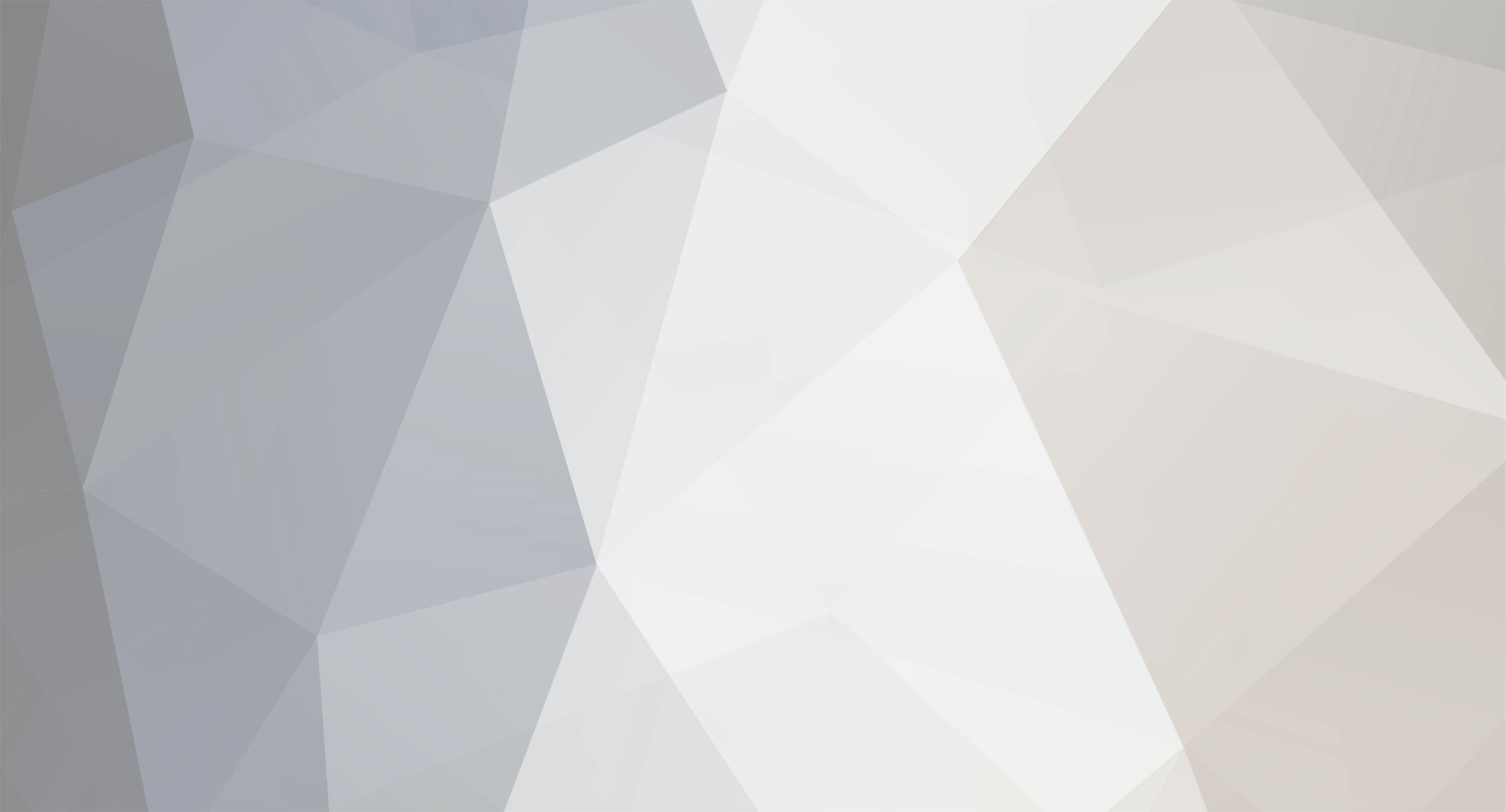
Night Owl
Members-
Posts
33 -
Joined
-
Last visited
Night Owl's Achievements

Member (3/5)
0
Reputation
-
Thank you Nick, i wouldn't have thought about it that way as I've been more focussed on maintaining the structural integrity of the installation. From the way you describe it, sounds like it's pretty common practice to 'chop' timbers before installation to address this type of issue? I'm surprised Velux don't pass this onto their approved installers as my window was actually fitted by one. Building control never mentioned it either when they looked at it.
-
Thanks for the replies. Personally I can't see what effect drilling a couple of small holes would have on the overall structure of the roof. For info, it is approx. 70 years old, made up of concrete tiles, 1x1 lats, bitumen felt, 4x2 rafters plus the 2x2 batons I've recently added to increase depth for insulation.
-
Thanks Wil, hopefully someone will be along soon to enlighten us. In the meantime, if I do find something I will post it here.
-
Anyone have any thoughts on the above?
-
Hello, I recently had a Velux window installed in my roofspace which will be used as an en-suite for the upstairs bedroom. I will be insulating between the rafters leaving a 50mm gap for ventilation between the roof felt and insulation. There are two areas (to the left and rightof the window) that will be effectively sealed off (due to double trimmers being fitted) from the ventilation path once plasterboard has been fitted. Would it be acceptable to drill these trimmers top and bottom to allow some airflow through the void? If it is, what would be the best quantity / size / location for these holes? Thanks.
-
Thanks again for the reply. Whilst I am lucky to have a blank canvas for my heating choice, I don't unfortunately have a blank cheque! I'd love to have a ground source heat pump but don't have the space or money for a bore hole system. I have however already installed the wood burner (multifuel actually) and am slowly building up a decent supply of logs for future use. Interesting info on air source heat pumps which I need to look into in greater depth. Interesting link you provided to see how heat pump installations are faring. Sounds like there is a lot to consider when designing a system for maximum efficiency. Finding a good installer who knows what they are doing could prove challenging in my area - only one listed in the link who also do gas and oil so not a dedicated renewables company. I agree that the price of oil is likely to go only up in the future as less and less gets extracted from the ground (if you believe this) but you can at least buy it when the price is cheaper during the summer months and store it for winter - something you can't do with electricity. I've never lived in a house where the heating is constantly on. I'm used to only having it on when needed which I know can be quite inefficient however my bills have always been reasonably low. As I'm getting older now and at home full time it could well make sense to have a system running all the time at a lower temperature for efficiency and overall comfort. Would be nice to not need an oil or gas tank freeing up some space. Lots to consider and research!
-
Thanks for your comments IGP. Interesting thoughts on insulation. My floors are unfortunately solid concrete with a bitumen DPM that has worked to a point but not completely. I'm planning on digging up some of the floors in the house to get some insulation in but finding someone willing to do it is proving a little difficult. I am lucky to have a blank canvas for the heating system that goes in, every option available bar mains gas. I have looked into heat pumps but always thought they only work well in a well insulated leak free house. I'm also nervous of being held to ransom by the electricity companies. Don't have the appetite for solar panels and battery storeage yet so may opt for oil heating. Has anyone ever heard of an oil heating system working with oversized radiators to run at a cooler flow temperature in a similar way heat pumps do?
-
No such thing as a stupid question! My aim is to improve the overall comfort within the bungalow without compromising the fabric of the building. I want the property to feel warmer, use a little less energy and have no future issues with damp (as a result of my work).
-
Thanks for the reply and advice on how you would tackle this situation. I have decided not to add anything to the exterior brickwork which is in reasonable condition and quite sheltered from the elements. I'm slowly going round sealing up areas where air can escape. I am realistic in thinking I won't plug every gap but will at least be able to make a decent improvement. Interesting that you would get rid of the cavity insulation and replace with beads. I understand that the beads are probably the best option for my situation and will look to getting a quote for this. Is it vital that the cavity is filled if adding IWI to avoid condensation issues? I presume the idea is that it will help keep the inner wall a little warmer?
-
Looking for thoughts on how others would tackle improving the insulation on my late 1950's dormer bungalow in the East Midlands. Wall make up is - Outer face 110mm red brick Inner wall 110mm red brick Cavity fill insulation is a white cotton wool material but lighter. Due to issues with damp I have had to clean out the lower part of the cavity walls above (and sometimes below) the slate DPC due to being full of material waste from the build. The cavities are now clear but as a result I have large voids around the lower part of the walls where the insulation has been lost. As I have removed all internal plaster from the walls I am looking to improve the insulation in and/or on the walls. Don't want to go EWI as I like how the bungalow looks as it is and it would be quite expensive. I'd like to batten out the internal walls that form the outside walls and add insulation and an Intello plus vapour barrier, then board and skim however I am concernedabout potential condensation issues going this route. Should I get the CWI removed, replaced or try and top it up? There is space in the rooms to add around 50mm extra IWI without looking odd. I have used sheep wool to insulate the loft which I like as a product although very expensive. 50mm in the walls won't make a lot of difference so would be interested to know what others would install. Thanks.
-
Haven't found a concrete company yet interested in delivering, probably due to the small amount. Quite a few don't carry pumping equipment too so that would be an extra hire cost. Looks like it might have to be done manually Anyone got a good formula / mix recommendation for waterproof concrete?
-
Hi, no not that I can see however the door that accesses the room was on an outside wall.
-
Looking for a few pointers in regards to the old boiler room in my house (1950's bungalow) which would have been originally solid fuel. It is approx. 3.28m2 and was constructed partally below ground for some reason but has long been removed. The floor level in the cellar is about 800mm below (slate) DPC and usually has between 6 and 12 inches of water in it during the winter months. Picture above was taken today where it has all but finally dried out. I want to bring the floor level up in this room to match the rest of the house, so approx. 800mm needed. My thought was to get a concrete company in to pour waterproof concrete to approx 300mm below dpc (1.64m3). Install DPM, insulation 200mm, 50mm concrete then screed to existing floor level. Can anyone see any issues with this approach or suggest a better (easier) way? Would also be interested to know why it was built below ground level. Thanks.
-
Thanks for the info Gus, makes sense. Just for clarity, when I posted earlier that all of the lintels at my property are the same, I didn't mean they had all been cast incorrectly. Just the one rogue one as far as I can tell! There are a couple of doorway formed from brick arches which look quite impressive from an old school builders point of view. I won't post any pictures of them as it could lead this thread down a whole new debate. Thanks again for all the input.
-
Thanks for the responses. I think the Lintel failed as it had been cast badly, probably 70 years ago. Only two bars in it and both next to eack other. All of the lintels in the property are of this type and set in brick that wouldn't meet current best practice. In the end I set it on a mortar bed and packed out above with slate before pointing up. Very little weight, bungalow non load bearing wall. All of the remaining lintels look solid with no signs of any movement. S.E didn't raise any concerns.