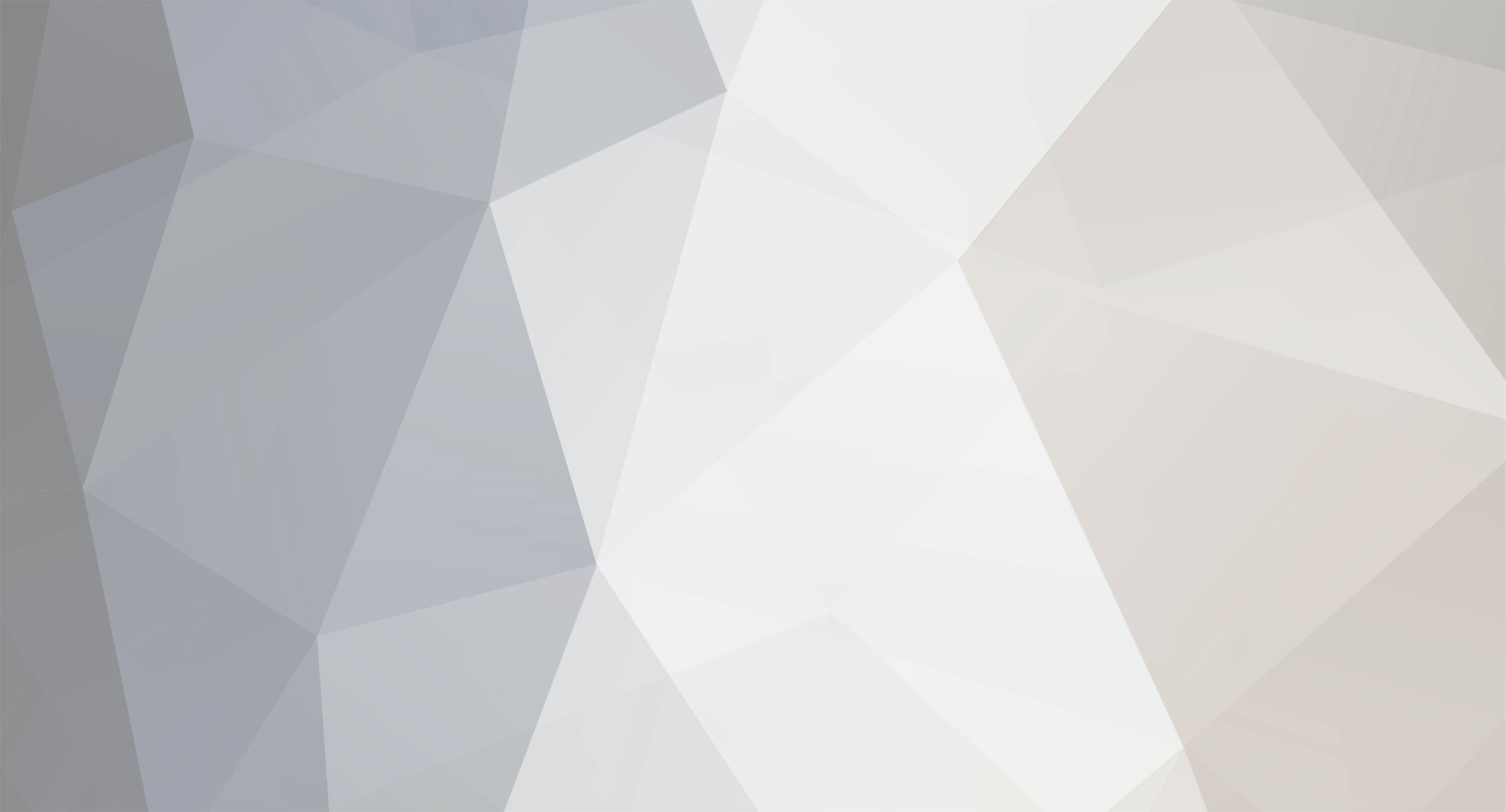
RJHumphrey
Members-
Posts
21 -
Joined
-
Last visited
Recent Profile Visitors
The recent visitors block is disabled and is not being shown to other users.
RJHumphrey's Achievements

Member (3/5)
0
Reputation
-
What Sewage treatment plant did you install?
-
Yes Russell Griffiths, that removed the worry of additional weight on the tank. Did you pour this in stages.
-
Thanks for your replies, I would have been more comfortable if I wasn’t adding the chamber riser (supplied by the manufacturer) so approx 1.5 metre of backfill on top of the tank. The tank isn’t going anywhere as enough concrete has been poured to secure it in place, up to the same level as you Joe90, where there is a route for any groundwater/ rainwater to naturally flow away, just concerned about the additional weight required to bring the ground level up to chamber level. I have phoned the supplier who is putting me in contact with the rep, but can’t see him knowing much about installation, may be proved wrong. Did think about adding lintels across the tank to support the weight, but is this overkill, and are these designed to be in the wet ground for years, if they were to fail it would be game over for the tank.
-
Hello, There are no dig repair options available, this all depends on the extent of the damage, there are liners that can be inverted into sewers from manhole chambers, which effectively gives you a new pipe inside the existing pipe, also cutters to remove obstructions from within the pipe, As long as you have access, you did mention a chamber. slightly off subject, I am working on a job where a homeowner has lived in a property for a number of years and just started having issues with the shared sewer running under the property. Water company survey the drain and identify a steel pile driven through it. This pile was installed when the previous owner had work done to support the bay window 20 years earlier, the new home owner is liable for the costs to remove this pile. Lesson learnt by me, survey sewers prior to purchasing a property. YouTube sewer lining. hope this helps.
-
Hello, just wondering about others thoughts on my current predicament. I have installed a Marsh Ensign 6 sewage plant and poured concrete up to the outlet level, as per installation advice, but now slightly confused on my next steps. In the installation sheet supplied it states if the ground is free draining, pea shingle can be used to backfill around the tank, but I have some concerns, obviously above the outlet level the tank is not provided support from the water inside, I also plan to use the supplied manhole riser which could add up to 1m of additional weight on the sewage plant from backfill to reach the cover height. Am I worrying about nothing? I did contact the manufacturer for advice, but felt a little fobbed off with their response, ‘as they can’t comment on individual sites as the ground conditions all differ’ I have visions of adding the backfill and the tank imploding, any advice gratefully received. thanks, Ryan
-
I need to support the first floor joists, so this is the reason for the stud walls, rightly or wrongly, I wanted to keep the timber off the stone walls, as the battens I removed from the walls when i first stsrted stripping the building weren't in great condtion, rotten and wet, i coulndnt deternine the cause for this, possibly from the leaking roof or moisture from the walls. There are examples of wood fibre wall make up with cavity, see examples below, these are timber clad, but principle is similar. I know this is a more expensive option, but I do think the woodfibre will manage any internal moisture, and reduce the risk of condensation better than a vcl and non breathable insulation route.
-
What route did you take?
-
What's the theory behind woodfibre rather than celotex etc, given that its isolated from the main building? Surely thats just more expensive? What constitutes "extreme" regarding the weather? Rain? Hello Roger, I like this about a forum, where people challenge others decisions/ideas, this is not a sarcastic comment, as this makes me revisit my decision process and potentially stops me making a costly mistake. My understanding is that a breathable wall makeup regulates internal temperstures, assists with the movement of internal moisture through the wall to the vented cavity, which should prevent mold growth. I have pasted a few snippets from the internet below, I am no weather expert but I have experienced the changeable weather while working on the property, including heavy rain, snow and sunshine all in one day. no doubt there are stats online for most locations the uk, but the rear of the property is exposed and you can see the driven rain hitting the walls. The chapel is located close to the Sennybridge weather station. Parts of the UK experienced the coldest night of the season on Tuesday, with temperatures of -9.4C (15F) recorded in the village of Sennybridge, Powys, The deepest snow recorded was 30 cm (12in) in Sennybridge, near Brecon, while High Wycombe saw 17 cm. The second named storm of the 2018/19 season brought heavy rain with more than 56.4 mm recorded in Sennybridge, more than half a month's worth of rain.
-
Another few days of reading several threads and attached links to websites and documents, I have a better understanding of the options available when insulating a solid stone wall, and why I decided to follow the route I have. I am going down the vented cavity route with a timber stud wall insulated with wood fibre. The chapel has stood for 160 years with little/ no heating and the walls are in sound condition, this cavity will act as a similar environment to how it has stood since it was built. The newly constructed insulated stud walls will allow the internal moisture/ air to travel through into the vented cavity. There is a chance of driven rain reaching the internal side of the wall so this is another reason I haven’t fixed insulation directly to the wall, the weather is extreme where the chapel is located, I also require the stud walls to support the first floor joists and didn’t want to fix a wall plate. thanks for everyone’s input and direction to other threads. Ryan
-
Thanks for the reply, I will have a read through the old threads to see if I have missed anything, any particular one you took most from? The photo was taken just after removing the render so the stone looked a lot lighter, and better in my eyes, but after a long winter it’s not looking so good, beauty is in the eye of the beholder and at the moment I like the look of lime washed stone, as it keeps the shape of the stone visible, rather than a render, are you not a fan?
-
Ignore the gypsum internal board( will use different board finished with lime) the airtight membrane between 60mm wood fibre insulation and vented cavity, no VCL as such, not unless I seal all penetrations of the internal osb board. The VCL debate in a breathable wall is another minefield, I can find every opinion imaginable for having a VCL or not!
-
Yes lime to be used for pointing. As for the cavity, there has been no heating in the building for 20+ years and an internal corrugated bitumen lining attached to the walls, which has been removed. I have created air vents through the wall so the air will circulate in the cavity. I can monitor what is happening inside the cavity with a camera that I can insert through a vent, and will have the option to block or restrict these vents if they are causing problems. Window returns I feel are a potential weak point if not sealed and insulated correctly.
-
-
I will look at bitumen tape, just need to work out how to attach it when I lift the stud sections into place.
-
Thanks, I will have a look at the site. I am planning to leave the front un-rendered as it is relatively protected, just repoint and lime wash, the weather comes in from the back and side, which will be rendered. I have made some decisions that I have regretted, which would be too costly to reverse, and if I was to take on another project I would do differently, but that isn’t going to happen! I am ok with the cavity, as I can see the logic of the wall acting as a form of cladding, can see the benefit of the fixed direct to wall insulation and cavity route. I have read lots of threads where builders have insulated stone buildings, but can’t think of many where people that live in these properties share how they have performed, so appreciate your building performance update. I know every day is a school day, just would be good to learn from someone’s else’s mistakes, rather than my own (is this something I should of said, or kept it to myself?) it’s not all doom and gloom and I am enjoying the process…….honestly.