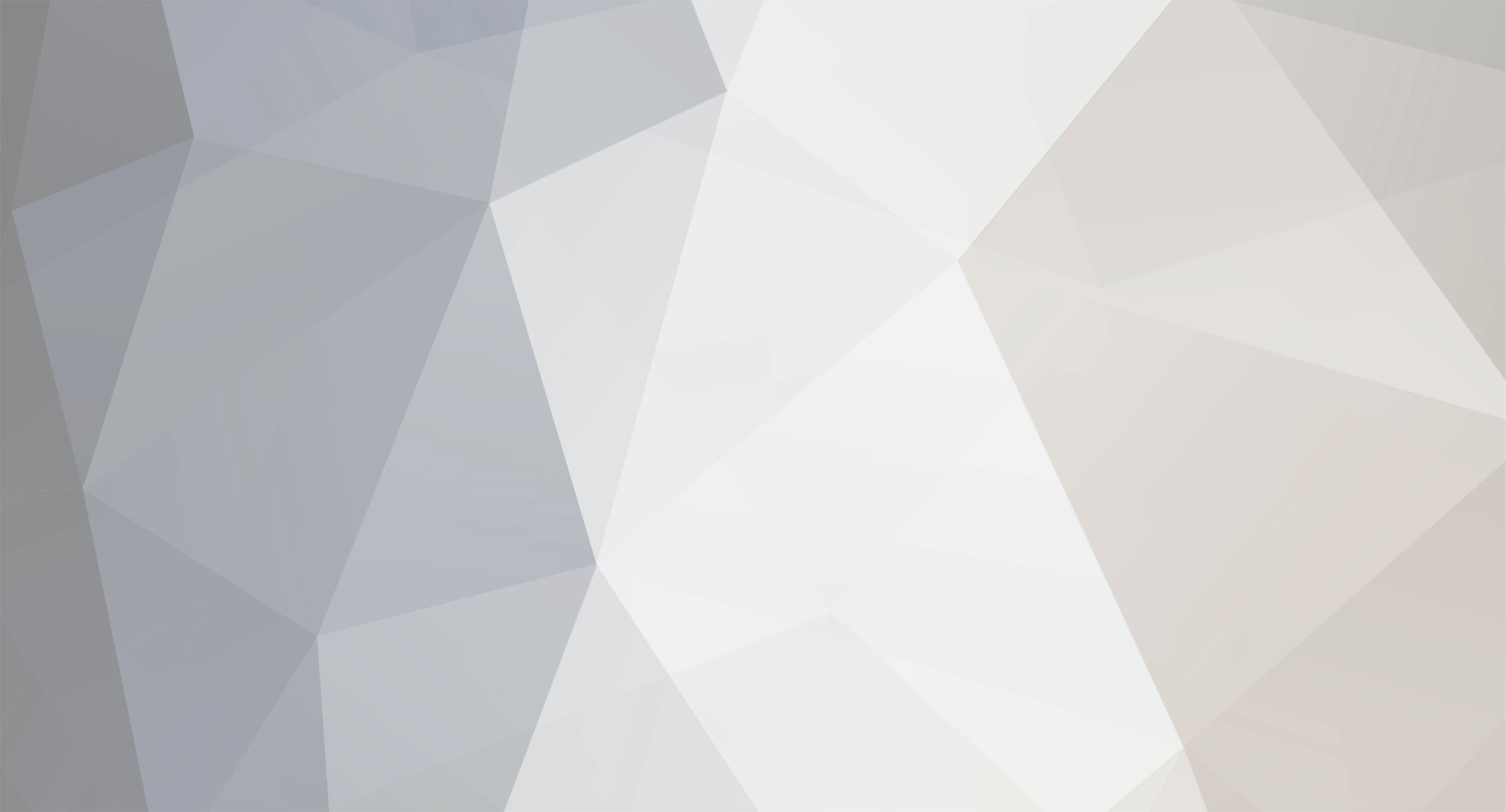
Bob77
Members-
Posts
67 -
Joined
-
Last visited
Recent Profile Visitors
The recent visitors block is disabled and is not being shown to other users.
Bob77's Achievements

Member (3/5)
7
Reputation
-
@rhymecheat I'd also be interested in any update. I seem to have a very similar set-up to you (Daikin Altherma) and I am also seeing flow and return temperatures identical, i.e. zero delta T. Even though just by sticking my hand on the flow and return pipes of the UFH I can feel the difference!
-
My heat pump is capable of having two separate heating zones (plus DHW), but the installer set it all up as one zone, for reasons known only to himself. I think a lot of installers just want to keep things simple and not have to explain complex stuff, as most of their customers are probably in the gas boiler mindset. As far as I know there is no way of changing the flow temperature automatically at different times. The flow temp for a given zone is either set at a constant or on a WC curve.
-
I haven't. To be honest as we still haven't finished the renovations after more than a year the last thing I want to do is start messing with plumbing again. Just to clarify, the radiators are on a separate thermostat and pump circuit - they can and do come on independently of the downstairs UFH. So I do as you describe and have the UFH heating up overnight before the bedroom rads come on. What I don't have is a separate LWT for the UFH and the rads. The central heating water is just one temperature, set by the weather curve.
-
Well now the heating has been running a bit more, my COP still seems to be averaging about 2.7, even though the weather hasn’t been cold enough to get the flow temperature above 40C. I suppose the real test will be how warm the house stays with a lower flow temperature, and what the usage is like if we get a spell as cold as last December (when it was below zero day and night for a whole week here). Peak daily usage was over 35kWh at one stage last winter, but I hadn’t got the settings optimised then, and I think there was lots of defrosting going on.
-
Daikin Altherma constant flow errors on DHW production
Bob77 replied to Bob77's topic in Air Source Heat Pumps (ASHP)
Hi @LT2023, I just saw this message. I meant to post an update last year but evidently forgot! A Daikin engineer showed up and replaced the flow sensor and it was worked without a hitch since then. I've only had the heating coming back on for the last couple of weeks and might need to adjust the WC curve to get optimum performance but I have not had any errors. I suspect the sensor might have been damaged during installation. -
Octopus Cosy - new tariff for ASHP owners
Bob77 replied to George's topic in Air Source Heat Pumps (ASHP)
I'm still pondering whether Cosy would make sense for me. At the moment I am on Octopus variable but with Economy 7. The cheap hours during BST are 1.30am to 8.30am so breakfast usage is on cheap rate, and if I am organised I can have the washing machine on overnight and then stick the laundry in the dryer and have it done before the tariff changed. Not so easy once the clocks go back and cheap rate ends at 7.30am. The question is whether with UFH I could store enough heat overnight to keep the house nice and warm using the cheap rate. During the summer we haven't been using enough cheap rate electricity to make E7 cost-effective - it needs to be about 38% on cheap rate, IIRC, and I have only been managing 25-30%. Once the heating comes on that will change, but Cosy might still be better. I don't like the sound of the peak rate in the evenings though, as it coincides with having the oven and cooker going. -
Since last winter I have added another 170mm of insulation to the loft (and boarded above that) so the upstairs bedrooms should be warmer. I think enough heat should travel up from downstairs to keep the bedrooms comfortably warm with a lower flow temperature, so maybe before the start of the heating season I will lower the WC curve by a decent amount and wait to see if there are any complaints regarding the indoor temperature!
-
Thanks @AliG for that detailed post. I suspect that my flow temperature can come down further and I will try that out once heating season starts. Because we didn’t have the house fully insulated/airtight and still had bare concrete floors etc during the coldest weather last winter I did have the heat pump working harder to make it more comfortable. And I certainly noticed the cost - when I started monitoring the ASHP usage in January (which was less cold than December) the peak daily cost for ASHP usage alone was over £16! But that was with a flow temp of probably 50C. I will see if the house is warm enough with a flow temp in the low 40s at zero outside. The way the system is set up is with a single flow temperature for space heating which is then mixed down to feed the UFH. I don’t know is if this is standard - the ASHP can do two loops, one for radiators and one for UFH, but it was installed as one loop with a separate mixing valve which takes the UFH temperature down to about 35C. So clearly any flow temperature above 35-38C ”should” be fine for downstairs, it’s the radiators upstairs that will need a higher temperature. Plenty to experiment with this winter anyway! PS I just got back from a few days away (rest of the family were still at home) and my lowering the DHW temperature by a few degrees already seems to have boosted my COP. For the last week it is just under 2.9, and I only changed the temperature part way into that week 👍
-
We are not using anything like 300 kWh per month for hot water. Even in winter it is no more than half that, and in summer it is less than 100 kWh. I have been logging the ASHP usage since the start of the year as well as the overall electricity use. We have two children including one who is not toilet trained and so we do rather a lot of laundry and tumble drying, which doesn't help our energy usage. (This is done overnight where possible, and we do dry outside when we can). Monthly values - total usage, ASHP space, ASHP DHW, (non ASHP use in brackets) Jan 2023: 1286 kWh, 635, 147, (504) Feb 2023: 1094 kWh, 500, 136, (458) Mar 2023: 1091 kWh, 435, 125, (531) Apr 2023: 794 kWh, 220, 110, (464) May 2023: 553 kWh, 53, 100 (400) Jun 2023: 433 kWh, 5, 90 (338) Jul 2023: 405 kWh, 0, 75 (330) Actually that's quite eye-opening how little of our energy usage actually goes on heating and how much is on other stuff! Apparently the average three-bedroom household uses 2900 kWh/yr of electricity for non-heating purposes, or 242 kWh per month. We are at least 50% above that 😐 I will turn the hot water temperature down to 47C and see how it goes. (I won't tell anyone and will wait to see if there are any complaints about the hot water temperature!) Regarding the comfort vs eco setting, I had it set to the higher temperature overnight, the logic being to get the heat into the tank at cheap rate for morning showers, and then if it needs topping up during the day we can probably make do with a lower temperature. The 13,000 per year figure was our total usage, not just heating/DHW. Based on my figures above, we seem to be using around 400 kWh per month for other things, so you can probably take off 4000-5000/yr, leaving a heating/DHW demand of 8000-9000 kWh per year. Albeit that was with a lot less space to heat!
-
Allowed placement, Under a kitchen window?
Bob77 replied to Post and beam's topic in Air Source Heat Pumps (ASHP)
We had planning permission for the extension (which I was surprised to get accepted building right up to the boundary - we are on a corner plot and our side extension wall fronts right up to the pavement, less a small setback for the eaves, whereas I thought they would insist on leaving a gap). But the application did not mention the ASHP, so that was installed under PD. -
Allowed placement, Under a kitchen window?
Bob77 replied to Post and beam's topic in Air Source Heat Pumps (ASHP)
My ASHP is under the kitchen window. I now see from other threads on here that it is not in a "legal" location as it is less than 1 metre from the boundary. But neither the installer nor the planning/building control inspectors mentioned this at all. In fact the installer was going to put it backing onto our boundary fence (against the pavement) and only changes the location to the front wall of the house because the builder failed to put the concrete slab in place in time in the intended location! -
50C at -2C so it is not very often 50C. The WC has a slope of 1 so every degree above -2C outdoors, the flow temperature is 1 degree lower than 50C. Generally during the winter the outdoor temp is between say 4C and 10C which equates to a flow temperature of between 44C and 38C. I did try having the 50C point at a lower outdoor temperature (-6C) but found the house a bit cold when the outdoor temp dipped to freezing. I have the UFH controlled by timed thermostats so the heat pump is on during the cheap rate to heat up the floor in the early morning, then it is set back during the day. I was still experimenting with changing the settings during the first winter, and haven't yet worked out whether it is better to use the "storage heater" ethos of pumping a lot of heat into the slab overnight when electricity is cheaper, or to have it "always on". I have read varying opinions on this. As I say last winter we still had a non-airtight house during the coldest spell so I need to test it more now that the building is finished. It's a three-bedroom end of terrace, 1960s but we have added a side/rear extension which has almost doubled the ground floor space. Floor area is now about 1300 sq ft, up from 950 previously. Bear in mind that this is not for a full year - the ASHP was installed in October. But it does cover one whole winter, so I suppose the space heating is for a whole year, more or less. We had electric storage heating before (no gas at the property). Our total annual electricity consumption was typically around 13,000 kWh in previous years, but I am not sure what proportion of this was space heating. The MCS estimate quoted annual energy requirements of 13,775 kWh for heating and 4,270 kWh for hot water - a total of 18,045 kWh which is clearly far more than we were actually using, but that was based on the larger footprint including the extension. Edit: I just had a look at the EPC and it reckons the house should need 8,098 kWh per year for heating and 2,943 kWh per year for hot water. So basically 11,000 kWh. We are certainly using less electricity than previously, even with the much larger house. Every month since we moved back in has seen lower consumption than the same month the previous year. Monthly values (previous year in brackets) Oct 2022: 599 kWh (639) Nov 2022: 841 kWh (1178) Dec 2022: 1293 kWh (1342) Jan 2023: 1286 kWh (1753) Feb 2023: 1094 kWh (1457) Mar 2023: 1091 kWh (1147) Apr 2023: 794 kWh (860) May 2023: 553 kWh (786) Jun 2023: 433 kWh (605) Jul 2023: 405 kWh (440) So I am not unhappy with the cost of running the system - it is clearly a lot cheaper than the old storage heaters, and much better in terms of maintaining a constant temperature rather than the old heaters which would be "boiling in the morning, run out of heat in the evening". I am just curious why the COP figures seem low. I know that some heat pumps report the "heat produced" as the additional heat produced (i.e. on top of the energy input), which means you have to add 1 to the apparent COP. But I am pretty sure that Daikin doesn't report this way.
-
Thanks for the replies, everyone. As far as I can see there is no setting for flow temperature for DHW, only the tank target temperature. I have checked my WC settings - it is a two-point curve (if two points can form a curve!) with flow temp 50C at outdoor temp of -2C and 25C at outdoor temp of 23C. But as I say the space heating mode is off completely at the moment. We have UFH downstairs and rads (new and sized for the ASHP) upstairs. The DHW is set with only two periods when it comes on - one overnight (to hit the higher temp) and a reheat in the afternoon to hit the lower temp. It is also set to reheat if the tank temperature drops below 40C but that only tends to happen if we have multiple baths or showers. Generally it only comes on during the scheduled hours. The back-up immersion heater shows zero hours of usage so it's not that. I will take the tank temperature down a few degrees and see if that improves matters.
-
The tank target temperature (which I assume is the same as the flow temperature for DHW?) is set to 51C, and 47C for the "eco" secondary reheat during the day which is not always needed. I will add the WC curve settings on here shortly - the unit is in the airing cupboard which is in our bedroom and I will lose points if I disturb my wife from her Sunday lie-in 🙂 But presumably WC is is irrelevant to the COP I am getting for the DHW? I am curious what COP people are getting in summer for DHW only. Is the warmer outside air offset by the higher flow temperature needed, which reduces the efficiency? I wonder whether I should be heating the water during the daytime in summer rather than overnight. I have always done it overnight as we are still on Economy 7, but I am wondering whether to switch away from that. At the moment we use about 35-40% of our electricity on cheap rate which is just about on the right side of break even. But if I am losing efficiency by running the DHW when it is 15C outside instead of 25C then I should switch! I've just had a smart meter fitted so more tariffs will be available to me now.
-
It's getting on for a year since I had my Daikin ASHP installed and I am wondering how my COP figures compare and whether they should be better. Since installation these are the numbers I have: Space heating: Energy in: 2753 kWh Heat produced: 6437 kWh COP: 2.34 Hot water: Energy in: 1179 kWh Heat produced: 2922 kWh COP: 2.48 I thought that 2.5 is the low end of what I should be achieving, but both numbers are lower than this. Even in the very warm month of June, with only DHW being heated, the COP only came out at 2.4. I had a problem (faulty flow sensor) when the system was first installed which meant that the unit was cycling on and off in the early part of winter but since then all seems to have been working well. I have weather compensation active when the heating is on, but the heating mode has been switched off since the beginning of June. During the cold part of winter we had building work going on and large holes in the wall, so the unit would have been working very hard back then, which I thought was to blame for the poor COP. I assumed that DHW operation during the warm months should improve my average COP but that doesn't seem to be the case. Tank temperature is set to 51C (comfort) and 47C (eco), and the unit is set on "schedule + reheat", i.e. it will heat up to the comfort temperature overnight and then heat up to the eco temperature in the afternoon, but will also reheat if the tank gets depleted during the day. Should the COP be higher for hot water at this time of year? Are my tank temperatures too high? The water from the hot tap is never "too hot" for domestic use (so can't be coming out at 50C!).