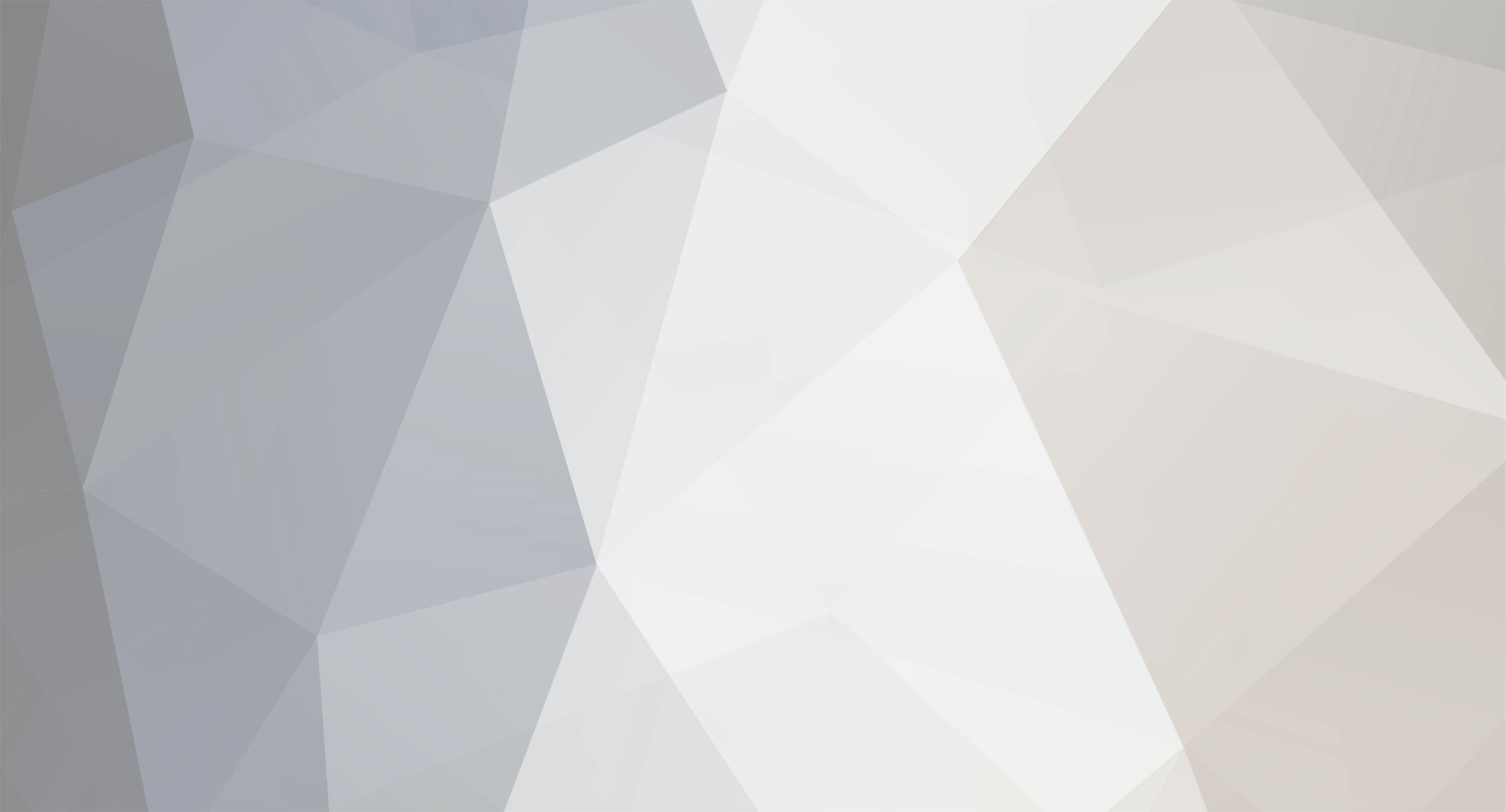
vala
Members-
Posts
225 -
Joined
-
Last visited
Recent Profile Visitors
The recent visitors block is disabled and is not being shown to other users.
vala's Achievements

Regular Member (4/5)
23
Reputation
-
That idea has been floated but the disruption to the f/f has muted it. but 100% would have been the simplest solution.
-
Hi Nick, which section to you mean? that particular L shape wall has the kitchen on one side, and top half of the staircase after the 1/2 landing. i've cleared the hardcore and dug done to hit clay. Can tamp that firm and place scaffold board under the prop.
-
So SE came round today and due to the state of the concrete slab under the wall it needs to be supported, remove concrete and whatever is under, and dig a footing. due to access on one side I'm hoping to use strongboys at around 800mm spacings off size 0 acrows. I asked a builder mate of mine who said strongboys can move a bit if not a solid wall above. but all the literature for strongboys says there fine for single storey walls. anyone here had any experience of using them with single storey walls?
-
It's a single storey block wall and the long part I believe has been created for the staircase stringers to fix into. The short section has a small RSJ coming off it to the external wall. Looks like this is to provide support for the timber joists. Above both sections, is a simple stud wall diving the bathroom/landing and bathroom/bedroom. Got 200mm PIR going on top of the sand.
-
In the build up to having a new structural slab installed the existing slab has had to be broken up. The groundsworkers have gone to town with the use of their breaker and created a bit of a mess here on a single storey block wall. Had my builder round today who wasn't impressed at all, but whilst I wait for the structural engineer to visit (hopefully tomorrow) I was looking for advice if anyone has in order to rectify. 1 suggestion me and the builder made today was put needles through at intervals, and prop using mini acrows. Most likely need to create a solid foundation for the acrows. Then remove all the earth and old slab, before digging a new footing underneath and building up with bricks/blocks for this wall to sit on. Any other suggestions welcome whilst I sit and worry a bit about this stage!
-
Thanks for all the comments. where the pipes will be coming out of the concrete and into the manifold is there a need to put some insulation/conduit over these areas or fine to leave bare? seen images of some with or without but cannot see why you would/wouldnt.
-
exact same level of insulation and floor build up/finish as the rest of the house. It's all getting done at the same time.
-
yes. thought it best in case that ever changed at some point to a habitable room. Plus I often work in there, so saves me firing up a heater.
-
Thanks all for the comments. Looks like some of the base units in the kitchen area will contain food, but as I don't know which ones yet think I'll play it safe and just leave that area unheated. Got the final plans through from Wunda and aside from a phantom door (circled in green) which isn't in our house, they've put the pipe everywhere in the small room at the front. Here there's just a washing machine and small unit for a wash basin. Worth veering round those 2 or just go under?
-
We have a polished concrete floor being installed in July so next month have to install the UFH. Had a design completed with Wunda and they have omitted any pipes under the kitchen units/fridge freezer etc. As it's a polished concrete floor, and expecting to be running low flow temps would having it under the units, fridge freezer have as much of an adverse effect on those appliances? My thoughts were that the heat would end up underneath them anyway as it's all being poured as one slab. So just wanted to gain and advice from here as to whether I'm on the right track and have the UFH everywhere? For what it's worth the fridge freezer will be a free standing unit.
-
An update to this thread. Bit of a u-turn but we've ended up booking in a firm to provide a polished concrete floor finish. They're also going to pour the concrete. Architect noted my area had a 2-3% chance of radon so suggested to keep BC happy install a radon barrier after sand bind. so build up now is: 150mm type 1 50mm sand radon 175mm PIR dpm ufh pipes stapled to PIR 125mm concrete Concrete firm install a193 mesh and use fibres as part of their work. SE is satisfied the compressive strength of the PIR will support the concrete. Is FI5000 PIR worth using over GA4000?
-
Thanks for all the replies. I've fired off the floorpans to a few companies and will see what they come back with. If the supply vents could come out of the wall I could run a duct beneath the ceiling (above the wall units), from the blue x on the ground floor and in the direction of the joists. Attached an image to make it clearer. Green x would be the supply vents. As for an extract vent by the sink (reply by @Marko), I possibly could get a vent beneath ceiling and above the wall units/extractor, then come up into the ceiling and over to the sink, but would depend on the height needed within the ceiling void for the extract vent. Don't think I'll be able to get a extract vent to the WC on the GF so maybe just go for a standalone unit in there.
-
Joists are solid. i will have access from the ground floor as existing plasterboard all coming down. so currently due to the floor build up for the first floor UFH I have approx 75mm space left, however I could increase this to 100mm with some baton.
-
house is 1970’s semi detached. Has 55-60mm cavities which have recently been filled with eps beads. Loft has 250–300mm insulation. New aluminium windows and doors, all installed with me508 membrane, air seal foam, compriband. ufh is at 135mm centres and sits on 100mm PIR and covered with 25-30mm dry screed. On top of this is t&g boards and aside from the bathroom this is topped with thermal stream underlay and a low tog carpet (total tog 1.8). In the bathroom 6mm hardie is on top of the t&g boards, then ditra mat, then tiles.
-
Apologies I should have been clearer. in ground floor, floor plan; blue ‘x’ is a small opening from ground floor through to the loft. It’s open at present as it’s where my flow and return for first floor UFH go up, along with h/w. blue arrows are direction of joists. green ‘x’ is location where a grille could definitely go. green ‘x?’ is a possibility. on first floor plan; blue ‘x’ is the location of the gap from loft to ground floor. red ‘x’ is where the bathroom grille would have to go. This is due to bathroom ceiling is solid surface and grooves for extractor already routered in. green ‘x’ is where definite grilles could go, with no restrictions on duct size as that would be in loft.