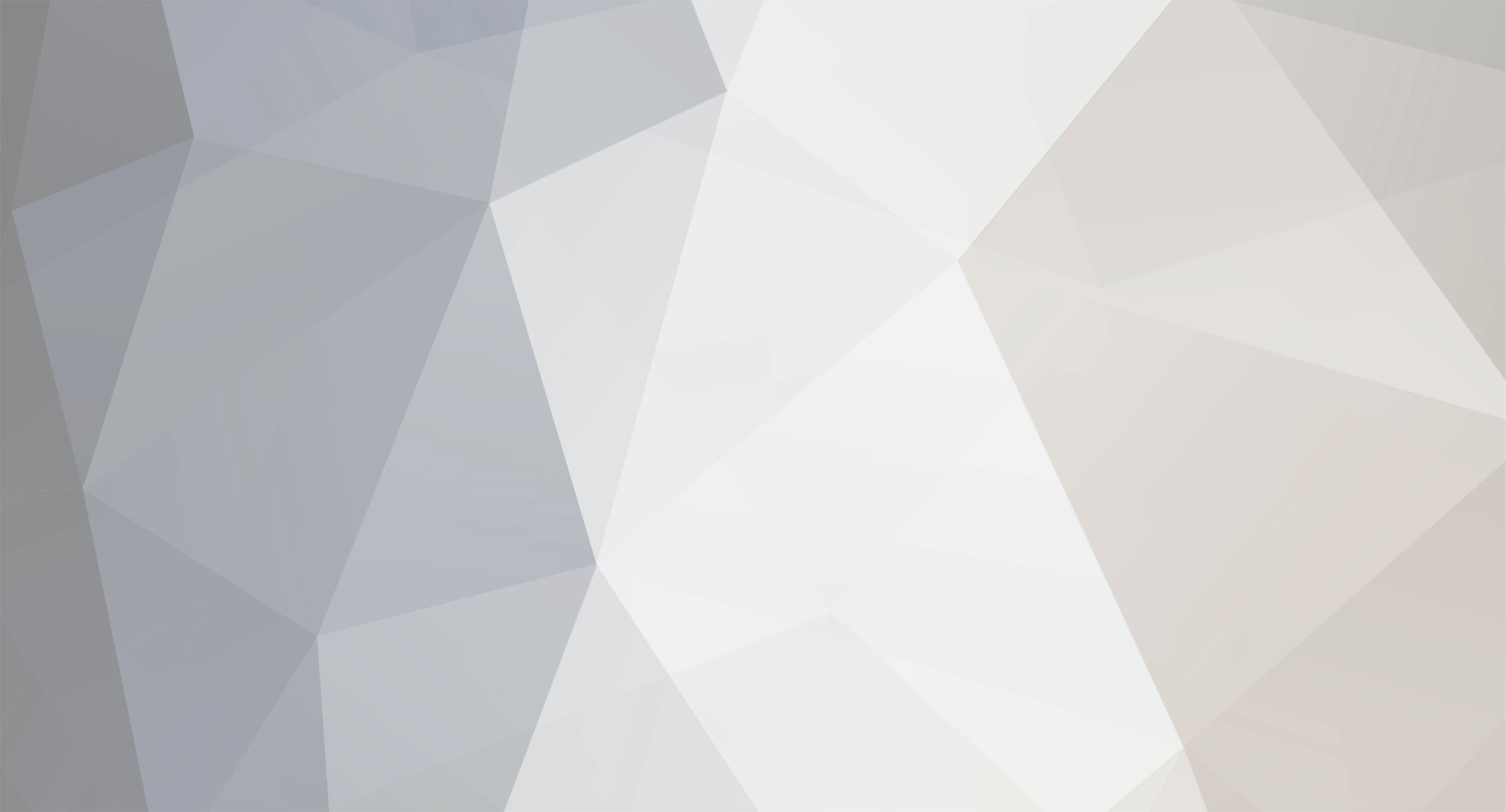
sphannaby
Members-
Posts
38 -
Joined
-
Last visited
Personal Information
-
Location
County Durham
Recent Profile Visitors
The recent visitors block is disabled and is not being shown to other users.
sphannaby's Achievements

Member (3/5)
1
Reputation
-
Hi, Haven't been on here for a very long time as our renovation got completed around 8 years ago, I think I was actually more active on the old forum and everything transitioned over to here during the latter stages of our renovation. Anyway the reason I am here is I appear to have an issue with my thermal store. Typically I am working away from home so I'm remotely trying to help the wife and get a plumber sorted. Our setup is a 300L TSS store which is fed direct from a Megaflo32ERP system boiler. Only CH tied into the system is UFH which we have throughout. I have attached drawing of my store (which is exactly how it is built but drawing is missing the pocket for thermostat). Anyway the problem I have is that my boiler has lost pressure and when going to check my wife noticed water round the bottom of the store. It looks like the drain valve on the store is leaking (see pic 1) and when I asked her to try and close the drain valve a bit more she said it started to leak along the stem of the valve. So I suspect I possibly have a drain valve that will need replacing. My main question is if the valve doesn't need replacing and can be reseated so it doesn't leak do I need to check the water level in the store as I have obviously lost some water? Not sure if the store will be topped up by flow from boiler or if I will need to check the level and if so how? Many thanks for any help.
-
Hello again everyone, I'm starting to get back on the forum again now. Been a hectic time finishing the house off, I was forced to change job locations just as we were moving back into the house which caused all sorts of problems and we ended up living in disarray for a while! House is pretty much done now with the exception of a bit commissioning left to do and some flooring contractors to have a date in court with. With the onset of our 3 day summer rapidly approaching my better half has turned her attention to our garden. Just to give you some background I have attached some basic sketches of what I currently have and what I plan to achieve.In the 1st picture I have tried to represent the current state of our garden. The slopes are not exact but they give a fairly good idea of how it is.The 2nd picture shows our plan of how we want it when finished. The decking area is 6.5m wide and 7.5 long.I had planned on outsourcing all of the work but funds have dried up a little so I am looking to take it on myself now.The right hand side of the garden as you look at it is definitely going to be levelled off for turf to go on. Plan was to have a retaining wall at the top end and to right hand side as required, this will be built by my father in law who is a brickie.One of the issues causing me a headache is the land which the decking will go on. When we had people round to quote they said they would simple take out of the top section of the decking base area and put in in the bottom to level it out and this would mean there would be no waste from that section. I was happy enough with that but my father in law informed me that this would then create a different height step between the levelled turf area and this new decking base area. He stated this would also need to be retained somehow. When I asked the lads who quoted the job they stated pieces of 3' x 2' would be used to retain this. My father in law reckons that wouldn't be good enough and a proper retaining wall would be needed.So my next thought was to take the decking base area down level to the same level as the turfed area and build the decking up from there. This would require another retain wall but that would be around the perimeter of the area rather than hidden underneath the decking. I feel this would look neater and also allow for greater flexibility in later years should we ever decide to get rid of the decking.My main question is if I level the decking base area down the same as the rest of the garden this will give me a height difference of 500mm from base to my desired finished deck height. Is this a suitable sort of height to be able to build up to using a bearer and joist decking frame?Once I know that I can get my head round things a little better. I have done a bit research but had a few other questions hoping others can help with:1 = Am I correct in thinking I should have bearers down first and these should be attached to steel supports which are concreted into the sub base? If so does anyone have any recommendations for supports to use?2 = How would I go about calculating what size bearers and joists to use?3 = I read that decking should have a 40:1 incline ratio to prevent water pooling. Am I correct in thinking this should be achieved by putting the incline direct at the bearers rather than packing the deck boards?4 = Because the length is 7.5m I guess I will struggle to get single length of deck boards. Would I be better cutting boards to 3.75 so I have a uniform joint line down the middle or is it better to stagger the joints for more stability (for example as you would with laminate flooring)?5 = With regards to the full length steps the Mrs has stated she would like wide steps, say 2 or 3 full boards (I have done my sketch based on 2 boards). From what I have been able to find on the internet I can't seem to find any pre-made stringers that would accommodate this. Am i just looking in the wrong places or are these generally no available for wider steps (total make up height of steps will be 500mm)? Any pointers would be greatly appreciated. Cheers
-
Renting an anemometer
sphannaby replied to Jayobn's topic in Mechanical Ventilation with Heat Recovery (MVHR)
@Jayobn can I ask what companies you found up North that offer hire as this would suit my location? Thanks -
Very cheap MVHR
sphannaby replied to sphannaby's topic in Mechanical Ventilation with Heat Recovery (MVHR)
You can change the position of the OA and EA spigots. Its only 4 screws which hold them in place and you just swap with the corresponding blanking plate You only get to move them by 90 degrees but this may help. Its a beast of a unit and I had to move the OA to give me a decent chance of getting in at the filters. -
I will try and dig out what I have when I finish work tonight. I do have spare tiles but thats going to add in extra cost to get a tiler back and I was wanting to avoid that if possible. I have 2 doors and 1 side panel going spare, free for collection in County Durham Pretty sure the doors are of no use, hopefully it will be seen in pics I post in a bit.
-
Thought it best to add onto this thread rather than create a new one. We have a 900 x 900 tray and need a new enclosure. The Mrs wanted a pivot door and I couldn't manage to change her mind. Anyway it came and when our plumbers have tried to fit it the enclosure would simply not work. The only way to achieve the door being square was to have the bottom section of the door on about a 30 degree angle, similarly if you put the door section square then the actual door itself was out by about 30 degree. I had lots of to and fro with the retailer who said first of all it was a faulty door, new one was subsequently sent out and the same issues existed! After more discussion they have just agreed to give me a full refund as they state their technical team can offer no more support. I suspect that this is the first of the type of enclosure they have sold and unfortunately I have been the guinea pig as they are not even interested in picking up the 'faulty' doors. Anyway my issue now is that I must find a new enclosure. I have managed to convince the Mrs to go Bi-fold or hinged. Our problem lies that the doors we took out had wall channels that were 42mm wide and so we need something at least the same width to either take up the same holes in our newly drilled tiles or at least to be able to hide them. Does anyone know of any such enclosures that offer this? I have done much trawling of the internet and it is difficult to get the channel width on most doors pillars, then ones I can find information on generally seem to be 30mm.
-
We used Liberon Danish Oil and our staircase and loved the results. Really brought out the grain, definitely not orange which we were keen to avoid. Very easy to apply and I imagine you could achieve a darker shade if you wish by applying more coats but we stopped at 3 coats as it was exactly what we wanted. Just reminded me that I still have 11 doors to do when I get back home in a fortnight
-
Humidity controller for MVHR
sphannaby replied to sphannaby's topic in Mechanical Ventilation with Heat Recovery (MVHR)
Thanks. I should have looked there myself! -
Humidity controller for MVHR
sphannaby replied to sphannaby's topic in Mechanical Ventilation with Heat Recovery (MVHR)
Its the BPC manifolds (flat rectangular shape) that I have with the 63/75 semi rigid pipe. I was actually thinking about drilling the extract manifold box itself but now you mention it I think I have one inlet blanked off so I can just drill the plastic blanking cap and feed the sensor through there. For sensor mounting I was just going to try and get it as close to the centre of the extract manifold as possible and bond it down with duct seal or a sticky pad of some sort. -
Maybe a bit late but thought I'd chip in anyway. We looked at LED downlights and found JCC and Ansell offer decent fire rated down lights with 10 and 7 year warranties respectively. Both give out 60 degree beam angle so you don't need as many as 'normal' down lights. We went with the Ansell Orbio 360 and have been really impressed with the output of the lights and also the ease of fitting.
-
Humidity controller for MVHR
sphannaby replied to sphannaby's topic in Mechanical Ventilation with Heat Recovery (MVHR)
EDIT. Was it possibly @JSHarris who suggested using the DCH-100? -
I've just bought one of the polish DCH-100 humidity controller that were previously recommended on ebuild. I can't find the post but I seem to remember someone saying that they positioned the sensor for the controller directly into extract manifold box. From what I can see that sensor is not exactly a tiny thing so wondering how this was done? Was it just a case of drilling the manifold with a hole for the cable and feeding the cable back through then sealing cable hole with duct seal? I can't think of any other way.
-
Decision on thermal store or not
sphannaby replied to sphannaby's topic in Boilers & Hot Water Tanks
got that @Nickfromwales, cheers again. We got it up and running last week before I came away to work and it was running very smoothly. I did\t wire full logic as I was just using stat to control everything and using the ZV manually just to get it commissioned. I'm going to knock up a wiring diagram while I'm at work as I'm doing all my others too. I will upload a copy to see if it meets with your approval. One question I have remaining. Can you explain what the issues are with convection circulation when related to a thermal store? Bear in mind I'm a thick sparky and don't know anything about convection issues in any type of heating circuit. I understand if this si not a simple thing to explain and I may need to do some more digging myself but from my google searches I don't seem to be bringing anything up of any substance. -
Decision on thermal store or not
sphannaby replied to sphannaby's topic in Boilers & Hot Water Tanks
Got my thermal store from Telford and they have forgot to install a pocket for the thermostat to go into! TS has to go back to be re-worked and then sent back out to me. Caused a lot of problems as I have now had to put back other trades because I can't have the plumbing ready. The joys of home building..... @Nickfromwales with regards to to your comment on using a 2 port zone valve to stop backflow from the TS to the boiler. Am I correct in thinking that the zone valve would be wired direct to a one channel programmer. Then I would have a spare set of contacts within the zone valve to give a boiler enable signal to my system boiler? Also with the 2 two port zone valve you mention to isolate the UFH. Would these be connected onto the downstairs supply and return 22mm manifold feeds or would it be one valve for the upstairs manifold supply and one for the downstairs manifold supply? ALso what would be the logic on controlling these? Hope this makes sense??? -
Decision on thermal store or not
sphannaby replied to sphannaby's topic in Boilers & Hot Water Tanks
Sorry should have stated yes it will be gas system boiler. I thought from other discussions by using a TS it would provide enough flow/pressure to the manifold that the UFH pump that is connected to the manifold would be enough to draw through required water. What I was wanting to know was would a UVC provide sufficient flow/pressure to do the same or would i need an extra 'supply' pump at the UVC to get it to the UFH manifolds?