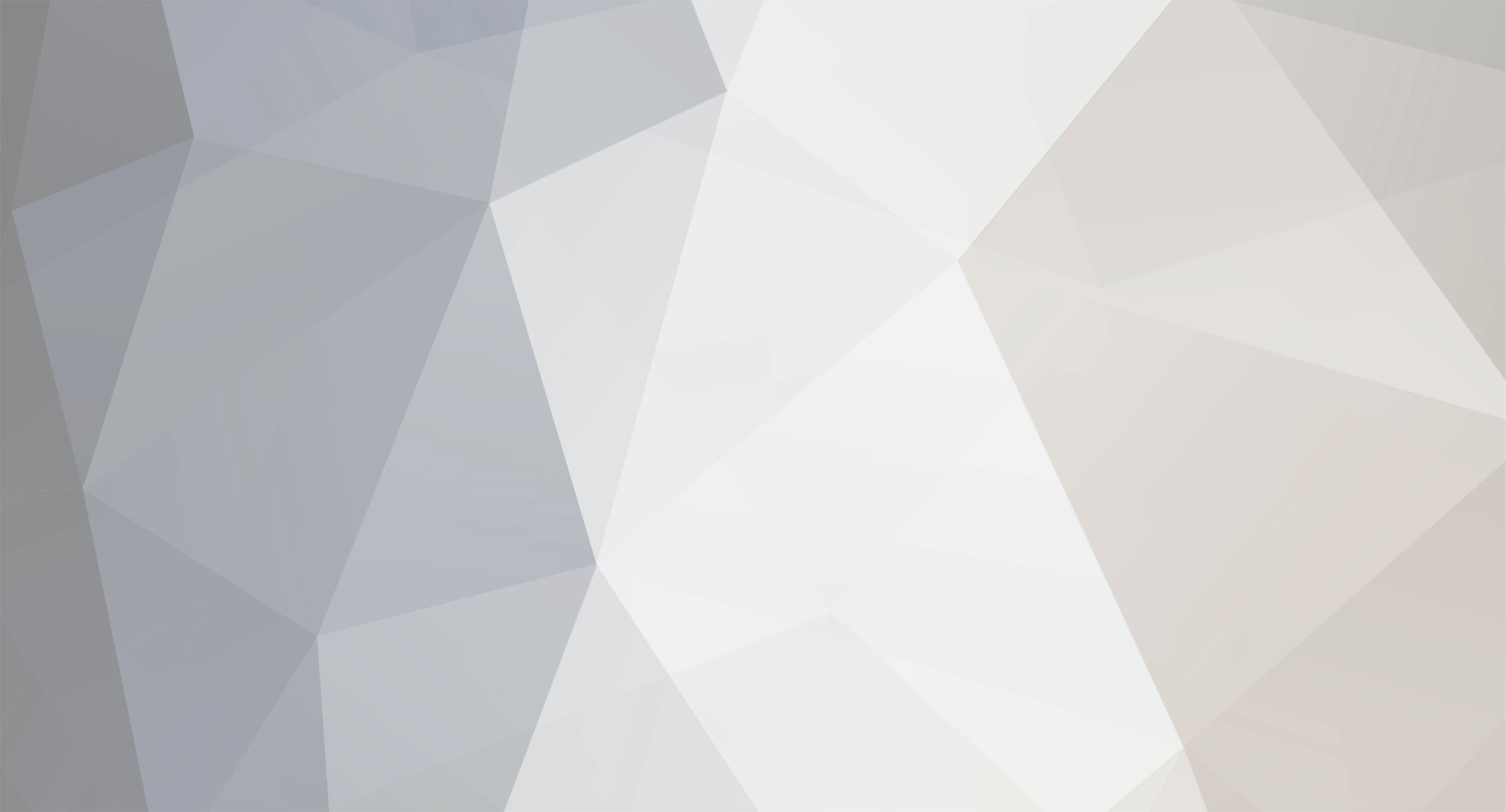
R2021
Members-
Posts
17 -
Joined
-
Last visited
Recent Profile Visitors
The recent visitors block is disabled and is not being shown to other users.
R2021's Achievements

Member (3/5)
3
Reputation
-
Siberian larch vs sweet chestnut cladding
R2021 replied to PeachyBeechy's topic in General Construction Issues
@RishardI've just bought 100m2 of Thermowood which I'm installing soon. Do you have any tips? It is T&G with shadow gap profile I read you butted up the boards tight against each other. Is that because there is no movement in Thermowood? I was a planning to leave a couple mm gap at the T&G and where two boards meet at a counter batten, but maybe I don't need to. Did you pre-drill the screw holes? I've heard Thermowood is brittle Did you use one or two screws side by side to secure each board to the counter batten? Did you put DPC between the board and the counter batten? Russwood's battening systems has this but I went to my local timber yard for the Thermowood and battens. -
Ledge Issue at Masonry-Timber Frame Junction
R2021 replied to R2021's topic in General Construction Issues
Thanks for all the advice so far. there are several similar comments so rather than reply to each, I will try to cover all points here... The house is on a sloping site with a flood risk, so the masonry ground floor is doing two jobs: 1) acting as a retaining wall tied into the raft foundation; 2) providing tanking for rain water flowing down the hill - it's filled with water proof concrete between the two leafs to 1350mm above ground level, i.e. a semi basement. So there's no way that wall is coming down now. The timber frame company were responsible for the detailed drawings for building regs, but they used a structural engineer to design the foundation and masonry ground floor to achieve a complete system for retaining walls and tanking. Unfortunately the two seemed not to collaborate during the design process. I was responsible for appointing a groundwork/building company to complete the foundation and ground floor, who done an excellent job following the structural engineers design to the letter. I've challenged the timber frame company, but their general attitude is that they weren't responsible for the ground floor design, which is rubbish as they are the company I paid for it, but what can I do. I don't want to destroy our relationship whilst their part of the build is in mid progress right now. The timber frame company are providing the windows but they don't provide battens, so that's my responsibility to fit. However they have dictated 100mm of battening and ordered the windows based on that. If I increase the batten depth now, they will fine me for changing the order and for the delays it will cost, which will also cause me to delay the renders and cost me more scaffold rental. The timber frame company are never going to absorb the cost. They've already charge me an extra £11k because I was one month over their deadline for completing the foundations and ground floor. The ledge is not going to look pretty, but it is only down one side and 2.2.m at the back of the house, so won't really be seen. @ProDave The DPC does stagger up the masonry wall to follow the slope. The timber frame insulation is already built into the frame (Ultima). It is supposed to be one of the best insulated frames on the market (before getting into SIP territory) at 0.13U. On the masonry ground floor, I need internal insulation because I can't further increase the perimeter with external insulation. So I can't increase the batten depth, or build up in blockwork from the outer leaf as @Mr Punter says because of the windows. There are a few suggestions for Aluminium trims which was where my mind was at, but I'm also the plinth brick as suggested by @Gone West looks an interesting option I will explore further -
Thank you @Iceverge that makes a lot of sense. From your comments I done a bit of Googling and found this video, which demonstrates exactly what your say. Interestingly after air testing the blocks, they apply a liquid membrane and test the improvement, but their final comment is that a render, as you suggested, is the best method.
-
My timber frame company outsourced the masonry ground floor design to a structural engineer and didn't notice an alignment issue until now. I've been left of fix the issue so grateful for this communities help. The timber frame aligns with the inner blockwork leaf as shown in the photo. The ground floor will be clad in slate slips adhered directly to the external blockwork leaf. The timber frame will have render board or timber cladding on 50mm counter battening creating a 100mm cavity as shown on the diagram below. The battening and render/wood cladding is yet to be installed but the diagram shows how it will align (or not) with the ground floor external leaf. I can’t increase the batten thickness because the window cills have been spec’ed and order for 100mm cavity by the timber frame company. The first challenge is how do I stop any water that gets behind the battens going into the blockwork cavity and channelling it out over the slate slips. A cavity or lintel tray has been suggested but I've not found any with the right dimensions. Grouting out the inner leaf mortar in the course above the outer leaf block and inserting lead or DPC has also been suggested. Thoughts? The second challenge, given the render board / wood cladding doesn’t sit flush or proud of the external block work leaf, is how do I get rain that runs down the cladding out and over the external leave & slate slips. A verge trim has been suggested and I believe that if I fitted a 140mm one between the horizontal counter batten and cladding it would reach over the slate slips. I've found aluminium ones online, which could work out expensive. My builders merchant recommended a fiberglass roofing fillet trim, which is cheaper, but flimsy, which might help with installation, but may not have a good lifespan. Any thought, alternative options or product recommendations would be very much welcomed.
-
Thanks @Icevergethat sounds straight forward then and good value for money. Grateful if you could explain the principles though (my experience in these things is limited and I'm trying to learn). With a high density block, I assumed the weakness from an air tightness perspective was at the mortar joints. Those being sand and cement, how does a sand and cement parge coat over the top improve the air tightness?
-
@Marv968I found the same - my local builders merchant not only said they didn't sell the Soudal product but they didn't believe me that such things as airtight paints existed. Like @eandgsays, I found there to be a few places online selling it for around £35 inc. VAT.
-
Thanks @Icevergethat's an alternative approach that I will consider. I will be doing this myself so a painted solution would be quicker (for me with my limited plastering skills). The sales team at Soudal confirmed that Soudatight LQ will fill gaps up to 5mm, provide air tightness, and can be rollered. It's a 3rd of the price of the BlowerProof and Passive Purple so that's my contender for a specific air tight paint option. Liquid DPM would still be the cheapest and easiest for me though so keen to know if that is a viable option.
-
My ground floor is a partial basement formed of high density block work with the cavity filled with waterproof concrete to mid height and liquid DPM below ground level. The upper half is an empty cavity. Insulation with be internal PIR. Upper floors are airtight timeframe. I want to ensure the upper half of the block work is as airtight as the rest of the build. Could this be achieved by painting the internal block work with liquid DPM or should I really be looking at a specialist product like BlowerProof, Soudatight LQ or Passive Purple?
-
Unfortunately there's nothing in the contract that specifies what they can charge. No it's not storage, it's labour, material and deliver price increases over the past 6 months. I see their point that their costs have gone up, but it's not helping my financial viability.
-
Actually not a storage fee - they will build the frame a week before delivery I'm told. It's increased cost of labour (factory and site), materials and delivery. They hold the price for 6 months but it has taken longer than that for my complex foundations and ground works to be completed.
-
That's what I had to do to get the levels right. And yes it was expensive with more muck away than I had originally been quoted.
-
Yes Pottons appointed structural engineer came up with the water proofing solution. which was to fill the masonry cavity with water proof concrete (although this means I need internal insulation so will lose some room space) and paint the outside of the walls with two coats of liquid DPM
-
I went for the Kingspan Ultima 13, which should give a U value of 0.14. The ground floor, being a masonry construction with internal PIR is looking to U value of 0.3 with 50mm PIR. The as designed SAP (by Potton) suggests 3 air changes per hour. I'm planning though to coat the ground floor masonry in liquid DPM and throw extra air tightness tape anywhere that might need it to acheive the best values I can. Glad to hear your happy with the Rationel Alu-clad windows.
-
A flood risk assessment was needed before the planning application could be submitted and it influenced the ground floor building reg side of things. but getting permission went through relatively smoothly.
-
I'd rather not give specifics, but it has five figures.