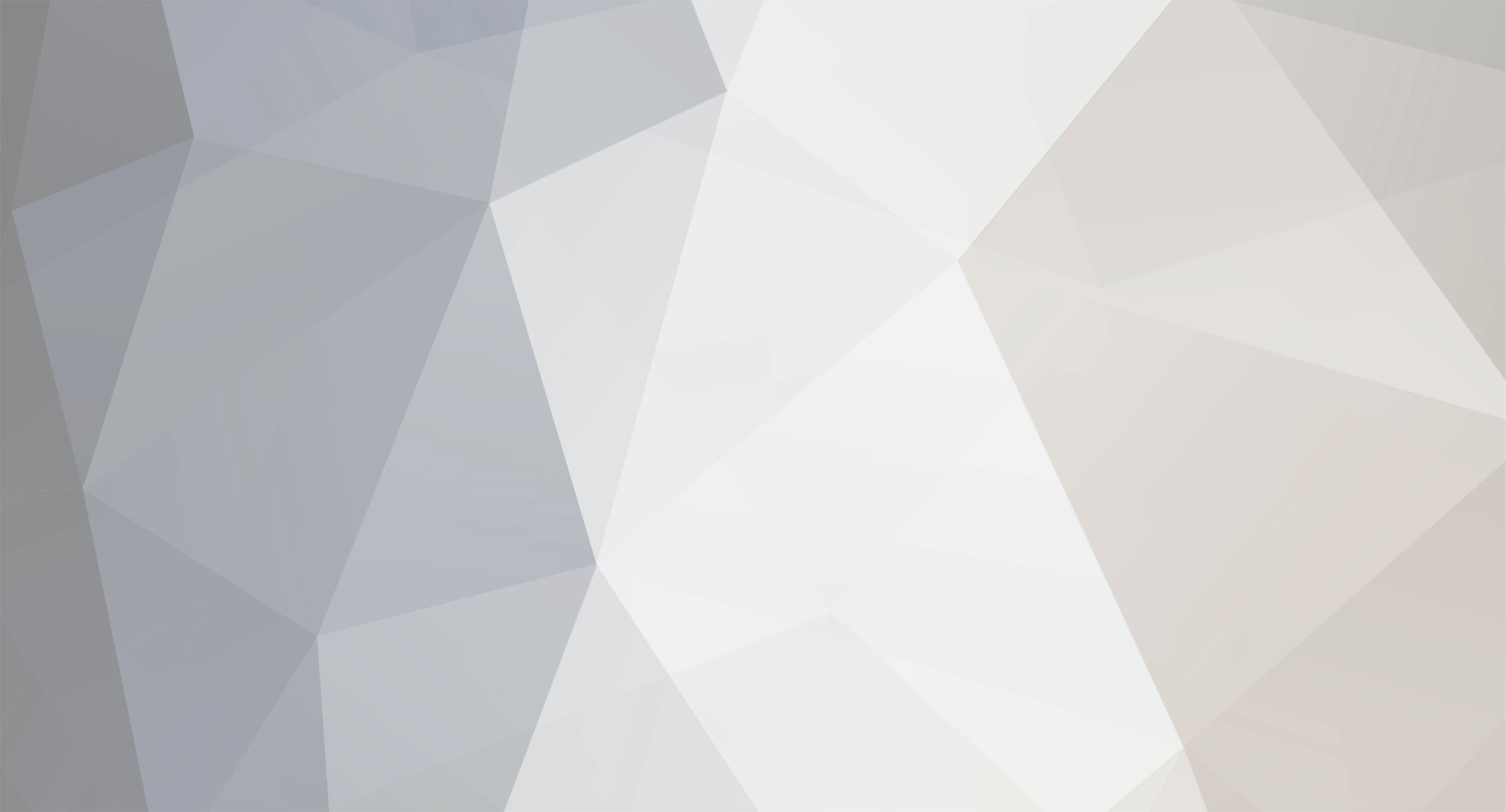
gc86
Members-
Posts
10 -
Joined
-
Last visited
Recent Profile Visitors
The recent visitors block is disabled and is not being shown to other users.
gc86's Achievements

Member (3/5)
1
Reputation
-
How much (as a percentage of the original costings) of material price fluctuations or increases, should a builder or contractor be normally expected to absorb as part of fixed price contractual works?
-
Thanks Mark, another question would be where to mount a small CU - inside the surface meter box, leaving as much space as possible for the meter and cut out - or mount it externally adjacent, and take the meter tails out to it?
-
Looking for some advice as the most efficient and cost effective way to provide temporary site electricity. (Scotland) I've already put up a timber board on 2 fence posts, roughly 1m wide, and mounted a surface meter box to the left side, leaving around the same space to the right for sockets etc. Duct has been run in and I have a hockey stick to the meter box. I'm now awaiting SSE to run in and connect the cable, and then meter install, but want to prepare the consumer side in advance. I'm looking to provide at least 2x 16A ccts with a 230v 16A commando/industrial socket on each. I think this should be enough for the builders requirements. I've seen some people using a second meter box as an enclosure for it all, but I just imagine the contractors leaving the door flapping about. Also, I've saw a photo of meter tails coming out of the meter box and directly into a IP rated consumer unit. Can meter tails be run outside the meter box, without conduit? Straight into a garage CU with a 32mm stuffing gland presumably to maintain IP? (short distance, less than 1m outside the meter box) I've also saw these RCD caravan hookup units, which look nice and compact with preinstalled 16A sockets - but can one of these act in place of a dedicated consumer unit? Can meter tails be installed directly into one of these? If so, maybe this would be the simplest option? Meter tails out the bottom of the meter box (hopefully they provide an isolator?) and into the bottom of the hookup? Any help appreciated
-
Cheers everyone. Should really start one of the blog pages and update the progress..
-
I just took my second drawdown with Ecology. Easy... 1. At any point during your build you can instruct a valuation. (small fee to pay). Ecology will get a surveyor to value the site in its current state and also a projected final value. 2. Within a few days, Ecology then tell you what your updated maximum drawdown/retention release is. 3. At any point after that, you fill out a form where you can request anything up to your max drawdown. 1 or 2 days later it's in your bank account. You can drawdown more than once for each valuation, you don't have to take the max amount.. Take as much as you need, when you want, up to the max amount based on the latest valuation.
-
Hi Gus Yea the kit is all wrapped up in DPM type material, stacked flat and lifted off the ground with batons. The bottom is open to let the air through. So not too concerned about it sitting. Did have a fall out with builder tbh, as I felt the part payment he wanted, added to the previous stage payments, was too high for what I currently have on site. Difficult, both sides have their own viewpoint. Anyway managed to come to agreement, just got to try and get to the end of it now. Construction has avoided suspension in Scotland today so hopefully they can proceed to get the kit up and weather tight.
-
Thanks, I do get the reasoning, although I thought it may have added something to the value, even if it was a low percentage of the expense. Just wondered if others had encountered the same. We have a contract with a main contractor which has set payment stages. They want a very high percentage of the wind and watertight stage payment paid in advance of stage completion, because of exceptional circumstances (covid) meaning they can't make progress as quick as they'd like to, and thus cant wait till stage is finished for the invoice. There is a clause of sorts for this in the contract of course, but no means of how to decide what the amount should be. A tricky situation, they have bills to pay for materials which I understand, but also I don't all materials on site, ie rest of kit, windows etc, nor has anything been constructed. Luckily we haven't drawn down as much as we needed to at the foundation stage so we can fund most of their bill, however I was under the impression that having the kit all prefab on site would have helped us out with by allowing a larger release, but seems this is not the case. Builder in the end has agreed to reduce bill down to what we can draw down, which wasn't too far away from what he required. But it could have been much worse depending on circumstances. Something others should be aware of if they have a similar turn key build contract. Another issue from the covid nightmare. Not a great time to be building a home.
-
We have our prefabricated timber frame sitting on site, but after a quick phone enquiry to our surveyor, he tells me that this adds no additional value, until it is erected. And it would be the same principle for any other materials delivered to site. Is this a common position for surveyors?
-
Could anyone advise in their experience, the % of the projected finished value, which was reached at each stage? Ideally based on a timber frame/closed panel build. Foundations completed Wind and Watertight First fix Second fix Completion I'm trying to estimate cashflow through our self build, but I only have builders cost at each stage and the final valuation from the mortgage surveyor. Obviously there will be some variations of work done at each stage between projects, but even a rough idea would help greatly. Think this would also be very helpful for prospective self builders.
-
I've been keen on Loxone for our upcoming build for years, following them since around 2014 when it was much more 'open'. I recently got an eye watering quote from a local installer and I've decided not to bother. After reviewing a lot of products, I'm now looking at Lutron RA2 Select for lighting, possibly blinds. My thinking is that this will have much lower initial cost and I could potentially add a basic Control4 setup for AV, cinema room and more advanced logic control on lighting etc at a later date when funds allow. Control4 can talk to and function Lutron systems amongst many others. The Lutron system is radio controlled, and can work with traditional wiring. The switches are battery powered (which I initially was trying to avoid) but have a 10 year battery life which is more than acceptable. From what I've read, Lutron products are very high quality and reliable. One benefit I see from going this way, is it can be gradually scaled up. Even the lighting could be wired normally and gradually added to the Lutron system. The Lutron app is used to add lighting circuits etc and looks easy to use. The Loxone approach with proprietary Tree wiring needs a larger minimum cost to begin (albeit, it is a much more powerful system). I'd also be interested in any alternatives people have used, or any feedback on the Lutron or also Control4. Ps, this is my first post so hello, I'll add some plans for our build in the introduction section