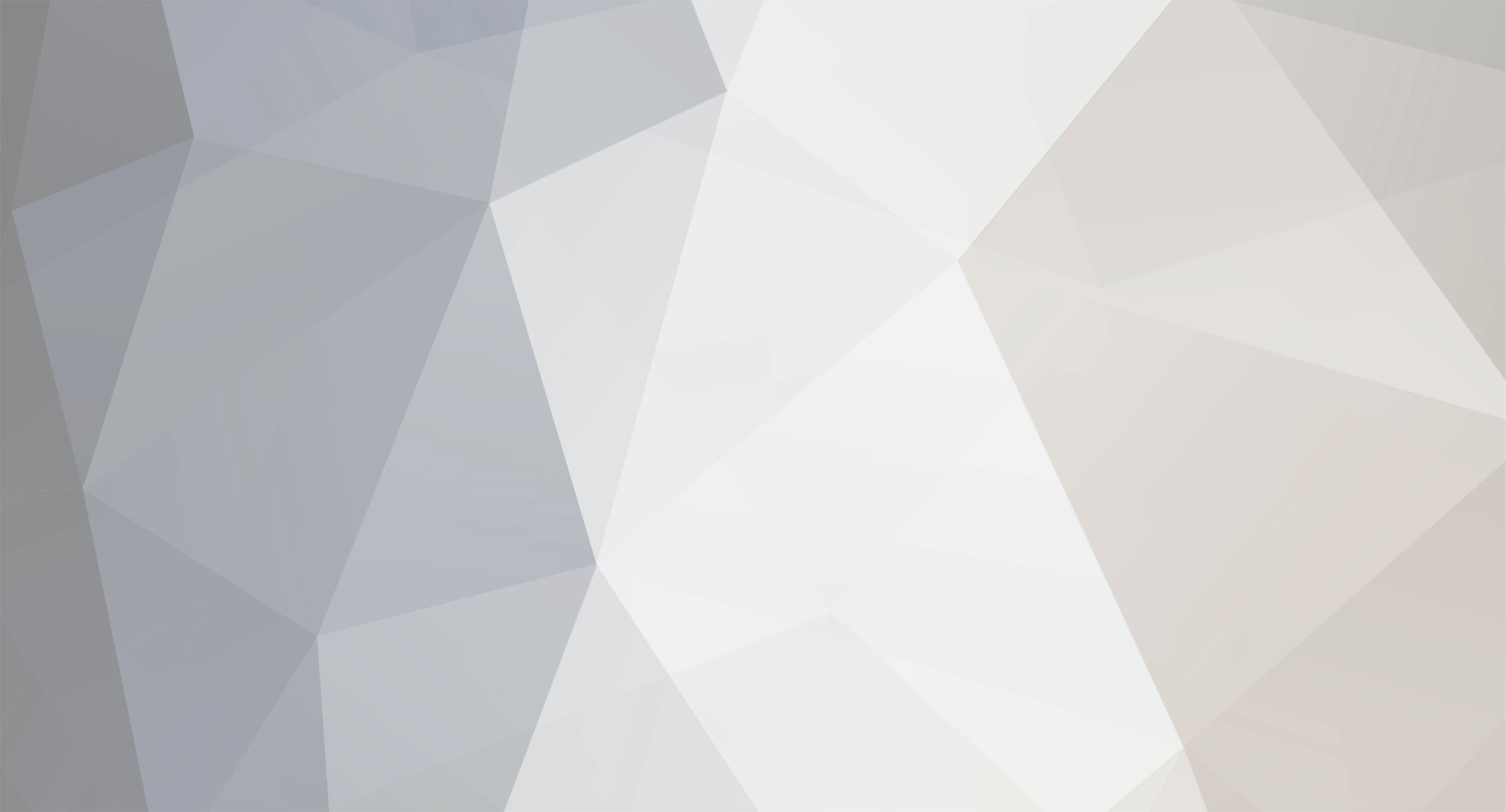
DInwood
Members-
Posts
26 -
Joined
-
Last visited
Personal Information
-
Location
N Devon
Recent Profile Visitors
The recent visitors block is disabled and is not being shown to other users.
DInwood's Achievements

Member (3/5)
1
Reputation
-
I was vaguely aware of this issue but chose to ignore it in my modelling. Perhaps I should look again. The Zehnder MVHR reports humidity as well as temperatures of the various airflows and Home Assistant logs 4 weeks of data. Looking at this I see a relative constant ~85% outside RH & 55% inside (measured at the extracted airflow, so from the humid areas). Here's the last 4 weeks daily averages for interest: We too always blade after showering.
-
Thank you all for reading my post and your thoughtful responses. It seems that nobody in this thread has tried do do this (predict daily heat requirements), but also nobody else is so dissapointed with their heating either. The scientific part of me is hurting because I really feel this is capable of being modelled and I can't yet see where I'm going wrong. Thanks to your comments I've gone back over my spreadsheet (which has data from before the heating started up and for a winter week it was off). I find that if I use a higher rate of heat loss (say 120W/C) then to account for the periods the heating was off, no realistic amount of internal heat sources would account for the house temperature. Conversely if I crank up my estimate of internal heating then the excess of Ecodan caimed heat output over predicted gets even worse. FYI I'm not ready to give up yet. Thanks also for the references which I shall now go away and study in more detail. In parallel I will continue with the efforts to increase the CoP. The MCS certificate used an sCoP of 4.1 - a long way from what I'm getting.
-
Thanks JohnMo. You are concentrating on the CoP side of my puzzle. That's fine - but are you saying I really should be achieving over 4 as measured by the Ecodan? If so, the installer needs re-educating as he thinks the current figures are realistic! I allow the DHW separately in my analysis. It is heated by ASHP with ASHP connected cylinder thermostat, there is an immersion but its never been needed as the ASHP gets the tank up tto 51C in about 45 mins.
-
No apologies needed. In all humility I'm looking to gain from the wisdom of more experienced people. So your feeling is that I'm underestimating fabric losses. Any idea how I could estimate what to allow for? I've tried some arithmetic modelling (eg looking at day-to-day variability and looking at empty periods) and if I increase the 88W/C by much then I couldn't make sense of the numbers (eg predicted negative heating days in winter). I fully accept I'm making some mistakes & I'll go back to my modelling to explore again. I'm very embarassed that I'm the only person who has tried doing this!
-
You are right, the MCS pack doesn't explicitly allow for internal heat sources. It does estimate annual demand & the document I've got doesn't say how this is calculated. It isn't hard to work out how it's done though & I'm certain they use "heating degree days" times their estimated heat loss per degree. I'm trying to emulate this "heating degree days" method by using actual outside temperature & estimated internal heat sources. I was hoping others had tried this also and had some experience to share or correct my efforts.
-
The MCS pack i was given was also wrong but only in its ventilation loss calcs. Indeed this gets at exactly what I'm trying to understand. I accept I might be wrong and am very open to ideas as to why. If I'm underestimating expected energy demand, what am I doing wrong? Is it my method of estimating other sources of heat? My method was pretty good at predicting when the heating would be needed. Is it ventilation load? Wind effects?
-
Thanks IanR. I'm puzzled why your average u-value is so high - have you got acres of glazing? My figure of 0.23 is the average weighted by area for each element and feels about right. Plus, as I said, my spreadsheet gives a very similar result to the MCS pack for the fabric losses. I'd be very interested to know what your actual heating energy input & outputs are. It could be I'm underestimating ventilation losses, but even if I double these it only adds 5% to the rate loss (ie I get to 94W/C), not enough to account for the discrepancy.