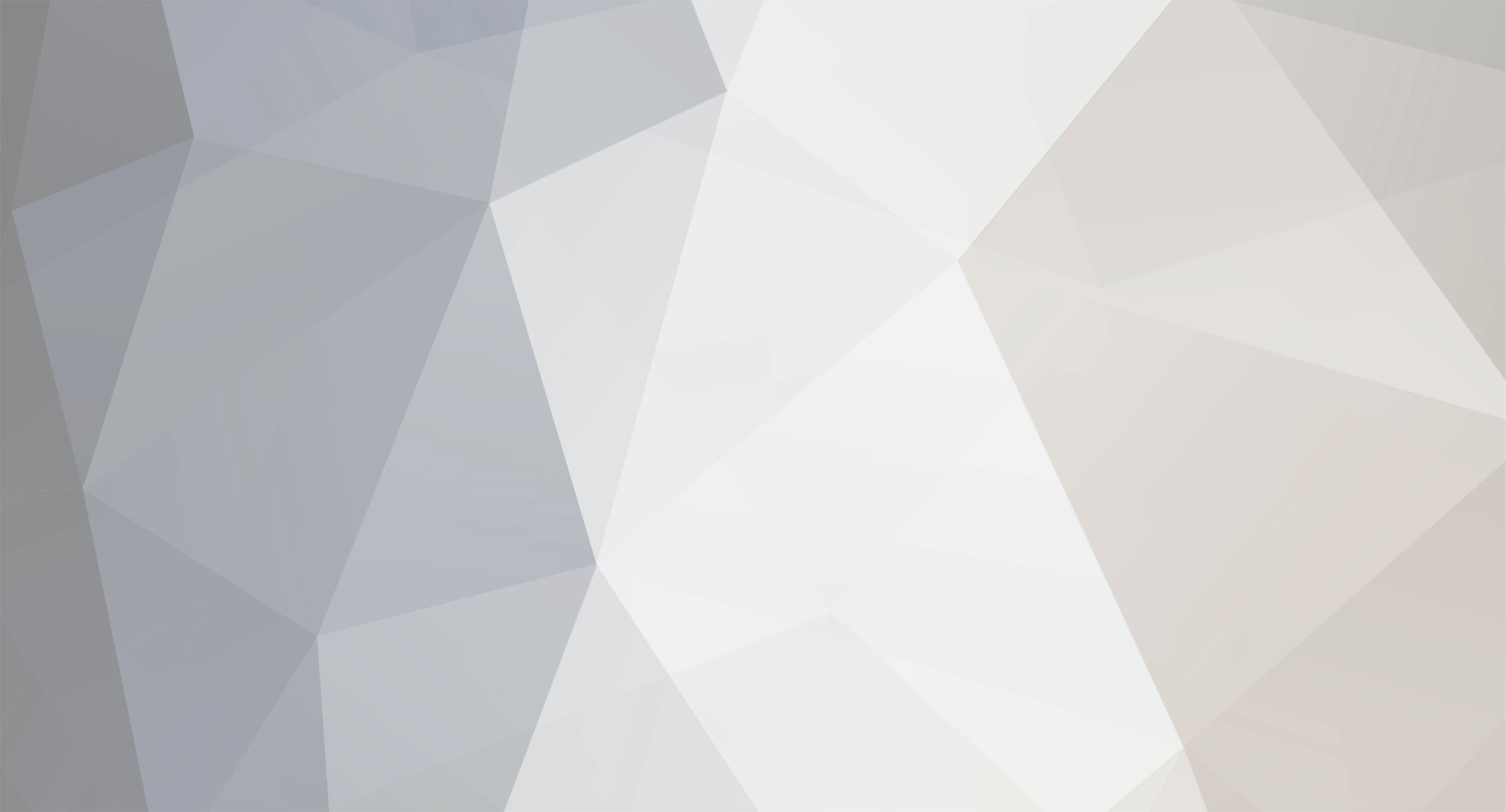
Indy
Members-
Posts
233 -
Joined
-
Last visited
Everything posted by Indy
-
Finally made a start to our project yesterday (mark the date) where trenches have been dug to relocate the existing gas and electricity cables etc - a long time coming after about 4 years of waiting! Wanted to find a way to view progress on site and do a sort of time lapse video. Looking for any recommendations that people might have used to record the progress. We don't have Wifi on site anymore but there is power obviously through the TBS and the builder is open to having a feed for the camera - although I see that there are battery powered solutions with solar panels that can be totally self contained. Would like the ability to have constant recording for up to a week when I can go and swap out the SD cards and also the ability to login remotely to see what's happening at any given time.
-
This topic comes up quite often and there are a lot of people on the forum that seem to indicate that TF houses aren't a problem to insure or get mortgages on. I did a lot of research and spoke to a very good friend who's also a partner at a Mortgage brokers, and the general reply was that if it's non standard - you will eventually find what you're after, but it won't be easy and it won't be cheap as you're ruling out the mass market deals which are targeted at the standard, identikit, lower risk options on the underwriters spreadsheet (block built houses). Partly the reason why I chose to go masonry (the other was that TF worked out to be marginally more expensive though that could be offset by lower labour costs and a shorter schedule).
-
Auction could be a good idea but you need to really know what you're looking at, and then there's the accelerated timescales in which you need to complete. Great if you're a cash buyer and can work to those and there may be an opportunity to look at some bargains - haven't ever done so personally. I guess the riskiest factor with auctions is not knowing what you're buying or what horrors lie underneath the surface, but if you're looking at it as a knock down and rebuild - then all you're interested in is the underlying land and value the plot that way. With regards to the rebuild cost - you'd be looking at a minimum of about £2k/sq m if you're project managing yourself and anywhere between £2.5k - £3.5k for a full turnkey project managed build by a main contractor. That doesn't cover any cost of land, professional fees, specialist landscaping and joinery usually. Work on that basis and you can then calculate the size of house and value of land you're able to afford. As to where to find them - I've only ever used the online portals (Rightmove, Zoopla etc) myself. Some people pay to access plotfinder services so you could try that if you wanted.
-
One option that worked for me personally was finding an old bungalow / probate sale type property. Large(ish for the area) plot with a relatively small house that allowed redevelopment. It doesn't stack up for a developer as there's no margin in these things but just about work for a self builder to do them up for themselves and live in. What's your budget out of interest (as you've chosen 2 of the most expensive home counties)?
-
Deciding to say "no" to a self build opportunity
Indy replied to maison d'etre's topic in General Self Build & DIY Discussion
Or the extremely persnickety who wants things to be just so and can't find pre-built houses (new or existing stock) that meet those requirements, leaving self build as the only option. -
MVHR and cooling
Indy replied to flanagaj's topic in Mechanical Ventilation with Heat Recovery (MVHR)
After a lot of research into UFH cooling with ASHP and Fan coils replacing radiators, this is the approach I'm going with. UFH with standard MVHR. Separate multi-split Aircon system to cool down the key rooms (bedrooms and living area). Heating things keep house nice, warm and relatively airtght. Cooling system blows nice cold air when I want it. Solar PV will mean you can run the air con on extremely hot days for very low costs. -
Deciding to say "no" to a self build opportunity
Indy replied to maison d'etre's topic in General Self Build & DIY Discussion
This. Pretty much the only reason why I'm still sticking with the whole process. The market where I am has definitely softened in the last 12-18m, so it's now possible to buy something which offers us the same 'amount' of space as we're currently building and largely delivering the other criteria (area, garden, proximity to schools, transport etc). However, every single one of them will need to be reconfigured and need additional time and money spent to get us the house in the condition that we want, the configuration we want, with the specific finishes and all that jazz. At which point, its just easier to build your own and do it all properly anyway and then you know exactly what's gone into the whole process and what to expect. -
Very interesting and quite a reasonable cost. I'm going for a traditional masonry build so makes even more sense to do it as the airtightness inherently will be worse than a SIPS product due to the nature of the build process.
-
Can I ask how much this cost?
-
Deciding to say "no" to a self build opportunity
Indy replied to maison d'etre's topic in General Self Build & DIY Discussion
Building a 285sq m house plus double garage will easily mean spending between £600k and £900k for a mid level/good quality finish without going over the top. Add in the professional fees/rental/SDLT and other related costs - you could be touching £1m on top of the £500k plot purchase price. -
Do I need a PM if I'm engaging a main contractor?
Indy replied to Indy's topic in General Self Build & DIY Discussion
Agreed. The hard part is how do you find out before you engage which one is honest and decent against which one is an shyster. Unless you plan for worst case scenario and cover the eventuality that all of them are shysters - thus leading me back to his statement (and adding increased cost). -
Do I need a PM if I'm engaging a main contractor?
Indy replied to Indy's topic in General Self Build & DIY Discussion
So mixed responses here. I agree (in my head at least) that it seems to be duplicating a bit of cost. However, I do also fully recognise my limitations - in a sense, even if I'm directly staring at some work that a builder/brickie/electrician/plumber would have done, I'd have no way to tell if it was good or not based on a visual inspection. I'd be relying solely on the word of the main contractor. I've done a lot of sifting through and found what I think are people that are trustworthy and people I can get on with - however, I'm not sure how much I can take anyone on their word. As my architect reminded me, everyone in this business is a shark and if they can find a way to charge you £500 for £50 worth of work, they will! -
Been working with 2-3 builders to get prices for our build based off the Construction drawings/BR submissions. Did not go down the QS route and getting a BoQ (unpriced) for a formal tender process - as it's a one off new build and probably too small a job to be tendered like that. In discussion with all of them, they've hinted/implied that the price we're working to is based on not having a QS engaged as it means more effort for them / and more money for me - i.e. if they have to demonstrate and argue the toss at each stage payment so they would have to build in some fat into the contract if we choose to go down that route. We're engaging the builder/contractor for a full turnkey finish, so they will have their own site manager/project manager assigned to the project (which I'm already paying for). Do I need to also engage a separate PM that visits the site once every fortnight and work with the builder to manage the stage payments? Not sure how much this would be but it seems like an added cost and is that something I'd be able to take on myself? How have others managed it on their builds?
-
Implication of not using MVHR
Indy replied to Indy's topic in Mechanical Ventilation with Heat Recovery (MVHR)
£2k sounds virtually impossible unless I source odds and sods off eBay myself - which implies I would know what's needed. Even the most basic unit from BPC without cooling was £4200 (Vent Axia) which then climbs up to £5800 for Zenhnder. That's the parts only without install. -
Current plans are for a masonry build and SAP calcs include MVHR + cooling option. Not passive house but BR specs and airtightness target of 3 (I think). After speaking to a local builder, we’re leaning towards a timber frame build (MBC maybe) for speed mainly. Wanted to understand what the implications would be if I decided not to go for an MVHR system – mainly for cost. It seems to be adding about £10k+ to the build cost and to be fair – I’d rather use it for an air con system. Not seeing the payback apart from the comfort option and my personal feeling is that the comfort I get from having heating/cooling/dehumidification from an air con system is going to work better for me. What would it mean for the windows – do I have to add trickle vents or is there another way to overcome this requirement in a generally airtight build? I assume not going for MVHR would trigger a new as built SAP calc to be done at the end of the build, but as long as we achieve the same or higher in terms of overall efficiency – that should be ok?
-
German kitchen brands - Nobilia, Bauformat or Leicht?
Indy replied to Indy's topic in Kitchen Units & Worktops
From what I've been told - a freestanding appliance is not eligible for zero VAT. So an American style freestanding fridge/freezer would not qualify but integrated appliances would as they are 'built into the fabric' rather than just unplug and take it away types. -
German kitchen brands - Nobilia, Bauformat or Leicht?
Indy replied to Indy's topic in Kitchen Units & Worktops
Yeah - nothing in materials and I don't have the exact breakdown, but adds about £500/slab in labour to achieve that finish. I wasn't aware that it existed until we saw it in a showroom in a very run down area. -
German kitchen brands - Nobilia, Bauformat or Leicht?
Indy replied to Indy's topic in Kitchen Units & Worktops
Very much the way we went with it as well, including the mitred joint and also shark nosed edge for the worktops (which adds a fair bit of labour). We did have a tambour unit (I didn't know what it was called - I just used to call it the 'shutter/roller' cabinet) but it went away in the final design when we added the larder which will have a slide out shelf to be used for things like the coffee machine, kettle, toaster etc. -
German kitchen brands - Nobilia, Bauformat or Leicht?
Indy replied to Indy's topic in Kitchen Units & Worktops
Yes, Self build so the VAT is claimable - apart from any freestanding appliances which seem to be excluded. So it looks like we'll have to pay it on the washing machine/dryer. Unless we go for integrated ones but then the cost of the surrounding cabinetry probably makes it about even anyway! Price wise - yeah, been to a few places and apart from a place that wanted to quote us £50-70k for a Hacker kitchen (same layout) - I haven't found anything cheaper. Not tried Howdens/Magnet etc as we like the German kitchen look. The reason I'm hesitating is that I think it's a little too much to pay for MDF cabinets - albeit very nice ones with top quality hinges and lights etc. We've also got a fair number of drawers, a double door larder and storage on both sides of the island, all of which didn't help the price. -
German kitchen brands - Nobilia, Bauformat or Leicht?
Indy replied to Indy's topic in Kitchen Units & Worktops
The price I've quoted above is for cabinetry alone for the kitchen and utility. Appliances are around £6500 ex VAT (need to finetune these as they've put in some really expensive ones as a default) Worktops (Quartz) - for the island, waterfall edge, splashback etc - £8700 inc VAT Kitchen/Utility fitting is around £5.2k - which is not too dissimilar from what our builder ones so we may go with the recommended fitters. To provide an idea of the space - here's a few images of the kitchen/utility space -
German kitchen brands - Nobilia, Bauformat or Leicht?
Indy replied to Indy's topic in Kitchen Units & Worktops
For those that went with local companies that made bespoke kitchens, can I check how pricey it was compared to one of the high street brands or the German options? I haven't really looked at this option even though it does sound very tempting but have it in my head that a bespoke kitchen would work a lot more expensive than an off the shelf one... -
German kitchen brands - Nobilia, Bauformat or Leicht?
Indy replied to Indy's topic in Kitchen Units & Worktops
Yes please, that'd be great. Happy to receive details via message. Re Schmidt - not yet, but it's on the list before we finalise. There's one not too far in Wimbledon too but we just haven't made it to them yet. -
German kitchen brands - Nobilia, Bauformat or Leicht?
Indy replied to Indy's topic in Kitchen Units & Worktops
Looks like they sell the Nobilia range. Have you used them personally and any feedback to share? -
German kitchen brands - Nobilia, Bauformat or Leicht?
Indy replied to Indy's topic in Kitchen Units & Worktops
I’m in the KT10 postcode area - Surrey/Elmbridge. -
German kitchen brands - Nobilia, Bauformat or Leicht?
Indy replied to Indy's topic in Kitchen Units & Worktops
We like the design as it's tailored to what we want. Several hours and visits spent with multiple companies and online planners to come up with that. Re the MDF - it's a fair shout and I do have some reservations. But we can't seem to find a handleless kitchen in the finish we want with solid wood doors. The alternative is a shaker style kitchen - which we don't want (or particularly like the look of). The sales patter from the kitchen showrooms is that laminate doors are better because they're not subject to expansion/contraction etc. What would you suggest as an alternative?