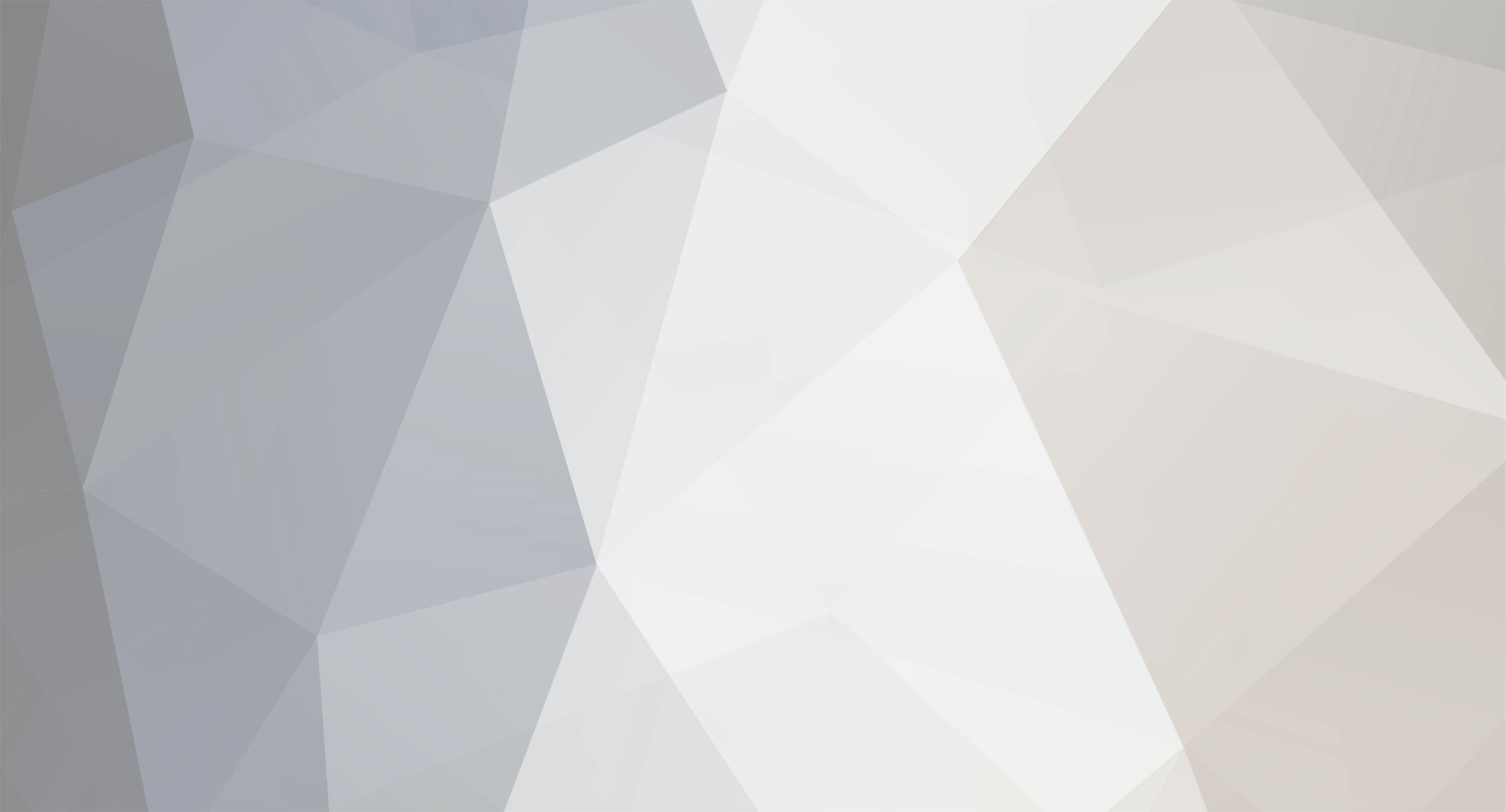
alfaTom
Members-
Posts
38 -
Joined
-
Last visited
Everything posted by alfaTom
-
As saveasteading said - you'll have to ask BC. We can't inform you of that as councils will want to see at different stages BC are really friendly and helpful round here so may as well just ask them.
-
I'm not that mad 😁 when we moved in it was an old 7kW thing. New one is a fancier 10kW thing with a wee touchscreen, this was the finished article. Mrs had a requirement at least one room in the house wasn't a horrid old 70s maroon bathroom... Yes - that sits as part of the inlet control group block - one feed to UVC and one to soft cold manifold. I do need to add in drain cock and NRVs in still that I didn't mention.
-
Thanks all, some good points and looks like I've simplified compared to previous plans. I think 15mm runs are likely to be fine, even for the furthest distances. All the information on this site is a blessing and a curse as I wouldn't have known about half this stuff if I hadn't been reading up 😁 Thought the electric shower would get people asking. When we first started the work it involved taking the old oil boiler out so we had no hot water. Electric shower went in so we could still shower, and it's not worth the effort of removing now given how often it'll be in use going forward.
-
I wouldn't like to guess - I'm not an SE. If you do go digging out then it's always best to do it as quick (and safe) as possible to reinstate the floor. I would have thought 500-600mm would be ok for a short term bit of work. Soon as you're at depth in goes the hardcore so you star to build it back up. But then I'd also say that might not be worth the effort going deeper - heat loss via the ground is less than the roof or walls etc so I'd probably rather put the money into those.
-
Our foundations in the old part of the house were about 650mm from finished floor level. I remember the builder looking at them and saying you couldn't even build a conservatory on them nowadays let alone a house 😁 If you need to find out the depth of your foundations you could dig a borehole near the external wall for that room - you'll find the foundation jutting out if you dig right down against the brickwork. Then just dig down on the edge of the foundation until you find soil under it and that'll give you an idea on depth. We've had to cantilever pile the old section of house to underpin and the new foundations are ringbeams on piles now so the foundations have been beefed up to a degree which gave me some confidence we wouldn't seriously impact the foundations.
-
I made a previous post where I got way too far into the weeds on satellite manifolds. To try and clear things up and provide a bit more clarity (as well as help anyone else in a similar situation) I thought I'd post a new thread with the current plans for plumbing in our property. Earlier this year I relaid our water supply and put in a 32mm feed. It's probably OTT, but the cost difference between 32mm and 25mm was so close I decided to go for the larger bore. The house has had all old plumbing ripped out; it used to be on a copper branched system and was gravity fed. I'm going to replace this with a manifold system to each wet room, and the DHW will now be via ASHP & UVC rather than oil boiler and VC. The water feed rises in the plant room where the UVC will be sited (with ASHP on the other side of the wall to UVC) to try keep things together otherwise I'd have a few runs crisscrossing the plant room. Water feed to UVC/manifolds: Tee with 15mm feed to outdoor tap with separate stopcock Main 32mm stopcock with reducer to 28mm Tee with 15mm feed to downstairs toilet and sink (This is because they are the other side of the wall to the feed so easy to supply) 28mm continues to control group (3.5/6) Cold water from control group is then split into hard water and softened Hard water heads to manifold Other feed to water softener (yet to confirm brand; don't really care about single/dual cyl or mech/elec function, more about not losing that pressure.) Softened water will then be sent to each bathroom in 15mm Manifold supplies and their estimated distances: Cold (Hard) water manifold Name Pipe diameter Pipe distance Utility Sink 15mm 8m Kitchen Sink 15mm 3m Cold (Softened) water manifold Name Pipe diameter Pipe distance Downstairs shower 15mm 2m Kitchen Dishwasher 15mm 3m Utility Washing Machine 15mm 10m Family Bathroom (Bath/Shower, toilet, sink) 15mm 8m Guest Ensuite (Shower, toilet, sink) 15mm 9m Master Ensuite (Bath/Shower, toilet, sink x2) 15mm 12m Hot (Softened) water manifold Name Pipe diameter Pipe distance Downstairs shower 15mm 2m Kitchen Sink 15mm 3m Utility Sink 15mm 8m Family Bathroom (Bath/Shower) 15mm 8m Family Bathroom (Sink) 10mm 8m Guest Ensuite (Sink) 10mm 9m Master Ensuite (Bath/Shower) 15mm 12m Master Ensuite (Sink x2) 10mm 12m (Note: No Guest Ensuite hot for shower as it is electric) For the above I am mainly concerned on pipe distance for the hot feeds, with the master ensuite being the furthest away at about 12m of pipe. I've split the sinks into a separate 10mm feed to try get hot water there quicker for handwashing etc, but otherwise I think the rest is ok in 15mm. I've ditched any thoughts on HRC and decided to keep it simple. All pipework will be run in Hep2o where possible. I could reduce the manifold size further by grouping the utility sink & washing machine, and the kitchen sink and dishwasher feed into shared 15mm runs but it should be easy enough to run a second bit of pipe if needed. Most joists are new posijoists so easy to run the pipes, just a bit interesting to clip to. Have I made any obvious mistakes? There will be isolation valves in various parts to help with maintenance so haven't listed them (i.e. control groups, softener). Only other thing I can think of currently is if manifolds should be fed from both ends or not to help when more than one run is active. Thanks all!
-
Another 'Cool Energy' heatpumps thread
alfaTom replied to HughF's topic in Air Source Heat Pumps (ASHP)
CE are working from my sizing - heatpunk shows roughly 8kW heat loss for the property. Couldn't get any heatgeeks or other engineers to attend to review and they all quoted £14k+ to fit ASHP & UVC. -
Another 'Cool Energy' heatpumps thread
alfaTom replied to HughF's topic in Air Source Heat Pumps (ASHP)
Thanks for the update @HughF. I'm currently in the process of arranging delivery of an ASHP & UVC from CoolEnergy via their MCS grant service. All the other installers wanted an extra £6k on top of the BUS, whereas CoolEnergy can supply the units and do the commissioning for the grant effectively "free" as long as I can arrange the install. I'm looking at the CE-IVT10-EVI which is billed as 4.89kW - 10.47kW @A-3/35. There is a newer model, the CE-ET10 but the capacity on this was slightly smaller at 3.89kW - 7.46kW @A-3/35). It's not on their website yet as far as I can tell. I've attached the spec sheet incase it helps anyone else. Once I've got hold of the kit I'll report back on ease of install & findings. CE-ET10 (QR).pdf -
Another month and I am back. Water supply has been connected up by Anglian Water and I have a nice shiny 32mm supply pipe. Left the required inspection pits and details accessible for them as per instructions but they were happy to connect up and head off - so glad I dug those pits back out for them! Looks like I have about 3.5bar pressure off the outside tap. If my maths is right the 45metres of MDPE should be capable of supplying up to 92l/m which should be fine for everything I want to do. I've tried to contact a few local plumbers to discuss plans - basically pay for their time to just go through the plumbing strategy and get them to quote for UVC/HP install, unfortunately not many seem interested. As mentioned on this forum before by others, it seems like buildhubbers are still more familiar with PEX manifolds than most plumbers. If anybody knows of someone reliable in the South Lincolnshire area it'd be appreciated! I have been reading up on some other threads on here including a recent one by @Sunil237 (thank you!) I think I can finally answer the question I stated at the start of this thread: Satellite manifolds are indeed a crazy idea for my use case. I'll be running a central manifold in the plant room that has a dedicated feed to each bathroom and tee off from that. I'll be redoing my diagrams soon so there are some iterations of the progress. Cold feeds to each room will be in 22mm, hot feeds will be 15mm. I thought about running hot feeds in 22mm with an HRC setup but I think I might just be trying to solve a problem that doesn't exist - surely it'd be simpler to run a 10mm alongside the 15mm if I wanted a faster hot delivery to a basin 10metres away; that'd be 320ml of water drawoff based on my GCSE maths... Thanks all for your help (and patience) so far!
-
Sorry - I meant I had opted for that in my designs. It's not in place yet, so my designs are still tbc. It was going to be 22mm from plant room to manifold in bathroom, with 10mm HRC on PIR. Once I get actual pressure/flow rates I'll then know what I actually need (and what is acceptable for the Mrs) and if I was just horribly overcomplicating everything like @JohnMo said to fix an issue that didn't exist.
-
So since starting this thread back in November I've only just really looked at the plumbing again since our grant has been approved for ASHP/UVC. Reading back on everything I can see there are really only two things I care about: Near-instant hot water when opening taps High-flow of water On my quest for high flow, I opted for 22mm pipe, and then, to compensate for cold slugs and meet the hot water needs, I went for an HRC. It's possible I'm overcomplicating things here and might need to do some tests before I make a decision. Our old 15mm copper pipe is now gone, and I have a 32mm MDPE line in its place waiting to be connected. (Terrific job to do last weekend given the cold weather by the way) I realised I have no idea what my pressure or flow rate will be in the house. I'm so used to cheap, rubbish combi boilers or the aging gravity-fed system that was present beforehand that I might be trying to fix a non-existent problem. So, the next steps are to get the pressure tested when the new pipe is connected, and then I can do a flow test off the garden tap to give me somewhere to start. Soon as I know those details I should be able to use the pipe diameter and distance to work out time to deliver for hot water and plan from there. Thanks all for your help so far, will update once I find out the pressure & flow and replan my piping!
-
Some good replies here - thanks everyone! Sounds like a satellite/remote/sub manifold will work for my situation, just need to KISS. A classic buildhub problem being left with too much time. This sounds similar in principle to what I'd be doing though I think. Two manifolds to "branch" in the further rooms and everything else off one local one. My main concern had been trying to keep everything radial. I think 22mm to feed remote manifolds with the HRC on the manifold via PIR or timer so the larger volume of hot water in the 22mm pipe gets circulated to mitigate that issue. I already have PIRs in place to activate the LED "pee" lights so you don't get blinded at night time so that could work...
-
Our build is coming along nicely and I'm getting to the stage where I lie awake for hours thinking about pipes. I've read plenty of topics on here about radial manifolds to reduce amount of water that needs drawing off for hot supply, plus also hot return circuits. I kinda want both, purely because I want the water to be hot quickly and I don't want to put in one solution and find it's not enough later. My problem is I don't think I could get an HRC on each radial leg without going totally overboard, so I'm thinking about satellite manifolds instead. I can put them in fairly easy-access locations in bathrooms so joints/leaks are less of a concern, plus I can run the HRC off the end of the satellite manifold back to the UVC. Is a satellite setup with HRC a wise idea? I can't see why having one manifold fed by a 22mm supply vs a few manifolds off a 22mm supply would be any different but I am not a plumber, just a hep20 enthusiast😂 A UVC will supply DHW, and the mains is being replaced from 15mm copper to 32mm MDPE, which means I don't know the mains pressure yet. I do know the HPPE was replaced in recent history so I am hoping the communication pipe is at least 25mm. (Keeping 32mm as cost difference is tiny and would rather not dig it up again later if water pressure drops in the area over time...) Picture for attention: I'm aware I'm missing lots of parts but as a "map" of what we're after hopefully it helps. The run to the family bath section will probably be 7-8 metres, but a big steel to support the opening stops me running all the individual pipes through and I'm looking for a "less is more" approach. The run to the master ensuite may be closer to 12-14 metres so would benefit from an HRC I think. Kitchen and the W/C is about 2 metres from UVC, and the utility about 4 metres. Layout of house (X is hot water point downstairs, triangle is hot water point upstairs) Thoughts?
-
1950's reno with a history of subsidence - the last 12 months
alfaTom replied to alfaTom's topic in Foundations
Unfortunately I don't have any photos but you could visibly see the difference in soil; much more clay-like at the front of the house and it went sandy towards the back. I also forgot to mention that the underpinning on the side of the house is also where the water main went, so I had to excavate that by hand in a few areas and then bring it up out the ground to get it out the way of the piling and beams. It's rubbish 15mm copper, unfortunately (?) not lead so will have to be replaced at my cost rather than the water supplier. Pipe is currently 15mm JG stuff running on outside wall of the house, should probably deal with that before proper winter... Just waiting on a response if I'm allowed a 32mm connection to the meter or not. Other than that plenty of random bottles, and a brick road under the old driveway which had to be cleared by hand otherwise the piles couldn't get through it. They say budget about £1k per pile & the ringbeam to the next pile. Gives you a rough idea on the cost without me having to type it out (Not sure I'm ready to admit that to myself yet😂 ). We then also had the additional depth charge to add on and additional charges for labour the unexpected complications around non-shrinking concrete and the different foundation heights. -
Improving dormer insulation - moving roof timbers?
alfaTom replied to Dave Lee's topic in Lofts, Dormers & Loft Conversions
Welcome. Can't see your photo - can you upload again? Any changing of roof timbers I'd ask that question to an SE and let them calculate the load. -
As some of you may have seen from my introduction post (shameless plug here), we bought a house in the summer of 2023 knowing it had subsidence. We decided it wasn't that bad. It was down as cash buyers only. Surely we know better than the lenders. Read on to find out if we were right... A summary We weren't looking to move house. We did the usual search on rightmove when bored. This house came up; the interior was old, it had subsidence but it came with a great plot of land and we could see it being our forever home. It has remedial work for subsidence done back in 2012, the walls had helifix bars installed and the offending trees were removed. We even had a full structural report written up from a proper MIStructE geezer, and he said the house was alright if a little wonky and the garage was more likely to fall over. What did the report say? Floors are a bit wonky, few cracks here and there. Walls are a bit off but yer roof timbers are alright. Nothing we didn't already know really, but nice to get it from a professional. No bowing in the walls at all so whatever happened was a nice even movement. The professional said some movement could be attributed to the trees at the rear of the property or maybe some damaged drains. (The worst affected area was literally right next to the guttering downpipe😱) What did you do next? I made a post on Buildhub, and contacted a resin injection company to see if we could do some localised repairs. The resin company wanted to inject an expanding resin around the front of the property and also down the sides. This came out at more than we had budgeted for remedial foundation work, and since we were planning to do some structural work (i.e. extension) they said the second we dug near the injected areas it would invalidate any warranty which would have turned it into one big gamble. As part of the resin injection investigation we commissioned some soil samples and drain surveys to understand the state of the ground and also see if we were right in our assumption the drains had failed. Below is a summary from the drain survey. A green X on a run indicates no defects. A yellow X on a run means a minor defect, and a red X means urgent defect. As you can see, there are no green or yellow, only red. 😂 Clearly the old terracotta pipes were knackered. Around the same time as this and thanks to some of the helpful advice on this forum I started a period of monitoring the house. Structural engineers say once a quarter is pretty good for measuring any movement on a house to capture the seasons; I did it every day. Us buildhubbers do like to go overboard... Bought the proper stainless steel measuring discs and a good set of digital calipers. I input all the data every evening into an excel sheet to make it easier to spot trends. I also made sure to do this at a similar time each day to try keep temperatures as consistent as possible. Variations between days were fine; I was looking more to see if we had a trend of cracks widening. I did this for about 5 months - not long enough to get a load of data, but I stopped in winter when the SE told me we'll have to pile the extension which meant my whole theory of monitoring to avoid underpinning was shot. As we have quite a high water table and a lot of clay they reckoned piling out be the most suitable rather than needing excessively deep trench or strip foundations. And because we'd be piling the extension it meant we'd have a rock-solid new part of the house and the old part move at a different pace; leaving us with a real risk of differential movement. Whilst doing the above we also replaced the drains around the house; installing two new soakaways to the front and rear of the property (appropriately sized for our new roof area too. When digging out the old drains this is what we found (no wonder we had some soil washout around the foundations) We decided at this point that we may as well go ahead with the SE's suggestion and pile the underpinning too. Yes, this cost a lot more than we had planned but if I'm honest I'm pretty happy now knowing that the house is fully supported. What was piling like? SE's came back and said pile everything in sight. You can see below the piles for the new extension plus the cantilever underpinning to the front and side of the property. So that's what we did. However trying to find a piling company who would work from someone else's plans AND do their own excavating was a nightmare. We had one company say they wouldn't excavate the ringbeams and would only pile, but also wouldn't tell us what level they wanted the ground at. They then agreed to excavate, and about a month later when someone else visited the site they changed their mind again and said they'd only do the piling. They were swiftly told where to go and we had to go back to RFQ stage to try find another contractor. As it turns out this was good fortune as the company we ended up using was brilliant. They did all the works end to end and also supplied an engineer to mark out the beams and the block profiles so it was ready to go for our builders. They even cleared the oversite down to the required level for the air gap under the block & beam flooring. Piling starts: Very grateful at this point for the large carriageway drive - made it much easier for getting the kit off the lorries. Was rather strange to see so much gear for one house; I definitely wish they'd let me have a go with it. We actually went through two rigs; one had the winch fail but we had a new rig onsite the following day to continue. The weight on them is about 750KG and is dropped from a pre-determined height. For us it was about 1.5 metres. On each drop of the weight they measure how many millimetres the pile slips and using calculations from the SE they can work out when the ground has enough bite to hold the pile. We thought we'd really feel this and we were also concerned for our neighbours, but it turns out aside from a little bit of vibration there wasn't actually that much disruption and we got used to it after a few days. They were on site for about 2-3 weeks (2-3 piles a day depending on the soil conditions) and we had no complaints. Once the weight went below a certain depth the shockwaves from the impact just sailed right under the neighbour's houses. Our nearest neighbours who were about 30 metres away felt very little, but we did have some neighbours about 200 metres away who said they could feel it; but thankfully no damage to their property. The contractors estimated about 6 metres for the pile depth for when we'd get the right bite, based on nearby BGS surveys and boreholes. Things were looking pretty good when we found a solid crust at about 3 metres and we thought it looked like we were in for a saving on the job! In typical fashion though what would have been the last drop forced the pile through the crust and it dropped about 13 millimetres. Once that happened they had to keep going and we ended up at 8 metres for the first pile. Because we found this solid layer at 3 metres but knew underneath was weak we HAD to go through it on every other pile. It got real solid in places but because they knew it wasn't solid underneath it couldn't be used for a fix. The other 35 ended up at between 8-10 metres and we found some very different ground depending on which side of the house they were on. When you got some good depth on the piles you could get a good echo out of them when shouting down though. Was really weird to just see it going down and down into the earth though. Once all the piles were in the excavation team were back to do the ringbeams. Some lovely Lincolnshire clay was waiting for them along with plenty of water. We had pumps running overnight to keep it clear as one trench just kept filling up. As a bonus in the above picture you can see the absolutely top-notch definitely not too thin or too sandy foundation that the original house was sat on. To add to that, the foundation in the house also wasn't level. This one really confused us and the excavation squad. At one point it was 5 bricks between DPC and foundation; at the other it was 8 bricks. You can see in the above where we had to step the beams down to get it to fit; which required some custom Z bars to bind the ringbeam together. You'll also spot the gap this left in the high points where we then had to get a more specialist non-shrinking concrete to meet the foundation. Another nice surprise and request to open the wallet. We still have no idea why they did this; either they decided after digging a certain depth for original foundations that they didn't want to did so deep (or didn't have to), but when you're doing a full set of foundations at once why wouldn't it be level?! Anyway, we persevered (or they did) and at the end we had a nice base to start our extension on: In the end we were in for 35 piles at about 8-10 metres, with 600mm ringbeam all round complete with hefty 16mm rebar sat in it but BCO have signed it off as good and we were on our way. The drone also makes for some interesting photos... footprint of the house is just a bit larger than it was before! Probably missed a few things here and there but hopefully provides a bit of insight into the joys of piling, subsidence, underpinning and just general mess. Absolutely loved spending £££££ for it to be covered in mud and never seen again; should have just filled it with £20 notes, definitely not being sarcastic. 🙄 tl;dr Whatever you are quoted by your contractors, double it. 😂
-
Thought might be worth adding to this since we are renovating a 1950s house and digging out the floors to add UFH... Our buildup is: 150mm MOT sand blinding DPM 170mm PIR Plastic sheet 75mm reinforced screed with UFH at 150mm Total dig out was around 425mm. You need to be careful you don't undermine the foundations and also fill it back in as soon as reasonably possible. If you're digging out the floors it's worth thinking about any cabling or drains you may need to put in - we've put a 40mm waste pipe for cabling to the kitchen island and also had to fit the shower drain run prior to the floor buildup.
-
Might be a bit late to the party with this one, (and the drawing was a tad confusing to decipher) but what makes you think it is the joists that need strengthening? You say you've not had the carpet or floorboards up yet so are the locations an educated guess? If the measurements are accurate then ironically I think notches were in the zone and new holes aren't. Holes would also be too close together if your diagram is right. On a more positive note if you have squeaky floorboards it could be just that. Old nails and rubbing T+G can cause this. There are probably lots of joists like this up and down the country that haven't failed yet... To help any more I think we need to know: What size are joists for depth and width Is it floorboard or chipboard Confirmed measurements Another possible route could be adding noggins for cross braces in that area to help spread the load and brace the joists against each other.
-
An introduction... Renovation + 1950s + subsidence = a challenge!
alfaTom replied to alfaTom's topic in Introduce Yourself
Thanks for the warm welcome back all, great to see so many people interested in our project. In that case I will try get something up this evening as a more substantial update. Sounds like fun! I am still going through the airtightness work at the moment so it's not comprehensive but some of the bits I found were: Sockets & Switches - one of the sockets had a nice 25mm hole through the brickwork and the ring main travelled through the cavity. That gave me quite the breeze! Cable is now chased into brickwork and the cavity gap is sealed. Skirting boards - A lot of our skirting boards were nailed into bits of timber offcuts that had been squeezed between bricks. This meant a lack of continuous pointing and again a nice easy way for the cavity air to get in the house. Old vents - We had vents all over the house, one had a lighting cable going through it up the wall to a wall-hung light. That got pulled out quick and sealed. Joists - All our 7x2 joists are in pockets on the inner leaf. Whilst they have mortar around them this is also a good place for a breeze as well. Windows - I know you said you've done some sealing here, but when we had our windows out and replaced we noticed not all of the window reveals had brick returns on them. We've put some cavity closers in now with insulation to hopefully reduce any thermal bridging. A can of insulation foam plus back of the hand works well round a lot of places, or if you're a bit of a nerd there are some USBC thermal cameras you can get for your phone. That was pretty useful at spotting cold spots and narrowing down where to look. Since I'm thinking about some service cavities on the older walls now I am starting to wonder if something like an AVCL + IWI could be an idea since the older walls are 50mm cavity with blown fibre and therefore a bit pants on the u-value (Heatpunk reckons 0.6 if it's to be trusted 🤮) Happy for you to move this, but I had planned this to be a more of a general update/build diary on the project as it goes. I'd planned to raise some topics in the other areas that could be a bit more specific and use this as a central page to link to the other areas. Since the first proper update would be on the demolition & foundations I'm happy to start a new post in the foundations section with our experience and move the discussion to there to keep it from being buried? -
An introduction... Renovation + 1950s + subsidence = a challenge!
alfaTom replied to alfaTom's topic in Introduce Yourself
I return... nearly 18 months later. The project is still ongoing, but I thought it was worth updating everyone on our experiences so far. I admit we've probably made a few mistakes but as a first attempt at a big project I'm pretty happy how we've dealt with issues and moved on; every day is a school day! If any of this helps anyone else then it's worth it even if I look a bit daft during it! So - onto the project. We started by demolishing the old extensions since the foundations for them wouldn't be up to supporting a floor above them, plus they were built inadequately for our needs (solid walls, weird floor buildups, even weirder roofs). There was plenty of advice on this site around the existing foundations and how to proceed with them which we really appreciated, but in the end we were led by the structural engineers and underpinned the property for peace of mind to avoid any differential movement. The extension foundations are piled down to about 8-9m and the existing property was cantilever underpinned using piles too. Overall we're pretty confident the house won't be going anywhere (we now have 36 piles!) We've then wrapped a fair chunk of the house in a new extension to better use the space, and put the poorer performing old external walls further into the property. Cavity is 200mm with 190mm PIR made up in two layers incl interlocking boards and tape, and the flooring is 240mm EPS insulation in the new areas, whilst we've just finished digging the old flooring out of the house which should be insulated to 170mm. I'd like more here but we're restricted by the depth of existing foundations which is a shame. The old electricity supply has gone from overhead to a nice new underground supply, complete with 3ph up to the DNO supply head so we're future-proofed (still only 1ph currently) and I'm waiting for a response to my request for a new water supply. Wet UFH is throughout, with the oil boiler gone and an ASHP to replace it (When I can get an installer on the BUS grant that won't rinse me). Spent a fair bit of time playing with Heatpunk and Jeremy's spreadsheet for heat loss predictions which is fun when half the property is 200mm cavity and the other is 50mm. I really wish here that we'd stepped the walls outwards and then EWI'd the older walls but I didn't think about this until it was too late - a good reminder to plan ahead here. I'm also scheming for 10kWp of PV to go on since we're having a new roof fitted. The savings in tiles & labour lets me man-maths my way into some GSE trays and panels 😁 My current focus is looking at the air tightness, not as much of an issue in the new section but the older part of the house is good fun, so I guess there will be updates on this part from time to time as I'd love to get MVHR fitted as well. Words can be boring sometimes, so the tl;dr is: should we have listened to you all knocked it all down and started from scratch? In hindsight, Yes 😂 Did we? No... (Be gentle 😳) time to learn from it and make the best of it! And the pictures: Steel reinforcement for ringbeams in place after piling at the back Starting the build to DPC Second lift and on the way to wall plate. Will maybe dump a few more before & after shots in the coming days or a specific focus on parts if anyone is interested. Poor house has been battered about a bit - for the greater good I hope! -
If you are a competent DIY'er then depending on your location you may be able to dispose of the asbestos roof sheets at your local household recycling centre. This should save you some cash from paying a specialist to do it, but you'll need to invest in quality PPE beforehand and obtain the sheet bags from your recycling centre. You could then use that extra cash on the roof - I'd go OSB and felt as you'd get a good roof from that but not sure what state the rest of the garage in - might be more effort than it's worth.
-
An introduction... Renovation + 1950s + subsidence = a challenge!
alfaTom replied to alfaTom's topic in Introduce Yourself
It's certainly a variety pack! Curious to see what I find elsewhere. I may try to cut the plasterboard below off so I can get almost a cross-section idea of the lintel. A shame the SE's seem to be taking their time coming back to me at the moment as that is holding us up currently. My understanding is that the wallpaper is newer, from 2012 when some work was done to the property. It doesn't seem to have a vinyl layer so it which reduces the chances as far as I am aware. There is plenty of asbestos elsewhere though; garage roof sheets, soil pipes, guttering etc as well as some tiles in the downstairs w/c. -
Help: Single wall brick extension, what to do?
alfaTom replied to CloGanga's topic in House Extensions & Conservatories
I have a single skin extension on the back of our house that holds the washroom, downstairs WC & boiler room. I have no idea the sort of foundations it sits on but I doubt they would be up to current regs. Luckily the external door & structural wall is still in place from the main building, so we will be knocking the single skin down and rebuilding. I doubt it'd add much to your cost to knock down and rebuild vs the extra labour costs in retrofitting fit wall ties etc. -
An introduction... Renovation + 1950s + subsidence = a challenge!
alfaTom replied to alfaTom's topic in Introduce Yourself
I have been a bit quiet recently - unfortunately, the weather at the weekend was terrible so no investigations outside were completed. I did however get the old cylinder lawnmower running again in the (relative) safety of the garage! I did finish the cut-out above the doorway though. After getting through a layer of plaster, roughfill AND plasterboard I found the lintel over the doorway. It looks like there is a metal lintel (can be seen below the timber and in the shadow) with the timber resting above it. I need to get more of it cut out to see how it sits but I didn't want to disturb it too much. Waiting on the SEs to respond to my queries at the moment around the soil vs drains, and I am waiting for the underpinning company to come back to me with answers about complications from partial underpinning and more info on guarantees. When I get more information I'll update this thread so the information is there for anyone in the future that may need it. -
Think about the fact you've taken a pond out and added sub-base in. If the fence stayed where it was when a pond was present then it should stay where it in once you have the sub-base in. You're not leaving it hollow so it'll have something against it. For sub-base I would use MOT1, Wacker plate it and sand blind. Might be a bit OTT but I think you'll need to compress it well into the old pond space to stop it sinking. As for ensuring it sits flush...you measure it and level it. Get the depth of your new patio slabs and subtract that from the build up, allowing for a cement mix underneath. I'd do full cement on the slabs, none of this 4 dots in the corner like some companies will do.