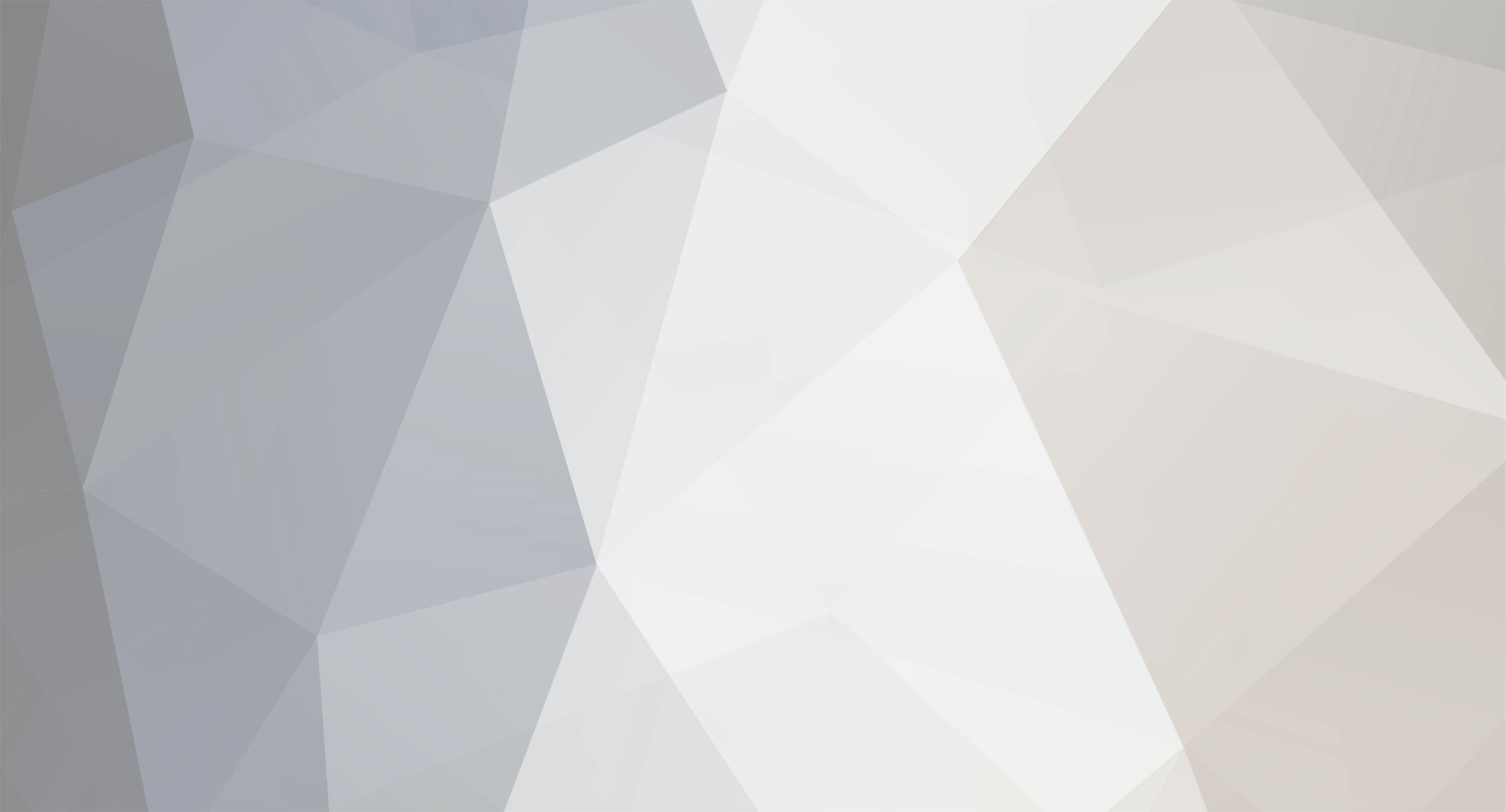
-
entries
0 -
comments
0 -
views
13806
About this blog
This blog http://eastkentpassivhaus.blogspot.co.uk/ will be copied here as it was to Ebuild, probably very slowly! It will hopefully be updated at the same time.
This blog http://eastkentpassivhaus.blogspot.co.uk/ will be copied here as it was to Ebuild, probably very slowly! It will hopefully be updated at the same time.