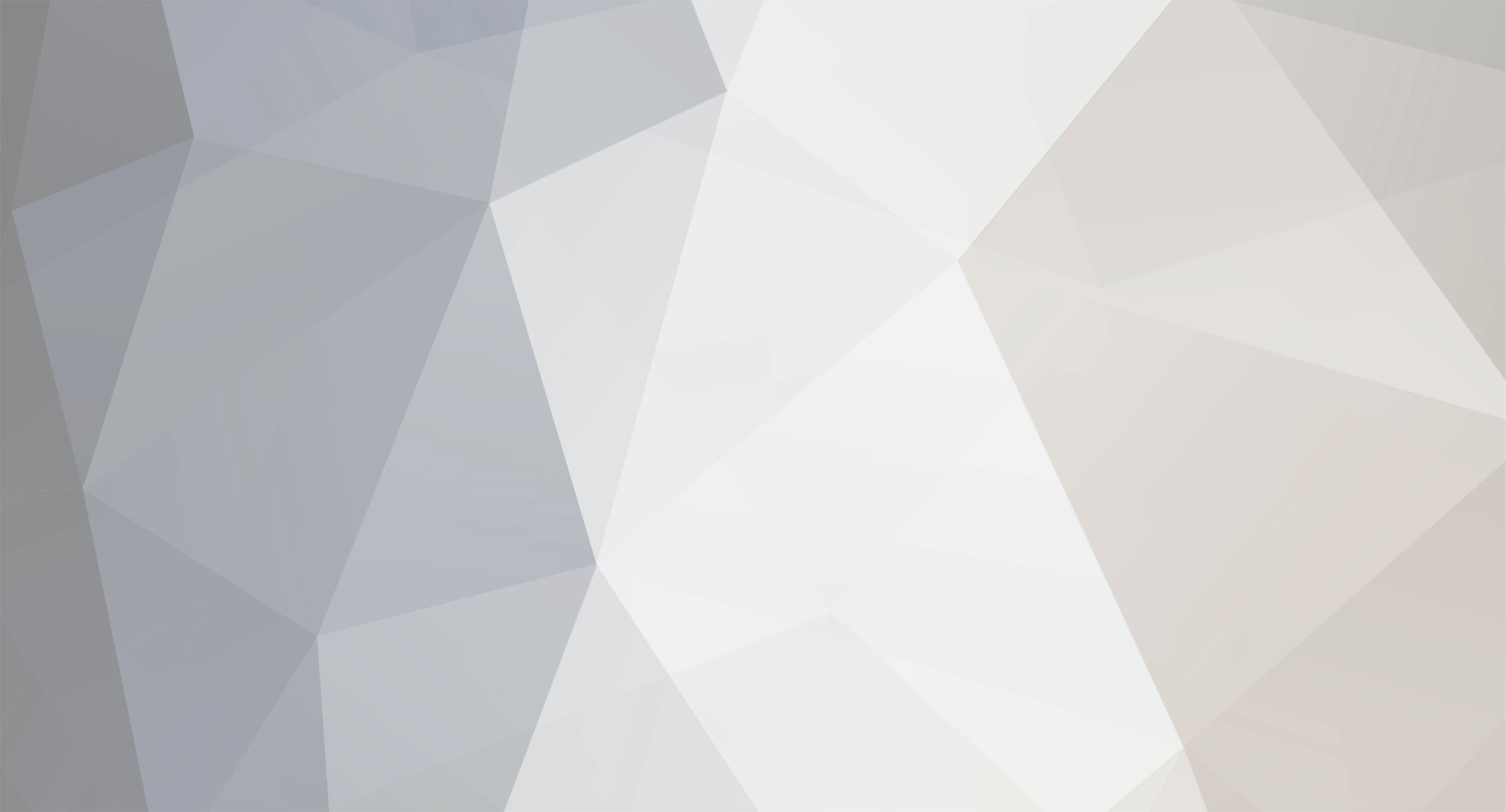
Nelliekins
Members-
Posts
157 -
Joined
-
Last visited
-
Days Won
3
Nelliekins last won the day on May 5 2019
Nelliekins had the most liked content!
Recent Profile Visitors
The recent visitors block is disabled and is not being shown to other users.
Nelliekins's Achievements

Regular Member (4/5)
79
Reputation
-
DIY hot water system needs replacing - Sunamp?
Nelliekins replied to Nelliekins's topic in Boilers & Hot Water Tanks
Filter replaced every year, but only because of a note on the calendar. No noticeable issues with flow or water quality from the boiling water. Tap itself gets cleaned maybe once a month, never noticed any scale on the end. -
DIY hot water system needs replacing - Sunamp?
Nelliekins replied to Nelliekins's topic in Boilers & Hot Water Tanks
Hah, we have a boiling water tap, no kettle! 😂 -
DIY hot water system needs replacing - Sunamp?
Nelliekins replied to Nelliekins's topic in Boilers & Hot Water Tanks
The statement from UU is that "the water supply to this area can vary in hardness from soft to slightly hard". That seems a total cop-out to me. But Worthington Lakes are literally 2 miles from our house (we are south of Chorley on the border with Greater Manchester) so there is every chance our village gets water from there. And the water there is definitely soft. I might just get it tested, though, to be on the safe side! -
DIY hot water system needs replacing - Sunamp?
Nelliekins replied to Nelliekins's topic in Boilers & Hot Water Tanks
That's the weird thing - our water is not that hard. I previously misread this information, and reported the Clarke value as PPM - it's actually 75ppm, which is still relatively low IIRC. Circulating pump is coming out this afternoon to be inspected / cleaned. -
DIY hot water system needs replacing - Sunamp?
Nelliekins replied to Nelliekins's topic in Boilers & Hot Water Tanks
Frankly at this point, the £3k outlay is becoming attractive. Showering in water that is less than 35C isn't pleasant to me. @PeterW and others - can I ask a few questions, to make sure i haven't misunderstood stuff along the way... 1. Should a 30kW system boiler be capable of replenishing the heat in the cylinder as fast as a single shower (@10 litres/min) can deplete it? 2. Should a 100kW PHE be able to heat the incoming cold mains to 50C at 10 litres/min, if it has sufficient supply of hot(ter) water to pass through it on the primary side? If the answers to both the above are YES, then 3. if we switch to using the Willis heaters for the UFH, could we reuse the indirect coil in the cylinder as a DHW preheat coil, to reduce the risk of cold showers happening again? (I am assuming that this mitigates the impact of reduced flow on the PHE primary because the uplift on the incoming mains is already reduced) -
DIY hot water system needs replacing - Sunamp?
Nelliekins replied to Nelliekins's topic in Boilers & Hot Water Tanks
That was the amount recommended (and indeed supplied) by the plumber who did the boiler side of the system, based on size of the cylinder, the header tank, and the pipework. But clearly not even close to enough... Even the instructions on the Sentinel X100 say 1%, and the system is somewhere around 200 litres. What are the odds that the level of scaling has completely killed the PHE? Am I better off replacing the whole lot, given I am disconnecting the UFH from it all anyway? -
DIY hot water system needs replacing - Sunamp?
Nelliekins replied to Nelliekins's topic in Boilers & Hot Water Tanks
Ok so there is some extensive scaling inside the pipework. Given there was 1 litre of inhibitor in the water, I am not entirely sure how or why it is this bad after a little over 2 years... Is it possible that the cylinder was too hot at some point and this is the result of kettling? This elbow was between the PHE and the cylinder, so I am expecting this throughout now... -
DIY hot water system needs replacing - Sunamp?
Nelliekins replied to Nelliekins's topic in Boilers & Hot Water Tanks
I haven't removed the PHE - that's next on my list. But it's the PHE itself dropping in temp very rapidly, which suggests restricted flow rate through on the primary side. The TMV appears to be operating as expected, because if I increase the temperature on it, I can get absurdly hot (>60C) water at a tap for a few seconds before everything goes cold again. -
DIY hot water system needs replacing - Sunamp?
Nelliekins replied to Nelliekins's topic in Boilers & Hot Water Tanks
Not hard water - "moderately soft" according to United Utilities (5.32ppm on last check for our area, which was apparently 1 week ago today). We aren't using a water softener. -
DIY hot water system needs replacing - Sunamp?
Nelliekins replied to Nelliekins's topic in Boilers & Hot Water Tanks
This is probably a silly question... If I am switching to using Willis heaters for the UFH side of things, is there any reason I can't try using the indirect coil for preheat of DHW? -
DIY hot water system needs replacing - Sunamp?
Nelliekins replied to Nelliekins's topic in Boilers & Hot Water Tanks
Yes, why do you ask? -
DIY hot water system needs replacing - Sunamp?
Nelliekins replied to Nelliekins's topic in Boilers & Hot Water Tanks
The stats are set at 50°C and 70°C. The immersion is set to 70°C and every time the solar diverter fires up to try and heat the cylinder, it tells me the cylinder is already hot. Yes, flow switch works as expected. Temps going in must be right, because the cylinder stats all say they are. Stats are operating correctly. The temp coming from the taps reaches design temp of 45°C within seconds (which means ~50°C at PHE as expected), but drops off rapidly (within 60s it is below 25°C). This is only slightly mitigated through reduction of HW flow rate. -
DIY hot water system needs replacing - Sunamp?
Nelliekins replied to Nelliekins's topic in Boilers & Hot Water Tanks
Here is a sketch of the hot water and heating system, please ignore the green link - that's how it was originally plumbed, but I have since remade as per the drawing. The immersion heater is in the top of the cylinder, though. DHW Design - draft 1.pdf -
DIY hot water system needs replacing - Sunamp?
Nelliekins replied to Nelliekins's topic in Boilers & Hot Water Tanks
I even bypassed the flow switch at first and set the pump to "always on" as an experiment (in case the PHE was getting cold too quickly). Pump seemed to run fine, but PHE still goes ice cold within a minute. Flow switch fires as soon as a hot tap opens. I will remove the pump and check that there is nothing reducing flow internally - I even found the handle for the gate valves the other day, so that shouldn't take long. Clearly, if the cylinder is hot enough (70°C), then: 1. The PHE isn't getting enough flow from the cylinder, or 2. The PHE isn't operating correctly, or 3. The blending valve isn't working as it should @PeterW the current cylinder is vented, with an 18 gallon header tank. Any reason to switch to a UVC? And last time I was on this forum, the Sunamp appeared to be almost the Holy Grail - what have I missed? Thanks! -
So... a couple of years ago, following advice from various sage individuals in these parts, I built my own "DIY thermal store" to provide hot water (and a heat buffer for the 250m2 of UFH). For the first year, it worked pretty well, but it's become less and less effective over the past year. Now, the hot water doesn't work at all. I have a 140 litre RM Aquastel cylinder, with dual stats (half way up, and at the bottom). It is heated by a 30kW Worcester Bosch system boiler (with the stats providing for a single long burn), and has a 2.8kW immersion heater powered by the solar diverter (which never fires - the cylinder is always hot when it tries). A single indirect coil in the cylinder provides heat for the UFH. We are perfectly happy with the heating side of things, but the heating requirement is so low that I am intending to use a couple of Willis heaters powered by our Solar diverter for the few days of the year it is required (heating hasn't been on once since middle of February, and was turned on less than 60 days in total last year). On the hot water side, I have what is normally the direct connection to the tank being pumped through a 100kW PHE, with the second side of the PHE being fed by mains cold. The water gets hot for maybe 45 seconds, and then goes (and stays) cold. SWMBO has had enough (and to be fair, I really don't blame her). I don't understand why it is so much worse than it was 2 years ago (when it worked perfectly well for 3-4 showers back to back without a hiccup), but I don't have the energy left to try and solve it. The cylinder is being kept at approx 70C, but the PHE temperature drops rapidly from the incoming cold mains and never recovers. So, as per the title, I am considering either (a) replacing our gas boiler and cylinder with a Sunamp, or (b) adopting a KISS approach and converting what we have into a "traditional" hot water cylinder (i.e. remove the PHE entirely, connect the boiler to the coil connection on the cylinder, and have the contents of the cylinder as the actual hot water that comes out of the taps). (a) seems a more appropriate long-term solution (since gas boilers are so 20th century now, and gas is probably going to skyrocket over the coming years). However, there is a large capital outlay on the Sunamp (£3-4k for the biggest models, plus installation etc). Plus, if we go the Sunamp route, there are a couple of questions that spring to mind: If we are thinking of getting a monobloc ASHP in due course, are we better off getting the correct Sunamp model (e.g. Sunamp Thermino 300 hp-SG) now? If we get the HP model, do we need to install the ASHP from day 1, or can the Sunamp HP models work with just electric heating as well? The KISS approach (b) would probably entail replacing the cylinder (since it has has primary circuit water in it for 2+ years, so inhibitor and whatever else inside it, and I don't know if I would trust just flushing it out a few times to make the water safe). But other to that, it's a bag of elbows and tee fittings and a bit of copper pipe, and I would be done... Help! 😢