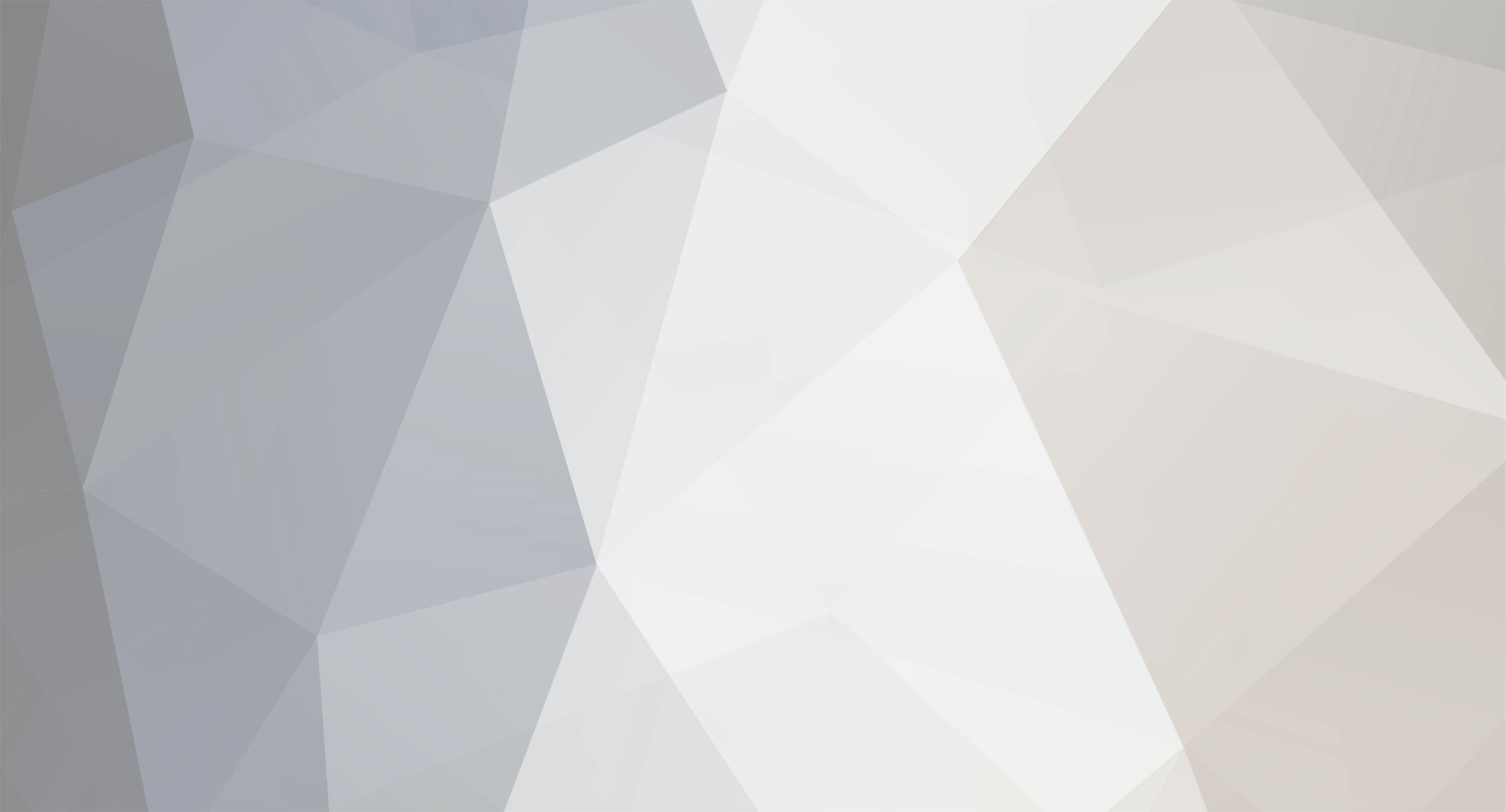
romario
Members-
Posts
43 -
Joined
-
Last visited
Everything posted by romario
-
RSJ Vs engineering joists for flat roof
romario replied to romario's topic in RSJs, Lintels & Steelwork
Thank you. There was a bit of learning to be bending the 25mm x 50mm battens. Going at the bottom of the roof on 10m radius was relatively easy. However, going higher and higher was challenging. At the end to be able to bend those on the top it was a combination of: - selecting battens without any knots - soaking in the water - then none of the battens were perfect straight anyway so then was trying to lay them in the direction that they are already bend. Fortunately I didn't need to go as far as steaming boxes Below photo showing precaution to avoid cracking on the knot Top rows shows the slates coming on larger angle but still the corners don't stick out too much that was mine worry. Still not sure how to finish off the top raw Possibly with lead? -
RSJ Vs engineering joists for flat roof
romario replied to romario's topic in RSJs, Lintels & Steelwork
Hi Mr Punter, Yes, it is for the Roundhouse to close a big hole Let me share some photos from the roof -
RSJ Vs engineering joists for flat roof
romario replied to romario's topic in RSJs, Lintels & Steelwork
Thank you for all your replies they were very helpful. Let me share my decision and design with you who replied and anyone else who may benefit from it in the future. At the end I decided to go with the web joists because: 1. Easier to handle and put together comparing to steel specially when installing with one helper and on 6 metre height. 2. Web joist supplier done all the calculation so no need to get separate structural calculations. 3. Web joists supplier manged to get the roof working with 219mm depth web joists. 4. With those wide web joist (width between 100mm and 150mm) it is so easy to attach ceiling plasterboards 5. Roof insulation. I need to educate myself a bit more but I came across what is called hybrid roof ( warm roof insulation on top more than 50% of total depth and then remaining insulation between the joists) As I said I need to educate myself in that topic to make sure there are no condensation problems. 6. Easy to run any ducting in the ceiling. On the other side the cost of the below design is £2500 inc vat so probably significantly more than a steel and infill timber but looking as a whole I thought the web joists was a better option. Thanks for your comments and I hope this might be helpful to someone else in similar position. -
Hi, I would like to share my thoughts and ask for other people opinions. I need to make 6m by 6m flat roof with 4 skylights. I've been a fun of engineering joists because of the light weight and how easy they are to install as well as how easy it is too put any ducting or pipes etc. However, with the timber price increases the quote that I am getting for engineering joists works out nearly double the price comparing to putting RSJ in the middle to half the span from wall to wall and use timber joists from RSJ to the walls. Also there is 7 weeks lead time on engineering joists while the RSJ can be bought of the shelf. The downside for RSJ is that will need to get structural engineer to confirm the spec and few people to lift it up :) I have a dilemma what to go for. Please see attached drawings. Thanks in advance for any comments.
-
Synthetic slates Vs natural slates and colour scheme
romario replied to romario's topic in New House & Self Build Design
Thank you for your comment and the pictures. I've seen those pictures as well online and that particular room is probably one of the best I've seen. That person cut every single slate to achieve the half bond. However, you can see how narrow the slates are at the top and the top rafters where not that long. I think I will probably need to go for random pattern but it is difficult to visualise until you put couple hundreds slates... -
Synthetic slates Vs natural slates and colour scheme
romario replied to romario's topic in New House & Self Build Design
Thank you Mr Punter for your comments. The current pitch of the room is 25 degrees which is ok for the synthetic slates and just about ok for natural slates. Because of the weight I haven't spent too much time on clay tiles. Initially I was planing to cut every slate to achieve perfect half bond. However, as the top rafters are nearly 8m long and the spacing in rafters goes from 600mm centres on the outside to 190mm in the centre that means if I started with 300mm wide slate at the bottom the slates on the top would need to be less than 100mm wide. I am not sure how such a narrow slates would look on the large roof. Then I've started considering going for random pattern which would be a lot more efficient. However on each next raw I will need to loose few slates. This will need to be done by either cutting 3/4 slate or half slate. This may not look pretty... -
Synthetic slates Vs natural slates and colour scheme
romario replied to romario's topic in New House & Self Build Design
I am not sure if I can get the credit I bought the land with planing granted for the roundhouse so I suppose there was no competition from professional developers when buying the land. I suppose my job is to try to make the best of it and look at the positives of the roundhouse -
Synthetic slates Vs natural slates and colour scheme
romario replied to romario's topic in New House & Self Build Design
Thank you for sharing your experience. You've raised a question in my head. If you go for natural slates and you get some that you are not happy with is it a normal practise that those can be returned /refunded? -
Synthetic slates Vs natural slates and colour scheme
romario replied to romario's topic in New House & Self Build Design
Thank for your sharing your experience. -
Hi All, I had some delay due to other work commitments. I am now back with the build and I need to decide between synthetic slates (Tapco / Britmet) and natural slates. I've put it below my thought process that might be useful to some but I would love to ask the community two questions: 1. What colour would go for the roof for that project? Brown or Black 2. Would you go with synthetic slates or natural slates? Here is mine decision making process based on limited knowledge: Synthetic (Tapco, Britmet) Positive: All uniform thickness, no selection needed. Also because of that possibly less sticking out edges on the round shape. Easier installation as lighter and pre marked for gauging Less likely to get damaged if I need to walk on them Natural Spanish slates Positive: Cheaper Possibly fewer slates as the required overlap is smaller and the gauge is larger Proven long term durability and appearance Natural product Non combustible When cut it still have original edge finish. The roof pitch is 25degree I have attached few photos Architect 3d vision Roof trusses Trial with synthetic slates to help me decide on the product and colour Thank you in advance for your comments
-
Thank you for your comment. I am based in Bedfordshire
-
Thank you Russell for your comments. Would you advise to cover from the top of the wall to the bottom or only the top couple rows and window openings?
-
Due to the delay with planing application change I wasn't able to put the roof before winter. I have exposed Ytong blocks up to the wall plate height. I would like to ask if anyone has any thoughts / recommendations in terms of protecting the walls for the winter from rain / frost to avoid any structural damage. Thank you in advance.
-
Thanks for your comment. I agree with you than when selling the value could be lower due to the lack of mortgages availability.
-
The plot has half an acre including the property. I have ambitions to use the remaining garden for kids activities and growing your own vegetables / fruits following permaculture principals. So if decided to go for green roof that would be partially also for growing vegetables The image below is the closest I could find in google images in terms of what it could look like. However, the limitation or no existence of mortgage availability is putting me off from the green roof idea.
-
I wonder if anyone is aware of lenders that would be happy to lend on properties with green roof. Initially due to the mortgage restrictions I didn't consider green roof. However the more I progress with the build the more attractive green roof becomes to me. The image below is showing approved design and what I am building but I've been thinking of flat green roof with raised centre part that would allow entrance to the roof. I will appreciate any comments.
-
Thank you Russell and Nod for your comments. Both of you are right. 300mm between window and ceiling looks good and with standard ceiling height of 2400mm and standard door 2100mm all works perfect. However, the reason I have increased the ceiling height and thinking of taller openings is that some of the rooms are quite deep and so to get more light specially through the open living to the kitchen (I've pasted the floor plan below) Then with the increased ceiling to 2600mm if I go for standard 2100mm openings that will leave 500mm between the top of the openings and ceilings which I am worried that will look out of proportion. Also will not meet the first objection to get more light further into the building. Good point about the cost of 2300mm height doors. They will need to be made to measure but there are 3 sets of French doors for the whole building so shouldn't be too much. I will welcome any further comments. Roundhouse floor plan with room dimensions.pdf
-
Hi All, After long thinking I am most likely to go for 2.6m ceiling height. I would like to ask other members what distance from the ceiling they would put the lintels for windows and French doors at that height. Would you prefer the set up on the left or the one on the right? The opening on the left would have lintel at 2330mm from the floor and about 270mm from the ceiling The opening on the right would have lintel at 2220mm from the floor and about 370mm from the ceiling The length of timber on the top is showing the wall plate. I will appreciate any comments.
-
Hi Dave, I've been thinking of doing the same on my new build because of the low FIT. Have you considered getting batteries for storing unused electricity. I came across recently an idea of using electric car as a battery storage but haven't looked into that yet.
-
Internal partition walls Stud work Vs block work
romario replied to romario's topic in General Construction Issues
Thank you for all the contributions. I find this forum amazing that I ask for an opinion between A and B and the conversation goes so much further and people come with options C, D and E that I haven't thought about. -
I would love to hear other people thoughts on deciding whether to go for stud work with plasterboards or block work. The property is a single storey and I am currently thinking of doing a bit of mix of both. Dense concrete blocks on: Walls on South facing side of the building to increase the heavy mass and for the sound insulation between kitchen / living and bedrooms Studwork on: Kids bedrooms, corridor walls, reasons for that: Easier to run any cables, safer for kids when they heat plasterboard wall comparing to concrete wall; It is a lot softer, I've done it myself Mixed filling on bathrooms. For sound insulation I would prefer block work but it is easier to run and hide plumbing pipes in the studwork. It would be great to see other people opinions.
-
Solid wall block choice, Ytong, Celcon, Thermalite?
romario replied to romario's topic in Brick & Block
I suppose I had a choice to cut the 3m bar lengths to shorter lengths and overlap the rebars. I left the 3m lengths and went for the standing platform to slide the block down but it is a 2 people job. I've chosen the hard way but without cutting I've been filling the hollow blocks every 4 courses as I am not sure if it would be a good idea to leave them free standing on its own. I suppose they are not very strong without the rebar and infill. -
Not sure if this is the best place for this post. I am relatively new here just made few posts and got really interesting comments. I wonder if it would be of interest to others either more experienced or beginners to meet sometimes on the self build site for a chat, learn from each other experience / mistakes / see it in real life. I am doing my project around Dunstable (Bedfordshire) if anyone would like to come and visit I would be happy to share my lessons and plans.
- 1 reply
-
- 2
-
-
Solid wall block choice, Ytong, Celcon, Thermalite?
romario replied to romario's topic in Brick & Block
Below DPC structural engineer preferred concrete blocks. I could either go for solid concrete or hollow concrete and fill them in with concrete. As the wall thickness is 215mm solid concrete blocks would need to be laid flat as the largest size I could get in solid format was 140mm x 215 x 440 I understand this is due to the weight of the blocks. I suppose the cost of laying solid blocks flat and so more courses comparing to hollow blocks and filling them in would be similar. I decided on hollow because when filled in with concrete they are actually a lot stronger. Also on South side there will be quite a few larger window openings so the hollow blocks when reinforced with steel bars and concrete can be used for columns. You can see on the photo the metal bars going down right to the footing. -
Solid wall block choice, Ytong, Celcon, Thermalite?
romario replied to romario's topic in Brick & Block
Thanks for your comment. I've been thinking about the ICF but there were couple reasons whey I decided on the solid block work with external insulation. 1. Being my first house build and roundhouse on top there was no way I could commit to fixed design at the beginning of the project. I am a person that I can make better decision seeing the things in real than just on the drawing. Right now I built up the walls up to the windows opening and I am still fine tuning the exact locations of the windows. This wouldn't work if I went for a big contractor but because I am hands on I suppose I can be a bit more flexible. 2nd reason was that because the house had planing with external cladding anyway I preferred the idea of having the block work on the internal side and insulation on the external side (A bit of the european style:) ) 3rd reason being already unique shape I wanted to keep it reasonably standard construction for mortgage purpose. I don't know if most lenders are ok with ICF. However, when I was checking every block for the first few rows with a long timber stick sometimes I wished I went for ICF