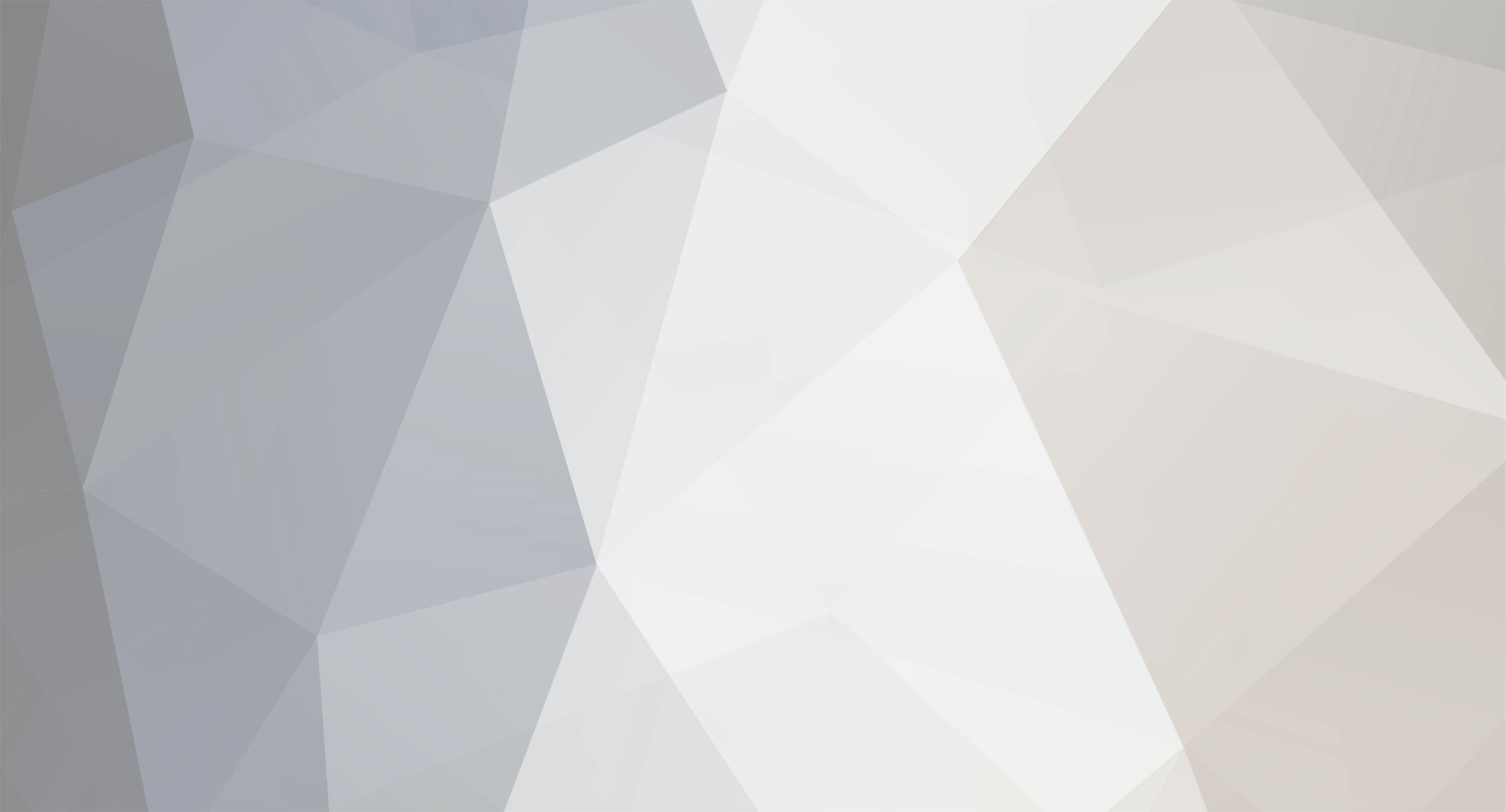
peekay
Members-
Posts
55 -
Joined
-
Last visited
Everything posted by peekay
-
We used this company for our Juliet Balustrade. https://www.ironoctopus.co.uk/ Was very impressed with the price and service. They did basic style galvanised steel one, bespoke to our dimensions and fixing method, and powder coated it RAL matched to our window frames. From memory is was only about £150 delivered.
-
Using an existing ASHP hot water supply to heat a pool
peekay replied to peekay's topic in Air Source Heat Pumps (ASHP)
I've got lots of PIR board offcuts from the build, so might try and fix it together in to a pool sized panel to create a 'lid' for the pool to use in addition to the thin tarpaulin type one. Will keep it out of the water though, as I'm not sure what effect the pool chemicals will have on the PIR board. Thanks. Still no thoughts on whether using my domestic ASHP hot water supply to do the initial pool fill is a good idea or not though. The pool and small ASHP pool heater have now arrived, so will be starting the fill over the weekend. -
Using an existing ASHP hot water supply to heat a pool
peekay replied to peekay's topic in Air Source Heat Pumps (ASHP)
Thanks, I've already ordered various pool chemicals. -
Hi all. We have an 12kW air source heat pump with a 400l tank for our domestic hot water. Temperature set to 55°C. We have just bought a 3.5m diameter, by 1m deep above ground swimming pool that we will put up for the kids to play in over the next few weeks once the warmer weather returns. This will likely stay up until autumn. We are looking at buying a small either 3.5kW or 5kW pool heat pump to warm keep the water warm to around 25-28deg (example: https://www.tradeinn.com/swiminn/en/poolex-nano-action-a5r-2020-5kw-2.5-m--h-inverter-heat-pump/139816348 ) My question: Rather than filling the pool with the cold water supply, and having the small pool heater work to bring the water up to temperature over a few weeks, would there be any benefit in filling the pool with water from our hot water tank 400l at a time until the pool is at the required temperature and then letting the small pool heater take over? I've read that I should expect it to cost about £10 a week to maintain the pool temperature, does anyone in the South East have any thoughts on whether this is a realistic budget? And is there any benefit in trying to insulate the pool in addition to the standard thin polythene pool cover? We have some old foam garage floor tiles that we were planning on putting under the pool for protection/insulation but would welcome any other tips about setting up or running a similar pool. Thanks
-
For our almost complete knock down and rebuild, our BCO said that we would be fine with lower sockets. We chose to put them in at the higher position. At some point we may appreciate not needing to get on our knees to plug things in. I've also not once looked at them and thought that they look high, or considered the plugs to be at an inconvenient height on walls. My general view on most things is that Building Regs are there for a good reason, and should be a guide rather than something to rely and get around.
-
German kitchen brands - Nobilia, Bauformat or Leicht?
peekay replied to Indy's topic in Kitchen Units & Worktops
For a large hand built using good quality birch ply (mix of oak veneered and Fenix veneer), good quality hinges, feet and drawer runners, worktops a mix of Fenix NTM and Valchromat, we paid about £8.5k in materials (cabinet maker built the materials orders with his supplier, who then invoiced me directly for VAT savings), and about £7k in labour for the time in his workshop to build the units, deliver and fit. I sorted sink, tap and appliances myself, but they came to about £6.5k I am doing some of the finishing work to save cost, such as sanding and oiling the cabinets, putting in back splashes. My electrician and plumber did their own bits. Total cost of about £22-25k. The cost for the equivalent from wren was about £15-20k, the Germans were about £35-45k -
German kitchen brands - Nobilia, Bauformat or Leicht?
peekay replied to Indy's topic in Kitchen Units & Worktops
We are only a few miles away from you and used a cabinet maker based in Brighton. Happy to share details if interested. Have you looked at Schmidt kitchens? They have a branch near you in Dorking. -
German kitchen brands - Nobilia, Bauformat or Leicht?
peekay replied to Indy's topic in Kitchen Units & Worktops
If you want handle less, with solid doors, have you thought about getting a local cabinet maker who specialises in kitchens to help? Most decent kitchens use high quality hardware such as Blum or Haeffle for the drawers, hinges etc, so a good cabinet maker should be able to use the same bits and hit the same quality as a German manufacturer for a lesser price whilst being bespoke to your layout/design. There are loads of really interesting materials that you can use, ply, valchromat, Fenix NTM, and an almost endless list of different veneers that you can have applied to ply such Formica, various wood veneer, Fenix etc. Not sure where you are in the country, but take a look at the sort of thing this company do, there will be similar companies nationwide https://www.instagram.com/woodworksbrighton/ -
Removing house from Council Tax list
peekay replied to srowe's topic in General Self Build & DIY Discussion
Yes, or at the point when it is added back on by the Valuation Office if you get it removed from the Register to avoid paying Council Tax during the work. -
Removing house from Council Tax list
peekay replied to srowe's topic in General Self Build & DIY Discussion
Have you considered that if you do remove it from the register, then it might be re rated at a higher council tax rate once completed? We chose to keep paying council tax for the 18 months of our large renovation/build, as looking at similar size properties in a similar location we could have expected to go up by two council tax bands when it is re rated and added back on the the register by the Valuation Office. Our break even point for paying 18 months of unnecessary council tax is 6 years of living in the house of paying the lower rate tax band. We expect the house will be re-rated to the higher tax band when we sell it. -
Do I Need Even more Insulation? Decision needed within next 24hrs
peekay replied to peekay's topic in Heat Insulation
Thanks Will have a read about the BC Condo Crisis. I've just checked with the builders, and the breather membrane definitely overlaps the external masonry wall on the ground floor. Their plan was to fix a concrete board to the external studwork, and then fix the EPS/EWI on top of this. Going right up to the soffit and sealing at the top. I'll discuss your proposal with them, thanks for the detailed knowledgeable responses. -
Do I Need Even more Insulation? Decision needed within next 24hrs
peekay replied to peekay's topic in Heat Insulation
If the top of the EWI is under the soffit (regardless of whether there is an attempt to close the cavity behind it or not), where could water come from? Are you thinking of just condensation? Thanks -
Do I Need Even more Insulation? Decision needed within next 24hrs
peekay replied to peekay's topic in Heat Insulation
Here are some photos of the gables taken at various stages over the last few months. I'm not around until tomorrow morning to take new photos of specific details -
Do I Need Even more Insulation? Decision needed within next 24hrs
peekay replied to peekay's topic in Heat Insulation
@Iceverge (and others)thanks for the replies. I'll upload some photos and annotate your sketch over the next couple of hours The membrane that can be seen from my photo is fixed underneath the studwork that can also be seen in the photo. Unless there are any tears that I haven't seen, whist it has been exposed any rain water hitting it has not entered the cavity below. More info to follow.... -
Do I Need Even more Insulation? Decision needed within next 24hrs
peekay replied to peekay's topic in Heat Insulation
Here is a photo of the gable. You can see the external line of studwork. VCL laid over 22mm OSB set behind this. Behind that is the 150mm PIR set within the internal stud wall, and faced with 50mm insulated plaster board. The cheeks of the dormers are tile hung. You can just make one out in the photo. The external insulation has already begun being fitted to the ground floor and can be seen in the photo. The plan was for a silicone render over all of this. -
Do I Need Even more Insulation? Decision needed within next 24hrs
peekay replied to peekay's topic in Heat Insulation
Haha. Good spot. It should have read 7.3N blocks! There is no detail on the drawings to say whether the cavity should be ventilated or not. I had similar thoughts, that if the cavity was open at the top under the roof, then the external EPS is not adding any value, therefore I have asked the builders to make sure that there is a good seal at the top. Maybe I should not have asked them to do this. -
Hello. We are nearly finished with a renovation (that is an almost new build). Large dormer bungalow shaped building. Ground floor 7.3kn blocks with Isover filled cavity and 90mm EPS covered in render. First floor gable walls and low stub walls below the pitch of skeiling starts, working outward: 50mm insulated plaster board, 150mm PIR board set within studwork, OSB, membrane, 100mm cavity, then external wall studwork on to which 90mm EPS will be fixed and rendered. We had a late design change from tile hanging the gables to render, hence bringing the gables slightly further out to allow a continuous render line. This has created the additional cavity at first floor level in the gables and stub walls. These will have the EPS board fitted by the builder on Monday. I have the weekend free. It would be about £250 in materials for me to stick some Isover 100mm Spacesaver within this extra cavity/within the secondary studwork line. Money is tight at this stage of the build, but it would be a lot more expensive to add more insulation at a later date. Is this overkill? Our SAP calcs don't require it, but is more always better
-
4 guys x 3-4 days to erect. Similar to remove. Equipment hire, disposables, vehicles, fuel, insurances, inspections. How much do you think it should cost?
-
When I looked at these a couple of years ago, I understood that they are in effect two small dishwashers rather than a single split dishwasher. I thought that felt like a lot of doubling both the risk and consequences of it breaking. I'm toying with the idea of having two full sized dishwashers in our kitchen. We have a space either side of the sink that would suit it, just struggling to justify the expense at the moment, so we might just save the space for the second.
-
We have designed one of the Liebherr ones in to our kitchen as a drinks fridge (in addition to a standard tall larder fridge). Having stayed at a friend's house where they had one filled with cans and bottles it seemed much more practical than sliding cans around a shelf on a normal fridge. They are about £950 though, so we'll have a blanking panel over the space that it will go in for a while.
-
Thanks. Unusual, but I like it. I've also recently seen someone mount a dishwasher at a higher level so that you don't need to bend down to load/unload it.
-
In many years of visiting houses and looking at them on Rightmove, the only time I've ever seen this is in a home that had been adapted for a family with some mobility issues. Even then the hob was on a height adjustable mechanism for those family members that didn't need it lowered. Do you have a photo?
-
@Originaltwist is that a copper worktop? Mind me asking who supplied it, as we've had a couple of quotes and it may be someone we've missed. Happy with it? We expect it to tarnish, mark and dent, but quite like the idea of it on our island gaining some character in what will be an otherwise quite modern ply kitchen.
-
I started this topic back in February, but as there has been a bit of recent activity on the thread I thought I'd give a quick update. We have found a local company that specialise in direct mount glazing to oak frames. They surface mount and then cover the edges with oak trims as described by someone earlier in the thread. I've in the last week finished sanding the internal faces of the frame and the glazing company have prepared the frame with various bits of DPC, and adding fillets/notches where required to sit the glass on. Rather annoyingly the glazing can't be finished until the front door is fitted, which will be in November, so we will have the upper levels glazed in the next few weeks, and the door level sections covered with Ply for a couple of months. We chose triple glazed glass, with a solar film, as the front of the house gets sun all afternoon and we wanted to avoid it becoming a greenhouse in the summer. None of this has been cheap, and if we were to do the house again, we might choose something more simple, but hopefully once it is all finished we will be happy with the choice.
-
Not really, but a few discrete steps on a non visible bit of the roof might mean I don't need to get scaffold up at some point in the future. I've scoured UK eBay and Amazon and don't seem to be able to find them. The only other places are EU sellers that don't explicitly say that they sell to the UK (I haven't emailed to check yet). Another solution might be to fit a bracket between the roof tiles near the top in a similar way to solar panel mounts that would allow me to hook a ladder over it.