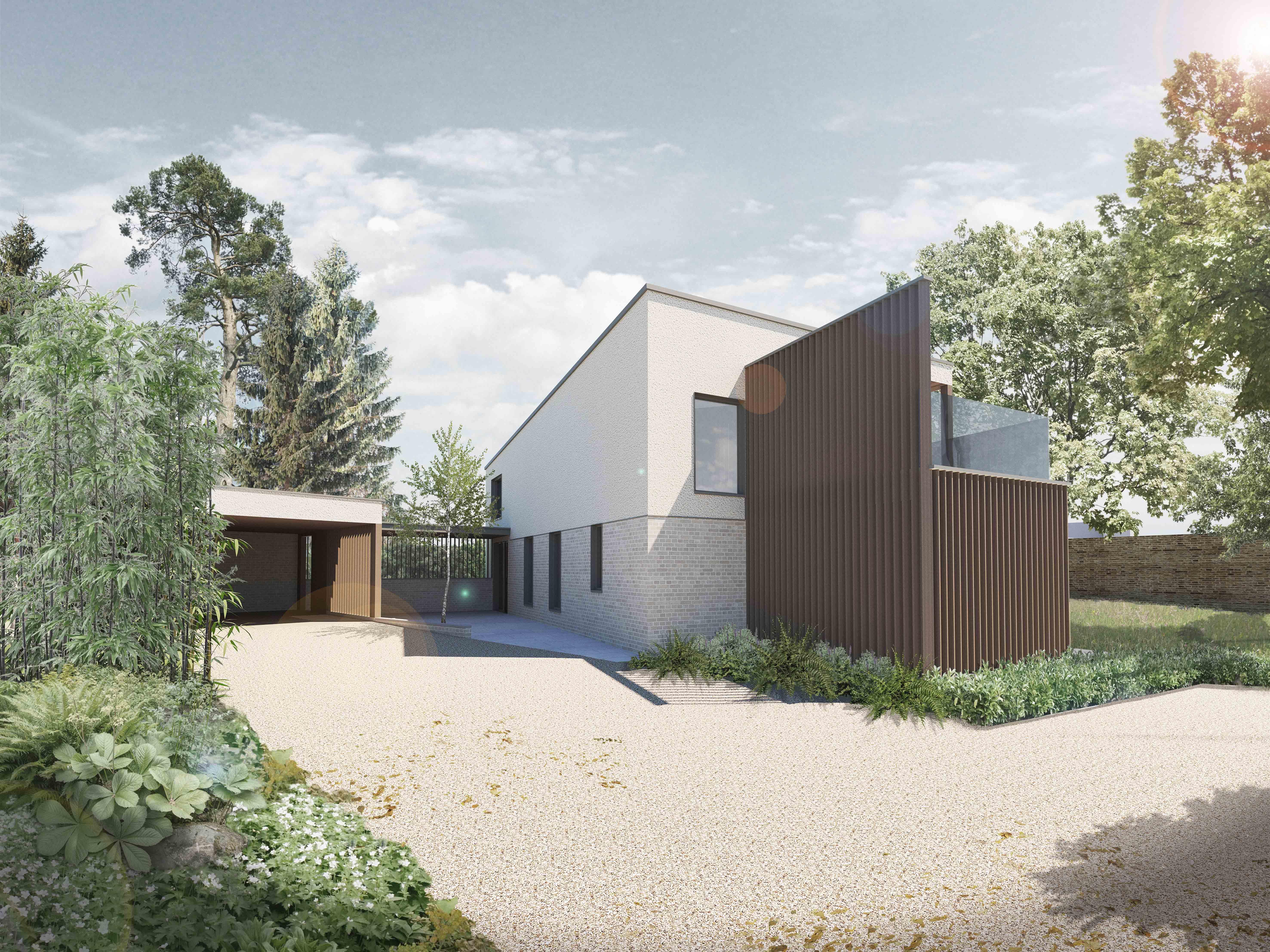
Mulberry View
Members-
Posts
711 -
Joined
-
Last visited
Everything posted by Mulberry View
-
I would love to have the intelligence to be able to turn that into something practical, but I don't know where to start. LOL.
-
Thanks for the reply @Nick Laslett. Our ceilings are a minimum of 2.5m throughout, but the whole Kitchen/Dining/Living room is under a 5° sloped ceiling that rises from 2.5m to about 3.3m, they are already quite generous. My current levels are to provide a completely flush threshold to our Dining Room door. But overall, you appear to be saying that the PIR route is minimally more expensive and so, in your opinion the better route?
-
That's my thought. The money saving would be lovely, but I'd like to try to offset the poor performance of the Beam & Block floor as much as possible.
-
We have a Nudura build with Beam & Block floor. The B&B is now installed and grouted, we did all the work and the resulting floor is pretty level/flat. I think the finish is good enough that we can examine/rectify any imperfections. Sand blind or not? I intend to see what the floor is like once we've had a day or tidying it up, but I'm certain its better than usual building site standard. Our internal walls are built from medium-dense concrete blocks on 100mm thick Marmox blocks Our design showed 150mm of PIR, but we can now better this due to some changes in build. We have approx. 290mm from the top of the floor finish down to the top of the B&B. We plan on Microcement throughout, which totals 4mm, so 286mm for Insulation and screed. We intend on having UFH (yet to be designed). What's the best split of Insulation and Screed for optimal performance? Drying time isn't a huge priority, although my head is fried all our other nonsense, I'd like to make some blummin' decisions and get this all underway before the weather cools down. I expect our Glazing to be going in late October or early November, all being well. Any and all help is greatly appreciated.
-
Soakaway fill material
Mulberry View replied to newbuild upnorth's topic in Rainwater, Guttering & SuDS
Because we're founded on hard chalk. Made for great foundations, but less so for water infiltration. The bottom of this hole is like a bathtub, the soakaway was designed to potentially be half-full most of the time. -
Soakaway fill material
Mulberry View replied to newbuild upnorth's topic in Rainwater, Guttering & SuDS
Anecdotally, if anyone is feeling frustrated by the amount of work needed for a Soakaway, know that this is what we had to have for our modest (200m2) 4-Bedroom house. 96 standard sized crates in 2 layers (though these are larger crates so there are *only* 60). Just under 20,000 litres. LOL. -
Expert Witness needed...
Mulberry View replied to Mulberry View's topic in Party Wall & Property Legal Issues
The installer is adamant that everything is compliant because the material manufacturer (who has ZERO interest in the installed roof) has issued their material warranty. I have raised several queries that are strongly likely to be detrimental to the longevity of the roof but of course failure of the roof due to any installed detail will fall back to the installer, so why would the manufacturer care? It's like the perfect storm of non-acceptance. -
Expert Witness needed...
Mulberry View replied to Mulberry View's topic in Party Wall & Property Legal Issues
The installer stated early on that no expert testimony would be accepted by him as he is an expert installer and therefore his view is the end of the line. I had to remind him that this is not how the law works, but finding an Expert Witness who can top trump this guys self-righteous disposition is the challenge. There are Expert Witnesses who do not specifically specialise in Zinc roofing, I can see we won't get the full picture that we need. Then there are Zinc roofers who have all the expertise and experience, but are not classed as legal 'Expert Witness'. We have found one person who has BOTH credentials, but he and our installer are mates. -
Expert Witness needed...
Mulberry View replied to Mulberry View's topic in Party Wall & Property Legal Issues
The installer that did my roof is so deeply in the pockets of the whole industry, it's hard to find impartiality anywhere. The local rep for the manufacturer with whom I discussed the entire situation as it was unfolding lives 15 minutes from my plot and would not come to see. They literally do not get involved in the installation. They provide standard details and general guidance, but cleverly disconnect themselves from installation issues. I have raised specific queries with them and shown them photos of what I claim are defects, they refuse to get involved. -
Expert Witness needed...
Mulberry View replied to Mulberry View's topic in Party Wall & Property Legal Issues
For us, the output of an Expert Witness report will probably define our route, it's why we want someone with deep experience of Zinc roofing, we want the outcome to be unarguable, either way. If the report deems the roof to be as fundamentally defective as we believe it is, then we hope we can assess the probability of our case and begin talks with the contractor about a settlement without going to court. I'm going to talk to some Zinc installers today in the hope of finding someone who can be expertly impartial in the hope that they can be accepted by all parties as a joint expert witness. -
Expert Witness needed...
Mulberry View replied to Mulberry View's topic in Party Wall & Property Legal Issues
Thanks for your detailed @Gus Potter. The contractor has taken the view that the installed details are all compliant because the manufacturer has issued their 'material-only warranty', though they take NO responsibility for workmanship at all. Read into that what you will. The installer has literally NO interest in hearing my concerns and explaining his reasoning despite the issues I have raised. I'm going to DM you as you might be able to help me. -
Expert Witness needed...
Mulberry View replied to Mulberry View's topic in Party Wall & Property Legal Issues
Our contractor does not know the word 'compromise'. He is deaf and blind to any problems, he just wants his money. I know the implications of court, but I really do not see that we have a choice. I'm hoping that a proper expert report might help him to recognise that there are faults, then we can attempt to discuss some sort of settlement offer. We're £45k in, the contractor does not believe he is even 1% at fault, so the alternative is walking away and taking a £45k hit and he'll still pursue us for the remaining £10k. That would finish us and the project would probably have to be sold. -
Expert Witness needed...
Mulberry View replied to Mulberry View's topic in Party Wall & Property Legal Issues
That's certainly worth pursuing. The hard part is that our contractor is VERY well known in his industry and highly devious. -
Some of you know about the legal issue were dealing with at the moment, our defective Zinc Roof is preventing progress on our project and has been for almost a year now. We need an Expert Witness and finding one is proving difficult. Ideally, I want someone with a good understanding of metal roofing (Zinc particularly). Can anyone here suggest how we can solve this?
-
Our plot is about 170m from the road and I too wanted a single unjointed pipe run. But a single fusion-welded connection is what I eventually settled for. We installed the 32mm MDPE pipe (100m) in blue 100mm ducting, but coiled it up at the end of the shared private driveway but just into our plot (still 100m or so from the house). The end of the pipe was attached to a TBS, which had to be lagged etc. We VERY crudely back-filled it and I mean crude. I arranged blocks and slabs to enable me to throw a few inches of soil over it so that it would appear to be back-filled. They signed it off and connected it without issue. After they were gone, the pipe was dug up, uncoiled and run up to the plot in the correct way. The fusion-welded connection was added about 30m upstream from where the TBS had previously been. The pipe was left long enough that it'll be able to serve the house when the time comes, but for now I buried the coil again and connected the end to the caravan and a TBS. It sounds like a faff, but it wasn't really. The coil is buried about 15m from the house and will easily pass in through a duct already installed. The only challenge will be what we'll do when we want water to the house, but are still in the caravan. So consider that. Believe me, things like this will pale into insignificance once you get into the build. All the seemingly great decisions you make early on will not remove the risk of having to re-do things or do them a little differently. Just do you best and crack on. I have to move the main drainage chamber I lovingly installed and currently services the caravan. Nightmare, but it's life.
-
EPDM - Viable for a full roof?
Mulberry View replied to Mulberry View's topic in General Self Build & DIY Discussion
That's pretty good. We have about 130m2 of roof area I think. So are the standing seams created with the product itself or in the build-up? Is yours a warm roof? -
EPDM - Viable for a full roof?
Mulberry View replied to Mulberry View's topic in General Self Build & DIY Discussion
That looks nice. You pleased with it? I know nothing about it at this stage. I didn't realise standing seams are used with EPDM? One of the main issues is that we have 3 rooflights that have turned out to be tricky to detail in Zinc. Do you mind me asking what it cost you? -
As some of you know, we're going through a bit of trouble with our Zinc roof. This rumbles on and no end is currently in sight, but I've had a bit of an awakening this week. Our roof is a 5° monopitch, there are 2 main and distinctly separate roof areas. Obviously you can't see much of it from the ground. You do, however, have a really good eye-level view over the single-storey roof (marked above as Roof Area 1) from the landing and from there, the oil canning is really obvious. I've come to realise that however good the installer is, there are some inherent features of standing seam roofing that cannot really be avoided. At least nobody will guarantee that these issues won't exist. It got me wondering... If an elegantly executed perfect metal roof just isn't possible due, in part, to the design of it then should I bring EPDM in as an option. In other words, is a well executed EPDM roof better for us than an imperfect Zinc one? This isn't a cop-out by the way, I'm just trying to be pragmatic. Our roof has so many defects and problems, at this point, I see no other option than stripping it fully. I have discussed this in this thread so don't really want to go over it here. Obviously we could have the absolute gold standard of EPDM for a much lower cost than Zinc and it makes me wonder if we really should consider it. Any thoughts?
-
What to paint a Steel goalpost frame with?
Mulberry View posted a topic in RSJs, Lintels & Steelwork
I've got a (roughly) 2.5m Goal Post frame made from 100mm SHS. What's the best thing to paint it with? It's forming an Oriel Window opening, so it'll be covered/cladded etc, but I want to paint it properly before it's lifted into place. Historically I'd have used Hammerite or something like that, but I thought I'd ask you good folk. -
How to regain traction...
Mulberry View replied to Mulberry View's topic in General Self Build & DIY Discussion
I think you've taken the point I made about the pile of debris in the gutter a little too literally. This was just something that happened this week that highlighted just how fast that gutter can fill with modest rainfall. It is not the basis for my complaint. The Zinc contractor specified the size (350mm wide) and fall (1:60) for the box gutter, which was built by me whilst they worked on other parts of the roof, but VM Zinc contradict this, so who is right? It's a fairly big gutter with only one possible exit point at one end. It's a weird quirk in the design as there is a window very close to it which does influence things, but if the contractor had highlighted his concern, I could have helped to remedy it, as I am doing now anyway (well, I can't alter the roof, but I can make preparations for the remedial work from the point-of-view of the bits I control anyway). As for watertighting the upstands. I hadn't wanted to screw anything into the upstand and so have made sheeted strong timber frames that lay on top, I strapped them in from the inside. They are staying in place and the plastic is good stuff, but not sure how long it'll last. I am looking for a metal roof contractor to both report on the existing roof and help with a remedial solution/re-roof and would gratefully accept recommendations, but they'd have to be above average because I've had 2 local firms round so far and whilst they had some good info for me, I'm not sure either have the credentials to take this on. -
How to regain traction...
Mulberry View replied to Mulberry View's topic in General Self Build & DIY Discussion
The box gutter is pretty big. Its about 5m long, 350mm wide and has a 1:60 fall along its length. Its outlet is 200mm wide into a hopper. I happened to be on the roof yesterday for the first time since the Scaffolding came down at Christmas and noticed that there was a large amount of tree debris in the gutter, so I swept it to the end in readiness to remove it. It was raining at the time, and not particularly hard. I got briefly distracted, but in the hour or so I was gone, the 'dam' of debris had caused the gutter to fill almost up to the 100mm seam. VM Zinc themselves say that if the fall was 3°, then the upstand could be lower, but otherwise it needs to be 200mm. They ignored the photos and dimensions I sent to them and allowed the installer to reassure them that everything is compliant. It makes no sense. The area of roof I'm standing on to take this photo is about 100mm higher the adjacent upstand, yet only 350mm away. We had the roof windows here on site when the Zinc team arrived. They ignored the installation manual (which to be fair doesn't provide specific Zinc detailing) and I still have the Velux flashings in packaging in my site office because their 'solution' apparently wouldn't require them. Velux insist they have to be fitted. Sadly the movement action of the "top hung" window runs to a VERY tight tolerance and by allowing 4-5 layers of Zinc to exist between the upstand and hinges, will effectively move the whole window back by an amount that will probably cause it to foul the upstand as it is opened. I have a report written by a specialist installer organised by Velux that highlights this issue. The hinges pivot at the bottom, so this removes the ability for many of the 'fixes' that others have suggested, such as running zinc 'skirts' around them. I've had almost a year now of trying to crunch this in my brain to solve it. Velux told me I needed to provide at least of 100mm of net upstand height, I provided 145mm (theoretical), but stacked materials and general building 'sloppiness' have resulted in around 120mm in reality, so 25mm was lost somewhere during the installation. The Zinc installers proposed workaround would result in 60mm from the roof deck to the first ingress point, VM Zinc expressly say that's not enough. I say that I do not accept they'll be able to achieve their proposed design at guarantee 60mm, it's far too technical and if the end result is 50mm or even 40mm, then it makes the situation worse. Even the fixed window is a problem because the Window itself lays onto the upstand and 'drapes' over the edges. By design, it is then screwed to the upstand and these screws will penetrate the Zinc and prevent the expansion movement it needs. The screw holes will only be about 50mm off the roof deck because the overall upstand height doesn't meet the dimensions shown here, again due to the stacked materials and weak adherence to tolerances. -
How to regain traction...
Mulberry View replied to Mulberry View's topic in General Self Build & DIY Discussion
The roof, for better or worse, is mostly finished. Sub-standard, but finished. There are no fascias to go on, what few gutters we have are on and the scaffolding was taken down in December (Nearly 4 months after the Zinc contractor left the site), after us having paid £4000 in over-charges to keep it up in the hope that the original installer would work with us to remedy the problems. Windows and doors are next on my agenda, we're close to a window order, so I need to focus on the issues that are preventing that. -
How to regain traction...
Mulberry View replied to Mulberry View's topic in General Self Build & DIY Discussion
There are some pictures on this thread, but further issues have emerged since. The world of Zinc-roofers is a weird one. I'm sure other sectors are the same, but they all love throwing each other under the bus and the 2 other installers I've had round to look since both claim that are involved in current remedial work for the installer who did ours. Who do you believe?! The lasting problem is that none of them will warrant any 'repairs' they do and of course the original warranty will probably be voided as soon as anyone else touches it. -
How to regain traction...
Mulberry View replied to Mulberry View's topic in General Self Build & DIY Discussion
Thanks @JohnMo. It makes sense. There are things I am getting on with, but always with a level of reservation and dread about where this could all go. The roof is reasonably secure, it is 99% water-tight, save for large bit of plastic sheeting that protects the incomplete box gutter flashing (the flashing renders our roof technically 'incomplete' and therefore the final payment is not legitimately due). This sheeting disintegrated in the uncharacteristic winds we had earlier this week, but I've replaced that now and I think it'll last. The slight worry is that if we did crack on inside and any of the covers over the rooflights were to fail, we risk damage to the internal work. The covers have been made fairly robustly using 4x2 timber frames covered with UV-stable Polytunnel sheeting. Pigeons have pecked holes in the rooflight cover over the rooflight in our upper 2-storey roof. I need to get up there and remedy that, but with no scaffolding, I'm scared to make that climb. With occasional help, I am the only person working on this. The Zinc contractor was the first and, so far, only major external contractor. We could not have afforded to do this without being true self-builders, hence the roof issue could really sink us.