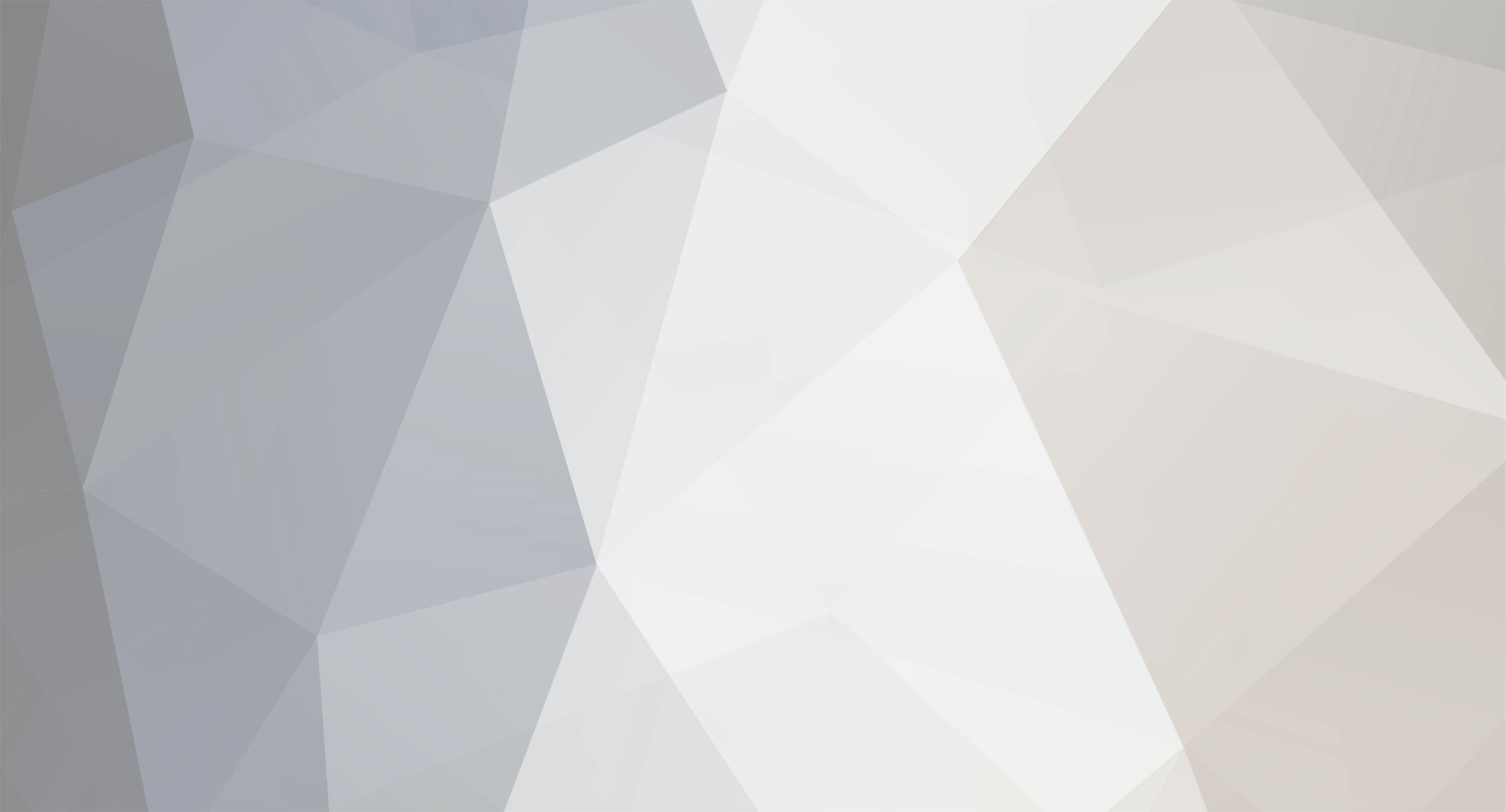
GP41
Members-
Posts
13 -
Joined
-
Last visited
Everything posted by GP41
-
Wild quotes and building regs for windows and doors
GP41 replied to GP41's topic in Windows & Glazing
OK, thanks. It wasn't so much the materials as the fitters. I was certainly left with the impression that being at the wrong end of the country wasn't great for them. To be honest though, I think we are going to have to discount that supplier anyway, just on cost grounds. -
Wild quotes and building regs for windows and doors
GP41 replied to GP41's topic in Windows & Glazing
OK, thanks - that was what I'd understood. I think Certass are the other one. I just found this on the website of another Internorm partner down in Shropshire, which backs this up. CERTASS - Spectrum Architectural Glazing Based on your figures, that makes my cheap S&F second quote sound very cheap. Quote 1: supply only £950/sqm, S&F £1250. Cheapest range Quote 2: S&F: £850/sqm. Best range! With inflation (not insignificant!), your supply only sounds comparable to my second cheaper supply & fit quote so my cheaper quote is really cheap, and my first, more expensive quote is really expensive! Distributors of the same kit in the same neck of the woods too. Bizarre. -
We've been looking at window and door options for a retrofit. We'd homed in on alu-clad timber Norrsken and Internorm but the prices were crazy high. We'd put this down to the long distance we are from the South Coast and the significant travel for Norrsken, and the generally high quotes people seem to get for Internorm. We've worked our way down the Internorm range, ending up, sadly, at uPVC. We were always having white anyway and from a performance perspective there doesn't seem to be much in it. We are also coastal and uPVC will probably fair better, so not all bad - I was just hoping to move away from uPVC. We've a couple of Internorm distributors close to us. Quotes from the first were heading up to £40k fitted for the cheapest of the range. Just by chance we decided to get a quote from the other local Internorm distributor and their fitted price (including delivery, access, lifting, etc.) for the top of the range was the same as the supply-only price for the cheapest option from the other distributor (~£850/sqm including a sliding door). This is making me nervous! The distributor in question has been around a while and seems credible but the price difference has knocked me off guard a bit. Is this just the craziness that is window pricing or does it seem strange - which price is the unusual one?? I'm also intrigued about building regs. As far as I can tell, neither distributor is registered under a competent persons scheme, with one of them saying they didn't see BR being an issue in our case and that they didn't need FENSA because they've had the required training from Internorm. Does being an accredited distributor give you the cover you need?
-
Retrospectively sealing cracks at 10+ year old plasterboard joins
GP41 replied to GP41's topic in Ventilation
That's really helpful thanks. Did you mean something like this for a flexible, airtight, paintable sealant? Acryrub SWS | Soudal -
Retrospectively sealing cracks at 10+ year old plasterboard joins
GP41 replied to GP41's topic in Ventilation
I managed to dig out some old photos and FLIR images. There are cold patches around the glulam but quite localised - presumably around where it was packed going into the wall, so that could be an opportunity for the drilled holes/expanding foam trick. In this room I don't think we suffer too badly with the plasterboard tent problems (as we do in a couple of others...) but there are certainly some problem areas - you can see there is an issue where the insulation in the ceiling meets the wallplate (I thought I had a better picture where I'd actually spotted the specific problem on this wall - I'll need to try to dig it out, but it was basically a flaw in how the insulation finished). -
Retrospectively sealing cracks at 10+ year old plasterboard joins
GP41 replied to GP41's topic in Ventilation
OK, many thanks, I'll see what I can find. It was more the corners where I was concerned, a lot of the crack repair advice seems to relate to simple hairline cracks in flat surfaces rather than inter-face joints like this that looked like they need a more significant solution that would stand the test of time and remain airtight. Thanks again -
Retrospectively sealing cracks at 10+ year old plasterboard joins
GP41 replied to GP41's topic in Ventilation
The ones in the pictures have never been touched, other than possibly some decorators caulk for first time pained. When you say "pull out all the dross and do it properly, either skim or do dry line properly, with tape and the correct fillers." do you mean take it all down? We do have the added challenge of trying to find a solution that cleanly abuts the glulam leaving its wooden appearance untouched. -
Retrospectively sealing cracks at 10+ year old plasterboard joins
GP41 replied to GP41's topic in Ventilation
On many of them it'll be first time. On some of those that are more accessible I've used decorators caulk or silirub. I expect I could remove that though if necessary. -
New member - stuck for what to do next to warm the house
GP41 replied to Sparrowhawk's topic in Introduce Yourself
Honestly, the parallels with where we are are amazing. Admittedly, I think you are starting with a bigger challenge, but the procrastination and perfectionism are real. The 3AM "how on earth can I get ducting through there" moments have been all too frequent - we're in the middle of backtracking from 'being sold' a solution involving rigid steel ducting run through a cold loft, told it will be ok to "just put it under the insulation" to now looking at a semi-rigid radial solution with ducting largely within the envelope. I'm currently walking into our living room several times a day to give it a good dose of deliberation as I try to work out how to install underfloor insulation to the suspended floor (how many times can I read the EBS guidance document), how to extend under the floorin the adjacent room that is covered in Amtico that we are not planning to remove, what to do with a false wall that contains an old pocket door that we know is a cause of unwanted airflow but that will be a massive disruption to remove. And in parallel with that and whilst waiting on the ASHP/MVHR pricing to come through, gluttons for punishment, we've started the process of getting window quotes. We've started with Norrsken, based on recommendations here and their commitment to taking end-to-end responsibility; after seeing your figure I'm thinking there's a lot we can do with our current uPVC 2G and a decent can of foam... And the arrival of MVHR is going to put pressure on progressing the airtightness work. It'll all be worth it though. 😊 -
Retrospectively sealing cracks at 10+ year old plasterboard joins
GP41 posted a topic in Ventilation
We are embarking on some "airtightening" work alongside installation of ASHP and MVHR - more background here. One of the things that I'm struggling with, is how best to deal with cracks in our relatively recent extension. Much of it was dot and dabbed and we have numerous cracks, either on the flat face of ceilings and walls, or at wall/ceiling - and sometimes plaster/glulam - junctions. I'm loathed to start pulling perfectly good plasterboard off walls, it just doesn't feel like the most sustainable thing to do. So how can I fill, and make airtight, those cracks? I have visions of taking the skim coat back, applying airtightness tape and reskimming - is that ridiculous? Would I be better with a caulk of some sort, and if so, how flexible and long lasting would that be? Here are some pictures of the sort of thing we are dealing with... From an airtightness perspective, I actually think our 12 year old extension is in a worse state than the original, wet plastered, 65 year old house. And in some cases, looking back at pictures I took during the build (I know, if I'd only known then what I know now...) I might be forced to remove sections of plasterboard to carry out remedial work behind plasterboard, in which case I have the opportunity to do a more substantial job. Any suggestions much appreciated? -
New member - stuck for what to do next to warm the house
GP41 replied to Sparrowhawk's topic in Introduce Yourself
@Sparrowhawk Great thread. I've just read through it, start to finish. It's certainly made me feel better about what we've taken on. Lots of great ideas. It looks like it's some time since you've posted. I do hope you were able to get to a better place - quite a challenge. -
Thanks for the welcome @Conor. I was just looking for longevity for the windows. I'd also just rather not use plastic - we've not had great experiences with uPVC and ideally, I don't want to be doing this again. Would aluclad plastic offer the same insulation as aluclad wood? The ground floor has three parts to it: - the original suspended floor that I would like to insulate the way I've seen in the ecological building systems way Suspended Timber Floor Insulation: From Above Installation Guide (Method 1) | Ecological Building Systems. - the original concrete floor (no insulation) - small area of original kitchen slab that we will probably have to live with. - new concrete floor that we have 100mm of celotex in (laid to regs back in 2012). There's also a section of boarded first floor that sits over the integral garage and I'm considering the ecological building systems 'from below' method so that I can seal the garage out of the house and insulate that floor at the same time. We've been considering various options for the floors, particularly because it currently makes it less sensible to fit UFH on top of, and that might have been a good match for the ASHP. However, we've a substantial area of the floor, including some of that suspended floor, covered in Amtico (laid on levelling compound on screwed down plywood) that will just be an expensive nightmare to lift, throw away and replace. I don't think there such a thing as a lift and relay of Amtico... So we are stuck here right now. I just don't know what the best option is. I've heard of people spraying insulation through some remote controlled device from underneath. The thought of sealing the underside of the floor that way fills me with a similar amount of dread as the thought of sprayfoaming the underside of the rafters in our loft and we know where that's got people! I'm also concerned about the radiator pipework that runs under there. It's going to be needing additional insulation as that void gets even colder. That's assuming it has to run under any underfloor insulation. Any ideas?
-
We are in the process of a not-too-deep retrofit and I'm really pleased to have stumbled across this forum through some of my recent internet searches. It looks like it's going to be a really valuable resource and somewhere to share our progress. So here's my intro - you'll need a cup of tea and a couple of bourbons. We have a 4-bed, 180sqm, 1960 detached house. It started off smaller than that and in 2010 when we moved in, we set about designing an extension. Completed that work in 2013 and have lived in it without so much as a drop of paint ever since. Just over a year ago, fuelled by an interest in houses that were appearing on Grand Designs that were basically existing passively in their environment with minimal carbon footprint, and keen to get to a place where we had taken full control of our home and its energy expenditure prior to retirement, we set about finding ways to improve. First off was reducing energy consumption and just being much more aware of what we use: a tired old dishwasher that I'd kept hobbling along with fixes and a past-its-best beer fridge in the garage went first, plus ensuring all lights were LED (apart from some stubborn under cupboard lights in the kitchen that we've still to find replacements for); also ensuring that, particularly older, devices were not left on standby. Replacing a broken washing machine also made us realise just how much more inefficient older appliances are. Some time ago we'd installed Honeywell Evohome TRVs on all our radiators. We were fed up with a central thermostat never getting things right. We'd either be downstairs all evening with it and go to bed in a cold upstairs, or sit overheating downstairs with the house cosy upstairs. Working from home a lot, I also always felt I was heating an entire house when I spent all day in one room. I know they are not everyone's cup of tea but it knocked 10% off our heating bills and has more than paid for itself now. I suspect as we move to a heat pump they'll become nothing more than a per-room temp sensor with the house heated more uniformly. Back in September 2022 we organised an assessment that included a door blower test. It highlighted a number of areas for improvement, in particular insulation, draughtproofing and windows & doors. Our air permeability figure was just under 7. We set about massively improving loft insulation to 3-400mm - including use of eaves ventilation to avoid issues up there. We made the loft hatch insulated and more airtight, and generally resolved quite a few draughty areas. Many of the windows and doors were in a poor state so we've temporarily draughtproofed them with foam tape until we replace them. We drew a line at any further draughproofing until we've put in proper ventilation (I know there's some chicken and egg here). I've bought a FLIR camera which has been amazing, both in terms of highlighting problem areas and in showing us how much improvement we've made as a result of a particular intervention. It has highlighted some things that we are probably just stuck with (e.g. that classic issue at the top of outer walls where the inner leaf of the cavity is exposed to the outside with no simple way of continuing insulation from wall to ceiling, or where RSJs up in the cold loft rest on the ceiling acting as thermal bridges). Finally, over a year ago, we installed a fairly substantial solar & battery system. 13.6kWp of PV on an east/west split with 27kWh of battery storage. This has been amazing. We overcooked the battery sizing (at the time you could only get the VAT off if installed at same time as PV, but that's since been dropped) but were futureproofing in readiness for further electrification of the house, in particular an induction hob and heat pump that will enable us to disconnect our gas meter. So where are we know? We're moving forward in several areas: We are in the process of designing an MVHR install. Had one false start working towards a design that involve significant rigid ducting in a loft space. We've backed out of this now and are close to settling on a revised approach using semi-flexible ducting in a radial configuration passing through voids within the thermal envelope. We are in the process of the spec/quote for a heat pump. We'd originally planned to do this for next winter but our 17 year old combi isn't behaving and I refuse to spend any more money fixing it. We're researching induction hobs that include downdraft recirculating extraction to appease the MVHR. We are getting quotes to replace windows. Windows in the front of the house are all over 17 years old, double glazed uPVC, badly fitted and poorly performing. In the back of the house, we've slightly updated uPVC, fitted just 12 years ago, but not fitted well. Whilst they still look really good, they are cold & draughty. We are looking to replace with alu-clad wooden triple glazing throughout. Sadly these are just one example of things that "if we'd known then what we know now" would have been a different product fitted properly for a small proportion of the cost of replacement now. From a performance perspective, the extension work is poor. Looking at some of the photos I took during the build, I can now see issues like badly fitted cavity batts, gappy, not taped, and in one or two places, sections missing - just makes me cringe. It would have taken a small amount of extra effort to have done it 'properly' at the time. As a result, I think the original 1960 build probably performs better in many ways, even whilst having a narrower cavity (filled with that pumped-in fluffy stuff but which according to our assessor still seems to be offering good coverage fourteen years on). We can resume work on airtightness soon. As well as getting properly fitted windows, key areas include: new seals on the Velux windows; work on the suspended ground floor (ideally without disturbing lots of Amtico flooring...), remedial work on a first floor room that is positioned above an integral garage, sealing first floor joist gaps and dealing with cracks in plasterboard joints. I'd love to know if there is a simple solution to this that doesn't involve ripping down entire walls of plasterboard. I could just fill them with a sealant but I don't know how long lasting that would be. I'd like to apply airtightness tape but that would mean taking back the skim coat of plaster, fitting the tape to the boards and reskimming - am I missing something? I'm considering further insulation options, both in terms of under the suspended floor but also walls. The cost of EWI seems prohibitive and I'm sure I've read that with cavities it can be ineffective and potentially damaging. We could just apply IWI to some 'problem walls'. I can see I'll be spending a lot of time searching threads in here. Overall, ideally I'd like to get us nearer to a permeability figure of 4 to increase the benefit of the MVHR. With all these things, the challenge seems to be the order in which to carry out this work with so many interdependencies and inevitably compromises to consider, alongside the usual considerations of cost and disruption vs benefit. Equally, I don't want to do things 'piecemeal' and find out there was a better way when looked at holistically. Finding a professional who is interested in that is difficult. Architects aren't interested because it's not a half a million pound fancy new build, individual trades are only interested in their specific field (understandably so) and from my brush with a seemingly very competent expert, they didn't seem particularly interested in 'joining it all together' or helping to devise a workable plan, just in charging on an hourly basis to answer questions you throw their way. So here I am, making my own way. I'll no doubt be along with some very specific questions but if anyone has any initial thoughts, I'm open to constructive criticism and suggestions! If you made it this far, thanks for reading!