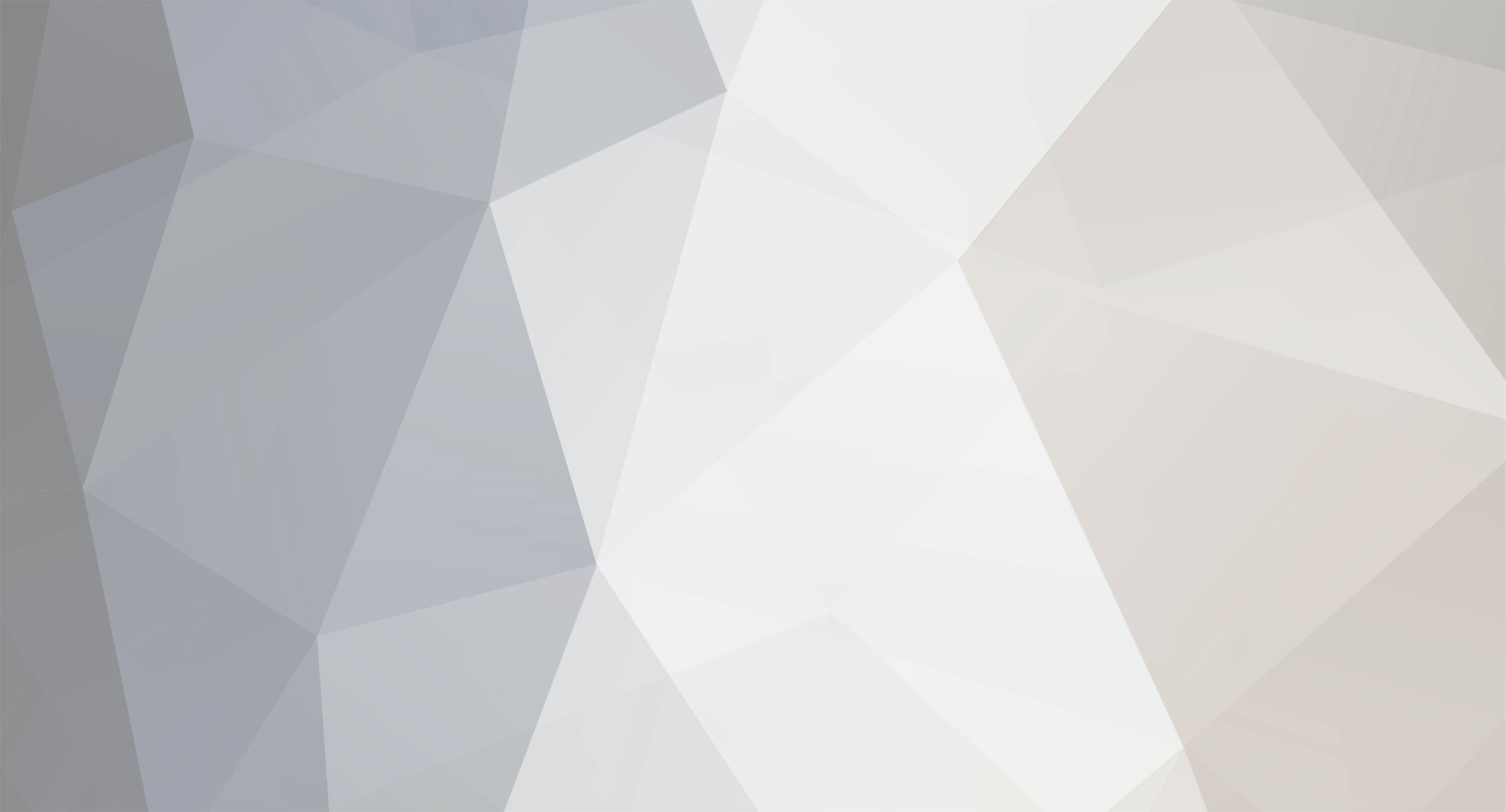
Bigdeadbadger
Members-
Posts
19 -
Joined
-
Last visited
Recent Profile Visitors
The recent visitors block is disabled and is not being shown to other users.
Bigdeadbadger's Achievements

Member (3/5)
7
Reputation
-
How to lap DPC - up or down - complex junction
Bigdeadbadger replied to Bigdeadbadger's topic in Damp & DPCs
Here is the "professional" version of the above (prior to gas membrane changes) , which is to scale, which is advocating for lap up approach. The EPS upstand is 150mm wide. The SIPS panel 217mm. I'm not keen on this lap up as any condensation has no way out, never mind water from rain. Hence the ask for collective wisdom. -
How to lap DPC - up or down - complex junction
Bigdeadbadger replied to Bigdeadbadger's topic in Damp & DPCs
-
How to lap DPC - up or down - complex junction
Bigdeadbadger replied to Bigdeadbadger's topic in Damp & DPCs
Here you go. It's not the paper I'm that worried about. That can easily lap down the wall and over the top of the EPS upstand (and another layer lapped under that one and behind the EPS upstand if needed) which will direct all water out from above. Due to the upstand there is no classic cavity or way out for water that’s at the DPC level -
How to lap DPC - up or down - complex junction
Bigdeadbadger replied to Bigdeadbadger's topic in Damp & DPCs
-
Was looking to borrow the collective experience of the forum on how to manage my DPC lapping. buildup is SIPS kit (so Osb outer) protec tf200 dpc sitting on insulated concrete slab with custom/extra upstand to insulate the soleplate. My dilemma is 1) whether to lap the DPC up the osb, behind the tf200? 2) or lap it down into the channel for the slab upstand. option 1 seems to have drawback of making a dpc bath for the sole plate leaving water no where to go. option 2 pushes the water into this Chanel also with no where to go. i can’t easily breach the outside layer of the insulated slab (with weep holes etc) as I also have a gas membrane which laps up the side of the slab insulation and upstand. Noting the gas membrane doesn’t need to attach to the house. I have BC sign off that it can stop at the top of the upstand. More pics in next post
-
Self build mortgage costings with our without VAT
Bigdeadbadger replied to PSC88's topic in Self Build Mortgages
Sorry for the delay, I reached out to individual trades. Used things like my SAP calcs and drawings to share dimensions / volumes etc for various bits of work. Was tedious to say the least -
Self build mortgage costings with our without VAT
Bigdeadbadger replied to PSC88's topic in Self Build Mortgages
Ecology made me do my most recent set including VAT and 10% contingency on top of that. Even though I showed them confirmation from suppliers that they would zero rate (for supply/install) -
I know there is a lot of love in here for Ecology, and it seems like they are back doing self build mortgages, however I wanted to raise awareness of my scenario which painfully affected my build. As with many providers, Ecology support a valuation based system where a 3rd party valuer inspects your build and approximates it worth as the build progresses. Simple. Well, not always. In my case, after completing my foundations (which were pretty extensive - insulated slab @200m2, 22KL water harvesting tank, gas membrane etc etc), Ecology's valuer suggested "irrespective of the cost of the work done, if we were to sell the site on the open market, a builder might rip out all works done to date". This position basically stunted the size of my next drawdown to being effectively useless, as they would not recognise the vast majority of the 6 figure sum to do the works as having had any material value on the site 😲 Why is this important? because it is compounded when you have a kit type build (like SIPS in my case). Which they also cannot recognise value from util the kit is fully erected, yet requires you to pay heavy upfront payments during its manufacture and then also costs to install. The nett effect of all of this is, Ecology only lent funds based on the original value of my plot, and then nothing until my founds were complete and SIPS kit fully erected. Now clearly, depending on the size and scale of your build, and the value of your plot, this funding gap may be easy to close yourself. However, I would hazard for most builds this is running easily into tens of thousands of pounds and more likely into hundreds of thousands of pounds. I certainly know, this was not the volume of cash flow I had anticipated I would have needed based on the Ecology story, and is still having ramifications as I try to fund Window deposits whilst having largely self funded all the way to getting my kit up. So, just something to factor in as you try to figure out your cashflow, and when Ecology might allow you to draw down.
-
- 2
-
-
The goal of this thread is to try and share topics for people to consider both in terms of their SIPS company and the SIPS system. I have tried to keep emotions out and try to structure the information so that it reads OK. However I'm sure some parts may appear random. Your mileage may vary and not all SIPS companies, and SIPS systems are the same. Likewise some of these situations could equally apply to non SIPS builds and just be good practice, however I would encourage the following: For many self builders, this will be their first time building a home (myself included) and therefore having the right things to look out for can be pretty useful. For context, my build was less modest than @G and J at over 300m2. 1) Understand how their contract is structured (and why). This is not the SIPS companies' first rodeo. Your SIPS company may want to sign you up for ‘Design’, ’Fabrication’ and ‘Install’. As a self builder, this can sound appealing as it means all this complexity is dealt with by one company and a single point for you the self builder to deal with. They may even offer to use their own appointed Structural Engineers as well. In this model, there are 2 key risks to watch out for. Firstly, their goal is not necessarily to design the physical house as you want, their goal is to design a structure that meets regulations, to the lowest cost/highest margin possible to them. So when discussions arise over compromises in the design, what you may find is that this package deal is compromised so you are the one making compromises. The 2nd and related risk is, they will load the contract with substantial fiscal penalties for withdrawal - such that your leverage to walk away from a design you many not be 100% happy with is left at almost zero. Same goes for using their Structural Engineers, as in this model, they are working for the SIPS company, not you. So their interest is in keeping their client happy - which is the SIPS company. So what can you do to avoid this? Break the contract down into smaller chunks that allow you to exit if your needs are not met. This will be a common theme in this feedback, but you need to be prepared that this will take time to negotiate and you need to be prepared that they may refuse and therefore prolong your search for a SIPS company. Same goes for the SE, find your own structural engineers who work for You - the paying customer. Granted, exiting at this point will still have a cost, but it is far far smaller than the potential penalties over the whole package value. 2) Design compromises, Steel and Timber vs SIPS public image In my experience, the value proposition of SIPS for large open spans and vaulted ceilings - especially on our 2nd floor did not reflect reality. What we ended up with was effectively a steel structure holding up SIPS panels. This was with even modest room widths (4.5m) and a 35degree pitch roof. (I will come back to steel later in the install topics). This room has both a Steel ridge and 2xSteel rafters, and its overall floor area is 20m2, so not particularly big. These steel components - more so the rafters, represent lovely cold bridges down through your SIPS envelope. In addition to this, what you may see in the pictures relating to joining your SIPS panels is the SIPS splines. In reality, what you may see is the splines replaced with timber. Again, some of this will be by engineering need, however in my case I have more timber than splines. Especially on my roof. This giving me in many places an effective width of 4 joists between SIPS panels (timber spline:rafter:rafter:timber spline). So again, rather than a complete SIPS envelop, you are left with more lovely cold bridges which will need more insulation (internal layer of PIR) to compensate, even with the thickest of SIPS panels - thus defeating a huge point of why you may have selected SIPS in the first place. How to avoid this? Again this goes back to contracts and breaking out at least the design phase as a single entity. That way you have a chance to force more of these topics and leverage to walk away. Ask for examples of final fabrication designs that are similar to yours (in terms of scale/size) BEFORE signing up. The final fabrication is important, as this is where the rubber hits the road and you can see how they intent to fabricate the kit. 3) Installation What you may find is your SIPS installers have no affiliation with your SIPS company and there may be several layers of subcontractors used, potentially ones that have never installed SIPS or worked for your SIPS Company before. In my experience, my SIPS company were an abject failure in managing the install team. Those failures were not limited to: No formal project planning of the install, around when installers would (or would not be) on site, what sequence of install events needed to happen in what order, how installers were paid, how long the install would take and large gaps between reviewing install accuracy and completeness. The net effect of this is that it is YOU that is left to manage the install team, and subsequent impacts and fall outs from install issues. 4) Scaffolding (and other ancillary dependencies like plant) Your SIPS Install team will need scaffolding to complete the install. Demand a scaffolding plan from the SIPS company a minimum of 6 weeks before install is due to start. That plan at minimum should cover the number of lifts, any initial gaps for access, at what stage in the build additional lifts may be needed. Going back to point 3) my experience was that the first time the install team looked at my design and any complexity was 1 week prior to arrival, where a long list of pre-requisite expectations were then given - over and above the pre-flight install checks I had already completed with the SIPS company. This is because in my experience, the SIPS company basically scoured the UK to find "anyone" who might be available to install a SIPS kit (more on this coming). The net effect of this is delays to your program - I had to get scaffolding basically at a weeks notice which then puts the pressure back on you and compromises how thorough you can be in securing those services. Furthermore, once install commences, demand ongoing updated scaffolding plans to reflect any changes they might need in advance (with a minimum 1 weeks notice). In my experience, my installers planned only from one day to the next. Meaning they could ask for scaffolding changes almost every other day. This requires you to then get your scaffolding company on a hotline - and costs a ton of money. As I'm sure applies to many of us, our designs are not square boxes, again, part of the value prop for SIPS was for creating interesting shapes, roof overhangs etc, all of which make scaffolding more complex than a square box new build from a major house builder. So there is an understanding that modifications in the scaffolding will be needed. However these cannot be managed on a day to day basis. 5) Timelines - Plant machinery Demand from the SIPS company a contractual timeline for the install. This needs to be done at the beginning of the engagement with your SIPS company. They wont like this, because it forces them to think and try and evaluate risk early on in their work and have methods to hold their subcontracting installers to account, which they are not used to doing. The numbers they generally provide are based on an average build and where everything has run smoothly. DO NOT assume this will be the case. It was not for me, and I know not for others as well. Any notion of a 4 week build for the kit is not realistic. Something large and complex may be something like 16 weeks of install time. This timing and planning directly relates to plant and machine hire (although I acknowledge there are other knock on impacts for when follow on trades can start and your overall build plan). DO NOT assume the responsibility for plant hire (cranes and telehandlers), push this back onto the SIPS company. Why? because when it's on you, you will be amazed how little bother is given to how efficiently this plant is used, whether it's busy or idle. Likewise when someone else is paying, the need to be specific in what is required is replaced by asks for the biggest (and therefore most expensive) equipment that takes any challenge off the install team. And of course, if the install takes longer, its you picking up the tab. Part of this experience is based on hearing about installers who more frequently work on building sites, where multiple houses are being erected, at different stages. Meaning they can hop between installs as they wait for something, or some dependency to be cleared. So on those builds, the equipment always looks busy as it's serving multiple builds and a) they don't give it a second thought to the use of the plant and b) they always expect it to be there waiting on them on tap. This is obviously not the case on a single self build (i.e. most of us). 6) Installer competencies Following on from my earlier comments around the volume of steel in my build. My installers had limited experience of installing steel at this complexity or volume (~70 individual steel pieces). I would have been bettered served with a dedicated steel install team. Why? My install team could not set out where steels would be placed, and therefore worked on a model, where a steel was placed, then SIPS walls added, until they needed the next steel in place. This stepwise fashion of steel, sips, sips, sips ... N+1 then steel meant the hired crane sat idle for most of the day(s) rather than placing as many steels into place as possible. Even simple concepts like pre-erecting joined steels on the ground prior to lifting was unknown to the install team, thus meaning each steel was lifted one at a time. Furthermore, this stepwise method prevented the steels from being bolted and levelled until after all panels were installed. This leads to panels covering over the steel pads and holes for bolting, which then leads to large sections of SIPS panels needing to be removed at a later date to access these bolt holes! What is most galling over this scenario (beyond the wasted crane time), is the tolerances that the SIPS company demand for your slab (+/- 10mm over 10m), yet they could not accurately place steels without this step wise build method. 7) Marking their own homework You may find there is no "formal" or "accredited" sign off for your installation. That process is an internal one where your SIPS company effectively self certifies their install is in line with the approved design (you can already probably guess where this heads). As the client - you need to find other ways (either yourself or through other professionals) to mark their homework. In my scenario (I ultimately feel lucky) I caught structural defects in the installation method BEFORE it was too late. This is especially challenging when some build parts do go quickly and large swathes of a building go up before you might get a chance to check. Those defects resulted (painfully) in a 2 month wait for the SIPS company to acknowledge (and no progress on site), and then further install delays as they removed panels and re-installed correctly. Roofing and Wall membranes can hide a multitude of sins. Don't wrap the building until you are happy. 8 ) Foam or no foam In my re-search prior to finding a SIPS company, I had never come across the idea of a dry fit SIPS kit. This is where NO foam is used during panel install, and only used sparingly at the end of the build. I came across DRY fit once my install started as that's what the SIPS company stated was their approach. This contradicts their public documents, every other kit I looked at, and also, any notion of having a (reasonably) airtight fabric. As i was doing some adjustments at the weekend to move a location for velux, here is a great example of what happens with a timber spline into a SIPS panel without foam. No whilst I know more of my kit is foamed than it may have been (as i caught it early), I know for a fact it is not consistently foamed with any quality. What can you do to avoid this? Get it in writing that the kit will be foamed on every join DURING install, and watch them like a hawk. This is probably a good place to end for the moment, needless to say, I am not a SIPS fan (for all of the above). It has brought needless delay, complexity and above all significant cost - you could realistically buy a decent home for the amount of money it has cost for this kit and its install, without any of the upsides of speed or thermal performance. I'm fully aware my experience is a sample size of 1 (with some other bits of feedback I've gathered directly) - however it is real world experience.
-
Please drop me a message and I can share my first hand experience of a 6+ figure install and the potential outcomes. whilst in principle, the design methodology has a lot in its favour, so much is dependent on the SIPS company and the install team (noting that these likely are not the same and more likely some subco’s to some subco’s). It is completely fair to say, the vision you are sold - either from Architects or the SIPS company - is not guaranteed to be the reality you will see. The concept of an airtight fabric with limited cold bridging is not a given, and unless you are abundantly aware of those limitations, there is the distinct risk that you may have the wool pulled over your eyes.
-
Thanks saveasteading, Re the ends of the building - yes, I have trenches in my design around the perimeter of the building that will allow the wind/venting up to the surface (2000mm2 per linear meter off the top of my head ) , but can only get to that as I look at backfilling in/around the slab at a later point. Cheers
-
I have just been through this very topic over the last year or so in Central Scotland. First recommendation - challenge everything. My experience here is that the "worst" case scenario is typically assumed with limited justification especially from 3rd parties. In our risk adverse world, I experienced people making (faceless) choices based on those worst cases vs what might actually be a more pragmatic approach. Had I challenged more - I would have saved time and money. As part of my planning application, I was required to do a phase 1 desk survey, which highlighted my plot was a low to moderate risk of unrecorded shallow mine workings (not uncommon for this area - like mentioned in earlier responses) and potential for ground gases. This outcome then placed a requirement to do an intrusive phase 2 site investigation as part of my planning conditions - including 6x boreholes for ground gas monitoring. Based on the phase 1 desk survey, my site was allocated an initial CS2 rating by my local councils 3rd party contaminated land consultant (noting my council outsource this work). It's at this point - I wish I had challenged more, as I feel in hindsight, this was excessive. Having obtained quotes for the phase 2 survey, a couple of things jumped out. The cost was ~£6K as per examples listed above and the monitoring period was over 3 months. Based on these costs, the potential for ground gas to be discovered anyway, and a naïve thinking I would be ready to build soon and the monitoring would hold me up, I took the decision to include a Gas Membrane in my slab design and accept a CS2 rating in Lieu of the gas monitoring. And that is where things got really fun, as for me, it was not just a case of "just" including a membrane. Instead, I had to: 1) for my building warrant, I was expected to provide a Contaminated Land Response, detailing how the Gas Membrane would be installed, and how the design met BS8485 2) not only was a membrane required to meet the points allocation needed to pass CS2, I also needed to demonstrate my slab was reinforced with minimal penetrations (pretty easy) but also then design in a passive ventilation layer below my slab (all of this is in BS8485). Giving me a points score of 4 (target was 3.5) 3) detail how the membrane would work along side my insulated raft formwork 4) provide external 3rd party validation of the membrane installation in line with CLA:IRE guidelines 5) my BC could not answer ANY questions on the topic. All discussions went via their 3rd party, had to be via a "design" and typically had a 3 week turnaround. Based on being thoroughly frustrated at this point due to many things on my build, I actually composed document 1) myself by getting hold of a copy of BS8485 and demonstrating a compliant design. I did not obtain costs for a 3rd party to do this, but I would expect low £ thousands as its (rightly) outside the scope of a SE and Architects specialization. All in all, by the time I include the Visqueen membrane, the labour, the 3rd party verification, the cost of the low fines gravel ventilation beneath my slab, I will have spent ~£10K. I sleep at night, by convincing myself that bore holes may have found ground gas, and I would have then spent and additional £6K on monitoring and I didnt spend extra on someone else designing the solution. BUT - some pictures below to show it can be done Low fines material for ventilation (this was quite expensive) - 300mm deep, 260m2 (my house is going to be quite big - ground floor at 200m2). Could be cheaper going for preformed venting sheets from the membrane manufacturers. And installed below my formwork (still to be dressed on the sides of the formwork). Excuse the mess. Hope that helps
-
Looking for Groundworkers - Central Scotland
Bigdeadbadger replied to Bigdeadbadger's topic in Foundations
Thanks for the details Kelvin, i'll give them a buzz although maybe too far for them (West Lothian) , but agree with your sentiment. Earlier searches I tried were also unfruitful because builders were (understandably) cautious about engaging before BW was approved. Now that is has been approved - it doesn't seem any easier! -
Hello BuildHub, I was looking to see if anyone had any recommendations for groundworkers in/near central Scotland - looking to start asap. Currently having limited success with cold calling - so any recommendations would be appreciated. Building Warrant in place and ready to go - insulated slab. Thanks