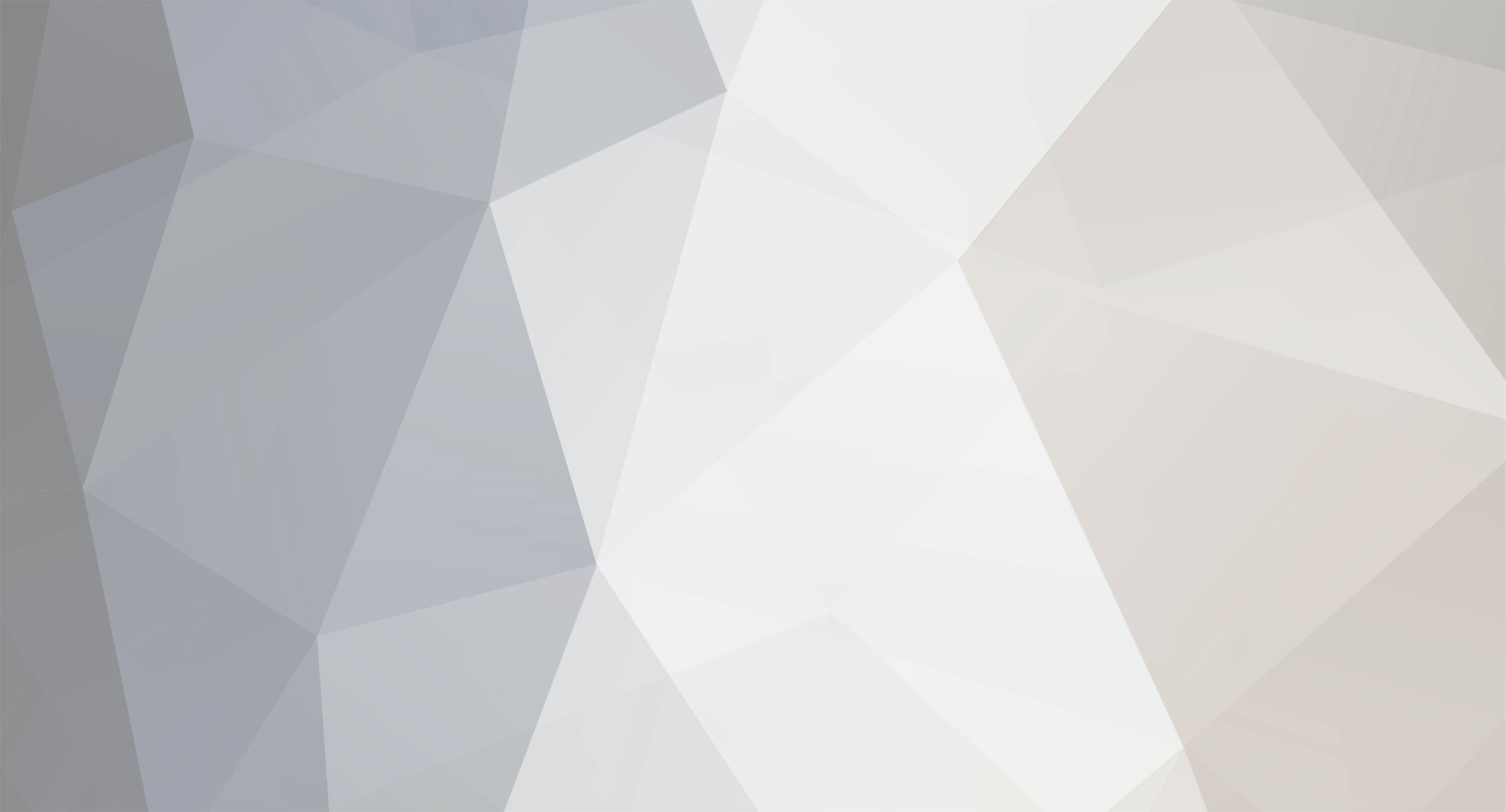
Edward
Members-
Posts
25 -
Joined
-
Last visited
Recent Profile Visitors
The recent visitors block is disabled and is not being shown to other users.
Edward's Achievements

Member (3/5)
0
Reputation
-
Unvented. The HW taps are not connected to the HW output. The plumber confirmed the hot water control on the boiler doesn't do anything, as nothing is connected to it. Thus the HW taps are draining the cylinder, which in itself is a PITA because its a sizeable house and the taps take forever to heat up, wasting HW in the process.
-
Combi boiler heats water, which in turn heats cylinder and therefore DHW is fed from the cylinder.
-
Hi all. Just after some advice/opinion to my setup as it slightly confuses me. We have a Worcester 8000 Life combi boiler. We also have a hot water cylinder in the loft. Given the boiler has both separate heating and hot water outputs, I would have assumed the hot water cylinder would have been fed from the hot water feed from the boiler whilst the heating for the rads would be fed from the heating output. Instead the heating for the hot water cylinder is on the same circuit for the central heating system. Is this correct? Is the hot water function only for hot water on demand? I am asking because i have turned down the flow temperature from about 70 to 55 degrees to a) reduce the energy usage and b) ensure return temps allow condensing to happen. However in doing so the hot water cylinder will never get to safe temperature (legionellas). Advice welcome
-
I dont know in all honesty. We didnt want to raise the FFL when installing the UFH so the plumber had to batton the side of the joists to put the foil panels in-between said joists. There is a chance your statement could be correct however. I seem to have fixed the issue somewhat by increasing the flow through the pipes to its max. I think this prevents the high temp thermostat from being triggered. Ive decreased the mixing to compensate for the lower flow temp from my boiler. All the literature i can find says the flow should be around 1.5 - 2 l/m but this just doesn't seem to work on m setup
-
Foil backed polystyrene, I think about 50mm deep, sitting between suspended timber joists with 150mm insulation underneath. Is it an issue the boiler and pumps will be running between 4.30am and 8pm non stop whilst the system tries to reach temp?
-
Hi. I have UFH in my kitchen and it wont get to target temp of 18 degrees, max is approx 16.5 degrees according to the thermostat. The set up is as follows: Gas boiler, Grundfos pump running from boiler to manifold about 10m away, 3 circuits off manifold (1 zone so no actuators), another pump pushing water through the system. Mixer value. High temp thermostat connected. The variables i can have had changed are the pump speeds, the boiler flow temp (reduced this slightly to ensure condensing occurs), the mixer temp and the flow rates which were set at 5l/m. I first noticed the UFH didn't get up to temp when i turned the boiler flow down from about 65 to 57 degrees - which is as far as im aware still plenty hot enough to run UFH. I reduced the flow meters to about 1.5l/m as my understanding is a lower flow rate allows for a larger dT thus more heat output. However this was causing the high temp thermostat to kick in and shutting the pump off. I have now increased the mixer temp to 55 degrees (not an actual measurement, just a number on a dial) and allowed the flow rate back to 5l/m. This appears to prevent the high temp thermostat from kicking in. However the room does not get above 16.5 degrees. I am beginning to think external environmental factor are the influence as the weather is much colder and the insulation underneath the (suspended) floor probably needs inspecting. My question is what speeds should the pumps be set at, whats the optimum flow rate to allow for a sufficient dT? What influence does my mixer valve have on heat output? Any other suggestions would be welcome.
-
Ive attached an image of inside the roof. We haven't lost any tiles however a batten or two have fallen and are rotten. Ive pulled the tiles back into place but they re not securely held. How would you go about fixing this?
-
Hi just after some advice on patching a roof. Its an old house with clay tiles and no felt. A couple of tiles have slipped exposing an area about 500-800mm in length. Gaining access externally will involve scaffolding due to the proximity and height of the hole however this can easily be reached from inside the loft. Am i going to be able to make a temporary repair from inside and if so what materials should i use? I am thinking of using some flashing and some adhesive - would this be the correct materials for the job?
-
The land on our property is retained by a wall approximately 3m high, our garage sits about 1.5m away from the edge of the retaining wall. Our neighbours are proposing to extend their kitchen towards the retaining wall. Their land slopes upwards towards the wall. My best guess is that to get the necessary FFL in their extension, they will need to excavate 800mm down at the deepest point, ie the point closest to the wall. I am therefore concerned their construction could possibly cause settlement issues on our property as the foundations to the retaining wall may become undermined. Is there any rule/regulations or even guidance which covers the topic about building at the base of a retaining wall? As of yet there has been no planning permission application so there is no immediate concern, however I would just like to empower myself with this knowledge when the inevitable application does come in. I do not know how close to the wall they are looking to extend to. Thanks in advance.
-
We need to replace our roof soon. It’s not far of 100 years old, we can see daylight through the roof, it leaks, is covered in moss which the birds pick at which further damages the roof, so…. What alternatives are there to the traditional roof tile, like a composite fitting or something, which will tolerate UV, cold, snow ice and hot temperatures? I have literally no knowledge on this topic so any insight would be useful. Would you trust the advice of a roofing contractor on materials or would you request a contractor installs a material of your choice? More than likely too is that the timber frame would need replacing as I suspect it could be in a better condition.
-
The Rehau smart system, in my opinion is the most unnecessarily complex and frustrating system to get working properly. The UFH comprises of three circuits heating my kitchen, therefore no manifold, quite a straight forward setup. I can not get the app to communicate with the system, I am not sure if I have paired the thermostat with the base, when think its been turned down I can hear the system opening up and pushing water through, the instructions are hideously complex and the flow diagrams dont appear to correspond with what I see on the hardware. So before I melt down, how easy is it to swap out control system for another manufacturer? If its fairly straightforward, any recommendations?
-
Forgive me but I am a complete layman when it comes to electricity. We have in our kitchen a pendant with 8 bulbs installed, specifically these in various shapes. https://www.thelightbulb.co.uk/4watt-pear-led-es-e27-screw-cap-very-warm-white-gold-finish-equivalent-to-30watt-dimmable/ The wiring, switch, the circuit into the distribution box including the box itself is all new. We replaced the current bulbs because they buzz, however these bulbs are worse. What’s the solution? Is it likely to be a new switch? Are the bulbs not suitable? id be grateful for some insight and some product recommendations to help stop the buzz!
-
Perpendicular to this, from the house to the retaining wall
-
My original post was concerting the specification around the steel.
-
Because the current retaining wall is failing and needs replacing. I also need to raise the patio inline with the doors to reduce the drop. If i use stone and a wheelbarrow, the new wall will need significant footings to retain the stone. In my suggestion, the new wall would not be retaining anything.