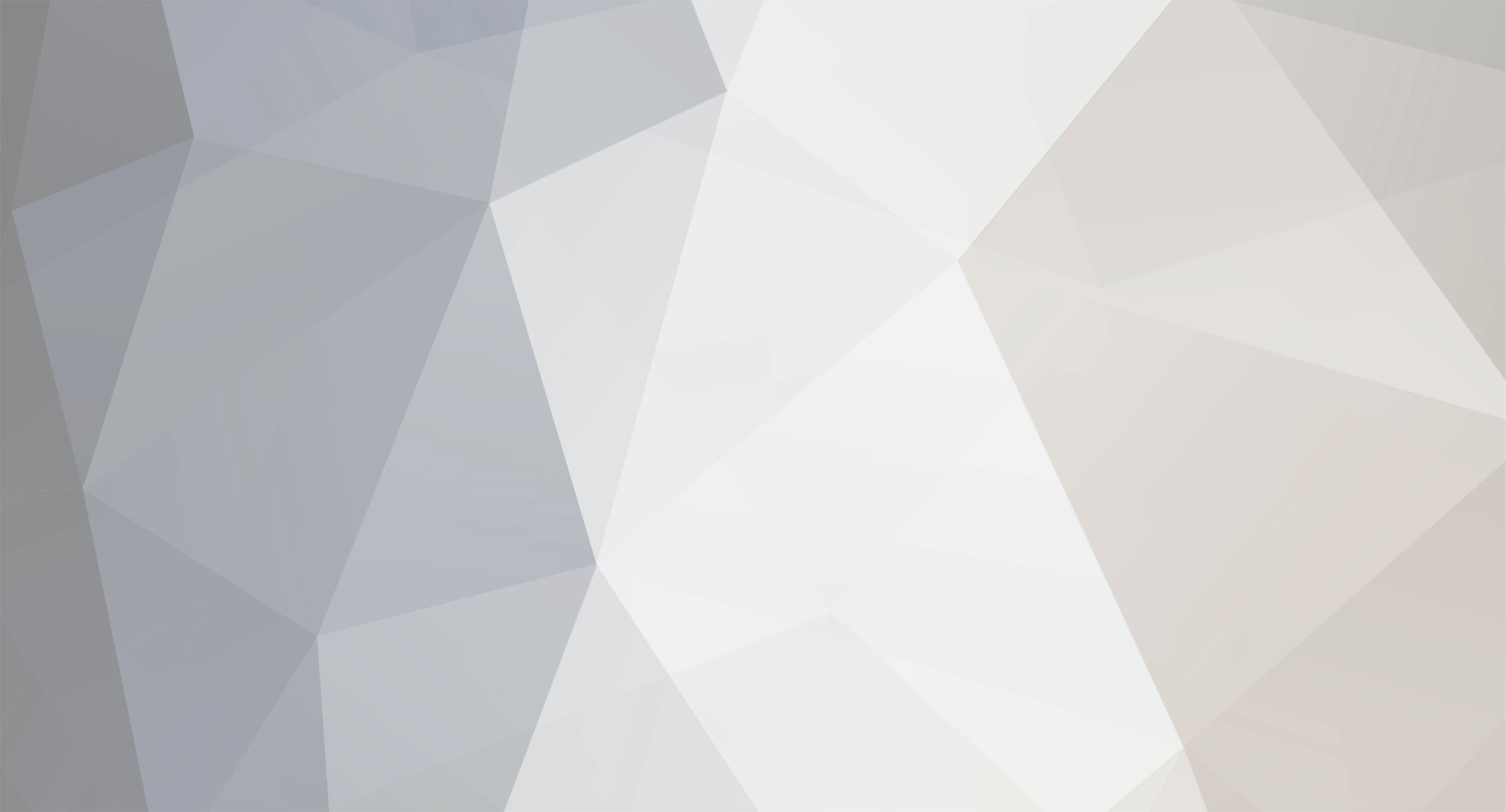
James_H
Members-
Posts
6 -
Joined
-
Last visited
James_H's Achievements

New Member (2/5)
0
Reputation
-
Hello all I'm not quite ready for to do the full MEV to MVHR retrofit I posted about a while ago, but need to replace some ceiling valves. There are a lot of valves around the £10 mark, but some fancier ones nearer £30 (or more). I've seen a couple of posts on looks: https://forum.buildhub.org.uk/topic/4782-aesthetic-considerations-of-ceiling-valves/ https://forum.buildhub.org.uk/topic/11560-ugly-mvhr-vents/ But something such as the Zehnder ComfoValve Luna looks interesting, as looking a bit neater than some others and supposedly offer acoustic benefits. it talks of the Coanda effect for the supply valves. The supply valve only handles 50m3/h (or about 14l/s), whereas the extract version will do 75m3/h (or 21l/s), so should be ok for the kitchen and family room needing one of each and 13l/s for the Part F requirement. It does have fixed settings for balance at the valve, though I'd plan to do it at the manifold instead. While £30 instead of £10, its not as excessive as the Lindab Airy needing various matching parts to be bought. Any particular experience with this brand, or is the relatively few posts on valves themselves means they are much of a muchness and not worth going for anything special?
-
There's no DPC and the floor blocks and beam ends are tight to the outer wall. I cannot be sure but I do not believe it was as a designed kit.
-
Thanks for the replies. It's not quite as much of a concern as I had first thought. I anticipate the DPC layer to be between the blocks and insulation. The PIR wall insulation technical doc advises to take it down to the bottom of the beams for this type of construction. Though with no cavity left at the door openings, the perimeter can have no more than the 120mm planned floor insulation depth below its top. Though it can go lower other than at the door openings.
-
I'm not sure exactly which would be the right sub forum but hopefully this is the right one. Though I'm not posting in the insulation board to avoid a biased answer. I'm having an extension built with construction details and thermal standards to be broadly the same as the newish build existing house. The beam and block floor has just been put down, but it is unlike any drawing I have seen where the door openings are to go. My construction drawings do not detail the openings, but match to what I would expect in that the ends of the beams and blocks go as far the edge of the inner block where it meets the cavity. For the sliding door openings, as built the beams and blocks have completely bridged the cavity. This bothers me that it might not be right and leave me with a thermal bridging problem. This is compounded by having no insulation in the cavity at or below the beam/block level. I have attached the drawings and a sketch of what has been built so far. The dotted lines will be finished floor level and patio outside. Note that DPC level for walls started already is higher up than that line as required. Am I right in being concerned about what has been laid? If not right, is it just not best practice, or is it something building control would be unhappy about?
-
MVHR upgrade from MEV
James_H replied to James_H's topic in Mechanical Ventilation with Heat Recovery (MVHR)
Thanks for the reply. For ground floor rooms, I would lift the carpet and cut temporary holes in the floor above. I am fortunate in that the joist directions run towards those shower voids. I was planning to use the 75mm semi rigid and realise that the semi unrigid nature might mean fund and games to thread it through. The MVHR unit I bought (Vent Axia Sentinel Kinetic Plus B) only asks the inlet and extract are at least 1.5m apart. I could manage further with any of those options, also chosen because the unit would go on that gable wall of the larger loft. Yes, I would need to insulate. -
Hello all. My six year old house was fitted with MEV by the developer but I’m planning to ‘upgrade’ to full MVHR. Although much MHVR goes on new build, plus some retrofit during refurbishment of older properties, I haven’t seen anything online about anyone upgrading existing MEV in this way. As background, my parents longed to do a self build, with MVHR oddly enough being one of the things mentioned a lot beforehand. It was installed in 2010/11, so I am familiar with such a system in practice. On buying my house new, the showhouses did have MVHR, but unfortunately all the others only have MEV. My original thinking was that I already have one half the of system in place, though perhaps I already get half the benefits. So while we get fresh air, humidity at reasonable levels and minimal condensation in the bathrooms, it galls me that trickle vents were cut into the frames of the triple glazed windows for supply and while I have two fans spinning 24/7, the heated warm air is just being pumped out. The extraction is not optimal – kitchen cooking smells permeate the whole house with the door closed, whether on boost or not. For some reason, only now are we getting some black mould in the en-suite bathroom. I have read up plenty since and so – as things stand – currently plan to go ahead. I’m also going ahead with an extension – highly glazed – and will need the SAP calc, so this is one of the few possible improvements I can make to the existing house if needed. (Loft insulation, firstly to building regs, though even better to the design spec, would be cheaper and easier so happening as well). The airtightness test result when new was 4.4 m3 /m2 hr @ 50Pa. Fairly average for recent new builds but certainly not spectacular. It’s below the figure where it should give some benefit, but above a level I expect some might think it’s not worth it. The extension will be built to a better standard, while there are some gaping holes in the existing house I am aware of and have filled or will do. Plus sealing up the trickle vents. Though at this sort of airtightness, I can’t justify a top end system professionally installed, it just will not pay back. Though I have acquired a good value unit and plan to do much work myself to limit expense. I don’t think I’ll necessarily use all that is currently in place. Rigid ducting was used for the extract and is not especially well sealed at joins where visible. The ceiling extract ducts were generally placed near the doorway, not at the opposite corner. The two existing roof extract terminals (there are two separate MEV units) are on the southern elevation but have insufficient free area to repurpose one as a supply and leave the other as extract. The manual boost switches might be the few parts I reuse. There is power to one of the MEVs that would also be the loft location – admittedly unheated – for the MVHR unit. I do have useful behind-shower voids at the front and back to enable semi rigid supply to all the ground floor rooms that need it, and back from the extract rooms. The doors already have sufficient gaps underneath. The reason for posting here is to ask a few queries on what I’m still unsure of. And if it does go ahead, perhaps be one of the few resources to document an MEV to MVHR upgrade. Savings are difficult to quantify at present. I would appreciate some hints on the following: Which of these positions, or something else entirely, would you put the external supply and extract terminals? A (Red): North roof through roof terminals, B (Gold): North roof soffits (might be easiest to install but need to watch the free area), C (blue): East gable end above the slightly lower roof. Overall I am trying to avoid the SW prevailing wind, be on the same elevation, far enough apart and be shaded in summer. I have seen a number of posts of DIY commissioning and producing the certificate for building control. As an alternative, there are a number of firms that can do testing, but is there a competent persons scheme for any of these testers? Reason I ask is that on speaking to building control they said it would be usual for installers to self certify as would be done for gas / electricity, in which case there is no BC fee. Though I have not found a similar scheme. If I have to pay the building control fee anyway, then I would probably test myself. Is this really worth going ahead with, or pulling the plug now? I am hopeful of getting this completed for under £2k all in for the parts, my labour counted as zero. One possible supplier for the large glazed doors for the extension wanted over £900 to add trickle ventilation. I’m not going with that firm, but whoever I use I avoid the need for those vents. Overall, I would hope to minimise the ventilation losses but have difficulty quantifying the payback. Non-financially, I would see benefits from input filtration (due to hay fever) and soundproofing from sealing the old vents. Sorry for the long post, and thanks in advance for any suggestions.