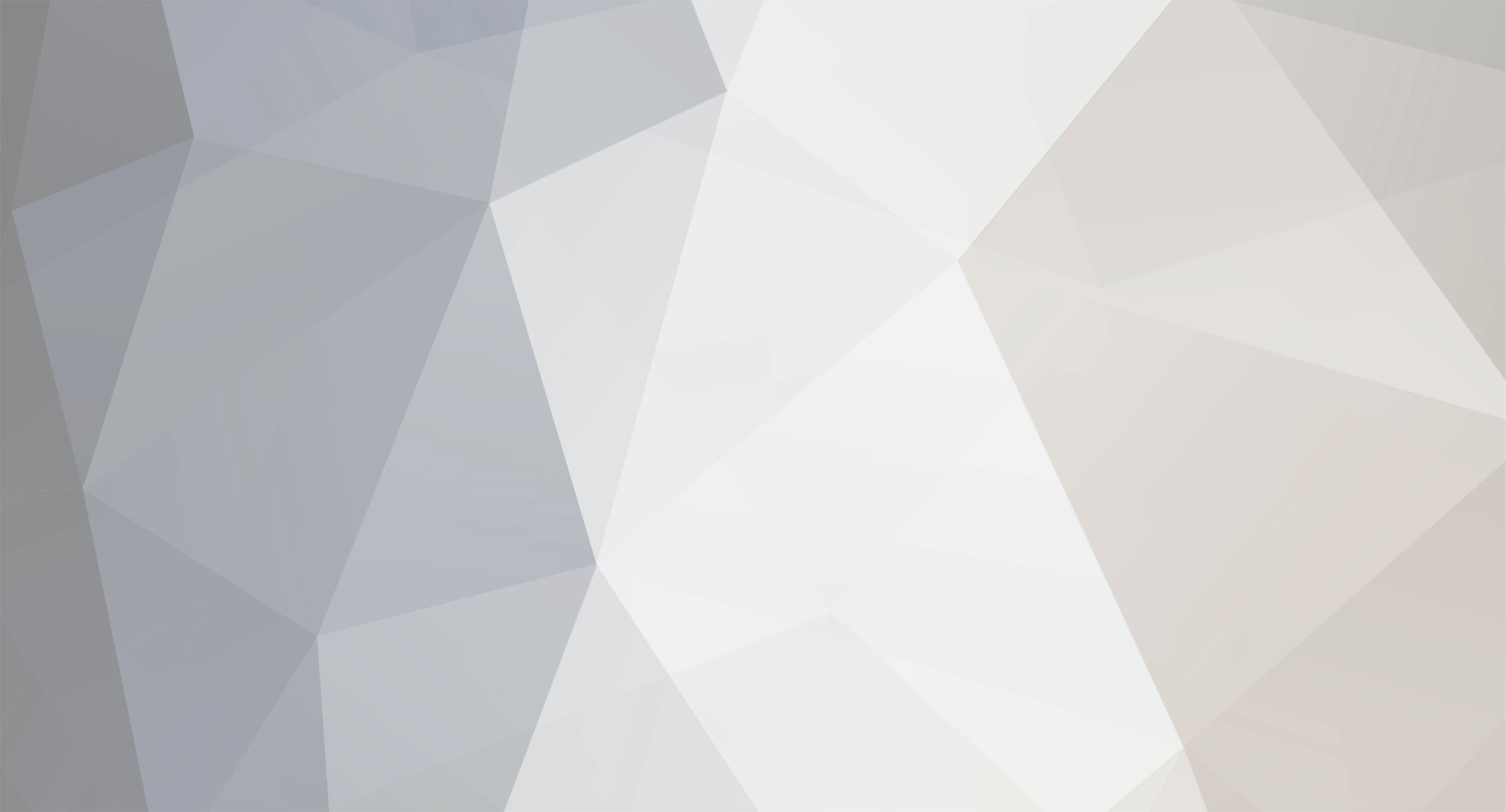
Bruce
Members-
Posts
22 -
Joined
-
Last visited
Personal Information
-
Location
Reading
Recent Profile Visitors
The recent visitors block is disabled and is not being shown to other users.
Bruce's Achievements

Member (3/5)
0
Reputation
-
Feels like a very straight forward piece of work, I wonder if I can get away with a onlione SE?
-
We are converting our coservatry to a habitable space, thus adding a insulated roof which the curent wall is not suitable for. So a beam will we added, resting on a brick column on a new pad foundation and a more robust wall in the other end. The new pad is going to the upper right corner on the drawing. The load from the column, roof (as shared between the two ends of the beam) etc. on the pad is estimated to be 7kN +100% margin=14kN. I have calculated the area of the pad to 500x500mm as per Table 10 of Approved Document A. Thickness is assumed to 400mm thick. I would prefere to not have it so deep but I have allowed to the depth to underside of pad to be 1000mm in line with Section 2EA as we have clay soil and I don't know how to show its shrinkability. A concrete column will be made to get up to the concrete floor level where the builder will make a brick column all the way up to the beam. I'm worried to about our building control, I don't seem to speak on the same wavelength as them so I'm trying to be proactive here as they are coming around to look at the hole where the pad is going. Have I done enough to calculate this, how can I prep so I'm prepared to make them happy without having to make bigger foundation than needed?
-
Garden Room - 'substantially non-combustable'
Bruce replied to having a go's topic in Garages & Workshops
I'm would be happy to put up fire rated plasterboard on the inside and steel cladding on the outside on the wall towards the neiboughrs garage but I have a hard time understanding when enough is enough and how much details I need to be carefull about. I want to do it right but it doesn't seem reasonable that I need to pay hundreds of punds to the BCO for their confirmation, especially as they don't offer any advice, the only check what is being submitted.- 8 replies
-
- building regulations
- garden room
-
(and 2 more)
Tagged with:
-
Garden Room - 'substantially non-combustable'
Bruce replied to having a go's topic in Garages & Workshops
We are about do the same but with a garage. What was your BCOs response? Ours are being awkward and I don't get any good responses from them.- 8 replies
-
- building regulations
- garden room
-
(and 2 more)
Tagged with:
-
We are preparing a new garage which we need to pull both electric and data cables to, at some point the ducting need to change from what is underground to the ducting the will run outside along the house to meet up with the consumer unit which is inside together with the network connection. I'm thinking that I should bury ducts, perhaps 2x 50mm O.D (intend for 10mm cable for potential PV inverter hense the size) and then teminate them into connection boxes on the house, the other end will terminate inside the new garage so they don't need to be water tight. But twin walled flexible ducts of this size doesn't seem to have glands or the glands cost £30 each which feels redicilous. The length undergrouund is only about 2m so could be done with rigid ducting if there is any that can be burried underground. My two picture below is for the whole length, our consumer unit is behind/indoor of the EV charger and the current carport is in the same location as the new garage, so I'm thinking that the interface between undergorund ducting and the wall conduit is near the ASHP isolator. Does anyone have any idea on how to do this? I feel like this should be done on many projects so I'm a bit suprised to not find a good interface between undeground ducting and rigid ducting/connection boxes.
-
Thank you Joe. After reading this thread once more I think I start to get the difference between the planning and building regs in this matter. I would be delighted to get some help with the design of the slab, even though this might be a spring project as the time just flies away with doing the rest of the house.
-
Joe that looks really nice. Me and my partner are looking at doing a garage in the same style as you but I'm worried about planning as it is is within 1m the boundary, bigger than 15m2(ideally) and made of timber. How did you go about your planning permission? And as I presume you went after PP in the end, how did you design the slab? I would like we already have some concrete hard standing under our carport which it will replace but it is not big enough, even enough or high enough so will likely need to add a slab on top of it.
-
I'm finally about to install the extract and intake ducts/terminals to our MVHR, I have abandoned the idea of venting to the facias as the space between the roof and the top of the external wall is only about 80mm so it will go through the roof instead. We have clay tiles that are about 160mm wide, picture from inside and outside of the roof below (sorry for that bad external picture, it's taken from the ground). Would the Ubbink UB19 work for intake and extract? It looks like it replaces 1+2+3 tiles, is that correct? https://www.roofingsuperstore.co.uk/product/ubbink-ub19-500mm-x-460mm-slate-vent-anthracite.html I would also have to add the 'adaptor' to be able to get the ducts on it + a steep down to our 120mm ducts. https://www.roofingsuperstore.co.uk/product/ubbink-felt-sleeve.html https://www.roofingsuperstore.co.uk/product/ubbink-stepped-adaptor-1.html Can anyone spot anything wrong with my assumptions/ plans?
-
That is a fair assessment but the amount of work with ripping out the old pad, the subbase under it and the pour a new pad is a lot more work than doing what I describe above and also much more costly, I'm not sure that the extra insulation added will ever be worth the investment. What it would likely enable though is a presumably easier routing the extension for the airing bricks, that solution is really what I would love some help/examples with.
-
We are planning on insulating an levelling the floor in our extension which was made in the 60s. The floor is concrete with tiles on top. We are planning on putting down a DPM then 100mm Kingspan Thermafloor TF70 with another layer of vapour barrier and then lay 16mm UFH pipes and 32mm liquid screed which should leave us with 13mm to lay tiles on top for the utility room. Total thickness we need to achieve to be level with the suspended floor in the next room is 145mm. The suspended floor in the next room is the where it gets a bit tricky. The airing bricks are just open into the extension and will presumably need to extended. So the question is, how do we do that with the least need to breaking up the old slab, or perhaps we don't need to do that at all somehow? And then, how do we connect the extension so the external walls in a good way? Attached are a couple of pictures of our utility room and our lean to/ conservatory, the floorplan with red drawings on how I think the 3 air bricks needs be extended, and the technical drawing from Kingspan that I think suit our situation. Any thoughts on how can do this?
-
Small update on this topic. We have now booked an install of the Gledhill 180 litre tank, PLUHP180, to be installed in a couple of weeks and will run it on immersion with a timer at the start. Is it standard practice to install a TMV to avoid scalding and minimise standing losses in pipes? Thanks everyone for your input
-
Many good comments here. Having a larger coil and the immersion element closer to the bottom both for now as we are going to use that as main heat source but also for better usage combined as a diverter with PV in the future sounds like good comments. The Gledhill 180 litre tank, PLUHP180 seems to be almost identical in actual usable volume as the Vaillant 200 litre version but with a 2.5m2 coil and has the immersion heater very close to the bottom. My understanding is that it has 28mm connection for the coil as well which should reduce risk of problems with the future heat pump installer. We are not getting any installers that doesn't know have to plumb a tank.
-
Yes it should be enough, it is a small 3 bedroom semi-detached with only one bathroom with a shower, so never any bathtubs to fill. No PV, it is on the which list but it will probably take a couple of years until we can afford that. The loft hatch is 68x78cm and is as big as it can get due to wall limitations. The loft should be able to take the weight, we have a plan to put up more 100x47's and put a platform on top made of 18/25mm plywood, this will be on top of a wall and just on the side on another T-connecting wall. I have made a post about it but think it was a bit confusing perhaps. Deciding on specific heat pump brands is hard, we have had huge problems getting quotes from heat pump installers, dragging out on time which is why we now have to install the cylinder separately so we can move into the house and accept that we have to live without heating in the house as we had to remove the gas boiler as part of the refurb and was promised by two companies that they would be able to quote and install the heat pump before end of Feb (We where promised this in late November last year as soon aw we knew we where actually getting the house). The size should be fine, see my response to TonyT above. The heat pump size I have calculated should be between 6-7kW. That is a good comment, I wonder if going from a 1.4m2 to 3m2 coil actually halves the reheating time or if it is more like 25% quicker, I would love to see some testing of this!
-
We are about to get a new hot water cylinder in the loft that we will run on immersion until we get the heat pump installed later this spring and our plumber has recommended the Vaillant 200l heat pump-ready cylinder, uniStor. I suspect he has recommended this mainly because they also install heat pumps under Vaillant umbrella scheme. These cylinder seems quite popular and it has the advantage that it is a bit shorter than many others of the same size, this is good as we can only fit a 1400mm tall cylinder with a 50-55cm in diameter. My concern is that these cylinders have a coil size of 1.4m2 whilst others from Gledhill, Telford etc have about 2-3.5m2 coil area, quite a lot bigger. Does this actually affect the SCOP of the heat pump or is it more of a matter that it takes longer to heat up the water when it has a smaller coil and such the house sits without heating for longer? Any other reason to not use a Vaillant cylinder when not knowing what heat pump we might end up with later this year?
-
We are going to put the new unvented cylinder in the loft to save space on the first floor. The first floor walls, especially the one between our two larger bedrooms are not built with load bearing support right under them on the ground floor, instead they are built on the floorboards that are supported on joists (brown in my drawing) that in their turn are resting on the external walls and beams (beams are blu in my drawing). The wall between the bedrooms is the red one, I have drawn it on the ground floor as well to show that it sits between the beams. The walls on the first floor are built of medium blocks/aircrete blocks. I cannot put the cylinder on top of the wall that runs in the middle of the house as the roof support is in the middle so it would have to sit to the side where there is not enough head clearance in loft. I think the best place is on top of the wall between the bedrooms. I have drawn my platform for the cylinder in yellow, my idea is to add 3 more 100x50mm beams/(joists?) next to the one that the roof supports are resting on (shown in my photo) and then put a 25mm marine plywood sheet on top of them to create a platform. The cylinders we are looking weigh about 260kg when full. What are your thoughts, if this good or should I do something different?