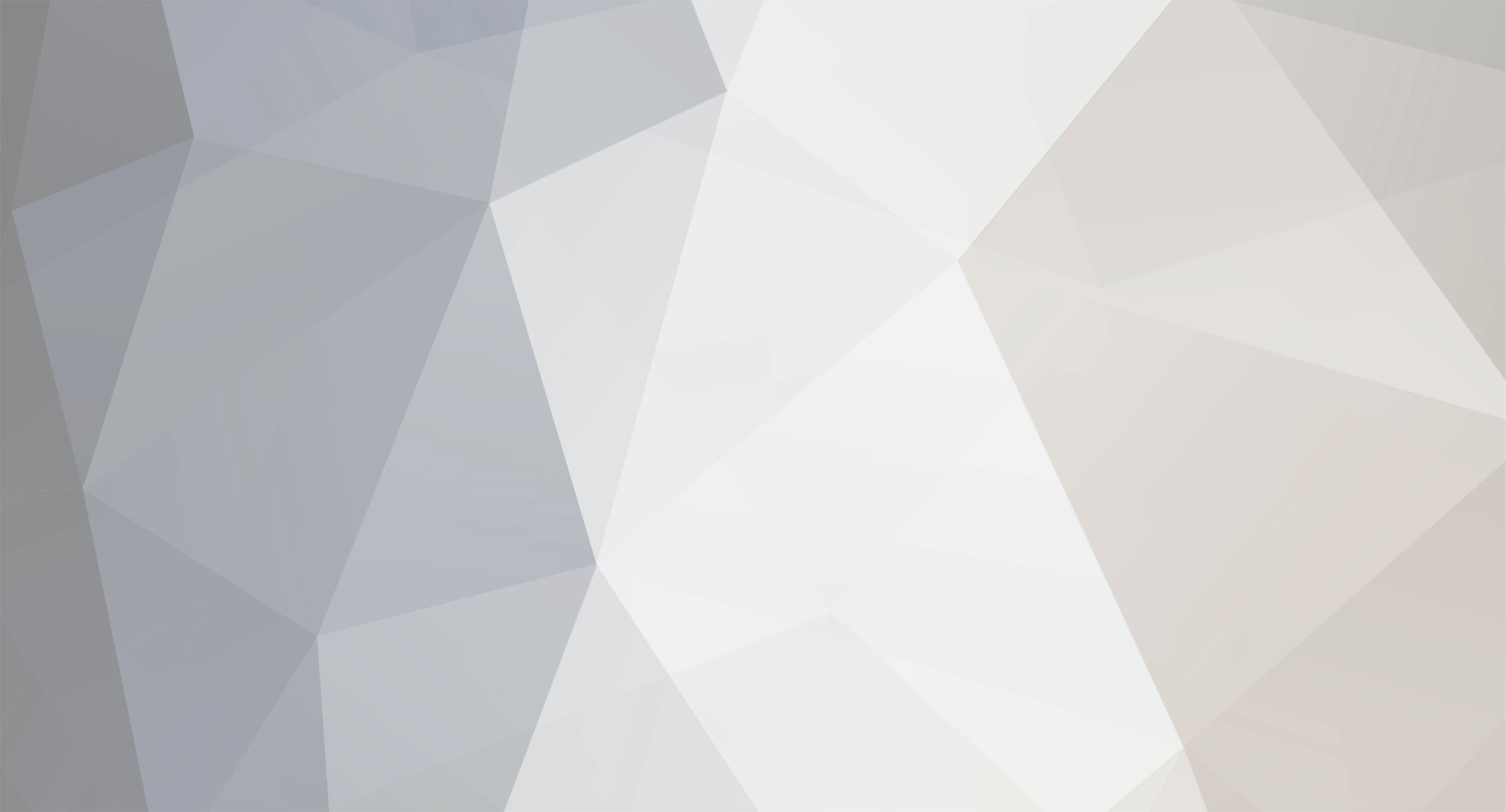
gaschick
Members-
Posts
30 -
Joined
-
Last visited
Personal Information
-
Location
Wiltshire
Recent Profile Visitors
The recent visitors block is disabled and is not being shown to other users.
gaschick's Achievements

Member (3/5)
1
Reputation
-
Warm v's Ventilated Roof - Which Way to go ?
gaschick replied to bob the builder 2's topic in Roofing, Tiling & Slating
Forgot to add, there are structural steels going into the walls as well, which complicates matters internally! -
Warm v's Ventilated Roof - Which Way to go ?
gaschick replied to bob the builder 2's topic in Roofing, Tiling & Slating
SO, the timber frame is being made off site between 7-10th April. The windows were ordered from the timber frame design to fit into the timber frame in December, and are being delivered 8th April. This is a very common thing to do with the specifications on the timber frame being so accurate. Otherwise, we would maybe be waiting 3+months for windows to be delivered. The top slope of the window is 13 degrees, but not shown terribly well in this plan! As you can see, there still isn't much space for the flashing at the point where the roof joins the exterior wall of the house. I hope that this drawing makes more sense. -
Warm v's Ventilated Roof - Which Way to go ?
gaschick replied to bob the builder 2's topic in Roofing, Tiling & Slating
Don't get me started on the roof angle! It cant't be changed as the window in the end wall follows the roof line and this has already been built off site. The roof started at 15degress, but due to the massive structural steel needed to hold up the left and slide triple glazed patio door, the angle changed. The roof has caused a lot of agro and extra expense as we had to take out the existing dormer in our bedroom. -
Warm v's Ventilated Roof - Which Way to go ?
gaschick replied to bob the builder 2's topic in Roofing, Tiling & Slating
Thanks @SimonD. The issue we have is that there isn't much space above where the new dining room roof joins the walls to add extra roof build up on top of the plywood (see drawing above on right). We have already had to remove a dormer window and replace with velux as we were concerned that we wouldn't have decent depth of flashing. The old roof leaked at the join due to lack of depth of flashing, and when it rained water pored down the internal walls. We don't want a repeat of this. -
Warm v's Ventilated Roof - Which Way to go ?
gaschick replied to bob the builder 2's topic in Roofing, Tiling & Slating
Yes, also, we are keen to maximise heat decrement delay as well. Hence not going with something like the multi foil insulation materials. We need to stay cool in the summer, not super hot! -
Warm v's Ventilated Roof - Which Way to go ?
gaschick replied to bob the builder 2's topic in Roofing, Tiling & Slating
https://www.womersleys.co.uk/techguides/productattachments_files_w_o_wood_fibre_insulation_u_and_r_values.pdf @Temp @Iceverge Here are the quoted values for the Steico flex products. Link to the suggested build up before. I realise that I have totally hijacked this thread, but it's the thread that keeps on giving! -
Warm v's Ventilated Roof - Which Way to go ?
gaschick replied to bob the builder 2's topic in Roofing, Tiling & Slating
@Iceverge If you read the whole thread, then I am proposing to use wood fiber insulation tight between the rafters on our standing seam roof of our timber framed extensions (e.g. Steico flex or Pavoflex). As the timber frame is being made off site, then having the 18mm plywood applied on site to the design I have included in the thread, I think it will be difficult to put the battens in except underneath the ply to stop the insulation breaching the ventilation gap. Joists are 220, so we have some room to play with. My U back-of-a-fag-packet calculations (without including the ply and roof) were 0.16, which will be within building regs. -
Warm v's Ventilated Roof - Which Way to go ?
gaschick replied to bob the builder 2's topic in Roofing, Tiling & Slating
@Temp you have literally just drawn a copy of the diagram that we drew yesterday! Great minds and all that! I have also done some calcs for the u value using the r values of just the Steico products in the first instance - flex in 160mm, their own general all purpose board, and then 40mm Steico flex in the service void. This suggested build up was from the Steico website https://www.steico.com/en/solutions/new-construction/roof-construction I don’t know how practical and easy it is to insulate a service void - surely an oxymoron?! A void is a void? Anyway, doing this build up, my back of an envelope calculation gives a ball park u value of 0.16 even without including the r value of the outer 18mm plywood sheet. I will try running this again with different insulated plasterboards. -
Warm v's Ventilated Roof - Which Way to go ?
gaschick replied to bob the builder 2's topic in Roofing, Tiling & Slating
Thanks @Temp for the useful video and guidance. I don't know why only 120mm insultation. We have fired off emails this morning to various folks. We are indeed worried about the fit of the PIR in-between the rafters. If it's done badly with not a tight fit, you might as well have just stuck some bubble wrap up there I guess as at least this would be flush with the edges! Builder wanted to use Actis Hybris [tag line -'tomorrow's insulation today...'] to start with as the local builders merchant told him it was a great product specifically designed for timber frames, and easy to fit. Having entered another internet black hole on best forms of insulation, and wanting the whole room to not super heat, mention has always been made on the decrement delay of these products not being great. So, I have explored using flexible wood fibre insulation instead of either the PIR or the actis hybris. I have tried to get in contact with several suppliers of this to get some guidance about this use, and no-one has got back to me yet. We would probably need to use several layers of the stuff in order to get a decent amount of insulation. But, as it's a push fit and fits snuggly, this might be the way to go. -
Warm v's Ventilated Roof - Which Way to go ?
gaschick replied to bob the builder 2's topic in Roofing, Tiling & Slating
@Russell griffiths It's a damn site thicker than the old roof we had on which was literally one layer of cedar shingles, a layer of silver foil, and a layer of plasterboard! I am quite looking forward to the sound of the rain gently drumming on the roof as at least it shouldn't leak like the last one! -
Warm v's Ventilated Roof - Which Way to go ?
gaschick replied to bob the builder 2's topic in Roofing, Tiling & Slating
-
Warm v's Ventilated Roof - Which Way to go ?
gaschick replied to bob the builder 2's topic in Roofing, Tiling & Slating
@JohnMo I have no idea, I am not an expert in this area. I am a doctor, not a building control officer, architect or builder! This is why we are paying people to design the structure, and do the structural calcs etc for it. As a reasonably intelligent person though, I try to do due diligence as best as I can about the things we are paying s''t loads of money for (much at the annoyance of my husband). I have enclosed the timber frame section through the roof. -
Warm v's Ventilated Roof - Which Way to go ?
gaschick replied to bob the builder 2's topic in Roofing, Tiling & Slating
Thanks @Bobthebuilder2 @Tempand others for this very useful thread. We have an alternative design for our ventilated roof which I was seeking some help with. We are also having a standing seam roof Greencoat PLX on a timber frame single storey extension. The 18mm plywood onto which the greatcoat is being fitted is bing supplied and fitted by the timber frame engineers, so we can't realistically have the extra sets of battens on top to form an extra ventilation cavity. Picture enclosed of the roof deign to which Roe are working. I was hoping to be able to fill the space between the rafters with wood fibre insulation eg streico flex, rather than the standard celotex to maximise the thermal delay. We don't want to end up with a noisy caravan like roof! No battens are shown in the design though, unlike all of the others. Should these be fitted to the underside of the plywood to keep the cavity and stop insulation pushing up next to the plywood? Anyone used a wood fibre insulation in this situation? Should we just stick to the celotex, realising that this will be much harder to fit tight between the rafters? -
Thank you @SimonD I will double check the specification from the TFM when I get home. Not as far as we know for planning conditions. The only people that will see the top of the roof will be us. It's not visible from our neighbours. The builders have used a qualified Sarnafil contractor before for another job
-
Hi @saveasteading Builder looking at Sarnafil standing seam effect £3780+VAT Standing seam £7164 +VAT WRT the visuality of the roof, the upstairs bedroom window, and landing windows will look down on this. I will try to upload the roofing plans. @SimonD the builder is getting specialist contractors in for the roof, so not fitting himself and was looking at Sarnafil. As we passed planning with a standing seam roof, I think that Building Control might say something if we changed the look of the roof now... p.s. we are in a very rural agricultural area.