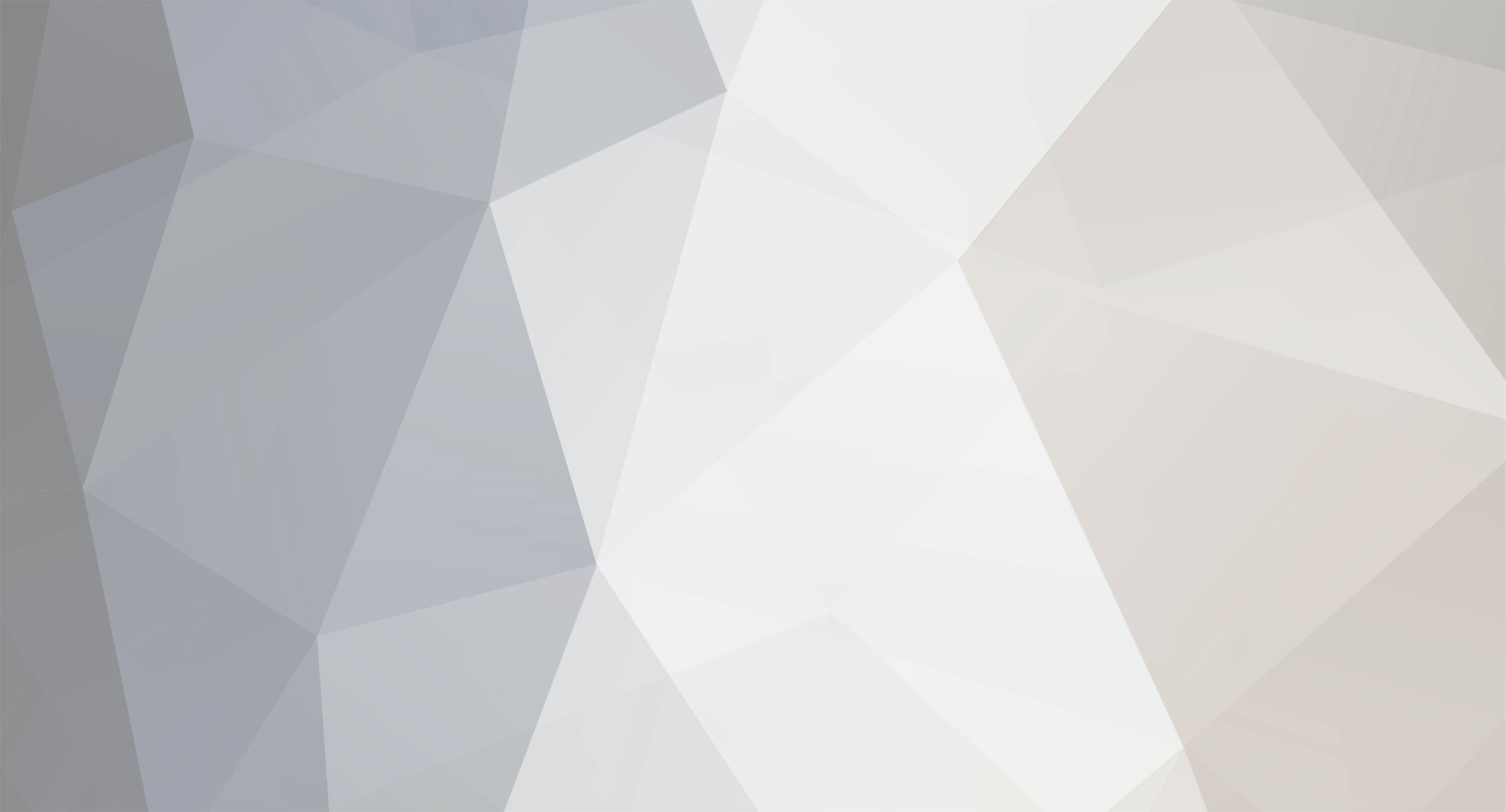
LinearPancakes
Members-
Posts
50 -
Joined
-
Last visited
Recent Profile Visitors
The recent visitors block is disabled and is not being shown to other users.
LinearPancakes's Achievements

Member (3/5)
8
Reputation
-
Thanks so much for the fast responses guys. Great suggestions. I'll run with the continuous strip approach. The existing ply will have been screwed through the membrane at stud locations anyway, so no harm adding a few more. I'll check the brackets & unit to see if I can get away with 18mm ply instead - much easier to get hold of than 15mm. I suppose fire retardant ply would be good here try to preserve the fire performance as well.
-
We have some DIY kitchens wall units to hang. They have 2x wall hanging plates per unit that are first screwed into the wall. Our wall is timber frame with air tightness membrane, 18mm plywood, 12.5mm plasterboard and ~3mm skim. The air tightness membrane is directly behind the plywood, so I don't want to screw in too far and make holes. This means 35mm long screws to account for the screw head protrusion of ~2mm. Obviously this is not a particularly long screw and only 18mm nearest the tip will be really gripping anything. Given they're heavy, slightly deeper than usual (320mm) wall units, I'm tempted to: * Cut away the plasterboard for a rectangular area around where the wall hanging plates will go * Glue and screw 15mm plywood to this area, leaving a consistent level The extra plywood would bond really well to the existing plywood behind, meaning there's 33mm of really good hold from the combined layers of plywood. But this might be overkill. I'd appreciate any insight.
-
Or.., given the challenge of installing OSB (nowhere to fix it to), a suitable size & thickness of celotex might be a good option. Could tape it to frames, side window without damage. It should help take the edge off the forces/deflection and would protect the glass from anything flying around too. 🤔
-
Obviously the window supplier said it will be fine, and referenced how they'd seen videos of this type of toughened glass bending like a banana before it cracked. They also cited previous installation of the lift & slide in costal areas with high winds. So I think the weak spot is probably the separate single window, as it has a thin aluminium frame and is not internorm, so will not have been through the same design verification process. I'll try to just not worry about it. Unless I hear of 80+ mph gusts coming, in which case I may try to find a way to fit some OSB to the outside of the single panel window. 😅
-
Thanks @Conor. I've asked for details on this topic from the window supplier. I'll report back what I find out. Hopefully, as you say, the software they used to spec out the Internorm lift & slide would have taken these things into account. The frame on the slider certainly is chunky, so not worried about the frame. The window is unfortunately not Internorm; one of the few aluminium frame windows in our build. Still triple glazed - not sure how much the layers will help, presumably a bit.
-
Thanks guys, I'll have a dig into those numbers. Sounds like the window supplier should have requested we co-ordinate with the SE, given the size of the panes involved? I guess if there's no regs for it, they'll not volunteer to do that. I admit it's just not something I'd thought about until I saw the reflections shift on the glass.
-
In the recent winds, we noticed a lot of bending on our large triple glazed panels. 1x aluminium framed window 2360x1550, 2x Internorm sliding door panels 2320x2100. We're mostly west facing, so getting a lot of direct wind in storms. We were up to 54mph gusts last night, though it has been higher in previous years. Obviously they're designed to flex, but it does make me wonder how much they'll withstand and what impact it will have on the containment of the gasses. It was pretty worrying to see. Most aspects of the building structure are designed/checked by the structural engineer, but I don't think anyone really owns checking these details. We specified the size, the window company supplied them. Any idea where I can see what the maximum rating should be? We could make some marine plywood sheets to fit externally in extreme cases, but the frames are aluminium and I wouldn't want to be screwing into that.
-
Whole House Cooling
LinearPancakes replied to sargan's topic in Mechanical Ventilation with Heat Recovery (MVHR)
Jury's still out @Nick Laslett - the unit is installed in the supply feed, but the water supply is not connected yet. Will report on any real world experiences. In the current cold snap, our upstairs rads seem to struggle a bit with the 45deg flow temp from the ASHP - probably could have done with sizing them up a little. Hoping using the ComfoPost to warm the air will help a little bit too, or at least offset the cooling due to inefficiencies in heat recovery. -
Many thanks for the responses guys. For sure the system is not balanced room-to-room. But the overall air resistance across supply vs extract is pretty balanced, and the machine appears to be adjusting the fan speed to match the flow rates anyway. My understanding is that overall extract/supply flow rates need to be matched to get optimal heat exchange performance. I double checked the connections and pretty sure they're right. It's a right hand unit, so external on the left, internal on right right like the attached picture. I called Zehnder support. He mentioned they once had a case of the bypass actuators failing. I took the front panel off and indeed the bypass actuators aren't doing anything on change - except a brief buzzing noise. From the pictures I could find, it looks like they're both stuck in bypass mode. Hence the limited heat recovery. I'll be in touch with Paul Heat Recovery (supplier) or Zehnder on Monday. Hopefully it can be repaired in place!
-
Finally got the MVHR system on yesterday after a lot of work and time. It's a Zehnder Q350 in a cold loft with terminals on the roof and Zehnder manifolds for supply/extract. Ductwork is Lindab steel with varying amounts of armaflex vapourtight insulation in the loft and on supply in the house (also have ComfoPost). Now I still have more insulating and balancing to do, but the heat recovery performance is not what I was expecting. On low (160 m3/h), seeing 21.6 degrees extract, 14.7 outdoor and 16.1 supply. The condensate drain is connected, I've ran the commission programme, covered the whole unit in mineral wood (to test), bypass is disabled. The unit seems be auto balancing the extract and supply flow rates anyway, though I did try covering supply terminals to make sure it wasn't over supplying. Any ideas?
-
You're right, thanks. I believe the last heatwave was 41deg peak and ~25% RH. So in a loft heated beyond that, the RH would be even lower. Looks like the plan for 10mm armaflex + 50mm ductwrap for extract and 25mm armaflex + 50mm ductwrap for supply will not have any significant condensation, even in worst case.
-
Our MVHR unit is going in our cold loft. To insulate the ducts I'm planning: 25mm armaflex wrap on supply ducts, as these could be cooled to ~14deg in summer due to ComfoPost 10mm armaflex wrap on extract ducts If I've modelled this correctly in Ubakus, it looks like there will still be a bit of condensation on the outside of the Armaflex in the worst case scenario (assuming heat wave, loft getting very hot). Applying a foil wrap outside the Armaflex looks like it will prevent this. Though I imagine it would be tricky to apply this well enough to provide a sufficient vapour barrier in practise. I also bought some foil faced fibreglass duct wrap that I'd planned to use outside the Armaflex to reduce heat transfer where not covered by loft insulation. But condensation skyrockets when I apply a similar setup (mineral wool). Better with foil wrap, but again, I doubt in my ability to make it a good enough vapour barrier. I find this curious, as if there's no condensation build up on the Armaflex. So my questions are: Would you expect the foil wrap outside the armaflex to help condensation that much? Will I get huge condensation issues applying the fibreglass ductwrap around the [possibly foil lined] Armaflex? I guess I could just double up to 50mm armaflex, but it's pretty expensive stuff. I was hoping 25mm Armaflex and then fibreglass ductwrap would be fine. Thanks for any insight you can give. Screenshots of Ubakus attached.
-
We've got an anhydrite based screed down that we're looking to tile shortly. Hopefully all OK from a moisture (will be testing soon) and laitance perspective. Using 1.2x1.2m porcelain tiles, wet underfloor heating and durabase matting. We had two tilers quote. One wants to use 2x coats of primer and cement based adhesive under the matting. The other wants to use 1x coat of primer and Anhyfix under the matting. From what I find online it seems maybe Anhyfix is the preferred option. Though I'm reluctant to ask the other tiler to use something he's not familiar with, and maybe the other option is perfectly fine too? To add to the confusion, Anhyfix is listed as discontinued and out of stock in a few places. 🤔 Any advice/thoughts much appreciated!
-
Non-vaulted roof, condensation risk
LinearPancakes replied to LinearPancakes's topic in Heat Insulation
OK, looking at Ubakus, as I feared, we'll get significant condensation on the membrane, if I entered it correctly: Looks like something like this would be better, and I have a good amount of 70mm Kingspan PIR lying around: