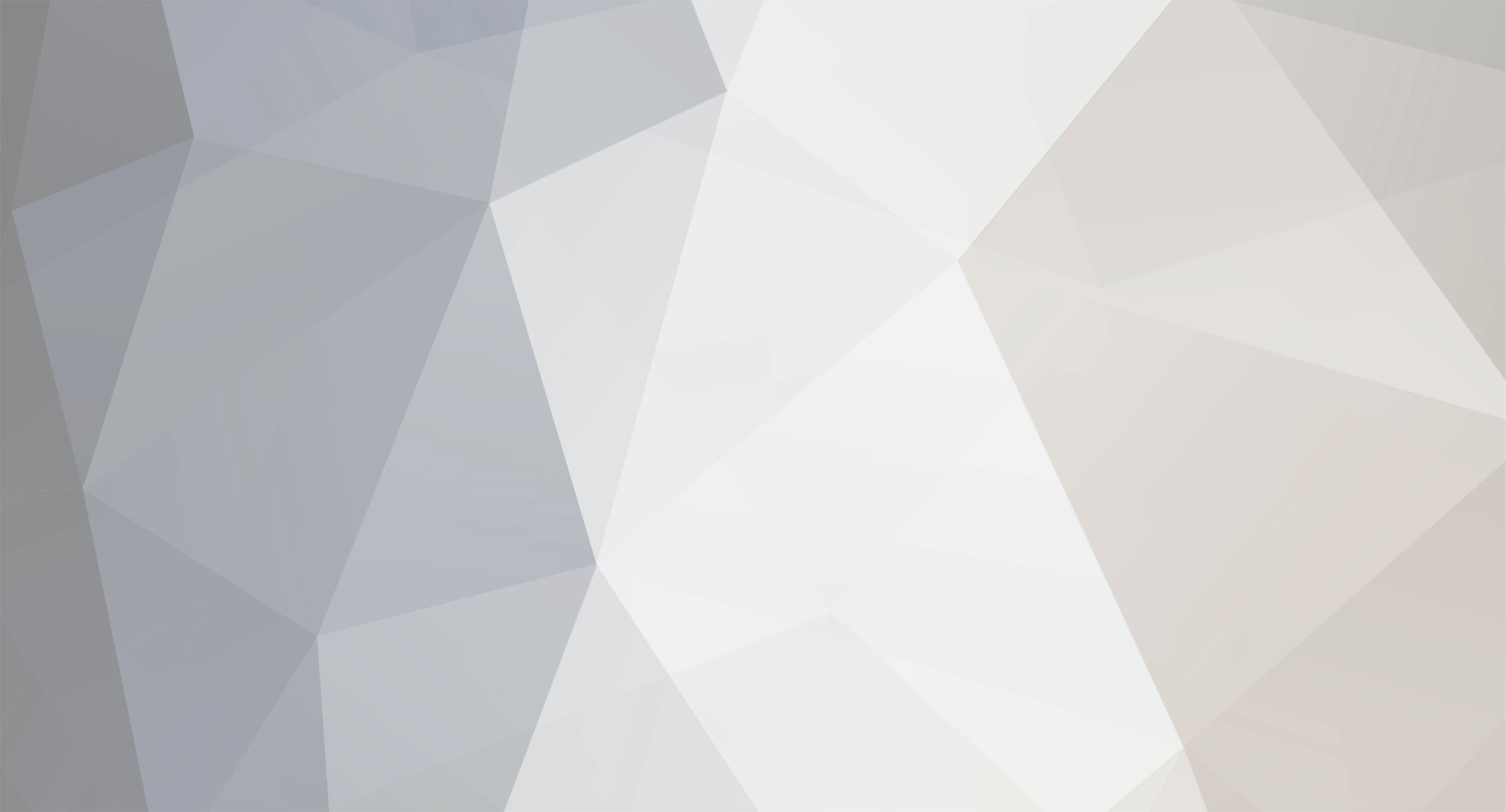
Gooman
Members-
Posts
109 -
Joined
-
Last visited
Personal Information
-
Location
Bedfordshire, UK
Recent Profile Visitors
The recent visitors block is disabled and is not being shown to other users.
Gooman's Achievements

Regular Member (4/5)
16
Reputation
-
Air-to-air ASHP replacing warm air heating
Gooman replied to Gooman's topic in Air Source Heat Pumps (ASHP)
Johnson & Starley are rumoured to be planning an air-to-water heat pump system with a warm air heat interface. That would be a direct replacement for most J&S units (and maybe others if the ductwork is compatible). Plus, as it's air-to-water it would be eligible for a heat pump grant. -
Air-to-air ASHP replacing warm air heating
Gooman replied to Gooman's topic in Air Source Heat Pumps (ASHP)
Just on that point ... we had assumed the same as well, but after a very thorough asbestos survey (which I would recommend you get) we found there was very little that needed to be done. The only asbestos in the heating system was a brown asbestos panel on the back of the furnace door (which was dangerous, and was removed for specialist disposal), and asbestos cement around the flue. The recommendation on that (as with most white asbestos) was to leave it in situ, with a suitable warning tag in the area not to disturb it. If your property is, like ours, a chalet-style roof (see pic) one of the most awkward parts of upgrading the building fabric was in properly insulating all the eaves spaces. Some of them were accessible as eaves cupboards, but some were sealed up. Existing insulation was 10mm fibreboard between rafters and on internal walls and a little (very little) loft insulation between floor joists. -
Air-to-air ASHP replacing warm air heating
Gooman replied to Gooman's topic in Air Source Heat Pumps (ASHP)
If anyone is interested, please use the Contact section on their website to let them know ... it might galvanize a response! -
Air-to-air ASHP replacing warm air heating
Gooman replied to Gooman's topic in Air Source Heat Pumps (ASHP)
PS - If I was going to try and persuade them that the UK is a worthwhile market, does anyone have any stats on how many domestic warm air heating systems are in use in the UK? -
Air-to-air ASHP replacing warm air heating
Gooman replied to Gooman's topic in Air Source Heat Pumps (ASHP)
Just saw this really interesting development in my news feed - it's an ASHP (air-to-air I think) with an indoor unit in a tower format, specifically designed to replace a forced-air furnace: https://www.electricair.io/ Notably, it also cools and dehumidifies and includes a HEPA filter for air purification. Not available until next winter - and likely in the US only, at least at first. But promising nevertheless! -
Air-to-air ASHP replacing warm air heating
Gooman replied to Gooman's topic in Air Source Heat Pumps (ASHP)
Apparently, J&S are rumoured to be working on an air-to-water ASHP unit + heat exchanger that would fit on the same ducting footprint as our current J&S unit. As it's air-to-water it would be eligible for the government grant (air-to-air isn't). When it might see the light of day is anyone's guess though! -
Air-to-air ASHP replacing warm air heating
Gooman replied to Gooman's topic in Air Source Heat Pumps (ASHP)
@severnside - really interesting results! In the pic below your thermostat of the ducting in the garage - is that the new ducted unit? What of the ducting shown there is original? Our current J&S unit is in a brick-built cupboard with ducting above (for 1st floor) and below (underfloor for ground floor). I doubt the internal unit could be fitted in the ceiling of that cupboard and connect to the existing 1st floor duct - there's just not enough room to work in. Do you know if the unit you have can be mounted flat on a wall, or does it have to be in the orientation shown? -
Air-to-air ASHP replacing warm air heating
Gooman replied to Gooman's topic in Air Source Heat Pumps (ASHP)
@Jeff V The other option is to go with something temporary until the Heat Pump/Duct tech is better proved ... second-hand J&S units do crop up on eBay from time-to-time, and might be an option if you have a local J&S-certified engineer who can install it. -
Air-to-air ASHP replacing warm air heating
Gooman replied to Gooman's topic in Air Source Heat Pumps (ASHP)
I've heard from other users and from AC companies themselves that there could be some gotchas here - but no-one has any hard data on real-world examples! There's been various musings about difference in cross-sectional area of ducting in a typical warm-air system being much, much less than in a typical AC installation and the effect this might have. It would be great to get some results from an actual installation - both subjective and specific (airflow rates and temperature curves). If that's not a problem, the other potential issue is if you run the AC in cooling mode - the original ducting wouldn't have been designed for that and might have problems with condensation. That's going to be much harder to identify on a test - other than maybe putting a humidity probe and/or camera down the ducting to see what happens. -
Air-to-air ASHP replacing warm air heating
Gooman replied to Gooman's topic in Air Source Heat Pumps (ASHP)
It's true that current heat pumps don't produce a high enough temperature airflow. But that is likely to change - there are some higher temperature models that are available now and more due to hit UK shores sometime soon (it's just a shame your unit has decided to go t*ts up at this point!): https://www.homebuilding.co.uk/advice/high-temperature-heat-pumps https://www.theheatinghub.co.uk/articles/high-temperature-heat-pumps It should be possible to link these with a Johnson & Starley Aquair - but you might want to check with J&S yourself. I have had informal conversations with them that suggest this should be possible, but we didn't get into specifics. -
Renovating and extending 1970s house with warm air heating
Gooman replied to Gooman's topic in Introduce Yourself
The door to our boiler cupboard had a brown asbestos panel on the back. Broadly speaking asbestos comes in three categories - white/grey (which is rarely a problem if you don't cut, drill or break it), brown (same as white/grey but a little more hazardous) and blue (very hazardous). We had the whole door removed and safely disposed of. We also had soffits in white asbestos, white asbestos in Marley floor tiles (who'd have thought?) and white asbestos in the cement around the boiler flue in the loft. All left in place - again, if you don't mess with it, it's not a problem. Was yours just a general survey or a specialist asbestos survey? I'd thoroughly recommend a specialist survey with a lab test on samples - that's what we had and it gave us great peace of mind. They'll put any old crap in a general survey just to cover themselves from you suing them later - quite often the stuff they come up with is total bs. If you didn't have a specialist asbestos survey with lab tests there's no guarantee that the ducts do actually contain asbestos. Can't think why anyone would put it on the inside of the ducts - it would impede airflow as it's not smooth. If it was used anywhere it would be on the outside - but ours had neither. If it is present, you don't need to actually remove the ductwork. As above, asbestos is generally safe if you don't disturb it. Just decommission the warm air heating and leave the ducts. The best way to negotiate is to show them examples of what else you could get in the same area for the same price. If they see that and have had trouble selling they might realise that they're overpriced. -
Renovating and extending 1970s house with warm air heating
Gooman replied to Gooman's topic in Introduce Yourself
I can believe that. All of our heating vents are at floor level, so the warmth starts at floor level and rises (rather than hitting the ceiling and then falling as it cools). -
Renovating and extending 1970s house with warm air heating
Gooman replied to Gooman's topic in Introduce Yourself
Given that this house is 50% larger, and looking at our bills (before the recent price increases) I'm certain that the warm air system is no more expensive to run than a wet system. Might even be slightly cheaper. But you're right, it's a lot more comfortable. -
Renovating and extending 1970s house with warm air heating
Gooman replied to Gooman's topic in Introduce Yourself
The boiler in the old house was a combi, only heating what was used, so wouldn't use as much energy as a whole tank. The immersion heater in the new house by contrast is heating the whole 140l hot water tank. -
Renovating and extending 1970s house with warm air heating
Gooman replied to Gooman's topic in Introduce Yourself
One other topic I'd be interested in any comments on ... in our previous home with a traditional wet system, our combi boiler was rated at 35kW output. With our current - 50% larger - home and a warm air system, the boiler is rated at 14.5kW. OK, it doesn't heat water, but that's using a 3kW immersion heater. Why is the energy output requirement so much lower? Is it because it's heating the air directly rather than heating water to heat the air? That's still a huge difference. ?