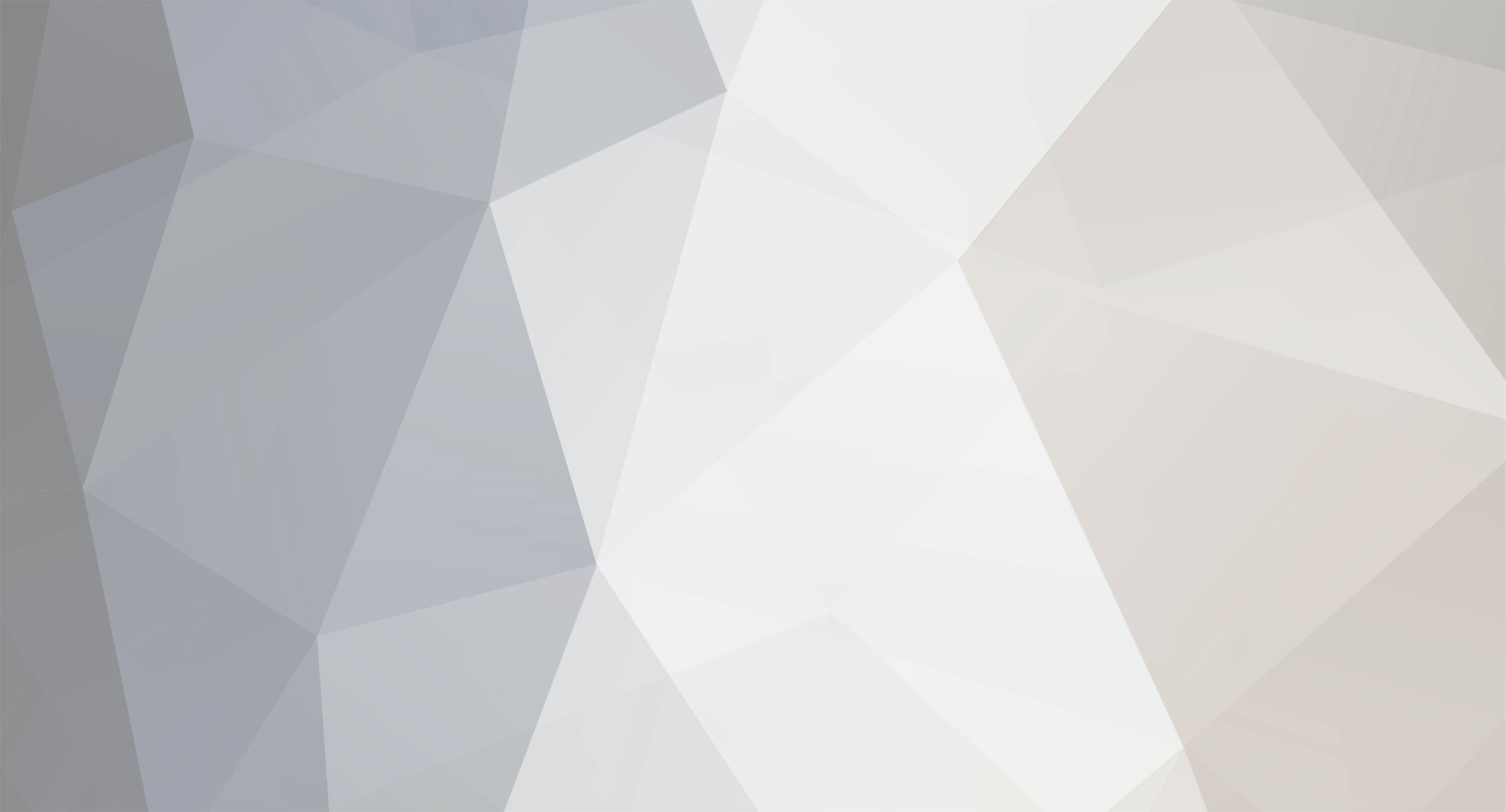
ash_scotland88
Members-
Posts
294 -
Joined
-
Last visited
Recent Profile Visitors
The recent visitors block is disabled and is not being shown to other users.
ash_scotland88's Achievements

Regular Member (4/5)
29
Reputation
-
Looking to order a caporra ceiling hood, the exhaust is rectangle from the motor. I am presuming it's easier to core through the house with a circle it'll be neater etc etc, even with builders employed than trying to form a rectangle shape in brick/brick. With that in mind when should the shape change to circle? From the motor, before the exhaust? Not at all and tell the builders to get on with it...
-
I'm wondering on techniques how this may be typically done. Property is brick/brick and filled cavity. I've read of running the cable in the cavity, which itself has potential for problems with damp and difficulty when cavity is (partially) filled. Obviously there's up to the soffit and into the attic, down into the solum or horizontally to enter at an other point. But in an ideal world the cable wouldn't be on show from outside, both for aesthetics and but more importantly saves tampering with the cable. I'm not sure if I'm being overly cautious/ paranoid to have a channel and conduit in the interior walled, with the cable exiting from ceiling/floor void level. The ceiling will be coming down anyway and other plastering works. Externally it's probably an ideal height to install a camera or two. So, yeah, any thoughts?
-
Looking for a sound out as I know there's a bunch of knowledgeable lot. I have a butler bell system I need to move, it's an electric 1930s one. I've lifted the floorboards above and can see it all (bell cable and power) going down into a conduit feeding the system. Power to it, I think I may be able to get away with reusing the existing, as I'm moving it closer to CU and it looks like it may be powered directly from it. If not wago box with trimming existing and extending with new. The bell cable, there are 10 bells, so 20 connections. Looking at CEF I was thinking about 2lengths of the 12 core SY control cable. But unsure of thickness (don't have a caliper to measure existing), the system is powered via a transformer, am I safe bets going for 1mm or think I could get away with 0.75mm. Two separate lines instead of one for ease, i still need to check sizing under counter battens. To make the connections I am looking at the 24way alarm junction box from Amazon. I've not been able to find anything else. Any thoughts guys?
-
Removing Baxi Burnall
ash_scotland88 replied to ash_scotland88's topic in Stoves, Fires & Fireplaces
Thanks RobLe. I was convinced the basket was hung in the opening. I've got in mind the other one we had removed was the same, but all drawings online show it should be recessed into brick. I should be able to nip under the floor to inspect this one before any works commences. I know the ventilation is just to the solum. But yes, heatloss is my big concern. Good bit of natural ventilation but you can feel the draft even with it shut and chimney rammed with wool. My final plans is to keep it minimal, no idea what with and how. But the classic clarence arch is a mottled beige with brown speckled. -
I want to do, the perhaps sacrilege thing, if removing a Baxi Burnall. Issue being as it's recessed into the floor and the hearth is tiled level to the floor we'd like to keep the hearth the same. Anybody removed one before? I'm not even sure what to expect. If anybody is nosey to know why, it's a fire in the to be dinning area. We'll probably only ever light it when we host, that's if we remember to do so in enough time. 50% will have their back to a fire complaining they're too hot and the other 50% can't see it. Looking to put something more manageable in for ambience.
-
Hate these posts on FB hence trying to remain anonymous here.... Also first post in a long time, hi team! 👋 Works are (without posting plans) Internal chimney removal, upto first floor only steels are 2x length with 2xcross bracing about 3500long. External slapping, taking to two window outer edges. Steel 3200mm. Non supporting brick wall removal, including returns for cupboards 3500mm. Strip and fit kitchen, including electrics and plumbing Removal of 1400 non supporting wall and infill of door. Strip and fit bathroom, including electrics and plumbing. Ceiling heights are roughly 2500. Priced the kitchen and bathroom stuff side, and a cost for bi-folds supply and fit. Any ideas what to expect for the rest? Obviously I'am missing out details like insulation, board and plaster but will be done too.
-
Semi-planning front door improvements for the summer. https://ibb.co/QFtHvqb Image is our current step. The quarry tiles are slippy when wet, couple cracked and I think a couple have delaminated, if not here then definitely in the couple of verandas with the same tiles. Ideally needs a step too As it's a pretty big lift up. But I'm lacking ideas what to do beyond sand stone on top and render front, I doubt the pre-bought semi-circles would fit anyway so presumed a custom job is in order. But also worried sandstone is slippy when wet and icy. And a general question. What's the large tiles lipping over the front called?
-
Thanks, forgot about engineered as an option! I'm 35 and tired of building materials being faux, fake and mock and made from thin laminated of plastic with low quality effect printed on and really not offering much of a saving..... Hopefully that's my grumble over.
-
I'm wondering what flooring options there are, and thoughts of each type? We're after "wood" (plank, in oak, exact style not settled) there's. Issue is being bathroom and bare footed I want it to feel real underfoot. We have SPC in the study (not lasting probably our poor DIY install) and as the name suggests it's plasticy to sound and feel. Parents have laminate through out at there's and again it's not a pleasant noise or sound. We're currently considering LVT and ruled out tiles as they'll be cold once the heating Matt cools down. Real wood, obvious concerns are of water damage but is there anything that can be done to protect them but it's what I would like? Sub-floor sheeting over timber joists, the original boards are beyond saving and will be worse once the room gets knocked about.
-
Thanks @Bozza it's good to know I'm not going crazy over this one detail. We've talked about having a (fake) living wall along that wall. The whole outside in, lying in the bath and looking at the trees etc so I think a half height stud would work as the "living" element will have a depth that hides any changes.
-
I'll get something up later, but thanks! Didn't even think about drilling and fixing near the each of tiles being an issue. I did have the other thought that we would like a shower niche, recessed shelf. If a tile fitter could cut out part of the tile (essentially creating a U shape or a hole in the middle) or if it would best to find a niche with an opening same heigh as the tile-600mm
-
Few questions looking to get some opinions from those with perhaps experience of these musings. We are thinking about paneling to a height in our bathroom, when we redo it. Less of the rebuking of paneling please. We are thinking of using the "precast" MDF sheets for ease and cost. I'm just looking for opinions if this would be suitable for a bath panel and use of as a splash zone around the bath instead of tiles. It would be painted/glossed/sealed etc. You see plenty of examples of doing the same but I'm hesitant of longevity. We are also looking to align the bath central to a window (omnitub if anyone is nosey)and in an "alcove" which would require spacing the bath out 48mm from the wall according to CAD drawings. CAD also suggests our bath tap filler would reach the bath sufficiently if positioned direct on the wall. I see two options, either stud out the paneling full or part depth (i'm sure no-one will notice alignment off by 20mm) which would allow bath taps to be fitted onto the mini stud wall. Or creation of a shelf running the length of the bath and if doing this unsure if it would be tiles or if some sort of panel the same material of the bath could be purchased? and lastly tile sizes... We found tiles we liked that are 1200 wide, our shower enclosure would be 1200x760mm Obviously the length would be trimmed down, would it look odd having same length of tiles as the tray? I know the screen is typically set back from the edge of the tray, is this sufficient? Opinions, thoughts, inputs?