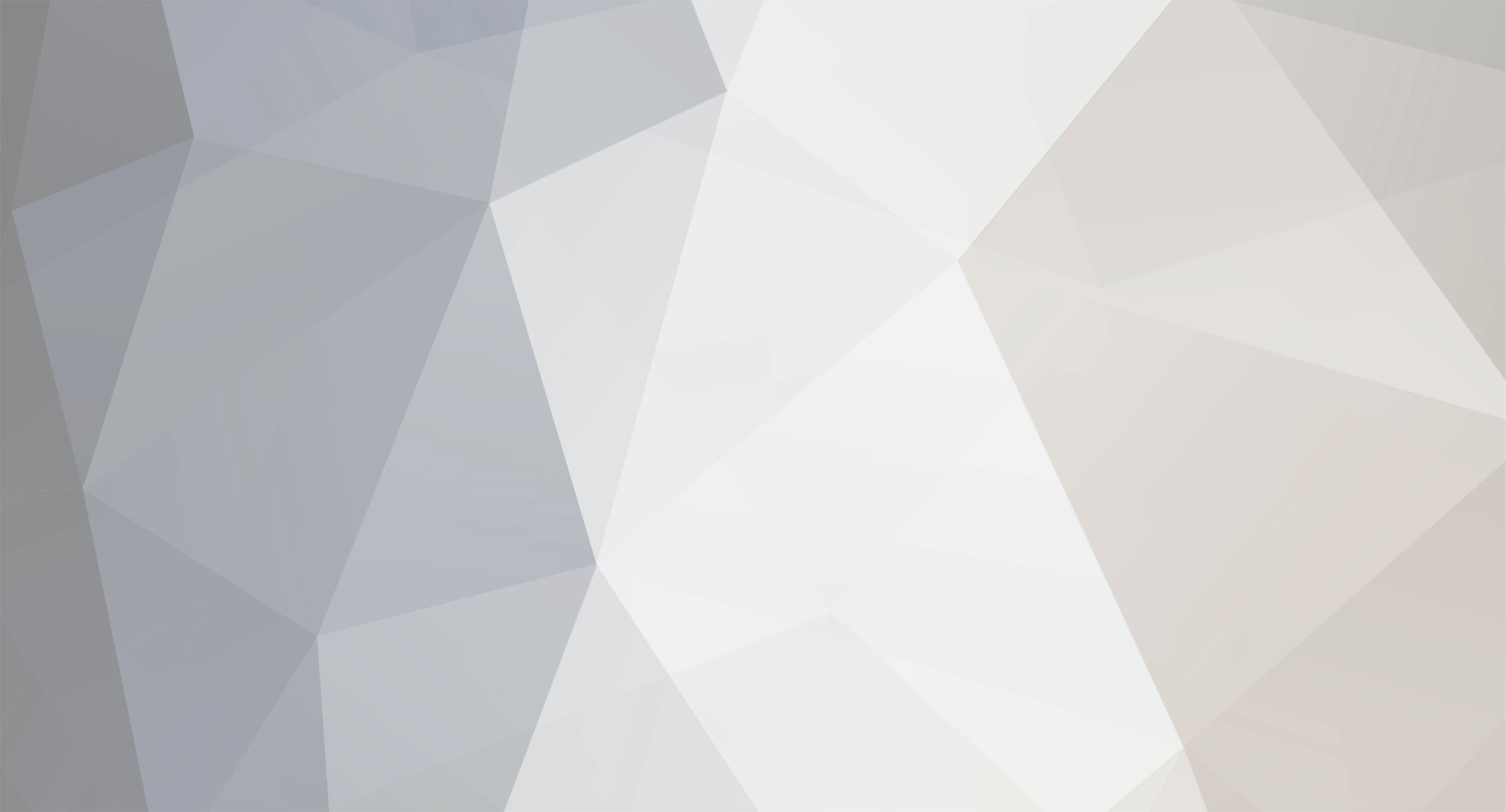
MarkW1979
Members-
Posts
55 -
Joined
-
Last visited
Recent Profile Visitors
The recent visitors block is disabled and is not being shown to other users.
MarkW1979's Achievements

Member (3/5)
3
Reputation
-
-
Aye, it was very windy. I'll try the hose, but like you say it looks like it's coming in from outside. Assuming the fix is render off, cut out some blocks and sort out whatever the issue with the dpm is? Thanks again
-
I dried out the spot with a hair dryer yesterday, although I'm left with a small dark area. No (or little rain) overnight and no patch today. I've run all the baths and showers and nothing. it's just odd because we had some dreadful weather prior to the patch appearing (I checked back on my pictures) and it just seemed to coincide with water being turned on last week (we also had poor weather though)...
-
I came out of construction mode about 2 months ago but I think i'll need to I'm leaning that way too; I'm assuming the dpm is quite hard to tear when the blocks go up. I think that's the way it is supposed to be... Thanks for your responses, will see what tomorrow brings.
-
Hi, Hoping someone might be able to help with an issue I came across today. A damp spot has recently appeared above my kitchen window. The house is timber frame construction with blockwork outer skin. It has been roughcasted (before christmas) and the walls were plastered last month. I have only noticed the patch today and. The water has only recently been turned on (there is plumbing above - a bath, but there don't seem to be any obvious leaks although I haven't run anything for a significant length of time). I can see from pictures last week that the area was dry. The dpm above the lintels and weep vents all seem to have been installed correctly... I'm a bit stumped.
-
Thanks guys, lightning fast response as usual! All the best
-
Hi all, and a happy to New Year when it comes. My plumber needs to know the sizes of radiators I am using and as usual I have left planning it to the last minute and thought interpreting the information I have from the heat pump installer would be straightforward (it may be that I am just overcomplicating things as usual!). The heat pump installer has provided the heat loss calcs for the rooms. I am only having rads in the bedrooms: 1,2 & 3. The radiators I am finding online seem to only need to be fairly small to match the wattage calcs as recorded below (at Delta 50) - I had expected them to be required to be much larger (i.e. oversized for a HP). Am I missing something? Should I be looking at achieving the stipulated wattages at Delta 30? Thanks in advance!
-
Thanks guys, but I will be using the renderboard - I was really trying to work out how the flashing works i.e. does it go against the renderboard or underneath it against the kit...
-
-
Too late for a lintel - the porch is already connected to the kit (which I'm guessing why it's done in the first place because it's easier for the kit builder...
-
Hi, I would very much appreciate some help with the following!: My timber kit porch has been designed with a render board panel above it (it is 1.75 storey timber frame with blockwork/render cladding - apart from the area above the porch). The detail in the plans is poor (and don't make sense to me) and I have had about 3 differing versions on how it gets done. It obviously has to get framed out out to 138mm + 12mm renderboard to bring out to the blockwork at 150mm (100mm block + 50mm cavity) but does anyone have experience of how this has been done regarding the roofwork? Does the flashing go to the renderboard when built out or back to the timberframe and renderboard goes over it? Plans say lead flashing wraggled in but can you wraggle into renderboard (I thought "wraggling" would be only possible in blockwork unless I have the wrong understanding of what wraggling means!). Thanks in advance, Mark
-
-
Hi George, Many thanks. The engineer has done the drawings but the brickie has come on site and basically said that what has indicated is a bit excessive and plans to rationalise from 11 to 9. The 9 proposed (in orange on the drawing) seems to make more sense to me but I am just trying to understand the rationale for the SEs drawing. Cheers, Mark
-
A quick question I hope someone could help me with re: movement joints in blockwork. Guidance suggests that in structures constructed of cement based materials (concrete blocks, artificial stone, concrete bricks, cement render and the like) then movement joints should be provided at 6m intervals and within 3m of corners, however re: the corners - does this mean within 3 metre in each axis from the corner, or just one per corner if that makes sense? (i.e. the difference between the 2 pictures - movement joint in blue): Many thanks!
-
Expansion joint locations
MarkW1979 replied to Barryscotland's topic in Bricklaying, Blockwork & Mortar
Hi Barry, Maybe we have the same Structural Engineer. I'm in a similar position - exactly the same wording on approved building warrant plans - how did you get on with your approach? Cheers, Mark