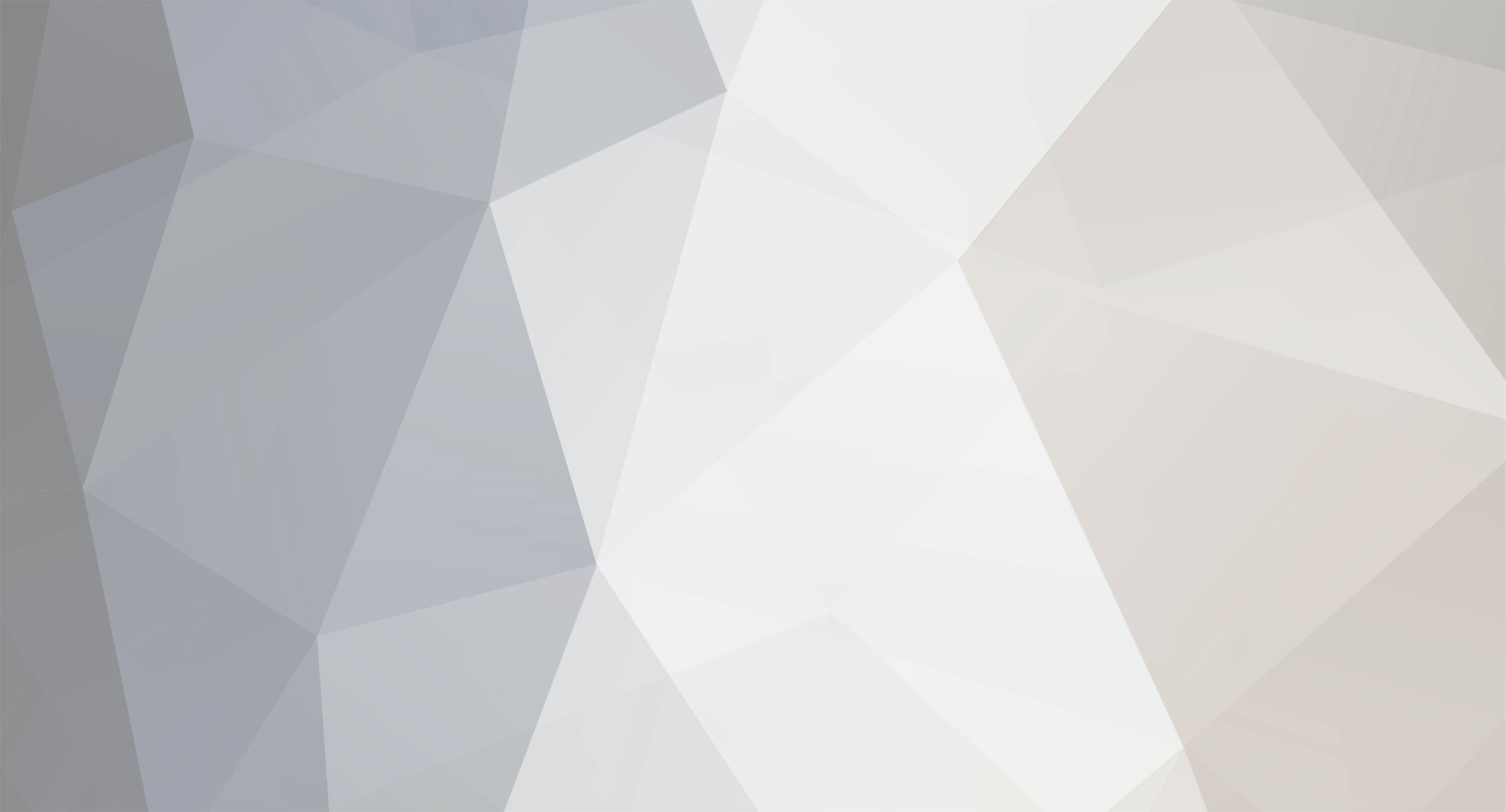
Edward
Members-
Posts
25 -
Joined
-
Last visited
Everything posted by Edward
-
Unvented. The HW taps are not connected to the HW output. The plumber confirmed the hot water control on the boiler doesn't do anything, as nothing is connected to it. Thus the HW taps are draining the cylinder, which in itself is a PITA because its a sizeable house and the taps take forever to heat up, wasting HW in the process.
-
Combi boiler heats water, which in turn heats cylinder and therefore DHW is fed from the cylinder.
-
Hi all. Just after some advice/opinion to my setup as it slightly confuses me. We have a Worcester 8000 Life combi boiler. We also have a hot water cylinder in the loft. Given the boiler has both separate heating and hot water outputs, I would have assumed the hot water cylinder would have been fed from the hot water feed from the boiler whilst the heating for the rads would be fed from the heating output. Instead the heating for the hot water cylinder is on the same circuit for the central heating system. Is this correct? Is the hot water function only for hot water on demand? I am asking because i have turned down the flow temperature from about 70 to 55 degrees to a) reduce the energy usage and b) ensure return temps allow condensing to happen. However in doing so the hot water cylinder will never get to safe temperature (legionellas). Advice welcome
-
I dont know in all honesty. We didnt want to raise the FFL when installing the UFH so the plumber had to batton the side of the joists to put the foil panels in-between said joists. There is a chance your statement could be correct however. I seem to have fixed the issue somewhat by increasing the flow through the pipes to its max. I think this prevents the high temp thermostat from being triggered. Ive decreased the mixing to compensate for the lower flow temp from my boiler. All the literature i can find says the flow should be around 1.5 - 2 l/m but this just doesn't seem to work on m setup
-
Foil backed polystyrene, I think about 50mm deep, sitting between suspended timber joists with 150mm insulation underneath. Is it an issue the boiler and pumps will be running between 4.30am and 8pm non stop whilst the system tries to reach temp?
-
Hi. I have UFH in my kitchen and it wont get to target temp of 18 degrees, max is approx 16.5 degrees according to the thermostat. The set up is as follows: Gas boiler, Grundfos pump running from boiler to manifold about 10m away, 3 circuits off manifold (1 zone so no actuators), another pump pushing water through the system. Mixer value. High temp thermostat connected. The variables i can have had changed are the pump speeds, the boiler flow temp (reduced this slightly to ensure condensing occurs), the mixer temp and the flow rates which were set at 5l/m. I first noticed the UFH didn't get up to temp when i turned the boiler flow down from about 65 to 57 degrees - which is as far as im aware still plenty hot enough to run UFH. I reduced the flow meters to about 1.5l/m as my understanding is a lower flow rate allows for a larger dT thus more heat output. However this was causing the high temp thermostat to kick in and shutting the pump off. I have now increased the mixer temp to 55 degrees (not an actual measurement, just a number on a dial) and allowed the flow rate back to 5l/m. This appears to prevent the high temp thermostat from kicking in. However the room does not get above 16.5 degrees. I am beginning to think external environmental factor are the influence as the weather is much colder and the insulation underneath the (suspended) floor probably needs inspecting. My question is what speeds should the pumps be set at, whats the optimum flow rate to allow for a sufficient dT? What influence does my mixer valve have on heat output? Any other suggestions would be welcome.
-
Ive attached an image of inside the roof. We haven't lost any tiles however a batten or two have fallen and are rotten. Ive pulled the tiles back into place but they re not securely held. How would you go about fixing this?
-
Hi just after some advice on patching a roof. Its an old house with clay tiles and no felt. A couple of tiles have slipped exposing an area about 500-800mm in length. Gaining access externally will involve scaffolding due to the proximity and height of the hole however this can easily be reached from inside the loft. Am i going to be able to make a temporary repair from inside and if so what materials should i use? I am thinking of using some flashing and some adhesive - would this be the correct materials for the job?
-
The land on our property is retained by a wall approximately 3m high, our garage sits about 1.5m away from the edge of the retaining wall. Our neighbours are proposing to extend their kitchen towards the retaining wall. Their land slopes upwards towards the wall. My best guess is that to get the necessary FFL in their extension, they will need to excavate 800mm down at the deepest point, ie the point closest to the wall. I am therefore concerned their construction could possibly cause settlement issues on our property as the foundations to the retaining wall may become undermined. Is there any rule/regulations or even guidance which covers the topic about building at the base of a retaining wall? As of yet there has been no planning permission application so there is no immediate concern, however I would just like to empower myself with this knowledge when the inevitable application does come in. I do not know how close to the wall they are looking to extend to. Thanks in advance.
-
We need to replace our roof soon. It’s not far of 100 years old, we can see daylight through the roof, it leaks, is covered in moss which the birds pick at which further damages the roof, so…. What alternatives are there to the traditional roof tile, like a composite fitting or something, which will tolerate UV, cold, snow ice and hot temperatures? I have literally no knowledge on this topic so any insight would be useful. Would you trust the advice of a roofing contractor on materials or would you request a contractor installs a material of your choice? More than likely too is that the timber frame would need replacing as I suspect it could be in a better condition.
-
The Rehau smart system, in my opinion is the most unnecessarily complex and frustrating system to get working properly. The UFH comprises of three circuits heating my kitchen, therefore no manifold, quite a straight forward setup. I can not get the app to communicate with the system, I am not sure if I have paired the thermostat with the base, when think its been turned down I can hear the system opening up and pushing water through, the instructions are hideously complex and the flow diagrams dont appear to correspond with what I see on the hardware. So before I melt down, how easy is it to swap out control system for another manufacturer? If its fairly straightforward, any recommendations?
-
Forgive me but I am a complete layman when it comes to electricity. We have in our kitchen a pendant with 8 bulbs installed, specifically these in various shapes. https://www.thelightbulb.co.uk/4watt-pear-led-es-e27-screw-cap-very-warm-white-gold-finish-equivalent-to-30watt-dimmable/ The wiring, switch, the circuit into the distribution box including the box itself is all new. We replaced the current bulbs because they buzz, however these bulbs are worse. What’s the solution? Is it likely to be a new switch? Are the bulbs not suitable? id be grateful for some insight and some product recommendations to help stop the buzz!
-
Perpendicular to this, from the house to the retaining wall
-
My original post was concerting the specification around the steel.
-
Because the current retaining wall is failing and needs replacing. I also need to raise the patio inline with the doors to reduce the drop. If i use stone and a wheelbarrow, the new wall will need significant footings to retain the stone. In my suggestion, the new wall would not be retaining anything.
-
Ok thanks. It would be my intention to remove some fill behind the wall to ensure the new wall would not be retaining anything. I was also considering removing much the fill to accept EPS blocks to make the levels. This would negate the need for a block and beam and possibly reduce the size of the footings.
-
Our current patio is ground bearing and is held in place by a retaining wall, which is failing as it has no footings. The structure is independent of the house foundations so there's no risk to the house. The patio is currently about 1.5m above the garden - we also need to raise it slightly so the step from the new doors is reduced (see picture) My solution is to remove the retaining wall and the necessary material currently being retained and create a new suspended patio using steel tied into the house and a new retaining wall. The steel will then support block and beam, to which we can then build the patio back onto using the existing York flags. The new retaining wall will have (i think) a cavity of which the steel will rest onto the blockwork, whilst we can reuse the bricks from the failing wall to finish the new wall. I have a few questions: a) How can i specify the stiffness of the new steel without the use of a structural engineer? b) Does the block and beam need a screed on top to accept mortar to then accept flags? Is there a spec for the mortar. b) how does this new steel tie into the existing house - is there a standard detail knocking around somewhere? Airbricks, DPC and drainage im comfortable with. I hope the above makes sense. Thanks.
-
Hi Hope this is the correct forum for this question. We are 80% through our renovation project. Our kitchen is the next major item to be installed. It is our intention to have brick slips on the wall which the kitchen units will rest up against. I have two questions regarding this: 1) My preferred order of works is as follows: Kitchen install > Quartz worktop and upstand measured and installed > brick slips installed, followed by mortar. Our builders order is slightly different as he wants to mortar the brick slips before the worktop is installed meaning the brick slips will be installed before the worktop and upstand. Our tiler, who is working for us not the builder, wants to install the brick slips after the worktop and upstand are in place. The builders justification is because mortar is a messy process and he must keep things clean. They tiler says he needs to work off from the upstand first. Which order would you suggest and why? 2) Can we mortar ourselves? Is it possible to use an injectable ready mixed mortar? If so can someone link some suitable products? This would save some cost which is always helpful. Many thanks
-
What U-value should these insulated foundations give
Edward replied to Thorfun's topic in Foundations
EPS 300 is a Jablite product. Cellcore and Heaveguard is a Cordek product, Cordek also manufacturer EPS, called Filcor. Enter your postcode here and you can discuss this with Cordek directly https://cordek.com/contact/ and they can assist you with your insulation calculations. Its unlikely you will need EPS 300 - its probably overspecced on the vertical, so this could save you some cost. On your second drawing, the slab does not appear to be tied in to the foundations. This wont work with the presence of heaving ground. -
Hi all Were about to install the Rehau UFH system in our old house, which has a suspended floor, with unequally spaced joists. The sizing of the joists rules our aluminium spreader plates and because we want to keep the FFL the same, we have decided on foil lined polystyrene panels in between the joists. Our builders are currently insulating the floor with Rockwool prior to the joists being installed. I have two questions: 1) There appears to be a few different type of foil lined EPS joists boards on the market, would you recommend one over another and if so why? 2) I am slightly concerned about the conduction from the foil backed board up into the floorboards - there is a chance of a small cold bridge here, would it be worth packing the interface between the EPS and the floorboard out with a conducting material to ensure there are no air gaps? 3) Finally is the type of tile on the floor important as we are most likely to use a porcelain tile. Many thanks
-
Thanks guys, this is a great help.
-
Yes, access to under the floor wont be compromised once the UFH has been laid. Nick, thank you. I understand the basic differences between closed and open cell foam. Can you elaborate on what should be used where? Obviously avoiding the timbers sweating is important! Thanks Ed
-
Thanks Scottishjohn. I think on second thoughts it would be easier if i get a contractor to quote for the spray foam as you suggested.
-
Ok thanks for the reply. I dont have any plans yet. Yes the floor is in, the house was built in the 30s. Its my kitchen floor, and the depth of the space underneath the floor is enough to stand up in. The u value of 0.25, as far as im aware, is the U value which new builds are required to achieve. What u value should i be aiming for do you think? I do not wish to raise the floor for a multitude or reasons which arent relevant at the moment, so the spreader plate is the only option at the moment. The whole purpose of insulating the floor is to stop the downwards loss of heat, and im trying to address that to the best of my knowledge. If what ive suggested wont work, what would be the best solution?
-
Hi everyone. New to the forum as i'm looking for some advice please. I am looking to insulate between the joists of my suspended timber floor (ground level) to an acceptable standard in order for my plumber to install UFH. We will be most likely using the REHAU spreader plate system so not to raise the FFL. Ive a few questions about the process: 1) Do i need to be concerned about moisture/condensation - should i install a DPC type membrane and if so, should this go above or below the insulation? 2) Does it matter if the spreader plates are touching the insulation, or do i not need to be too concerned about the space between the top if the insulation and the bottom of the plates? 3) Should i ensure any gaps between the insulation and the joists, external walls of the house are as air tight as possible? Should i use a tape or expanding foam? 4) Finally, im torn between using a rockwool type insulation or a kingspan board which will need cutting to size. Any opinions of which to use and why is appreciated. Our builder has quoted £5k for this aspect of the renovation (i asked him to achieve a u value of 0.25w/m2 or less), and as far as im aware its relatively straight forward. Any advice is greatly appreciated, thanks in advance Edward