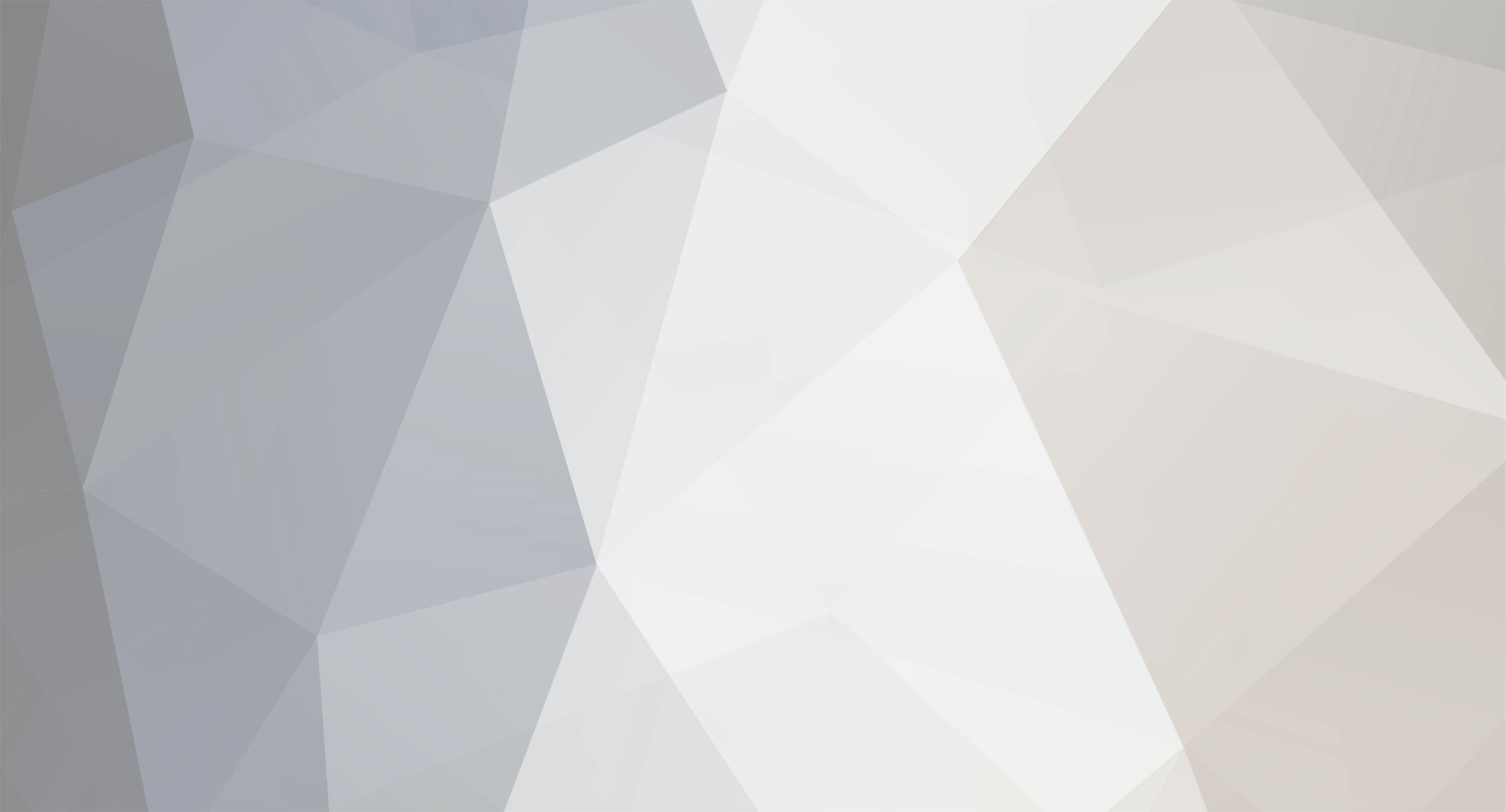
rh2205
Members-
Posts
173 -
Joined
-
Last visited
Recent Profile Visitors
The recent visitors block is disabled and is not being shown to other users.
rh2205's Achievements

Regular Member (4/5)
16
Reputation
-
The entrance to our driveway is too narrow but quite long, we have decided to pull up a section near the double garage for some additional borders to screen this incase we convert at some point & widen the width of the driveway over an existing flower bed using our reclaimed pavers so we can properly have two cars parked side by side (or 4 cars if double stack). What’s the most simple way to do this? When we have gone to companies nobody wants to touch a half job they just want to rip it all up and start again, I don’t particularly want to pay the labour either or what will be quite high material costs if we are starting from scratch and maybe having to lay a whole new sub base. I don’t think the original driveway had any actual MOT laid but other than few very minor dips it doesn’t seem to of moved, looks like they put in a soldier course on one side. It’s a fairly old driveway with 100mm thick highway spec blocks. Will it be that hard to lay some MOT and compact an area next to the current entrance and extend it out using the same reclaimed paving, or is this a bad idea?
-
Best/easiest way to do cheap patio jointing?
rh2205 replied to rh2205's topic in Landscaping, Decking & Patios
This polymeric sand sounds great (we used some amazing resin jointing on our main patio so know how good modern day options are), but it’s going to make a cheap reclaimed patio pretty expensive if I spend £350 on the quantity I’ll need to fill the size of joints even if it is cheaper than resin! But if anyone’s got any tips on the most time efficient technique for a robust traditional way then please let me know! -
Best/easiest way to do cheap patio jointing?
rh2205 replied to rh2205's topic in Landscaping, Decking & Patios
And this will stand up to pressure washing? Why do people pay so much for brush in jointing compounds if it’s so straight forward with dry sand & cement mix! -
We’ve just relaid ourselves 50sqm of concrete utility slabs 50mm thick which we reclaimed from the garden for a side garden outdoor gym / clothes drying area, part of the frontage area nearest the garden we actually reused some very old 50mm thick riven sandstone, not quite like the modern day more precision cut stuff, so the joints ended up quite wide. It looks pretty neat all laid half bond on full mortar bed, only issue is now all the joints are about 25mm wide and 50mm deep because of the initial slab choice and trying to keep it looking tidy. I think we now have no choice but to hand point it (I did some calculators on some of the jointing compounds & the cost was insane). Any tips on how to do this as quickly and pain free as possible? Materials seem pretty cheap the old fashion way it’s just the process and actually not doing a crap job… so please send us any and all advice or if there’s some other better way of doing it.. We obviously are expecting this patio to outlast us so also want to be able to pressure wash it too & not deal with significant weed ingress!
-
How can we tidy/improve this garage visually..
rh2205 replied to rh2205's topic in Garages & Workshops
Oh good idea on growing something up it once painted, plenty of scope for that given the driveway that needs sorting! Yes I did wonder whether anthracite would just make the damn thing disappear I’m glad you have confirmed my suspicions 😂 -
How can we tidy/improve this garage visually..
rh2205 replied to rh2205's topic in Garages & Workshops
Would it look weird if we painted the garage doors anthracite, just have a slight aversion to white garage doors… otherwise you are probably right given the condition of it it’s not worth spending too much now other than to try and make it look semi in keeping with the house. Still a bit against leaving the brickwork bare especially as down one side of the house in the side garden it’s already partially painted white by the previous occupiers, but I know painted brickwork can look pretty awful too. -
How can we tidy/improve this garage visually..
rh2205 replied to rh2205's topic in Garages & Workshops
Probably something I didn’t add I believe there is also a bit of movement in the foundations, some slight diagonal cracking in one location, the lintels above the windows are totally shot, the garage slab is also cracked in half on one side (the two sides of the garage were actually built at different times), nothing particularly progressive but in reality external rendering could still crack without major improvements hence why any option needs to be a diy improvement rather than having to pay for skilled people to come in. -
How can we tidy/improve this garage visually..
rh2205 replied to rh2205's topic in Garages & Workshops
But does this make sense if in 10 years we alter the garage door openings, I think long term we’d replace one garage door with a normal door & brick up one side. Still after recommendations for plastic roller door paint type, otherwise if it’s all scrapping and flaking off nearly immediately that will probably ruin any attempt to tidy it up. I’m just not sure how good our rendering ability is & labour costs round here are sky high… but maybe we are able or at least dumb enough to render it ourselves.. -
We didn’t see the point in spending money doing it up at the time the house was done but now regret it as it’s an eyesore compared to the house! What paint will stick to the upvc roller doors? Graffiti spray paint in anthracite?? Also thinking we could paint the bricks anthracite & pull off the upvc garage entrance strips, just seems to be normal brick behind, doesn’t interact with doors so no clue what they’re for other than apparently decorative? Could we paint the upvc fascia’s too? Paint recommendations for that welcome too. We do have planning permission to put a pitched roof on it but I don’t know what this pitched roof is for other than to look pretty, maybe in 10 years we might want to convert it into another type of space in which case spending lots of money on it now is kinda pointless as we are happy just to use it as a storage garage for the foreseeable future. Any other relatively DIY friendly solutions welcome. Keeping in mind we have a 100sqm driveway also to sort out ourselves (my next post) and I’m not sure we can handle a lot of involved DIY on it, though obviously will take the sensible advice of members if we’re not taking it far enough.
-
How to deal with house overheating/sun in face when dining?
rh2205 replied to rh2205's topic in Windows & Glazing
Internal blinds would have to be fitted on the wall above the window recess otherwise will catch head on them when walking through the door so hardly an attractive position as the metal bracket/roll up dimension is lower than the current opening ( they usually run at about 7cm our frames are 3cm). If we don’t want cords due to width of door & needing approx 4 separate blinds we also have to pay out for electric ones at a cost of £900. -
We have two issues due to oversight when we designed our house. The most pressing one because we have a child who is starting to protest is that the dining table area gets very sunny in the morning, we have 6metre wide patio doors. The sun at the height of summer passes over by about 1pm so it could be worse. It would probably ruin it to put curtains up & top mounted recessed electric blinds would drop 4cm below the very thin outer window frame profiles & we have an extremely tall person in the house which would then catch their head on it when walking through the doors. On the outside we have some very pristine white external wall insulation & we are scared to mount anything externally plus I am not going to lie we really don’t want to be spending more than a few hundred pounds on the solution in an ideal world. Second issue is our house gets very hot… if I could go back we would of designed external blinds at the outset to combat this issue plus improve sleep quality as quite frankly this countries idea of ‘black out blinds’ are utterly useless. Do we just live with all our shortcomings for the next 20 years? Because it was a major refurb but not a full rebuild we have big windows with no consideration for overheating! I don’t see that we can easily retrofit external blinds now for various reasons without totally ruining all the external facade which to be honest worked out as somehow the best finish on the entire house (sorry we clearly put our money & thoughts in the totally wrong places being inexperienced & in a rush). Upstairs the window recess externally is only an about 50mm & we have all this lovely vertical concrete cladding to contend with for fitting anything upper floor. I did see you can buy some pretty cheap external tarps that could be hooked up on the hottest days but that would still require some fixings into the insulation & all the faff that comes with putting it up only saving grace is we have a very tall person who doesn’t need a ladder. But there is also the day to day morning sun issue. Any & all ideas on a budget now welcome because I don’t like the idea of potentially spending £1000’s on stuff as in my mind all the expensive solutions literally ruin the appearance of the entire house either inside or out for the times in the day you are not using it! It’s £550 for instance just for one of those internal blackout blinds with ugly outer frame to fully blackout 1 window upstairs for instance, and there’s 2 windows in the master bedroom…
-
We have grey EPS beads in our 1960s cavity, no problems so far 18 months in, though we stuck 100mm EWI on the outside too so I’m guessing damp will be unlikely from such a set up. Do wish we’d gone for triple glazing though as the obvious issue is our new aluclad windows are on the crap side of performance & we seem to have a lot of them!
-
We had a vat exemption on an empty bungalow & added a 2nd floor. Did a full refurb only saved external walls & concrete slab altered every other external opening. Came in at £1250sqm inc. 5% VAT. All looked after by a builder, we did the painting & laid a couple of basic floors/tiling, builder added EWI so it doesn’t feel drafty downstairs though there is a slight temperature differential by about 1C probably from that uninsulated slab! It seems pretty efficient & our energy use has been a fraction of the amount estimated on our EPC using an ASHP. But yes it has it faults & we would have underfloor heating if we’d started from scratch but there are scenarios where it does work out better & I’m happy we saved 150k as the faults are not worth that much to me (plus unless you lived on the street most people who visit think it’s rebuilt). The rebuild rate was about £2500sqm when we did ours and is currently at £3500sqm. We had some crazy quotes so be careful with the figures the architect tells you unless you can do much yourself! Also round here it takes about 2 years of planning to have all the permissions to start a new build and quite a bit of expense with all the conditions they add, so the type of planning authority might also be a factor - this might sound like an exaggeration that I don’t have experience of but I also work in this authority so it’s not second hand info, it was a big deciding factor for us.
-
Yes rockwool fitted, we came every day! There was a bit of an argument over plasterboard thickness so we agreed to 12.5mm instead of 15mm specified, maybe if we’d of looked into it we might of ditched the osb for thicker plasterboard, but I don’t know what really would of worked best, it’s definitely feels more hollow than our crappy 1980s masonry bovis home, but it’s also bigger & we don’t own much stuff so probably doesn’t help with how noise travels.
-
No it wasn’t architect spec’d it just because of being able to affix things easily, we also have external osb & EWI on the outer frame so there’s a lot of osb & I presume the outside osb will act as the bracing. Of course no one realised or questioned this until the work was started & we just went along with it..