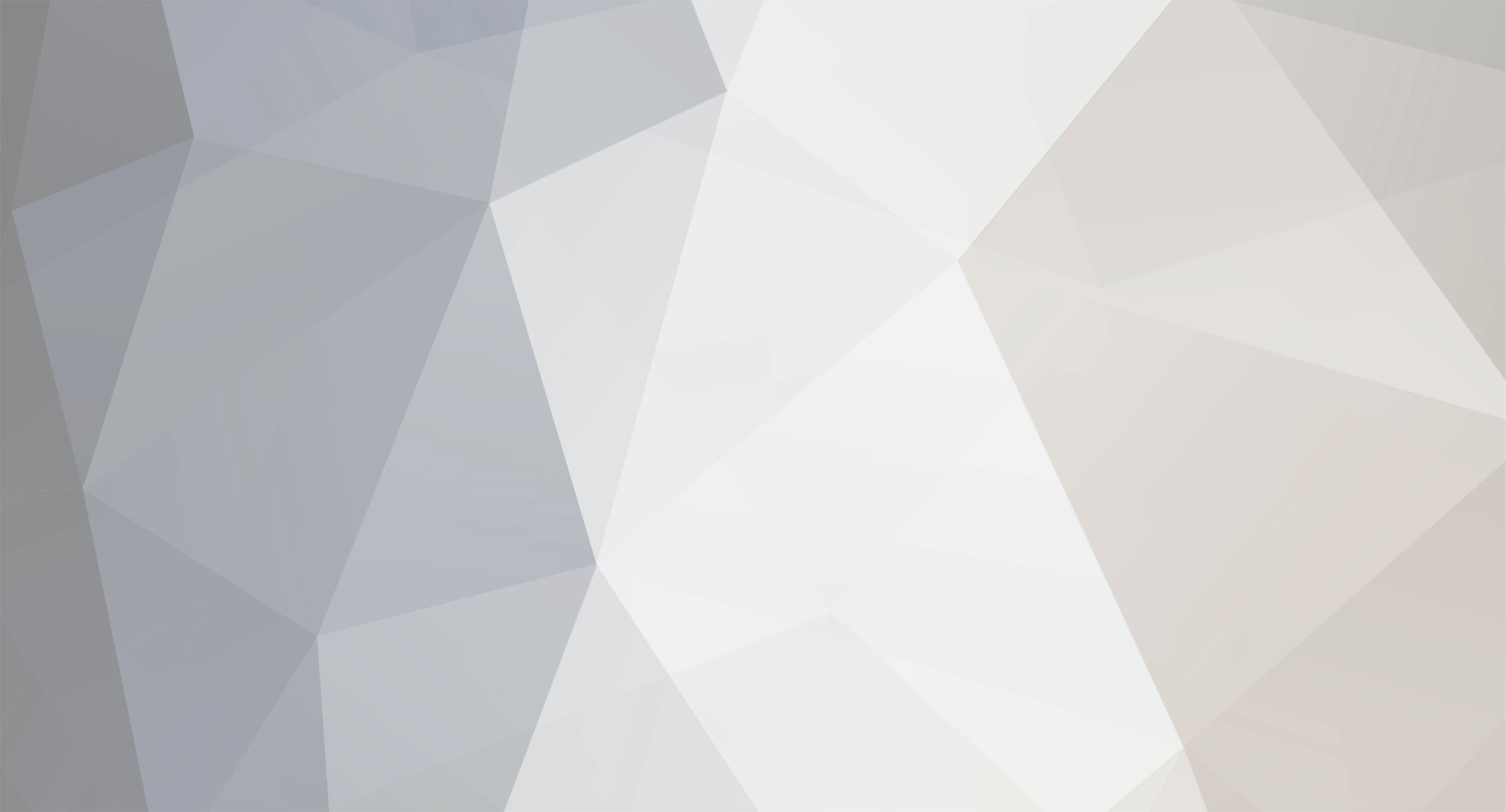
jimmyhorns
Members-
Posts
15 -
Joined
-
Last visited
Recent Profile Visitors
The recent visitors block is disabled and is not being shown to other users.
jimmyhorns's Achievements

Member (3/5)
1
Reputation
-
Why so thick screed layer? Am I being an idiot
jimmyhorns replied to jimmyhorns's topic in Underfloor Heating
but the big question for me is why? is it because of strength and the flexibility of what is underneath? -
Why so thick screed layer? Am I being an idiot
jimmyhorns replied to jimmyhorns's topic in Underfloor Heating
But why can't self levelling (liquid screed) be a lot thinner than 50? It is specified for use at 6mm for levelling (some brands you need to add sharp sand if you want to lay thicker than 6mm). Its why it needs to be so thick that confuses me. No pun intended. -
i am having a bit of a nightmare working out what is going to be the best way to install underfloor heating in one section of a room that is going to be a kitchen / diner / living room. The bulk of the room (27m2) where underfloor heating is going to be laid is new - and so has an insulated floor, and there is plenty of room above (75mm) to screed over the UFH pipes in the traditional way. I think the builders will be using the traditional method for screeding. The kitchen area is a similar size, but only 17m2 of this will have underfloor heating due to cabinets etc. This floor is existing, and appears to be traditional screed (60mm) on concrete. It was made in the early 80s and I doubt is insulated. Taking up the screed is a piece of cake with a breaker. The concrete not so much. I could have the screed out of the areas required in half a day, but this will only give me 60mm depth to play with. The UFH heating pipe I have is suitable for being buried under screed. It is also suitable for being retrofitted in insulation boards directly below the finished floor surface - I.e. it is strong/durable enough for this. These boards are covered with a very thin layer of flexible self levelling compound. I have read that a lot of the thermal loss from floors is laterally - and it will be easy to fit insulation laterally around edges of the removed screed to reduce this. To fit the 16mm pipe I would be looking at 40mm PIR insulation with 20mm screed on top. I would fit 100mm wide strips at the edges to prevent lateral spread. The area will eventually be tiled. So a couple of questions 1) Why does screed need to be so thick if you are laying it as liquid screed/self levelling compound? 2) How crazy is my above idea 3) Are there any other 'reasonable' alternatives (there is no space for radiators) Thanks James
-
I have also posted this in the screwfix forum, so apologies if you look at both! I'm currently in the process of mapping out how and when our current heating and hot water installation gets changed over to the new system as part of a house extension. Currently we have a regular boiler, feed and expansion tanks for both the central heating circulating system and the conventional vented hot water cylinder. We are moving to a system boiler, with an unvented cylinder. I understand that with a system boiler, the water that is sent to the unvented cylinder is heated on its way there by the system boiler. What happens once it has gone cold in the cylinder? (is there still a loop with a 3 way diverter valve taken off the central heating circuit like the current Y plan design.....? ) Surely it cant rely on the water having been heated in the past and not getting too cold?.... Thanks James
-
Radiators (generally) are plumbed in a parallel circuit in order for them to work correctly. If you join them in a line (serial connection) then one radiator will be hotter than the other, and the flow through both radiators will be limited to wherever the greatest restriction is. I cant draw where I am answering from at the moment, so will try and do it with words. Where the current pipes are connected you will need a T piece, on both the feed and return lines. take a connection from each of these to the new radiator. Once the system is then refilled and bled, rebalance the new radiators to the system. You will of course need to adapt the pipe work to the first rad as it is half the length of the old one. You should have a TRV on both new rads, and balance the system using the valve on the other end.
-
Thanks Tony When there is reference to the area being floored, does the floor have to be flat and continuous. What I mean by this is that in the wider angle photo, if I floor the 'gaps' between the 2x6 going across the trusses, is it ok for the installer and later engineer to have to step over the remaining supports? There is 600mm between centers for the trusses, so presumably the metre in front needs to be the width of the boiler plus as much as I can leave? There is a single immersion in the tank as a back-up and for frost protection and looking at the spec while this wont give us the luxury of 2 baths being filled simultaneously, its enough to get away with in a push.
-
Thanks Peter I hadn't thought of Tracpipe as there is a significant external run (4m up from the meter box) on the outside wall of the house and didn't think this would be acceptable.... It would however allow the whole run to be done as one piece without any joins. I've just ordered 10m of the 28mm along with tape and fittings which should be completely future proof in terms of if we need a bigger new boiler. I can get the tank in (just) at 530mm in diameter by removing the loft hatch (i fitted it with screws rather than nails about a decade ago 'just in case'). Its 1600mm in height. The current 227 litre tank is raised off the trusses by a jenga arrangement of 2x6's, presumably to give it some height (there are 4 levels). This spreads the load across 5 or 6 trusses, the end two of which are doubled up. This has been carrying the weight of the tank, and the heating circuits e/f tank for 40 years and looking at the total loading from the new system I will be about 30kg over this which will hopefully not be an issue, though with some of the wood I am removing I am likely to get to more like 20kg over or even closer to neutral. The expansion vessel isnt actually connected to anything - I was just trying out the location for height and access and then realised I had better plan for the boiler now rather than later!
-
Do be fair, I am surprised the thread stayed intact as long as it did!
-
That's pretty much what laparoscopic surgery is Always difficult to get into the corners without making a mess of it.
-
Be careful what you wish for I have just posted my first 'proper' post.....
-
I am in the process of getting my loft ready for (and doing some of the fitting of) a multi-phase process. An extension is being undertaken and the current heating and hot water system is being significantly changed. Currently we have an vented heating and hot water system, with heat coming from a regular 'heat only' boiler in the ground floor kitchen. An expansion / feed tank in the middle of the loft for this system, a pump in the airing cupboard on the first floor on the opposite side of the house from the boiler. There is a expansion / feed tank (227 litres) for the hot water cylinder that sits in the airing cupboard. The airing cupboard is going (it forms part of the new ensuite) and as a result we are swapping over to: Unvented hot water cylinder in the loft (to replace the 227 litre e/f tank) Unvented primary circuits on the central heating / hot water system, with the expansion vessel and filling point being in the loft. Once this is done we will then be moving the boiler to the loft (or installing a new one, not sure yet) and moving the circulating pump and 3 way valve up in to the loft. There appears to be only one sensible layout for the relative positions of these things in the loft. Mostly this is driven by where there is adequate support for the weight of the new unvented cylinder, and where the gas supply will be entering the loft. Having done the calcs, to allow for the 2x 45 form bends to get the gas pipe in through the soffit board and then onto a truss and then two further 90 degree form bends to get to the boiler, in the planned 22mm pipe the maximum length is 5.5 metres. Once allowance is made for the drop down and out of the soffit (before it mates with 28mm pipe from the metre) this only gives me 5 metres of length to get to the boiler, both in the horizontal and vertical axis. The bends required to get into the loft make running 28mm through the loft a nightmare and I am keen to avoid this. I am hoping to have everything ready to go for the boiler fitting on this conversion for a gas safe fitter to come and do the soldering of the gas line, and then connection of the pre-installed flow and return feeds, and of course the installation of the flue. When I say everything ready to go, I mean all the pipe cut to size, with the appropriate bends etc (not soldered where joins are required). Partly this is down to me wanting to do some of the work myself, but a great deal of it comes down to cost. There is limited budget for the extension, as with most things in life and I would prefer to be able to move the boiler rather than leave it where it is to save costs (the kitchen becomes a 'snug' room after the extension is done). So I guess the point of the post is to 'sense check' where I am planning on the various bits being installed, because it's going to be a massive headache if all of the water side of this gets done, and then it turns out this is the only place where the boiler can be. I have attached a couple of drawings of what is there now and what I am planning. The new boiler position would be just to the right of where the expansion vessel is now.
-
Gynaecologist..... We tend to be less keen on lopping things off....
-
Hi, James here. Im 40, going on 20 going on 60 depending on what job I have ahead of me with the house! We live in a 1980's build, which is about to be extended. I have always tried my hand at most things, but in this instance the actual build is going to need to be left to professionals. Lots of work will be required for me to get the old bit of the house ready though, including a fair bit of plumbing and a boiler move. I'm reasonable at plumbing, carpentry, electrics (to the limits of what is allowed of course). By trade I am a surgeon. Looking forward to seeing who I can contribute and what I can learn here.