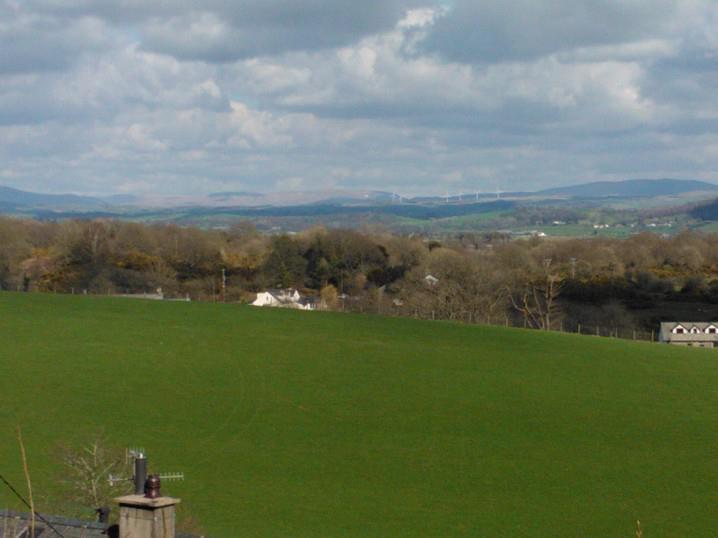
-
entries
11 -
comments
96 -
views
2183
About this blog
Having done a large renovation project and turned an old 1770s vintage wreek into a fantastic Home we decided that living in Cheshire was no longer for us, so we sold up and moved, to be closer to family in the Southern Lake District.
However the journey was far far from straightforward, we really had no idea what we were looking for, was it to be another renovation project or a self Build? Having viewed around fifty ‘oportunities’ ranging from dilapidated houses, to an old pub, to a closed garden centre, we gave up!! Then about six weeks after ‘giving up’ Debbie had to come clean, she’d not actually given up, but had been searching online and she thought she’d found what we were looking for. So we arranged to view a rather sad looking dormer bungalow on a very wet, cold and overcast March day. Once into the property we both realised this was the one! So we bought it and moved in.
Having lived in the property for a year it was clear that this wasn’t a renovation job!