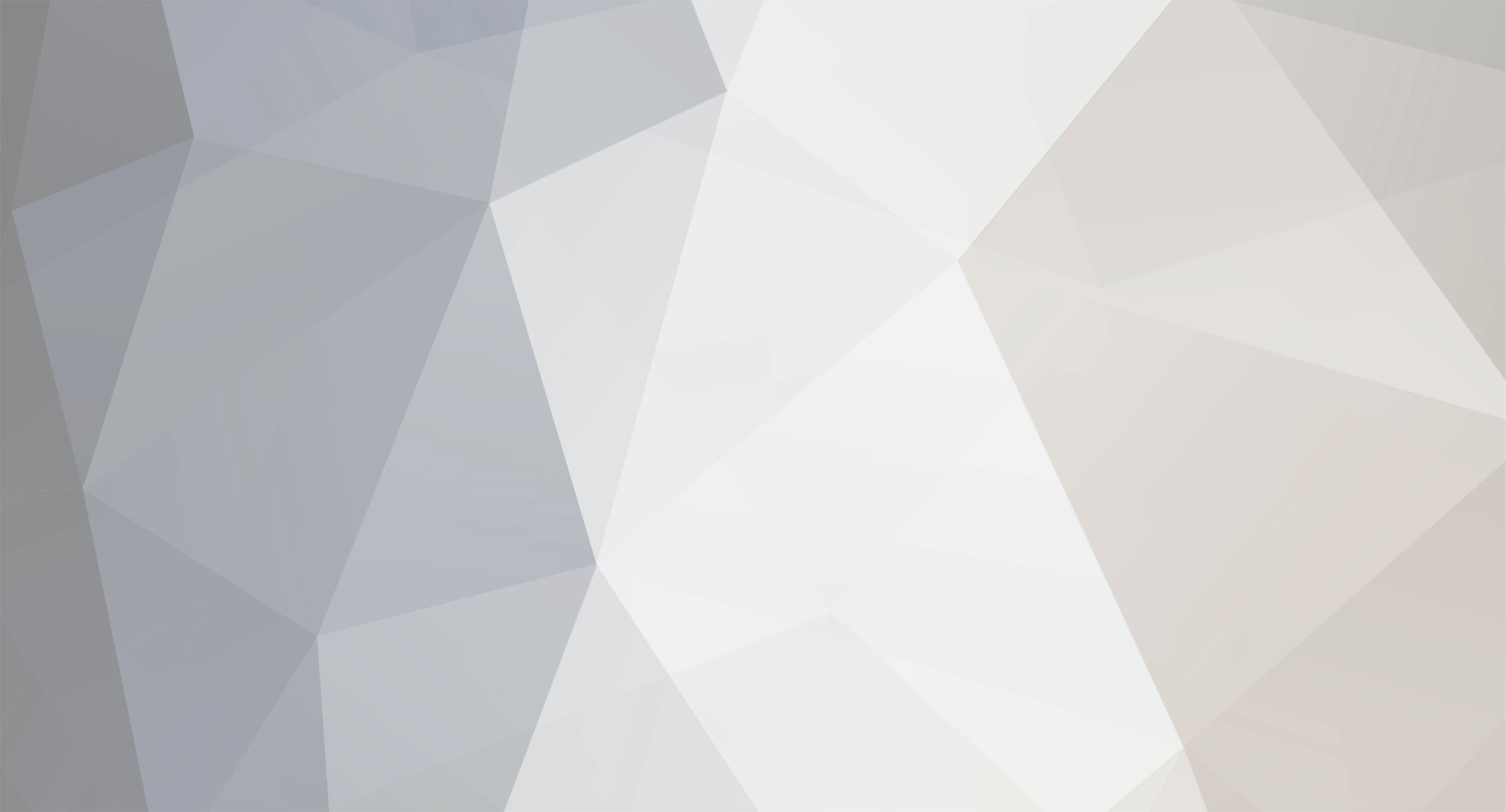
willmo
Members-
Posts
9 -
Joined
-
Last visited
willmo's Achievements

New Member (2/5)
1
Reputation
-
Lovely stuff! Thanks @Nickfromwales that's helped settle my mind. I'll set it up like that. @Onoff very interesting! Thanks for that as I was certainly going to mount it vertically. I'll either change my design or look for one that doesn't have to be horizontal. Surely it can't be due to the very slight pressure difference due to the change in height on a vertical set up
- 51 replies
-
- cold mains
- bar
-
(and 2 more)
Tagged with:
-
It's a retrofit in to our existing house with chipboard floors upstairs so I'm trying to keep them down for now.
- 51 replies
-
- cold mains
- bar
-
(and 2 more)
Tagged with:
-
Hi @Nickfromwales I have a similar situation to this comment you made. Our stopcock is in our downstairs toilet next to the utility room, and I'm hoping to get an unvented cylinder installed in our airing cupboard upstairs. I'm planning to run a 22mm feed up the soil pipe boxing, through the loft and back down to the unvented cylinder. Probably in plastic up the soil pipe, and copper across the loft. To save me running an identical feed all the way back to the downstairs toilet and utility room, can I just install a pressure reducing valve right after the stopcock, and tee off my new supply line to the UVC straight away? It would go: - 25mm main in - Stopcock - Pressure reducing valve - Tee with drain valve - Tee off to toilet/utility room. We will install a shower in the downstairs toilet, I don't know if this will change anything - Supply through loft to UVC - UVC's pressure release valve - Balanced supply to rest of house (upstairs bathrooms and kitchen) I guess it would even be worth sticking a tee before the pressure reducing valve to the outside tap.
- 51 replies
-
- cold mains
- bar
-
(and 2 more)
Tagged with:
-
Tell me about it! The original part of the house is from the 1800s, so there's not a spot of insulation in there. It's a mix of suspended floors and solid (I assume it must just be compacted earth in the kitchen). I've currently ripped the floorboards up in the suspended section for 100mm of PIR, with UFH spreader plates on top of that, and then the original floor boards on top. Along with the log burner, and 50mm insulation on the inside of the one external wall, that room should be very nice and warm. The place is draught city though, and we can't do too much about the single glazed front windows at the minute. We're currently trying to find what we allowed to do in the conservation area. Secondary glazing doesn't do a bad job though. The wooden double glazing from the 90's at the back of the house is way more draughty. Our priorities are reducing draughts, improving insulation, UFH in that order I think.
-
If only they'd put a bunch more insulation in when it was build in the 90's eh, this would be so much easier. But you make a good point on how it should be easy to pull up. Hopefully in practise it would be just as easy. I've had a little research of putting insulation directly on hardcore (with DPM in between), and then a screed. It looks feasible, as there has already been a slab down everything should be sufficiently compacted. Thanks for the help. Yep, that would be the dream goal. Thankfully we have the room to not have to use this part of the house for a good few months for any work to be done, so time wise it's fine, however we don't want to sink a load of money in to it. Do you have any idea how much something like that would cost? 5k, 10k 15? Oh wow, that's a great amount of insulation! I wish we were doing the extension from fresh, so that we could specify something just as good. The cost to add it during the build isn't a lot more, however it seems a bit wasteful to pay to rip it all out and start again.
-
I probably should have been clearer, I'm thinking we'll also need a couple of radiators in the room too - which would allow the UFH to run colder. We're thinking of a herringbone wood effect, however are not tied to wood. So tile, engineered wood or LVT are still all on the cards. I believe tile would be the best for UFH performance? That's probably the most sensible option isn't it, even if it is slightly more expensive due to the routed T&G, it will probably pay off in the future. Especially as we've got polystyrene under there at the minute, it would be good to switch that out for something more efficient. I remember seeing a post of someone who tried to route out their own T&G and said it was a nightmare. I've got a nice beefy router, but am thinking it might not be worth doing it myself. Oh wow, I've not come across that. The lack of prices online makes me think it's super expensive (looks maybe around £70 a square meter?). I'm just drawing the house up on autocad so can send it over to get a quote. Thanks!
-
Unfortunately, given the front door threshold, 30mm is the maximum we can increase Going any higher would mean moving the front door, back door, and two sets of french doors, which I assume would mean moving the lintels up etc. If we were to get stuck in to that amount of work, I think digging the slab out would also become an option.
-
I'm fully aware that there will be heat loss to the ground. So am more than happy to include radiators in the room. However we want to get away from having a freezing floor. As far as I'm aware, keeping the UFH to a lower temperature will reduce heat loss to the floor, whilst keeping the floor warm. I guess then it's the trade off of the cost of install of the wet system, vs running costs of an electric mat. I think given the area, wet might win the cost comparison. Unless there is a better way to achieve a warmer floor?
-
I'm looking to fit UFH and just can't work out the best solution. We're going to fit it in to a 60m2 extension that was build in the 90's (knocking two 30m2 rooms in to one to create a nice big open plan kitchen living room). Luckily we were left the drawings from when the extension was installed. The current floor set up is: - 150mm compacted hardcore - DPM - 100mm concrete - 40mm EPS insulation - is it worth changing this to more efficient PIR insulation whilst we're at it? - 22mm T&G chipboard - Underlay - Carpet The maximum that we'd be able to raise our floor is by an additional 30mm, due to external door thresholds etc. I'm looking for ideas on what would be the best way to install UFH. Obviously the most efficient way is to dig everything out, have a 100mm concrete slab, 125mm PIR insulation, then the UFH in a 75mm screed. However I reckon that the cost of this will be much greater than the additional heating costs by leaving the current level of insulation as is. For this reason, I'm looking at the various retrofit options out there. - Replace this chipboard with this pre routed chipboard. At £30/m2 this looks like a very expensive way of doing it, and doesn't add any additional insulation, however will not raise the floor. - Low profile UFH on top of chipboard, with self leveling compound. This would be quite an easy job, and would fit within the 30mm of extra floor height we can afford. However I don't know if it's worth upgrading the EPS insulation. - Low profile EPS/Aluminium spreader plate hybrid - Install this on the existing chip board. Adds a little extra insulation, not too expensive. Keep the exisiting PIR insulation? I just keep going round in circles. Our goal is to have a room that is efficient as possible with a nice warm floor that we can walk on in bare feet, with maybe a laminate or LVT floor finish. I'm happy to accept that this system may not meet the 4000Wish power requirement for the room, so we may need to keep a few radiators. Any help/guidance or additional ideas will be really appreciated.