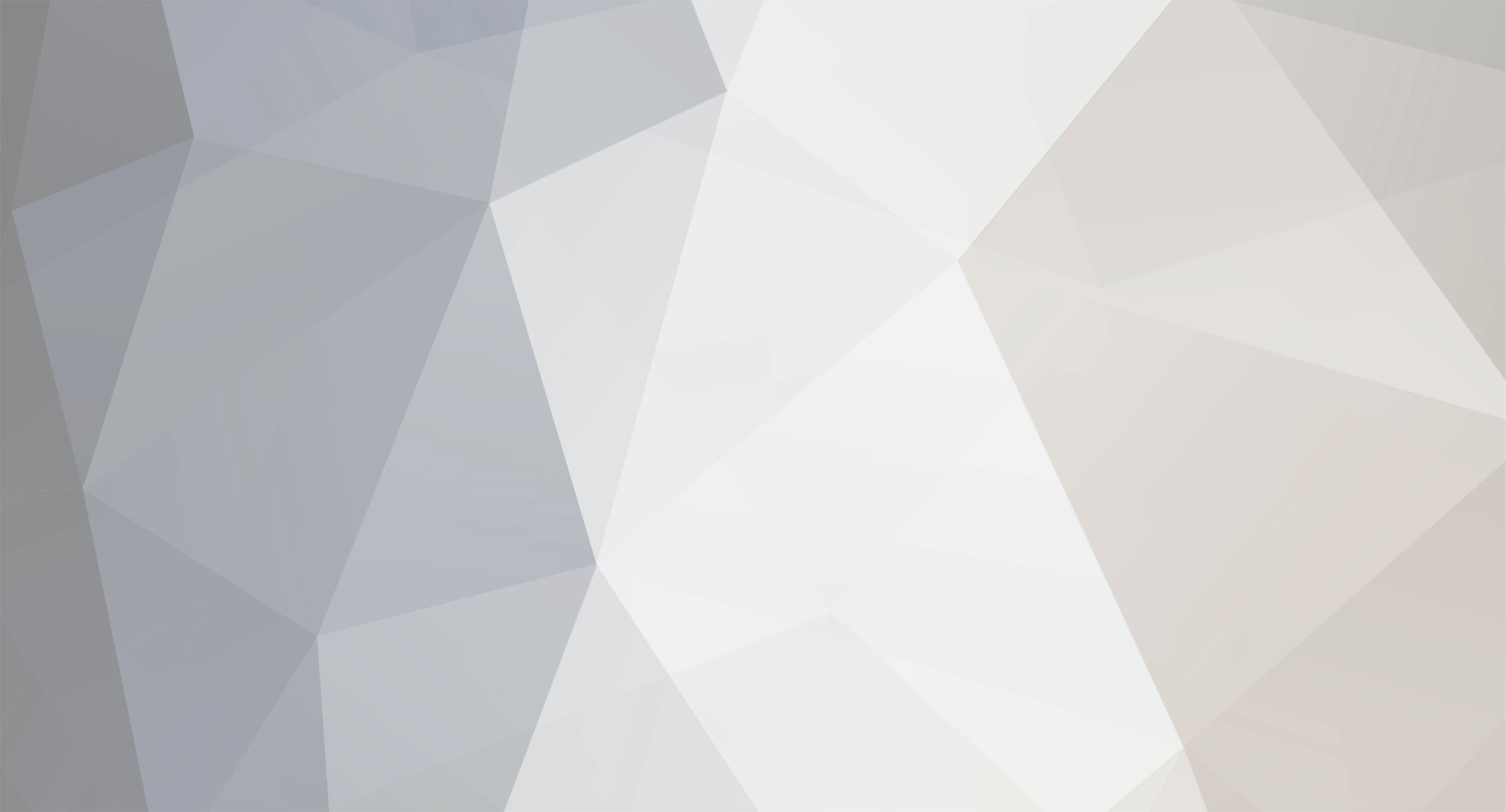
BrianWg
Members-
Posts
12 -
Joined
-
Last visited
About BrianWg
- Birthday December 21
Personal Information
-
About Me
Optimistic
-
Location
Carshalton, Surrey
Recent Profile Visitors
The recent visitors block is disabled and is not being shown to other users.
BrianWg's Achievements

Member (3/5)
0
Reputation
-
Many thanks for your comment - am I being paranoid? - The VCL is on the outer side of the rafters under the insulation so it also acts as an airtight layer - logic being that downlighters can be fitted into the plasterboard ceiling without penetrating the VCL, My fear is that by adding acoustic insulation on the inside of the VCL I create a condensation layer between the acoustic insulation and VCL - your thoughts?
- 2 replies
-
- roof insulation
- condensation
-
(and 1 more)
Tagged with:
-
Completing a self build that has an Attic room under a pitched roof, construction is over rafter VCL+120mm PIR. Site is on a busy main road and have noticed quite a lot of road noise in the room. Can I fit acoustic insulation (e.g. Rockwool) between rafters (i.e. under the VCL) or would this cause a condensation problem?
- 2 replies
-
- roof insulation
- condensation
-
(and 1 more)
Tagged with:
-
I have planning approval for a "Erection of a detached two storey dwelling with basement with car parking spaces and new vehicular access" A condition is "Prior to the commencement of development, an Energy Statement incorporating 'as-designed' Standard Assessment Procedure (SAP) outputs must be submitted to the Local Planning Authority and approved in writing which demonstrates how the proposed dwelling/s will apply the Mayor's energy hierarchy (use less energy, supply energy efficiently and use renewable energy) to achieve at least a 35% reduction in CO2 emissions below the target emission rate (TER) based on Part L1A of the 2013 Building Regulations and at least a 10% reduction in total emissions (regulated and unregulated) through on-site renewable energy generation. The development should exceed the minimum Part L1A emissions standards through energy efficiency measures alone. The development shall be carried out in accordance with the approved details and thereafter retained. Reason: To comply with Policy 31 of the Sutton Local Plan 2018. This condition is required to be precommencement to ensure that these details are considered at a early stage of the process and the required details are an integral part of the construction." I have had a SAP assessment on the design construction - but my SAP assessor has emailed me " The current documents show the nominal 2013 dwelling against your design and currently with the modified documents I sent to you, the dwelling achieves a 5.8% reduction in carbon emissions. This can be see using the Code For Sustainable Homes document. The water calc does not have an impact and the as designed air tightness target of 0.3 is already included (0.3 is very low) You don’t have a choice regarding renewable energy systems, these must be introduced to the dwelling. In my experience, the only way to achieve the 35% reduction is with a heat pump (either air source or ground source) and with solar PV on the roof. We can explore a biomass boiler to see how it performs. They are asking for an energy statement to be written demonstrating the how the design meets the requirements. This is a lengthy process which I can do for you or you can do yourself. My price to write the statement is £500. (no VAT to add) Ouch! - can anyone explain what this means to me? Is there any chance I could meet this condition without an ASHP - a ground source heat pump is out of the question as I have a very limited footprint for the plot 6 -170A Banstead Road design stage-CSH.pdf 6 -170A Banstead Road design stage-PredictedEPC.pdf 6 -170A Banstead Road design stage-SAP Input.pdf 6 -170A Banstead Road design stage-CheckList.pdf
-
Many thanks - really interesting paper - cannot find out much else. Certainly doesn't seem to be an accepted practice over here. Have emailed rawplug to find stockists and will try it.
-
Has anyone any experience of using PU mortar with concrete blocks ? Is it a realistic system for wall construction + what are the costs.
-
Self build design - sound insulation
BrianWg replied to BrianWg's topic in New House & Self Build Design
Brilliant, many many thanks -
I am building a detached basement + 2 storey home, with all internal floors & walls being timber constructed. Part E seems horrendously complicated but after many readings I think that only E2 applies and that it is only Airborne test and that my internal walls can be either as type A or B and Floor of type C This seems so simple that I am worried that I might have missed something - can anyone help put me straight?
-
All good - if Jonathan can achieve a 0.31 ACH then I am going to go for 1. Sand cement render with lime for flexibility and breathability. (Windtight layer) 2. Concrete blocks (not airtight) 3. 100mm Ursa 35 Full fill cavity batt (seems the cheapest at £5 sqm) 4. Concrete blocks ( again these are not airtight!) 5. Services chased into inner wall and sealed 6. Sand cement lime render 7. Skim plaster Joists set into hangers but with that section of blockwork having been parged before installing the hangers and hope for a similar .3 ACH
-
Have just seen a passivhaus article that indicates that blockwork can be made be made airtight as long as the entire surface is parged, so I think you guys are right and I am best to concentrate on the internal skin and leave the external as breathable. Many thank for the advice
-
From what I am reading it appears that it is difficult to create an airtight seal on the internal wall - as there are either cable runs/switches/sockets + joists and so on that have to be effectively sealed or you line it with a dpm and create a false stud wall to enclose all of the services. The latter will take off a precious 50mm or so of room on the outside walls and the former seems like a lot of fussy work with a great risk of leakages Am I overestimating the problems with an internal approach?
-
Just found "https://www.labcwarranty.co.uk/blog/weep-holes-in-rendered-walls-when-are-they-required/" which states "Whilst render potentially offers additional protection some water penetration will still occur. As a result it is important in rendered masonry walls that cavity trays are installed with stop-ends over openings and lower level abutments where the external wall becomes the internal wall. However, because of the increased protection offered by render British Standards state, “weep holes need not be provided if walls have a rendered external finish." This relaxation is based on the assumption that the small amount of water that may penetrate the outer leaf and collect in the cavity tray will dissipate by natural ventilation. This exception only applies when there is no unrendered brickwork above the rendered section." So this seems to indicate that I can avoid weepholes and therefore make a continuous layer that could be airtight. But any ideas of how I make the render airtight?
-
I am planning a self-build on a plot that I have approval for a two-storey detached house with basement. The structure is a traditional tiled roof on full fill cavity blockwork walls, rendered on outside and painted, with an external footprint of 7.5 x 9m. Looking at air tightness I can find many guides and products that relate to the sealing the internal structure but I cannot find anything that relates to sealing the externals. My thought is to use the external render to provide the airtight seal, but I cannot find any articles that either promote or dispute this approach. Surely it must be the best solution for as long as the doors/windows and service entries are sealed, whatever happens with electricals/plumbing etc inside is then irrelevant. I would be grateful for any comment or views as to whether this approach will work or not.