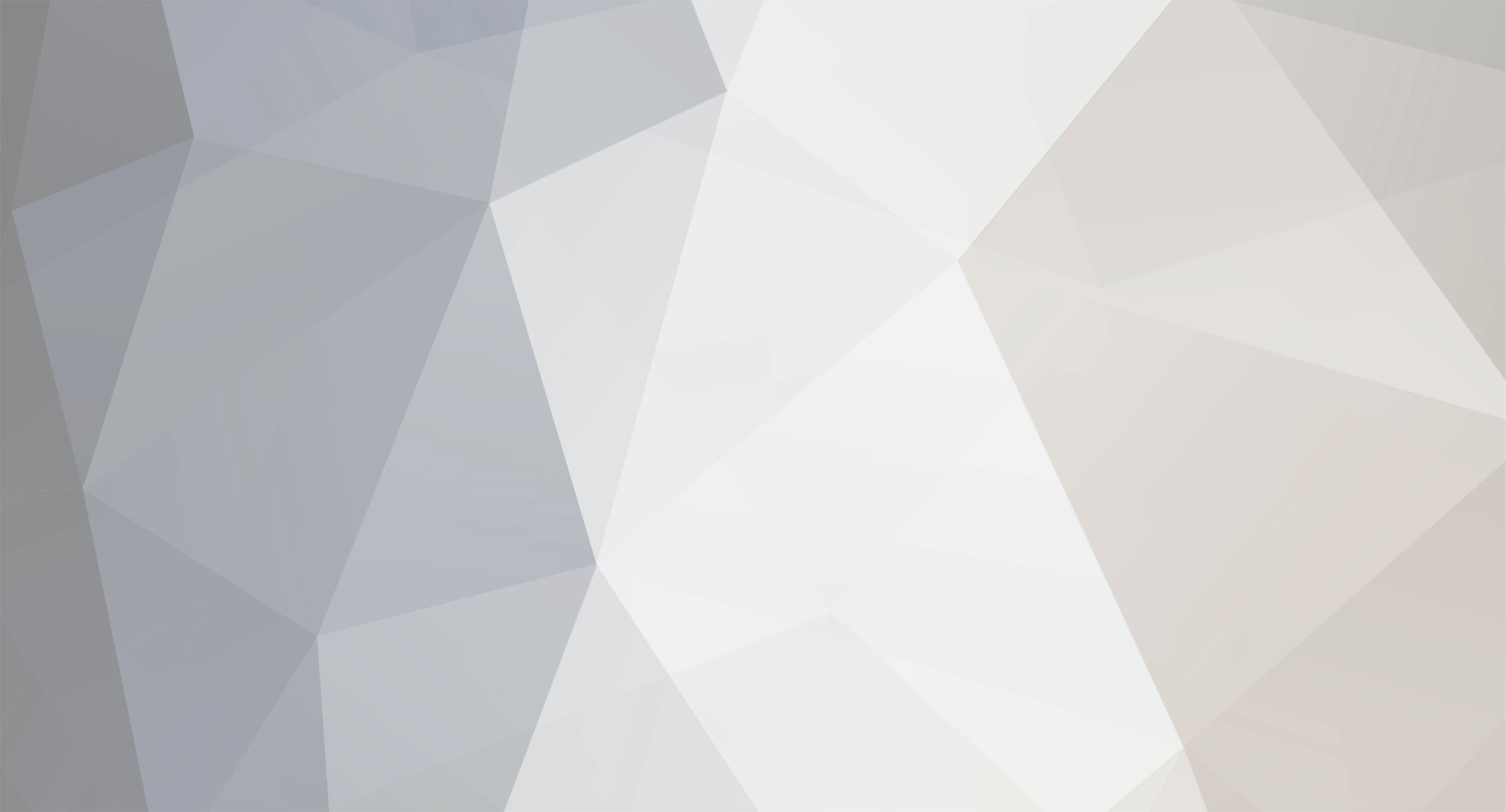
Kilt
Members-
Posts
117 -
Joined
-
Last visited
Everything posted by Kilt
-
cheers for replies.
-
In Scotland, what would be the recommend, most robust finish for transition from cope stones to slate? Seems similar arguments for a skew fillet over soakers or a Watergate, with cover flashing under the copes, leading over the soakers. I have the option for either, we current have soakers and fillet and live in a VERY exposed location. A fillet seems more robust to the wind, than flashing. Am I right in thinking when applying fillets, they should not be in-contact with the slate during curing and be separated by paper/felt/greaser. Metal lath can be added for extra strength??? Any advice would be appreciated.
-
Dot and dab foil backed 9mm PB was their answer. the worst offending area, I kicked off, as there isn’t sufficient margin for any build up. they’re coming back in spring to take window out and alter stone work for that one. .
-
A lot of the stone work is lime mortar, or soil based, so any disturbances, create massive movements. It’s all rubble/field stone, some are massive stones, so I could end up with some pretty big holes! ?
-
Looking for recommendations for insulation around window reveals. Just had new upvc sash windows put in our barn conversion, replacing rotten old ones, however the new frames are far thinner than old, (window company cockup) so im struggling with some of the reveals and getting some insulation in there. The tightest clearance is 20mm. Looking for advice. I had thought about using super quilt, but without the recommended battons, or using some insulated board of some form. I even tried Wedi board, but it’s too brittle to support a plaster finish and kids. attached photo is of one of the better reveals, I’ve been able to get battons and 20mm PIR in here.
-
Incase someone in the future searches for this, I spoke to Wedi. They say don’t use PVA, recommend SBR or a acrylic based primer. However in the same sentence they also say use whatever plaster manufacturer recommends.
-
Any recommendations for primer? Wedi say yes you can plaster onto it, but with a “suitable primer”. Anyone used one that’s worked? pva, sbr or febond blue grit?
-
Yeah that’s the major concern, even with the mvhr, there’s going to be a big difference in temp, with the kitchen next door, humidity is going to be higher
-
Short - Daft idea is to leave external rubble stone, window ingles open and on show. I’d re-point it up in lime and probably give it a few coats of a (hot) lime-wash. Long - I’ve just had 10 new windows put in, and there’s been a bit of a surprise behind one of the existing stud/PIR insulation walls. During the original conversion, they never removed enough stone on this one window opening. So the stud work was only about 20mm thick, as was the pir. The new window has thinner frames, so I’ve subsequently only 13mm to play with, between stone and window opening mechanism. Now I either take out stones/sthil saw offending stones, to give me some space, to rebuild… or a leave it open and on show. I haven’t been able to find any dot-dab insulated plasterboard, thin enough, and can go on an external wall. Issues - I have a timber kit home internally, and a cavity, so closing that off might be tricky. Window opening is close to a kitchen, so household humidity is at its highest, but we have a MVHR, so rest of house sits at around 50% humidity.
-
What to do with this mess of a concrete sill?
Kilt replied to Kilt's topic in General Self Build & DIY Discussion
-
I’ve just had a new window put in, and was checking underneath for a draft. Ive found the concrete-precast sill has no DPC or much of anything behind it. There was a load of bricks just chucked in the gap, prior to photos. The external building is a rubble-stone barn conversion, all done in lime. what should I do, back fill the sill with lime mortar, to try and minimise water ingress? no way of getting a DPC in.
-
I talked to Masons Mortar and they said no, can't be used with UPVC. I have been trying to avoid using cement on the property (18th Century, lime etc) but at this time of year, don't really know what the options are to fill the 2-30/40mm gaps.
-
Masons-mortar use 'Rosin oil' in their burnt sand. Sadly no data sheet, so will give them a call later today. Not come across 'Rosin' before, but a terrible google search pulls up not to use on plastic due to leaching (which I guess it damaging plastic), but that's if you're planning on eating the Rosin!
-
I’m assuming it’s the oil, if some of the ready-mix stuff use petroleum oil, rather than a natural base like linseed. Purely speculating. The only thing I’ve found is on a Everbuild Site for their trowel mastic, which states: ”LIMITATIONS ▪ Unsuitable for plastic frames heat absorbing glass.” but that’s petroleum based.
-
I’ve been led to believe that burnt sand mastic is detrimental to upvc, and shouldn’t be used. however I’m struggling to find any factual basis to back this up. does anyone know if this is true? I’m trying to marry up old wonky stone work and seal some newly installed windows.
-
I'm finishing off a faux chimney breast stud work around a RSJ, and a little unsure where best to place the vapour barrier. The whole RSJ is within the internal/warm side fo the building, however it is against PIR on a external wall. The existing PIR external wall had a vapour barrier upon it, which was removed along with plasterboard. I was going to reinstate the vapour barrier behind the new plasterboard, which would place the RSJ, Rockwool AMW 60 insulation on the external side of the vapour barrier. The faux chimney breast cavity and RSJ will be sat on a screed floor with UFH buried within.
-
The verbally discussed increase was a just price increase. Then when invoice has arrived that verbal discussed increase has doubled, with increases itemised. bit like a restaurant saying there’s going to be a £5 surcharge.. then when bill arrives is £10. and regarding some people are never pleased.. I take people at their word. I just don’t have bottomless pockets.
-
Their delay.. too busy.
-
that's kinda my point. It was discussed, briefly on site, but was only a 10% increase which I was more than willing to accept. I totally get that materials have gone up massively. Yeah that's what I meant by I feel I'm paying for poor planning/errors on their part, which should have been included from the start.
-
not really anything to pop up, as only the extras were itemised. Original job/price is just one line. original price was £4000 for work ( end of 2020) 50% deposit in Jan 2021 then Invoice has extra £300 for material increases and £420 for some extra equipment/labour required to lift a piece of steel.
-
price of materials was reason, but when increased mentioned, it was around a 10% increase. When invoice has arrived, that's jumped to 35%. It has been broken down, quote was from end of 2020, deposit paid Jan 2021, as mentioned if material had been ordered in Jan, surely price would have been accurate? I think materials have only been order a few weeks ago (as they've been so busy, I've had a 8 month wait for work), hence price increase. Materials could have been ordered in Jan and easily stored on site. I was under impression this was plan, but was only discussed verbally. Just feels like I'm paying for them being so busy and not factoring in material increases and having to use more labour, to ensure job happened quickly so they can move onto next job.
-
Just had some work finished, and received the invoice for the work. However its 35% higher than quotation! I'm looking for advice on the best way to approach builder on this. I appreciate materials have gone through the roof, but quote was accepted in late 2020 and deposit paid in Jan 2021, in my mind materials should be charged at that price (they could have been ordered then and delivered to site). Whilst on site I was told materials have increased, and quote may increase, but not by the final 35%. I don't want things to get heated/legal, I'm happy with the work.. but a 35% increase seems a great deal and I feel I'm paying for misjudgments in material/labour. Any advice appreciated.
-
Thanks, I might try this for the smaller gaps... but there's some weight on the joists (hence the bowing joists).
-
thanks for the Link, that's a goldmine of stuff!!
-
thanks, but it's a retrofit, so there's floors, UFH and carpet on top of the sagging joists.