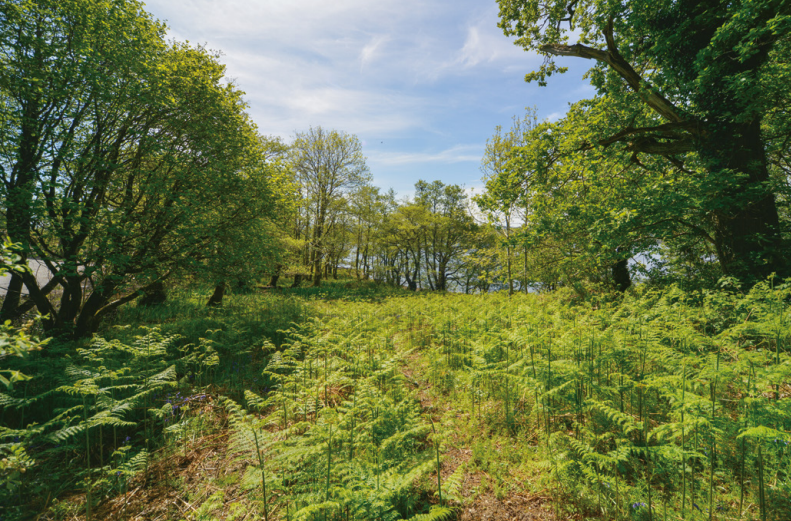
mattp22
Members-
Posts
29 -
Joined
-
Last visited
Personal Information
-
Location
Oban
Recent Profile Visitors
The recent visitors block is disabled and is not being shown to other users.
mattp22's Achievements

Member (3/5)
8
Reputation
-
barn conversion. SIPs or stick build ?
mattp22 replied to mattp22's topic in Structural Insulated Panels (SIPs)
thanks for the comments. I'll do some homework re: warranty required on conversions. and the visible stone reveals looks great. cheers -
Hi, I'm trying to wrap my head around a barn conversion I want to start soon. Stone barn in Scotland, very thick stone walls- structurally ok. Slate roof/ timbers well past their best and i need to raise ridge height for first floor head room, so existing roof & trusses are coming off regardless. I have full PP. To convert i saw 3 routes- a) drop a SIP kit inside. fast, slim and thermally efficient, but tricky to get 100% correct with existing window openings etc, and adjustment on site is not really possible i believe. circa £60k exc. assembly, but includes most internal walls too. b) ICF- thermally efficient again, reasonable fast, prices quite high and that's excluding a roof. easier to tweak on site to fit existing walls & openings. circa £68k exc. roof, 1st floor joisting & internal walls. c) stick built on site with local joiners. takes a longer time, but easy to work with existing structure. Including insulation and trusses significantly cheaper than a or b. So option c) seemed easier, but now I'm reading that stick built would perhaps prevent me getting a 10 year warranty and/or straight forward mortgages? There is a good chance I'll sell within 5 years. The ease and speed of using SIPs is very appealing, but i suspect these benfits will go out the window if i have to adjust the panels on site. Are there other viable build options I've missed? Is adjusting SIPs even possible? I specifically asked the SIP company to give me oversized (too wide & too high) openings for windows & doors so I can bring them in on site with stud work to suit existing openings, but maybe I'm just opening a can of worms. Thanks!
-
Hi, I'm trying to wrap my head around a barn conversion I want to start soon. Stone barn in Scotland, very thick stone walls- structurally ok. Slate roof/ timbers well past their best and i need to raise ridge height for first floor head room, so existing roof & trusses are coming off regardless. I have full PP. To convert i saw 3 routes- a) drop a SIP kit inside. fast, slim and thermally efficient, but tricky to get 100% correct with existing window openings etc, and adjustment on site is not really possible i believe. circa £60k exc. assembly, but includes most internal walls too. b) ICF- thermally efficient again, reasonable fast, prices quite high and that's excluding a roof. easier to tweak on site to fit existing walls & openings. circa £68k exc. roof and 1st floor joisting & internal walls. c) stick built on site with local joiners. takes a longer time, but easy to work with existing structure. Including insulation and trusses significantly cheaper than a or b. So option c) seemed a no brainer, but now I'm reading that stick built would perhaps prevent me getting a 10 year warranty and/or straight forward mortgages? There is a good chance I'll sell within 5 years. Are there other viable build options I've missed? Or is the stick built/ warranty issue not really a problem? Thanks!
-
Hi Everyone, any recommendations for a piling foundation contractor for a site near Oban? Thanks
-
Connecting-up my empty meter box…
mattp22 replied to Dreadnaught's topic in Consumer Units, RCDs, MCBOs
Thanks for clarifying, much appreciated -
Connecting-up my empty meter box…
mattp22 replied to Dreadnaught's topic in Consumer Units, RCDs, MCBOs
Hi, about 20 metres -
Connecting-up my empty meter box…
mattp22 replied to Dreadnaught's topic in Consumer Units, RCDs, MCBOs
Hi, just jumping on the band wagon here. I also have exactly same scenario with meter box at edge of my plot but with 100amp fuse in cut-out, no meter (yet) Did anyone have any luck working out size/guage of cable to run from cut-out into house? I'm glad this is an accepted method rather than having to move the whole fuse into new house when it's finished. Thanks -
lol, i hadnt realised- i am speaking with SipsEco just now. Sorry for typo. Seems EcoSips are based 20 minutes away from them- confusing! Must be a story there... I've got Kore at about 60% of Isoquick cost but excluding installation. I will be remote managing so thought supply & fit might be less of a headache.
-
I'll check out Ecology again but i couldnt find any standard % rates on their site, presumably because they don't deal with standard builds, but any more than 0.75% points more on mortgage would push the numbers in masonry's favour for me. Bonkers in 2020, but that's mortgage lenders for you. For what its worth i've been advised renderboard over the SIPs would satisfy many high street lenders and therefore get you the lower interest rates. SIPECO is the way I am going too, with Isoquick slab (i think). Isoquick were £6-8k depending upon insulation level but that's for SIP/timber only build. I hadnt realised adding masonry would bump the cost up so much so i might revisit Kore and ask my ground works crew to install to lower costs (although they have not done an insulated slab before, so that should be fun!) Good to know that ECOSIPS are getting their BBA cert so soon- they just told me it was in progress. That's cool you're pulling the trigger in 2 weeks, when are you hoping to start founds and SIPs? Are ECOSIPS doing SIP install too?
-
SIP is 169mm, 0.2 w/M2. I understand with blockwork and cavity this will drop to around 0.16 w/M2. We were going to increase panel thickness/ insulation anyway which added £2k to SIP cost, but no need now that we're adding blockwork- so the £2k can be taken off blockwork cost i guess. good point about protection in a storm, it's not like we're 10 metres from the Atlantic, oh.. no.. wait minute...
-
not sure i've got an option unfortunately if comments from lenders are to believed. i've not costed for the blockwork accurately yet but have estimated £6k inc. labour for 160 sq mtrs (based on several online calculators). In terms of mortgage savings- around 2% rate from highstreet lender should be possible given location, non-trad construction and loan to value. Specialist lender who would accept SIP + cladding with no masonry would be 3% if lucky but closer to 4% in reality, and construction type would deter re-sale if i ever had to move. Over 5 years that would cost me an extra £8k @ 3% or £16k @ 4% in repayments so makes sense to go for blockwork now even if it is hugely frustrating and unnecessary. Broker i've used for several mortgages and she has really done a lot of leg work on this construction method for me.
-
i think with rendered block outer skin you should be fine with highstreet lender and thus lower % rate. My mortgage broker has spoken to about 20 lenders and it seems with masonry element then about half are happy with SIP construction. Timber cladding on masonry reduces pool further though but that's the look we want (and Planners!) Last time i spoke to Protek they wanted £5k for my warranty but that was without masonry element, timber only construction. Hopefully they'll reduce it a bit now. Was your SIP kit BBA approved if you don't mind me asking? I am probably using a company in Fife for kit but they are not BBA approved (yet) and i'm a bit wary of consequences.