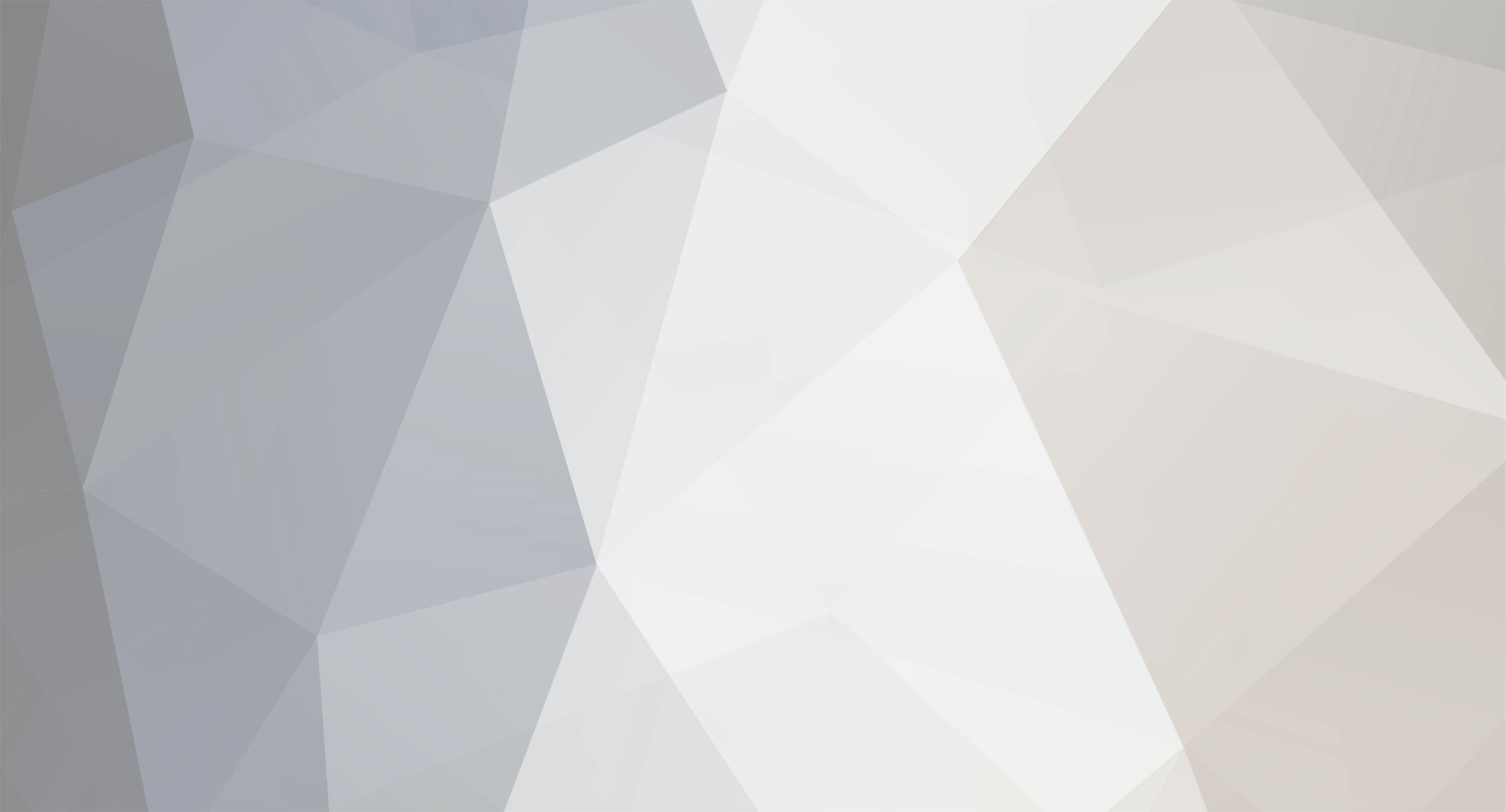
Chathura
Members-
Posts
10 -
Joined
-
Last visited
Personal Information
-
Location
United Kingdom
Recent Profile Visitors
The recent visitors block is disabled and is not being shown to other users.
Chathura's Achievements

Member (3/5)
0
Reputation
-
That's a very clever solution as well. But when considering the costs for both PIR insulation boards and insulated plasterboard together, that's going to be really expensive, isn't it?
-
Even though this is an old thread, I believe this situation is still valid and more relevant to 2023 due to 2022 and 2023 amendments in Building Regulations - Part L which requires a wall construction with a U-Value of 0.18W/m²-K. Our engineer has made a mistake or probably his draughtsman has copied-pasted a detail diagram from one of his old AutoCAD drawings. Therefore, the footings of our extension were already built following the specification below. This was sent to me somewhere in the middle of 2023—but this does not even remotely address the U-value requirement. But unfortunately, I trusted them and never had a secondary verification from someone else. The building control officer also never gave me a straight answer (I've seen it from many authorities in the UK. They don't give an answer that they would hold accountable. They give double-sided responses so we have to stay prepared to waste time and money if they suddenly say something else in the end. This also happened when I was getting approval from the water company for a public sewer diversion). Therefore, I now have a few options to correct this. Undo the oversite, break the footings and redo it with 150mm cavity instead of 110mm above. Undo the oversite, build another layer of blocks in the inner skin and allow space to create a 150mm cavity. Keep the footings as is and improve the insulation thickness to create a fully-filled cavity. (This saves me time) 100mm×1200mm×2400mm PIR is the cheapest option. Also, one board would cover the entire height of the wall giving the best possible performance. But, I don't know if the bricklayers could manage it with 11kg heavy boards. (calculated down to a U-Value of 0.166 W/m²-K) 100mm×1200mm×450mm PIR is light (2kg) and easy to manoeuvre. However, this does not come with a tongue and groove edge. We are living in a Sheltered Area on the Exposure Zone Map (given below)—therefore, this might be fine and I can use something like Stormdry for extra protection from rain penetration. Celotex Thermclass 90mm×1900mm×450mm is probably the PIR that was created for this purpose. It has a tongue and groove edge for easy installation and protection from rain penetration. However, this is about 1.7kg heavy and twice the price of the above-mentioned (calculated down to a U-Value of just 0.18 W/m²-K) I am waiting to discuss these options with the builder and choose the best option out of these three. Meanwhile, I appreciate it if anyone has a better idea or opinions on these options. I'll also update the thread accordingly as we proceed for the use of anyone who finds this thread in future.
-
Yes. This is an extension of a semi-detached property. The extension is being built over a public sewer (with a diversion). It costed me £15,500 already for the foundation concrete, MOT oversite, and the sewer pipes diversion. To fill the oversite fully with MOT and complete the work, the groundwork contractor is waiting until the wall is built up to the damp by the main builder. The main struggle is to get them on-site to continue work and to get any updates on what's going on. They are nice people—but don't keep me informed about the work schedules. So whenever I check, one party is waiting until the other party completes something. This is why I try to involve.
-
Thank you very much. I wish my builder was as clear as you on this. He is the person who asked me to order 2.9N blocks and then 3.6N blocks later. Surely, I am overthinking. But that's mainly because he himself told me that he has to work a lot in order to understand how to match the levels. Then I asked him if that meant that the groundwork contractor (his friend) did a poor job; then he panicked and started to say that this was not a problem. So, I thought I needed opinions from a wider audience.
-
The builder will have to cut the blocks to lay along the entire length of concrete B, won't it? If the builder just lays the blocks normally along Concrete B and cuts the block in the Concrete A side to match the levels, that shouldn't be a problem, right? I am not sure about the block manufacturer's instructions about the structural integrity of horizontally cut blocks. We are about to use 3.6N concrete blocks for the footings.
-
Don't tell that to anyone though. The council or some authority will come up with a plan to send you a bill somehow and get some business for their friends in the industry. 😅 Even though they can't find a legal point, they will fearmonger you first and see if you would fall into the trap. Once you finish going through all the stress and come up with a proper legal argument to question them further, they will say "Sorry, it wasn't absolutely necessary, we only advised you for the good of your own family" or something.
-
First contact your water & sewerage company and try to obtain maps of the public sewers in the area of your property. If they have it, then you can simply provide that to your builder. If the water company doesn't have maps or up-to-date records with them about public sewers in your area, you can open the inspection tank (manhole) in your property and see which side is upstream (direction from where water/soil flows into the manhole). Then talk to your neighbour on the upstream side, and pour a bucket of water in their inspection chamber (manhole) and see if that water flows through the manhole of your property. If the water you poured flows to the manhole of your property, then it is a public sewer. This means you need the approval of the water & sewerage company to make any diversions. Example: You will have to lodge an application for the approval process and make initial payments. As far as I know, since 2020, the water companies must comply with Design and Construction Guidance for foul and surface water sewers https://www.water.org.uk/wp-content/uploads/2021/07/SSG-App-C-Des-Con-Guide.pdf Therefore, they will just offload the entire pain of checking these standards, preparing all the technical documentation and buying the "Adoptable" products that comply with BS/Kitemark specifications while they also charge you for just issuing the approval. In our case, neither our architect/engineer nor the builder was very familiar with these (the only thing that the builder could do was curse the water company people saying that they were only interested in the money). Therefore, I did all these technical documents myself. The water company however will send you a list of these documents: Longitudinal sections Manhole schedule Site layout Manhole construction details Pipe bedding details Lintel details Your land title etc CCTV survey of the drains Once they are satisfied with this, they will give the green light to start work. Then you have to pay another amount for on-site inspection. Then your builder can work with the on-site inspector of the water company and finish the work. Please try to prepare these in advance if possible. Otherwise, it will cost you a lot of time depending on the water company in your area. In our case, they asked us to put Clay pipes for the new sewer line also as there had been cases where plastic pipes had blown when the pressure washer was used by them (we used Hepworth super sleeve). Also, when buying Plastic inspection chamber products, they will ask you to buy the products marked as "Adoptable".
-
Hi everyone, The below diagram depicts the trench-fill foundation of our house extension. Our builder introduced this groundwork contractor who did the trench-fill foundation and the oversite. The levels of the two segments that I have marked as 'Concrete A' and 'Concrete B' are very different. Concrete A is about 113mm taller than the Concrete B segment. Is this normal in the industry? or is that a poor job? Our builder who introduced them to us said that he could match the levels when doing the brickwork of the footings up to the damp. But it felt like he was also concerned (when thinking of how to lay the lintel), but did not tell me that because they are friends who work together on similar projects. The funny part is that this contractor who did this was laughing at one of our neighbours on a previous day saying whoever did their driveway had done a bad job and that driveway isn't properly levelled.
-
HDPE Adoptable and Non-adoptable inspection chamber products
Chathura replied to Chathura's topic in Waste & Sewerage
Yes, the builder cannot do anything against what they say and they have an Inspector visiting on-site to check and verify what the builder does. It's the property of the Water Company afterwards and if they say OK, I can't force the builder to install a different product either. I am just curious to know what is the difference between these 2 product categories when it comes to their qualities (construction, dimension or durability). I personally prefer to install the best possible stuff so that I have full peace of mind. -
We are doing a public sewer diversion in my garden by installing two new HDPE inspection chambers by removing the existing concrete/brick manhole. The water company expects us to install an "Adoptable" inspection chamber product. However, I saw that the builder has brought Polypipe UG440 which is categorised as a non-adaptable inspection chamber. In theory, if it is from the Polypipe brand, the inspection chambers should be SFA440 type. Since this job is already priced, I understand that the builder would keep the cost of material as minimal as possible. However, the inspector from the water company will probably ask them to change it to SFA440 or a similar product instead that's listed as "adoptable". Other than the fact of how many properties it would serve, is there any real difference in the dimensions or construction quality between Adoptable and Non-adoptable inspection chambers?