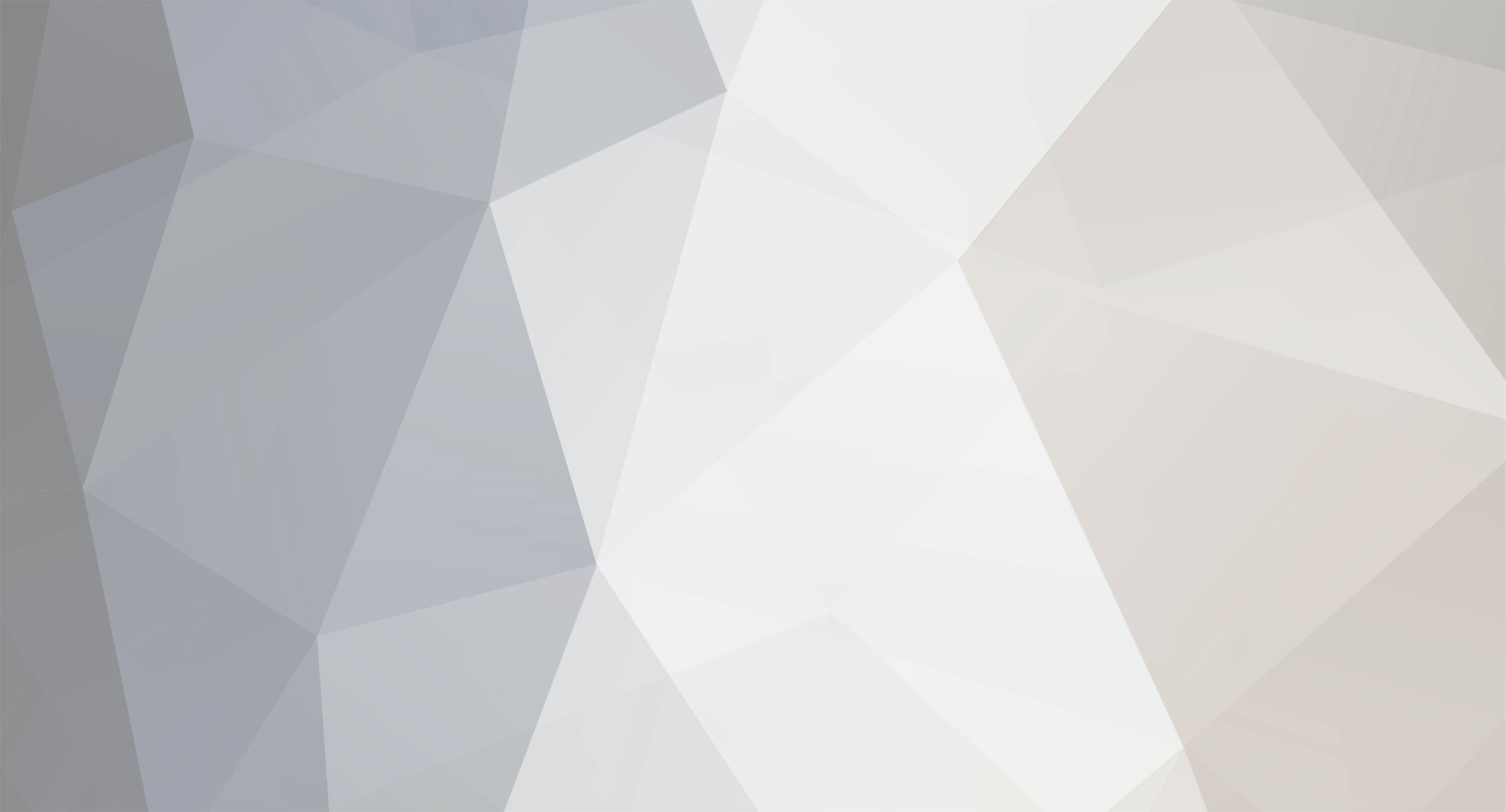
Haku
Members-
Posts
15 -
Joined
-
Last visited
Recent Profile Visitors
The recent visitors block is disabled and is not being shown to other users.
Haku's Achievements

Member (3/5)
1
Reputation
-
Am I correct to assume there should be a stop bead set 20mm down from the soffit and 5/15mm down from the underside of window cills for the render? I asked the builders to leave this gap in the blockwork and then fill with compriband, they've then just rendered over the top of the compriband. I assume I need to ask them to correct this and leave a gap for settlement. Do you just fill the gap with flexible mastic over the top of the compriband or leave it open? (On the clad areas they've left the gap at soffit & under cill level but I gave them a detailed instruction on how to install the cladding)
-
I think so. been speaking to some of the other suppliers and they aren't expecting nearly the same scale of movement. Also hoping by getting frames put together in the summer the timber wont still be soaked from sitting in the yard through a damp spring.
-
The first houses are for resale so will be a main contractor doing all the work I think. The last house is to keep so that will be a mix of me and trades on day rate as needed. I dont plan to rush the houses but at the same time the build schedule is only planned to be about 7-9 months. Sounds like this is too short and could lead to some issues.
-
Thanks. I just found the tech spec for this earlier today. Looks good and makes sense. I'm a bit concerned about cracks etc and a dodgy looking finish around windows as the properties are for resale - if I was living in them I'd be working slower, have more settling and drying out time and would be happy to patch up the decoration after a year. The thought of being called back once my builders have moved onto other projects is a bit of a concern.
-
Cygnum have computer controlled cutting machines that cut the insulation and then squeeze it in place when the next timber is fitted - its an automated factory production line. Flight timber are manually cutting and their uValue for the same build up is significantly worse. I've ended up erring towards the bigger higher tech factory produced frames for this reason. I would have preferred a small local firm but actually all the companies are within an hour of site.
-
First multisite development. I've renovated about 15 properties and completed a couple of B&B houses left by builders part way but no Timber frame experience. Having watched builders hand cut insulation before I have my doubts that they can better a machine cut fit? What do you mean by 'research suppliers a bit more - my short list have bad reps? Poor build quality?
-
In speaking with one frame supplier last week he said to expect up to 10mm settlement at the ground floor and more at first floor over the first two winter heating cycles. Do others have experience of how much compression you actually saw as the frame dried out and what the impact was inside the house. The conversation came up as I was worried about how to finish the exterior window cils prior to the brick skin being built. It looks like there are specialist flexible sealing solutions for around windows to manage this. Any other considerations or pitfalls to be aware of? Is it better to get the roof on and then leave the timber frame to dry out for a while before fit out and bricking up the outside to reduce risk of cracks etc?
-
0.17 or 0.19 at worst I think. I've got my cost comparison between quotes based on 0.17 from various suppliers. Does this sound reasonable? Kingspan advice was to use 0.21 but the cost to upgrade was relatively small so I thought I'd step up. I had quotes from Kingspan, Cygnum and Flight based on rigid factory fit insulation - Local frame companies quoted but only do the timber frame supply & erection and I'm not convinced insulation on fitted on site will achieve the same results.
-
Absolutely agree....but if you have to value ROI and are already building at a uValue above the regs requirement, installing ASHP & car charging points how much more should a developer do. None of these things add much value from a buyers perspective but from a responsible developer perspective I want to build sustainable homes because that is the right thing to do. MHVR seems to be a small incremental gain from an eco perspective and wont pay for itself over its lifetime so then it comes back to does it improve living conditions sufficiently to justify the time & cost of installation. So far it seems to be a bit like Marmite!
-
I'm on a country lane in a village so air quality is generally good with pollen the only real concern. 5K is quite a chunk of money isnt it! I have space to put the unit in the plant room or loft but right now I dont have PV panels and if I'm going to upgrade something that looks more obviously useful to run the ASHP....unless the MHVR is a necessity rather than luxury
-
I'd been looking at the system Kingspan can supply as part of the frame build/supply/installation package (Rega Heat ventillation). I'm struggling to find a builder with Timber Frame experience so hadn't planned on installing it (simplicity is best) until I realised one of the potential frame suppliers could do this. My concern is about the buildings overheating. I understand this isnt aircon but if the system alone can keep the house to a comfortable temp in summer I'd be tempted to add it.
-
That's a great question. These 4 houses are for commercial resale. I've retained the 5th plot for my house which will most likely include MHVR as the cost:benefit considerations aren't the same (I have hay fever so filters that require checking every 4-6 months in exchange for less pollen is totally acceptable to me personally). I don't believe Joe blogs has a clue what MHVR is when they are out house shopping so I'm just trying to work out if there is a noticeable benefit from those that have it. Saving £100 a year on heating isnt a selling point in my view if you have to call in an engineer to do annual maintenance. Its about 3-4k more expensive than having extractor fans and trickle vents so the question is does it really improve quality of living significantly and does it noticeably cool the house in summer when potentially I think the houses will be very warm.
-
I'm just planning 4 timber frame houses and am in two minds over MHVR. The houses have bifolds along one full wall of the kitchen/diner and also the long lounge wall and all beds have big windows so my instinct is the windows will be thrown open whenever it is warm. The houses will be well insulated though so I'm trying to think about whether they will overheat and does the MHVR add value. Looks like a fully designed & installed system is 5-6k which would pay for PV panels a couple of aircon units and a car charger instead. Has anyone recently built a TF house in the SE England and regrets not fitting MHVR? Has anyone recently built a TF house in the SE England and regrets fitting MHVR and wishes they'd put the money into something else? Any opinions gratefully received. I have no experience of living with MHVR and whilst it looks interesting on paper I'm struggling to find a financial justification or indication that it improves the iar quality in the house enough to justify.
-
Did you look at Ipswich Timber Frame? They dont do in factory insulation - just design & erect the frame. I had a quote from them based on recommendation from others locally. They dont meet my needs as I want a high u-value factory insulated frame but could be good for what you need.