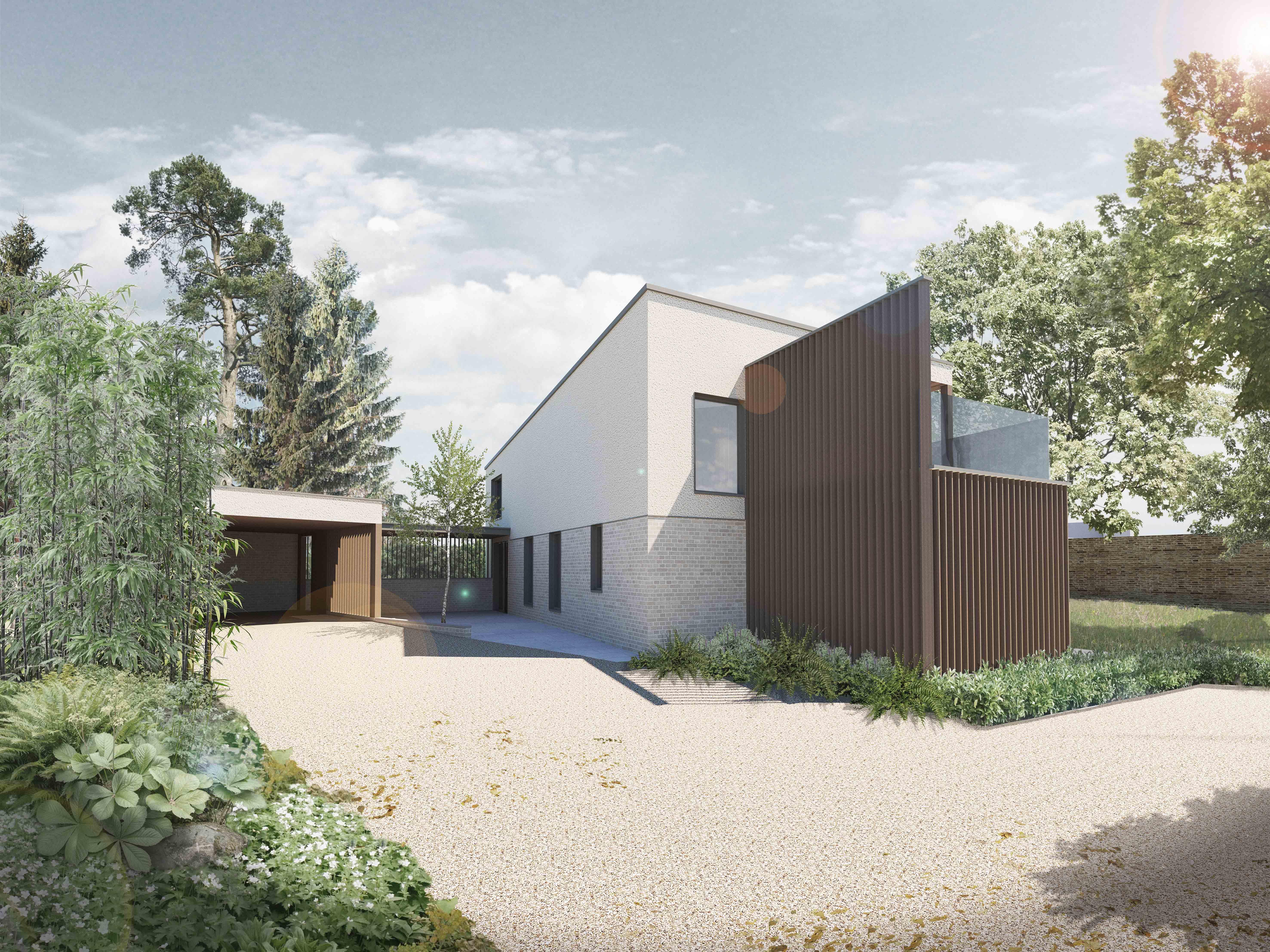
Mulberry View
Members-
Posts
711 -
Joined
-
Last visited
Mulberry View's Achievements

Regular Member (4/5)
117
Reputation
-
I would love to have the intelligence to be able to turn that into something practical, but I don't know where to start. LOL.
-
Thanks for the reply @Nick Laslett. Our ceilings are a minimum of 2.5m throughout, but the whole Kitchen/Dining/Living room is under a 5° sloped ceiling that rises from 2.5m to about 3.3m, they are already quite generous. My current levels are to provide a completely flush threshold to our Dining Room door. But overall, you appear to be saying that the PIR route is minimally more expensive and so, in your opinion the better route?
-
That's my thought. The money saving would be lovely, but I'd like to try to offset the poor performance of the Beam & Block floor as much as possible.
-
We have a Nudura build with Beam & Block floor. The B&B is now installed and grouted, we did all the work and the resulting floor is pretty level/flat. I think the finish is good enough that we can examine/rectify any imperfections. Sand blind or not? I intend to see what the floor is like once we've had a day or tidying it up, but I'm certain its better than usual building site standard. Our internal walls are built from medium-dense concrete blocks on 100mm thick Marmox blocks Our design showed 150mm of PIR, but we can now better this due to some changes in build. We have approx. 290mm from the top of the floor finish down to the top of the B&B. We plan on Microcement throughout, which totals 4mm, so 286mm for Insulation and screed. We intend on having UFH (yet to be designed). What's the best split of Insulation and Screed for optimal performance? Drying time isn't a huge priority, although my head is fried all our other nonsense, I'd like to make some blummin' decisions and get this all underway before the weather cools down. I expect our Glazing to be going in late October or early November, all being well. Any and all help is greatly appreciated.
-
Soakaway fill material
Mulberry View replied to newbuild upnorth's topic in Rainwater, Guttering & SuDS
Because we're founded on hard chalk. Made for great foundations, but less so for water infiltration. The bottom of this hole is like a bathtub, the soakaway was designed to potentially be half-full most of the time. -
Soakaway fill material
Mulberry View replied to newbuild upnorth's topic in Rainwater, Guttering & SuDS
Anecdotally, if anyone is feeling frustrated by the amount of work needed for a Soakaway, know that this is what we had to have for our modest (200m2) 4-Bedroom house. 96 standard sized crates in 2 layers (though these are larger crates so there are *only* 60). Just under 20,000 litres. LOL. -
Expert Witness needed...
Mulberry View replied to Mulberry View's topic in Party Wall & Property Legal Issues
The installer is adamant that everything is compliant because the material manufacturer (who has ZERO interest in the installed roof) has issued their material warranty. I have raised several queries that are strongly likely to be detrimental to the longevity of the roof but of course failure of the roof due to any installed detail will fall back to the installer, so why would the manufacturer care? It's like the perfect storm of non-acceptance. -
Expert Witness needed...
Mulberry View replied to Mulberry View's topic in Party Wall & Property Legal Issues
The installer stated early on that no expert testimony would be accepted by him as he is an expert installer and therefore his view is the end of the line. I had to remind him that this is not how the law works, but finding an Expert Witness who can top trump this guys self-righteous disposition is the challenge. There are Expert Witnesses who do not specifically specialise in Zinc roofing, I can see we won't get the full picture that we need. Then there are Zinc roofers who have all the expertise and experience, but are not classed as legal 'Expert Witness'. We have found one person who has BOTH credentials, but he and our installer are mates. -
Expert Witness needed...
Mulberry View replied to Mulberry View's topic in Party Wall & Property Legal Issues
The installer that did my roof is so deeply in the pockets of the whole industry, it's hard to find impartiality anywhere. The local rep for the manufacturer with whom I discussed the entire situation as it was unfolding lives 15 minutes from my plot and would not come to see. They literally do not get involved in the installation. They provide standard details and general guidance, but cleverly disconnect themselves from installation issues. I have raised specific queries with them and shown them photos of what I claim are defects, they refuse to get involved. -
Expert Witness needed...
Mulberry View replied to Mulberry View's topic in Party Wall & Property Legal Issues
For us, the output of an Expert Witness report will probably define our route, it's why we want someone with deep experience of Zinc roofing, we want the outcome to be unarguable, either way. If the report deems the roof to be as fundamentally defective as we believe it is, then we hope we can assess the probability of our case and begin talks with the contractor about a settlement without going to court. I'm going to talk to some Zinc installers today in the hope of finding someone who can be expertly impartial in the hope that they can be accepted by all parties as a joint expert witness. -
Expert Witness needed...
Mulberry View replied to Mulberry View's topic in Party Wall & Property Legal Issues
Thanks for your detailed @Gus Potter. The contractor has taken the view that the installed details are all compliant because the manufacturer has issued their 'material-only warranty', though they take NO responsibility for workmanship at all. Read into that what you will. The installer has literally NO interest in hearing my concerns and explaining his reasoning despite the issues I have raised. I'm going to DM you as you might be able to help me. -
Expert Witness needed...
Mulberry View replied to Mulberry View's topic in Party Wall & Property Legal Issues
Our contractor does not know the word 'compromise'. He is deaf and blind to any problems, he just wants his money. I know the implications of court, but I really do not see that we have a choice. I'm hoping that a proper expert report might help him to recognise that there are faults, then we can attempt to discuss some sort of settlement offer. We're £45k in, the contractor does not believe he is even 1% at fault, so the alternative is walking away and taking a £45k hit and he'll still pursue us for the remaining £10k. That would finish us and the project would probably have to be sold. -
Expert Witness needed...
Mulberry View replied to Mulberry View's topic in Party Wall & Property Legal Issues
That's certainly worth pursuing. The hard part is that our contractor is VERY well known in his industry and highly devious. -
Some of you know about the legal issue were dealing with at the moment, our defective Zinc Roof is preventing progress on our project and has been for almost a year now. We need an Expert Witness and finding one is proving difficult. Ideally, I want someone with a good understanding of metal roofing (Zinc particularly). Can anyone here suggest how we can solve this?