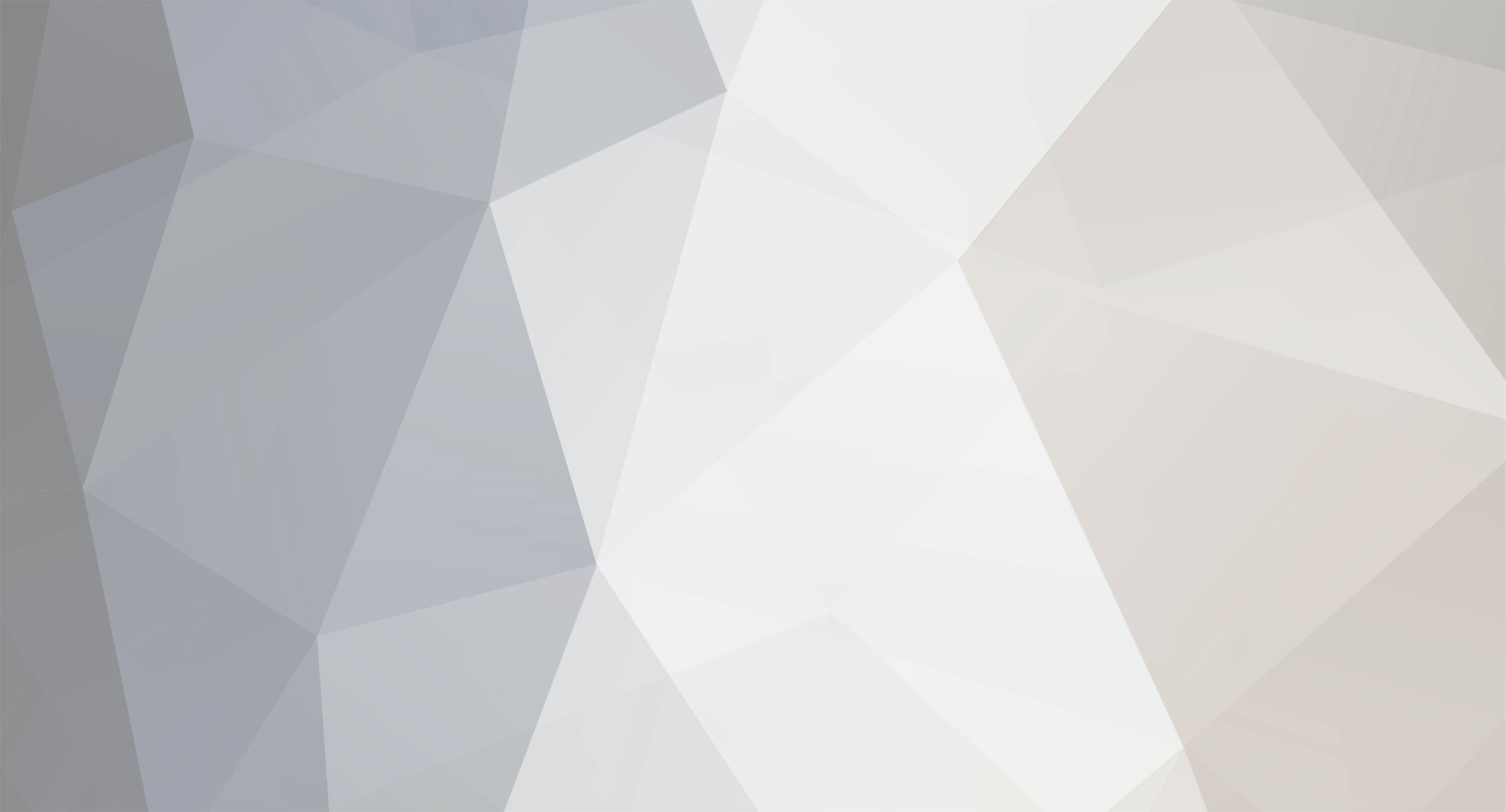
David R
Members-
Posts
25 -
Joined
-
Last visited
Everything posted by David R
-
Marks on Larch cladding when using stainless steel nails
David R replied to David R's topic in General Joinery
Iceverge I did this along with several other types of nails to see if I could get the staining happen again. The test piece got a bit busy with most of them showing some staining. I tried again today with another piece of larch now none are showing staining! Confused dot com. -
Marks on Larch cladding when using stainless steel nails
David R replied to David R's topic in General Joinery
Johnmo I have tried the magnet on some other stainless nails and they are not magnetic. You could be onto something. Timco are sending a courier to pick the nails up so they can investigate the issue. -
Marks on Larch cladding when using stainless steel nails
David R replied to David R's topic in General Joinery
Thanks for the quick replies folks. The nails are slightly magnetic, when tested with a powerful magnet, from a good bit of googling I understand that this could be possible. Working 300 series stainless can make it slightly magnetic. I am trying to eliminate the gun as the cause, it could be fragments or nozzle marks. I have deeply scratched a test piece of timber with the nozzle and fired other nail types to see it they will mark, still no signs of marking. The stainless steel nails in the test piece have a distinctive tear stain forming, the galvinised nails are showing no marks yet. ( I will upload a photo ) I will drill some holes in the test piece and see it the show any staining in the morning. I know that green larch has a quite high acetic acid content this and a combination of steel fragments, could be the culprit. Surly I cant be the only person to have come across this issue. -
Hi Folks, Can anyone help me shed some light on why these marks have appeared on my larch cladding? The marks appeared within a couple of hours, the larch is green and it was raining. The nails are Firmahold 2.8 x 63 stainless collated being fired from a Dewalt 18V nail gun. I might understand if the nails were galvinised, but for the marks to appear so quickly is worrying. Where the timber I used was a not damp from the rain there are no marks. Thanks in advance.
-
I had looked at the Grant oil / ASHPs and think it is good that the industry recognises that there is a need for them. We have a Grant oil boiler and it has performed really well, if a bit noisy. The idea of fitting an oil boiler outside is appealing. The next step will be getting my head around controlling both the ASHP and oil boiler to get seamless uplift. Could you recommend a thermal store / controls ?
-
Thanks Nick your thoughts are appreciated, most of the insulation is in already. Taking it back out and cutting boards to fit between the joists, is going to be too much work. Our intention is to use Vinyl flooring. I worry that an overlay system would be able to achieve a flat enough surface, plus the time / cost of fitting it. I take on board what you say about insulation it makes sense. I have been taking care and foaming gaps in the insulation between the joists and could fit rockwool insulation underneath to help with draught-proofing Reading a few educating posts on here on "thermal mass" and don't think I will use that term ever again! If I could start again, I would have of used block and beam construction, with insulation and concrete slab on my sloping site, plus educated myself far more on correct floor build up. I like the idea of a hybrid system. My Ex ships engineer neighbour has a similar stone built property, he has a back boiler in his wood burner, ASHP, PV, Oil and solar thermal, I need to keep up a bit. AliG, Thanks, I have been a bit of a numpty in understanding the PA ratio, it is not "1" it is .35 as I included the internal wall as you alluded to. It is double glazing with a triple glazed roof window. I do not have 80 / 90 mm build up for tiles, this would have been a good solution.
-
AliG, you comments are really appreciated. they are helping me get my head round the UFH. The floor has 165mm Celotex well fitted between the joists, I am doing it right now, what a pig of a job to do! It would have to be 22mm boards or 20mm insulation as I do not have the build up space for both. I prefer the boards as it would give a more solid floor. The U-Value is around 0.15 or better, with a PA of 1 and according to the architect plans it is 0.15. There is about 50% glass in the extension. The reason for wanting to keep the oil boiler and fit an ASHP is that the older part of the house, which we are living in, could be upgraded with larger radiators etc at a future date, plus the older part is not so well insulated. Also, I do not want to fit an ASHP to find out that my electricity are unmanageable or that it cant cope. I am also fitting a wood burning stove in a lounge area of the old part of the house and perhaps another one in the extension once it has all been signed off. The is in an exposed sight, the winters can be a bit harsh. Any input is appreciated.
-
Thanks for your responses. Scoobyrex, Thanks, I have spoken to a closer located screed company and they have a similar product to Speedflo and say that screeding on top of boards is not an issue, they said the membrane / tanking system used (plastic sheet ) acts as a slip layer plus the screed would flex. They are sending a rep round next week to have a look at the job. Temp, Thanks, there will be 165mm of insulation between the joists, ( my badly worded initial question ) now you have me worried about thermal bridging and should not fit the boards, but fit a layer of 20mm insulation on top of the joists. I like the system you used, it would save lifting boards in a retro fit.
-
The joists are on 3400mm span. would there be any flex or do you always get flex in a wooden floor no matter how rigid? My architect has not done this before as far as I can tell. I will look into decoupling mats, I have never heard of them.
-
Hi Folks, I have a question regarding placing underfloor heating pipes on top of 22mm chipboard flooring. I am building an extension, the original design was to place heat dispersion plates between the 195mm x 50mm joists at 400mm on top of 165mm insulation. We have decided to place pipes in a 50mm pumped screed on top of the joists / chipboard flooring in order to make use of the thermal mass. the extension is around 70 Sqm. Our engineer says the weight is not an issue and we have allowed for the height difference of the screed, by building the block work lower. Does anyone know of any issues with placing the UFH pipes on top of chipboard? Second question, the UFH will be heated with an oil boiler and ASHP. The room will be a living room, kitchen, dinning room open plan. Would it be beneficial to have 2 heating loops as opposed to one? Thanks in advance
-
ETC. Thank you, tile vents are a good idea, plus a 150mm up stand. The person who put the rafters in ignored the fact that it needed venting. The roof will be getting stripped and a dry ridge system fitted as well. The original roof is a bit rough, loads of birds nests under the tiles, ancient fiber board under the felt and rotting battens. I intend pushing the boat out by using Aultrix 600 vapour barrier. I will be very glad when I have got this build water tight.
-
Mr Punter thanks for the quick reply. You are correct the insulation ideally would be going on top of the rafters. The design is for a cold roof with the insulation between the rafters. The roof was to be a walk on roof, but plans changed. I could change the roof to a warm roof come to think of it. What I am trying to get my head round is, how do I refit the gutter and vent the cold roof or do I not fit the gutter and allow the existing roof to drain on to the flat roof? Answering my own question, if it was a warm roof with the insulation on top it would not need venting. Good man, I should have asked you earlier, I was loosing sleep over this.
-
Hi Folks, I have an issue with abutment detail on my cold flat roof where it meets the existing sloping roof. There is not enough height on the wall to allow for a 150 mm upstand. The height above the new flat roof joists to the existing roof tiles is only 120mm max. With 18mm for my OSB and 80mm for firring, it does not leave anything to pay with. Has anyone encountered this issue before? I cant drop the joist height as the ceiling is low enough all ready. There is an issue with ventilation as I need to vent the cold roof where the roofs meet. Would it be possible to re profile the existing roof some how, big firring strips? The truth is I am at a loss how to proceed. Thanks in advance any ideas would be appreciated.
-
Gus Potter. Gus, Many thanks for your detailed explanation and drawings. I now have a far deeper understanding of the straps intentions and will ask my SE about the impact of timber shrinkage. They have allowed 12 mm for joist shrinkage in height above the steel but nothing for shrinkage horizontally. Apologies for not putting sufficient detail in my original post. Unfortunately, the steel is in place on site, with most of the kit in place. I know what you are saying about joiners being aware of nailing too close to joist edges, the speed of construction on my kit did not allow for a lot of thought time. The joiner missed the straps out but luckily we can retrofit most of them, apart from under one panel on the gable. We had the opportunity to rebuild the panel, and fit the straps, as the joiner built it not on the steel beam but on top of the floor joists. He said that the steel was in the wrong place not his panel and the joists hangers would support the panel and my roof. The kindest thing that was said was by my architect "what an incredible lack of common sense". Not my words when the brickie pointed it out. His company are billing themselves as timber frame specialist, go figure.
-
SimonD, Mrpunter Thanks for the replies. I had a talk to my architect and he explained it was due to the SE having to issuer the SER certificate and their liability insurance having to cover potential structural issues. He also said that this particular detail is not unusual. He did comment on the change over the last few years from timber beams to over sized steel beams.
-
Mr Punter Thanks for the comment. I would have thought the same. Why the extra restraints? I have the spit gun. There are about 100 joists if you include the balcony which they need restraint straps on as well. It is a bit tricky, firing a strap to a web of an rsj then fitting 2 packer battens then hoping the joist is in the right place. A bit of forethought is requires. The dwangs on the the flat roof will need notched for ventilation as the strapping is required over 3 joists as the joists don't run the right way, then does the flooring sit well on the straps? Plus the furring strips for the flat roof will need rebated to sit over the straps ( perhaps ). all a bit of a head ache. I wish I just could understand the science behind it. Wind loading? BS standards? The spec for the joist hangers is SAE, I don't understand that either when jiffy hangers are the norm, I could even shot fire them to the steel. Why do engineers go so far over the top and don't give a hoot about the practicalities?
-
Hi Folks, Has anyone ever had to use restraint ties to tie in first floor joists to the steel frame? or any part of a steel portal frame. My design plans show that every joist should have a 600 mm 2.5 mm x 30 mm strap each end of the joist , shot fired into the steel rsj's / beams of the frame? I know that this is the engineers detail and should be carried out. However, the engineering spec so far, is very cautious, to say the least. Has anyone used steel portal frame construction and had similar level of detail? Thanks in advance.
-
I think we have found a steel fabricator that is a decent fit for the project, pragmatic and practical. He builds lots of agricultural buildings and says farmers are always changing their minds last minute. So any on site issues would not be a problem to sort on site. He is willing to help as much as possible with levels. He will produce a cad drawing for us as soon as we give him our assumed sizes. From this we will get a better idea of the steel layout. We have been working through the drawings and have found errors in both the SE drawings and architecture plans. Incorrect joiting detail, wrong build up of ceiling / cold roof, that would make the terrace higher than the inside room, wrong type of under floor heating ( no screed / thermal mass, just spreader plates ) feel a bit foolish for not noticing earlier. I am very glad that we have caught the mistakes now as later on would be very expensive. Makes me wonder how contractors get on after being handed plans that are wrong and don't spot the errors at kick off. Being made to go through the pain barrier of measuring all build ups and steel structure has led to a better understanding of the build.
-
MarcC and Russel. I have been thinking along these lines myself. It is starting to make more sense, I could splice the posts. this would allow an as and when needed approach. It would also mean easier handling and install. Bit more expensive on splices but off set against getting it wrong big time. Interestingly, the last fabricator said he did not work "hot" on site. Any alterations would mean the crane coming back in and taking the section back to the workshop. This in itself ruled him out, as it would be better to get it wrong with a fabricator with a quote coming in at half the price, who was willing to work on site. The_r_sole, I will try to get some drawings uploaded, when I can edit the engineers and architects details off the pdfs.
-
SuperJohnG I have full structural engineers drawings approved with building warrant. What I lack is the heights, but I will calculate this from the plans. I just need to go through the pain barrier of doing so. My biggest issue is conceptualizing the entire steel frame from the plans. I thought I could pay someone to do this, but it appears that this is not the case nobody wants to be liable for getting it wrong and then having to sort it. I am unsure how wrong it could go, as long as the build is below roof height of the existing build, even then I doubt a wee bit over would bother building control. This is not quite true but true enough to put a main contractor off if he had work elsewhere. At this point I am not looking for a main contractor, not at the prices I have been quoted so far. The surveyor, architect and engineer have all seen the founds pre pour, probably worth nothing to a main contractor. The wall is as straight as they come, but being 100 years plus old will always throw up issues. as for the ridge height I think I can measure down through an attic hatch. to the ground floor and work from there. When I got the surveyor in originally I wanted measurements to cross reference with the steel fabricator not to give to them and say build this. Any how, I have one more fabricator to come back to me and one that has quoted coming to inspect the job on Monday. Yesterday the steel fabricator inspecting the site wanted to build the entire frame in the field then crane it into place on to the studs and into the one wall pocket, more days on site I guess. Has anyone heard of this being done?
-
Today was a game of mixed results The steel fabricator came to site, expressed his opinion about the architect. He told me that he was certified under the regulations and that the bloke round the corner was not and his steel would be " illegal" and if I used his steel and had a fire my insurance company if they found out would not pay out! Up until this point he was talking a lot of sense and pointing out which levels I would need to give him. Has anyone heard of the need to use an accredited steel manufacturer, can my steel structure be illegal? He did send me a quote which was 3 times the bloke round the the corner's quote. If it had been double I would have accepted as he seemed like he knew what he was doing but still no commitment to sizes. That would be my job! TOC top of concrete, ( my surveyor did this ) TOS top of steel and the height of the house. Does anyone know how to measure to the the ridge of your house? The builder I thought who would do the block work, steel and joinery, had to be pushed and asked to "close the loop" said the job was not of interest. Reading between the lines he could not measure the steel either! I have another steel person coming on Monday his quote is twice the bloke round the corner, fingers crossed. The good thing about talking to lots of tradesmen and getting quotes is that it informs you more and more about the process of the build.
-
Hi Folks, So many replies, thank you everyone for your advice. I do have full building warrant, engineers drawings and architects drawings, plus the services of a surveyor with a total station. I ended up pouring the founds myself as the crew left a la del boy chandelier cleaning style. I will leave that story for now. Everyone is correct Eiffel and Brunel had square shoulders and knew a bit about jiggery pokery. I feel that if we give a contractor enough work on the job they can facture in some error into the price. If a main contractor was doing the entire job there would be no issue as he would have enough lee way in the price if a beam or post needed re done on site. I have not employed any consultants for the construction phase, I was not aware that this service existed. The steel structure is straight forward enough the rear wall of the house is super straight having been rendered a couple of times, the surveyor confirmed this. There is no steel going inside walls and we have determined floor levels. We have a structural engineer coming at 11.00 to give me build and install quote, he seems plain talking and sensible. I will report back as to his comments. It was a wild night last night, I have not seen or heard an electrical storm like that since southern Spain. The founds are full of water so I will have to go turn the pumps on, once again!
-
Hi, Thanks for the quick responses. I am just out side Dunfermline, you are correct nobody wants to take any responsibility. I am in the process of trying to get a builder to give me a quote for the masonary work and the first fix as well as installing the steel. It may well be the only way ahead. From speaking to another steel fabricator today, they seem to think that working with a contractor to give them at least some definitive sizes is the way ahead. They are coming to site tomorrow. so I will find out what are the definitive sizes they need. I do not feel experience enough to define to the millimeter where the steel stops and the timber starts. It seems very strange that I can not find an expert to pay to do the steel drawings. The extension is 11m x 6m, open plan living room and dining room, so will require some quite large beams. Second floor has a pitched roof with steel forming the apex. The surveyor has defined where the brick line and steels should be. He did initially say he was going to size the steel but shied away in the end. This was important as it Is a sloping site with steps down through the 50cm stone wall from the old part of the house to the new extension. Mr Punter, I have had the survey carried out, now I have a surveyor, engineer and architect who will not supply me with a steel drawing. There is no point in asking any of them in any manner whether they can help any further on this issue. Yes, the steel fabricator is supply and install, the one I am keen to use as he is only along the road, everyone in the area seems to use him but he only works from supplied drawings.
-
Hi Folks, I am attempting to have steel fabricated and installed for my two level house extension and I am running into problems with measuring the steel structure. The engineer and architect have point blank refused to provide steel dimensions ( lengths and heights ) for my extension. They along with the fabricators have said that it is the main contractors responsibility to provide these dimensions. As this will be a self build, the responsibility is mine to provide dimensions for the fabricator. I do not feel confident about providing the sizes. We have poured the foundations and had a surveyor mark out the points for installation of the beams and blockwork. But nobody I have spoken to are willing to provide the service of structural steel measurement. Can anyone point me in the right direction of someone who has the ability to measure up my steelwork, of should I take a stab at it myself? Getting a bit tired of looking at the flooded strip foundations. Thanks in advance "any" advice on this would be appreciated. David
-
Hi Folks, We are at the start of what hopefully will be our last renovation , I know never say never . We purchased a very run down small holding in the Kingdom of Fife, it has a stone built farm house plus attached and detached outbuildings. We have renovated much of the farm house inside and are at present putting on a large extension. It has been very painful trying to get out of the ground with the extension, but I will post my tales of woe in the correct part of the site. I hope to be able to share some advice and experience as well as get some advice from fellow site members. Best David