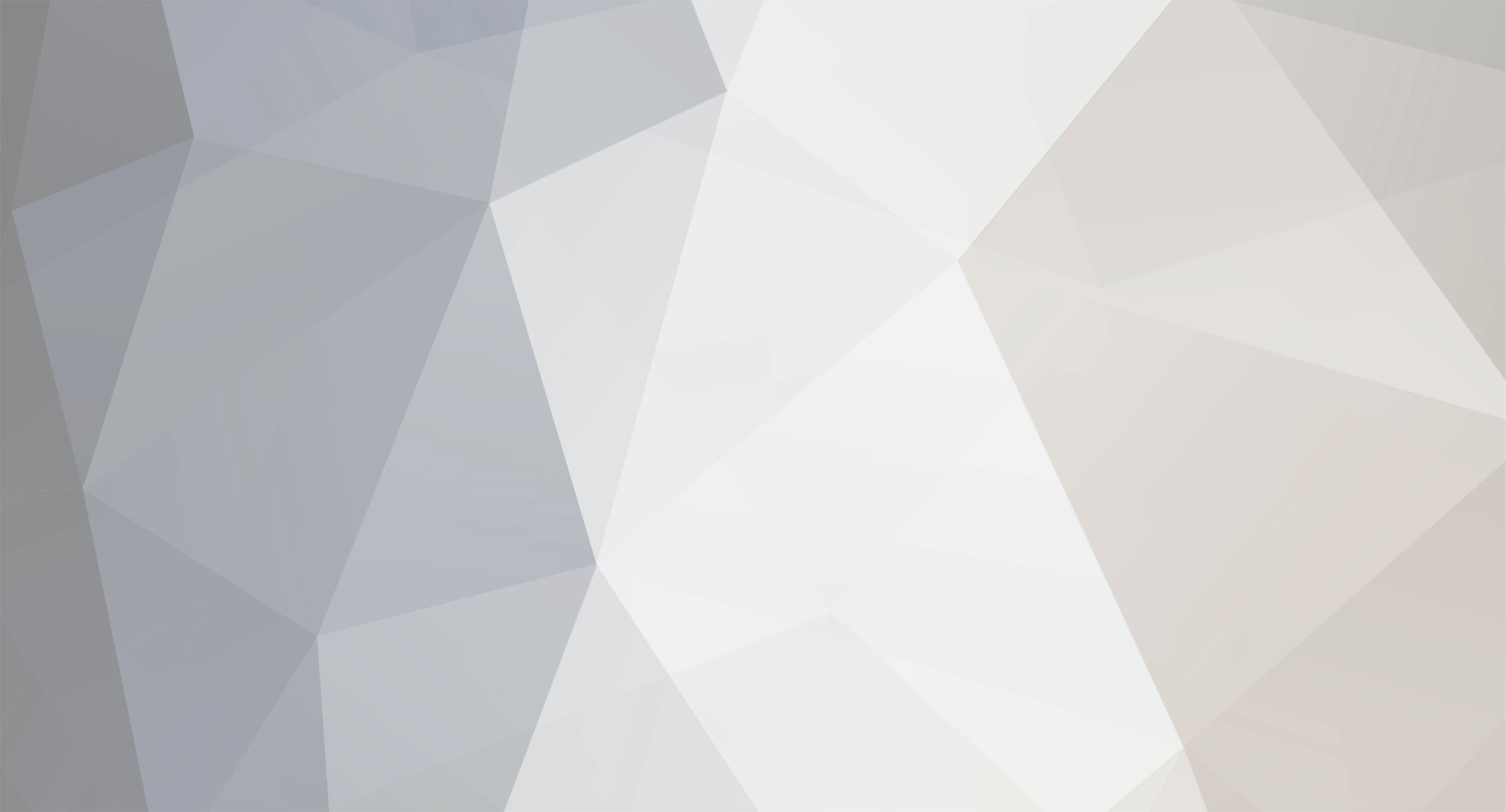
WGL
Members-
Posts
22 -
Joined
-
Last visited
Recent Profile Visitors
The recent visitors block is disabled and is not being shown to other users.
WGL's Achievements

Member (3/5)
2
Reputation
-
Had a telephone consultation with a local reputable installation firm today. The sales guy I spoke to was very helpful. He was very disparaging about the GSE frames which I'd been eyeing up. They had used them a bit in the past and had no end of problems apparently. Plastic warping (in warehouse as well as on roof), fixing holes in the plastic opening up over time and leaks because the drainage channels become blocked over time and water backs up. He spoke very highly of the Viridian in frame panels and system, which I'm going to have a look in to. As for having E, S & W arrays, he made a convincing case for the pro, in that you're most likely to want the power in the mornings and evenings when the East and West are producing. Makes sense I suppose. He was pushing the Tesla Powerwall 3, which does sound great, much to my inherent suspicion. It's all sounding very expensive mind😬
-
Hi there. We're going to entirely re-roof the house and do a loft conversion, just doing a rear extension at the minute. Not happy reusing the existing plain tiles as they're 60yr old concrete and looking a bit thin. Instead of buying new clay plain tiles (minimum £60 per m2 material cost and 150m2 needed), should I just put as many solar panels in a GSE type setup as possible? Front elevation of house faces due South, 45 degree roof pitch. Have always planned on getting as much PV on this as possible. I do also have a lot of East and west roof elevations where the vast bulk of the roof tiles will be needed. Should I spend the money on PV instead on the East and West? Am I likely to get much generation? There is very minimal shading from the odd conifer in winter. I do plan on getting battery storage and an ASHP in due course. All thoughts greatly appreciated. Thanks
-
I think self leveller with an airtight foam around the perimeter will do a good job of airtightness now I think about it
-
Adhesive foam to the underside of joist and between the sheets. Insulation retaining washers screwed from underneath as well. The last rows will be fun, but I'd work something out. Perhaps wire attached to the washer, fed through the board and tied off against joist. I would add some netting so that the weight of the fibreglass isn't borne on the EPS. Doing it with the EPS and rafter roll would give me a decent u value, without having to cut mounds of thick celotex. With the best will in the world, it's very hard to get right and a horrible job. I swore a decade ago I'd avoid cutting it if at all possible.
-
Yeah, makes sense. I'd be reluctant about a VCL under floorboards as they need glueing. Renovation screed over the top with a liquid DPM perhaps? Bitumen paint to underside of floorboards?
-
I don't like rigid insulation between joists/rafters/studs for many reasons. I plan on putting a lambda 32 'rafter roll' between the joists on my suspended timber floor when I lift the boards. Rather than using lapped breather membrane with taped edges, any reason why I couldn't put a graphite EPS board (50mm?) on underside, as it's open cell and therefore breathable? This assumes that I; Maintained a 150mm air gap underneath Adequately sealed and jointed with foam Fixed them securely Could actually get the bleeders in place I've tried to find actual breathability data and struggled. I would assume that thicker the EPS the less functionally breathable it would be. Would be interested to see what others thought
-
I've attached a pdf of my floor plans. North is at the top of page. Would be great to hear what others think regards M&E in general tbh. I'm looking to situate MVHR unit and any main heating source in the 'plant room' next to the utility ideally If I stuck with a vented cylinder arrangement, that would likely be in a cupboard in the first floor bathroom (not shown on plan) as that is where the cylinder is currently. If we went with unvented, that would be in the plant room. As stated prior, air con unit would be situated at top of loft landing space eventually (there is a section of flat roof for the external unit to sit on). If I could get away with a large A2A as the primary heating, would be good to situate there I think. I suppose I wouldn't have a problem with siting any of the other systems up there if it worked more efficiently. I'm open and appreciative of all suggestions. Thanks in advance. Will formatted floors 11-23.pdf
-
Thanks everyone. A lot to take in there, but it's all appreciated. I wouldn't be averse to installing a separate 'air recirculation' ducted system in addition to MVHR and wall mounted A2A. Not the most outlandish thing I've done over the years, but I suppose the devil is in the detail. I expect significant solar gains as main elevation is due South with the bulk of the glazing, so recirculation would aid with that. I anticipate installing aircon at the top of the 2nd floor landing regardless, in order to help alleviate overheating. Now I've done my calcs correctly 🫣6kw is the figure. Would rather go for 90% MVHR, I'm just playing it safe with the calcs at this stage. I can see me not having to heat the upper floor much in practice. Done quite a few loft conversions and often the customer ends up switching their rads off, plus they're guest beds anyhow (unless my folks move in of course). Dry air will definitely not be a problem. It's effectively temperate rainforest out my back door. UFH is out really unfortunately. The ground floor extension which has a concrete floor is basically kitchen units and a games room for the kids (pool table slapped in the middle). The main ground floor living area is suspended floor currently and in good condition so not concreting it, just going to insulate and airtight. I'll get together floor plans? They're all on autoCAD at the minute, so I need to play around with formatting first. Would be great to get opinions from all angles. Walls 0.18, Roof 0.16, Floor 0.18, timber DG argon low e. I'm doing the work myself so airtightness will be much better than on a site in reality. As a builder I know where the corners get cut unfortunately.
-
Thanks JohnMo, you were very helpful with my heat loss query yesterday. Sorry, Noddy question coming; If I factor an outside temp of -2 (I'm in South Devon so mild winters) and inside temp of 20 degress, what DT should I use? I hadn't even thought 2nd hand was an option! Can you give me (or direct me to) some information about your setup please? How did you install and commission it? How does the cooling work? Anything and everything you've got really. I've got my 18th Edition and Part P electrical qualifications, plus loads of experience with plumbing, so if it was possible for me to do the work that would be amazing. Thanks again. Will
-
Need some external opinions and advice please. Thought it best to post in this section as I want to go back to first principals. Going to begin renovation and extension on my 1960s house in the new year. It'll be broadly up to new build regs when finished. It's also going to be large (130m2 footprint and 3 storey) - because as a builder myself, why not? Just finished my heat loss calcs and with an 80% efficient MVHR system it'll be 4.8kw at DT of 18. Struggling with the heating option though. Currently have a rock solid but inefficient old natural gas boiler, 28mm main pipework and 22m to 15mm rad connections. I have a small log burner also. Giant asbestos header tank in loft so going to stick with a vented DHW option of some sort as I'm not getting that down. Very good mains pressure. Plan on having Solar PV with battery storage. Will need to change my rads regardless of option. Options as I see it; Small gas heat only boiler PROS; Cheap straight swap, given the heat needs will be cheap to run, easy DHW solution and an all round known quantity so I'm happy to run pipework and connect rads (done lots of this in past), heat only boilers are pretty reliable as they're so simple CONS; Not Eco ASHP PROS; Existing pipework suitable, cheap to run, eco CONS; worried an installer is going to way over specify and subsequent cost will be enormous (even with grant), concerned installer won't allow me to do the installation donkeywork and save money, we don't like it warm at night so a constant temp is not ideal, DHW a bit more of a faff than with gas A2A heat source PROS; with solar PV and storage negligible running costs, virtually free cooling, no rads, eco, more instant heat than ASHP, potentially better air quality if filtered??? CONS; how to recirculate the heat around a large house? no DHW, similar over-specification concerns to ASHP, not as easily configurable as an end user (seems to vary wildly between manufacturers also), less room by room control The A2A would be my preference really, but I discounted it because of the problem of evenly distributing the heat. Only back in consideration as the heat loss figures are so low. Is it conceivable to design the MVHR or some other ducted system to evenly distribute the heat cost effectively? They're large rooms, but it's definitely not open plan. I appreciate all input and thanks in advance. Will
-
Thank you for that, makes complete sense now. Much appreciated
-
Thanks for that. Sorry about my wording, I meant some sort of more traditional mechanical ventilation with trickle vents when I stated natural, you're right to point that out though. So how does the heat recovery (or lack of) get incorporated into my heat loss calcs? I'm calculating the heat loss to ventilation as; m3 of room X 0.33 X ACH X internal to external DT = Watts of ventilation heat loss How do I factor in MVHR vs MEV into this calculation please?
-
I'm about to embark on a full upgrade and extension of our 1960s house and I'm looking to carry out fairly accurate heat loss calcs. I want to know myself what size system I need. I am an experienced builder and able to do u value calcs and I feel I understand the pitfalls of building fabric issues well. Having looked at the formulae, ACH rate seems to make a huge difference to the result and is the main unknown variable. I'm aiming to get the place up to what I would call a 'decent quality new build' level of airtightness. The end result will be EWI to existing (has blown EPS in cavity also), fully VCL and taped membrane timber frame with rendered blockwoork skin to extension, new double glazing and a warm roof loft construction. Existing suspended timber floor is the week spot, but going to rip up boards and insulate. We also have an under 5kw log burner which we're hoping to use a lot less. Roughly what ACH value should I be looking at please? One for natural ventilation and another for MVHR would be great. Apologies in advance, I'm sure this info is on the forum somewhere but I'm struggling to find it.