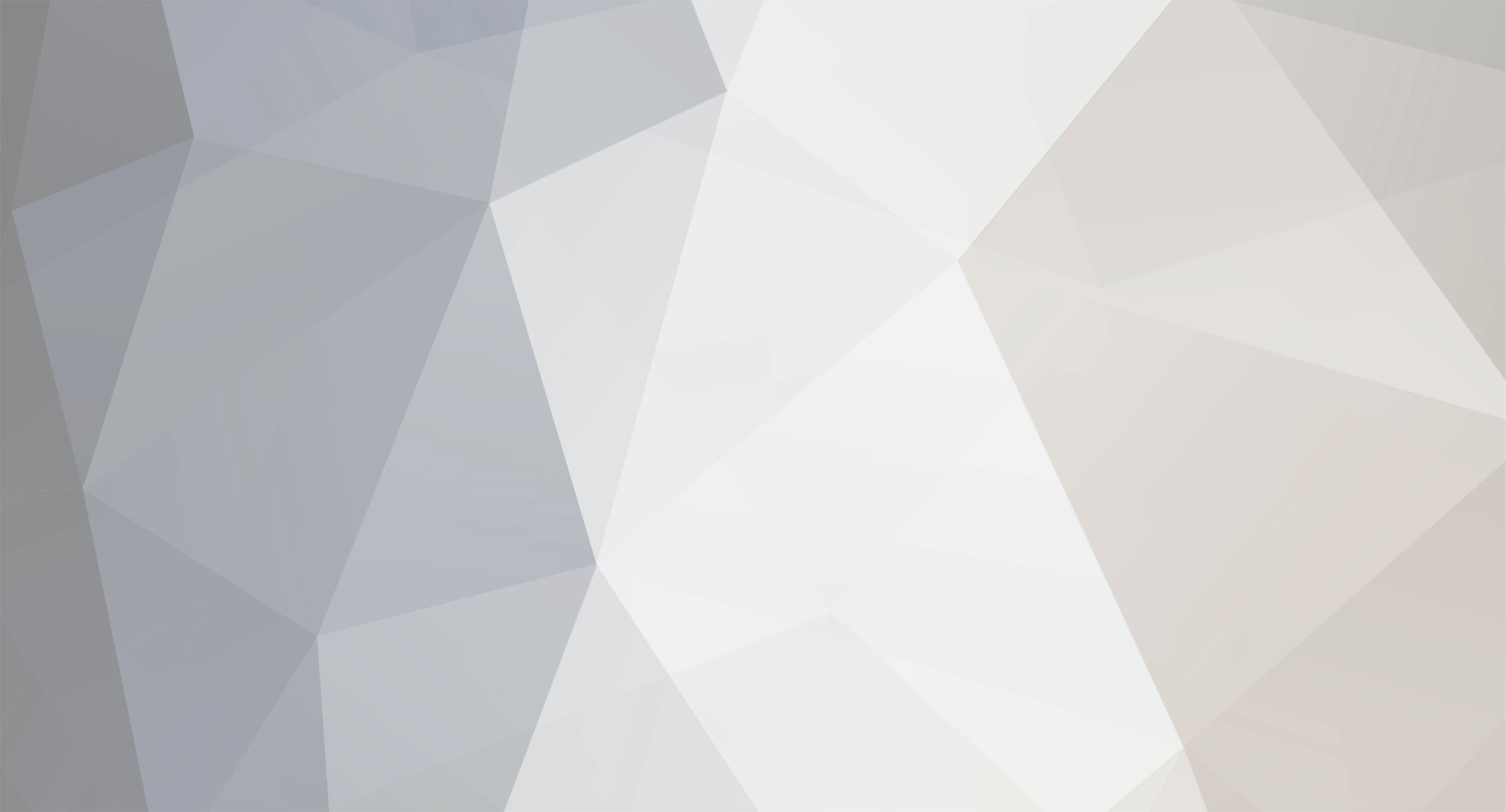
Duncan62
Members-
Posts
153 -
Joined
-
Last visited
Recent Profile Visitors
The recent visitors block is disabled and is not being shown to other users.
Duncan62's Achievements

Regular Member (4/5)
33
Reputation
-
Occasionally we got a clash of batten/cladding screws. Mostly we angled the cladding screw to get around the batten screw. Occasionally we had to remove the batten screw and move it 20mm one or other way.
- 63 replies
-
- cladding
- open joints
-
(and 1 more)
Tagged with:
-
Cladding battens, Pressure treated or not
Duncan62 replied to gavztheouch's topic in General Joinery
Don't recall snapping any. stripped a hex head or two when I wasn't paying attention/pressure on the impact driver. I and another guy installed all of ours, we're the careful types, not the bang it up types. -
Cladding battens, Pressure treated or not
Duncan62 replied to gavztheouch's topic in General Joinery
https://www.tcfixings.co.uk/product/a2-stainless-t25-part-thread-wood-screws-60mm-x-180mm/18642 -
Cladding battens, Pressure treated or not
Duncan62 replied to gavztheouch's topic in General Joinery
I went with SS screws for what it's worth. Same layup, 60mm external insulation, 25x50 counter batten. 50x50 batten. Once you start getting custom cut larch, the price must be similar? -
https://www.theheatpumpwarehouse.co.uk/shop/heat-pumps/air-source-heat-pumps/samsung-heat-pumps/samsung-ehs-gen-7-r290-heat-pump-5kw/ Will this Samsung Gen7 cool out of the box?
-
DIY Inline Carbon Filter
Duncan62 replied to Duncan62's topic in Mechanical Ventilation with Heat Recovery (MVHR)
Man that is cheap. Did you use one? Thanks you for the suggestion. Never used Ali. Any idea on pressure loss? Another reason for DIY is because carbon filters for "plant growing" will never be discontinued, how would you get replacement filters in this case? I guess you could buy another whole unit if it is discontinued, bit of a faff tho. -
DIY Inline Carbon Filter
Duncan62 posted a topic in Mechanical Ventilation with Heat Recovery (MVHR)
How's this idea for a DIY inline carbon filter? Will be placed on the supply side of the MVHR. The reason to DIY is to double the carbon bed size at a slightly reduced cost when compared to Blauberg Clean box 150. The Blauberg Clean box 150 has carbon filter: 220 x 400 x 45 = 4,000,000 cubic mm DIY Rhino Pro Carbon Filter: Pi 150 x 300 x 50 = 7,000,000 cubic mm Lifespan: Rhino pro states 2 years at 600m3/h. So at 150m3/h (my case) expecting an 8 year life span. Part List: 150 duct. £15 / 3m 150 coupler. £3 Rhino Pro Carbon Filter: 150x300. £100 Custom 150 F to 355 M Reducer. £45 355 Duct. £90/3m Standard 355 to 150 Reducer. £20 Totals About £270 Blauberg £400 -
MVHR Unit + Ducting Suppliers
Duncan62 replied to Duncan62's topic in Mechanical Ventilation with Heat Recovery (MVHR)
Thank you, supplier list: CVC systems BPC Anyone used: Paul heat recovery? Blauberg? 21 degrees? -
Heating / Construction type.
Duncan62 replied to Ryan 2023's topic in General Self Build & DIY Discussion
The cheapest option is to cut you heating demand. This is done by cutting your heat loss from the building. This is primarily done with lots of insulation (very cheap to do) and triple glazed windows (very reasonable options exist). Solar orientation, building form and air tightness also have significant effects of heat loss. Is it simply money/month or do you value human comfort too? If you then follow the rabbit hole to its conclusion, you might consider building a certified PassivHaus. -
Thank you. No not from my place, was an example i found of someone elses PH. We did exactly this, DPM on slab. Sole plate atop. Warranty instector was happy.
-
Open Faced Cladding - Batten SPEC?
Duncan62 replied to Duncan62's topic in General Construction Issues
Appreciate that. And I agree. Finding it in non fencing sizes is not easy however. Also about 4x the cost. Pragmatism won out. UC2 used. End grain sealer on cut ends. DPM paint on top of the horizontal surfaces. -
membrane/drip tray/fascia detail on cassette roof?
Duncan62 replied to junglejim's topic in Roofing, Tiling & Slating
Literally having this issue now! I think counter battens should end early. So the drip tray can sit on the roof deck with a slight kick to the eaves board. The membrane sits on top of the tray. The vent sits on top of the membrane to allow air into the cavity behind the tiles, exciting at the ridge vents (and take moisture away from the building) The tiles then sit on top of the vent strips. -
Open Faced Cladding - Batten SPEC?
Duncan62 replied to Duncan62's topic in General Construction Issues
@ToughButterCup @the_r_sole @Gary M @markocosic @Dave Jones @joe90 what did you guys use for the battens please? -
Help please! I have spec'd open face cladding - what USE CLASS specification should the batten and cross battens be? I am concerned I require UC3 treated wood (pressure treated to push preservative into the wood), and not UC2 which is easily available (green treated timber that is dipped, not pressure treated. i.e. roofing battens). Because open cladding means the battens will be subject to constant moisture - I think UC3 should be spec'd? Correct? Further info: https://www.jamesjones.co.uk/assets/uploads/files/treatment/tanalith-e-suppliers-guide.pdf Then we can get into actually finding this UC3 wood in sized like 25x50mm, 50x50mm or 50x100mm, I cant find it anywhere.