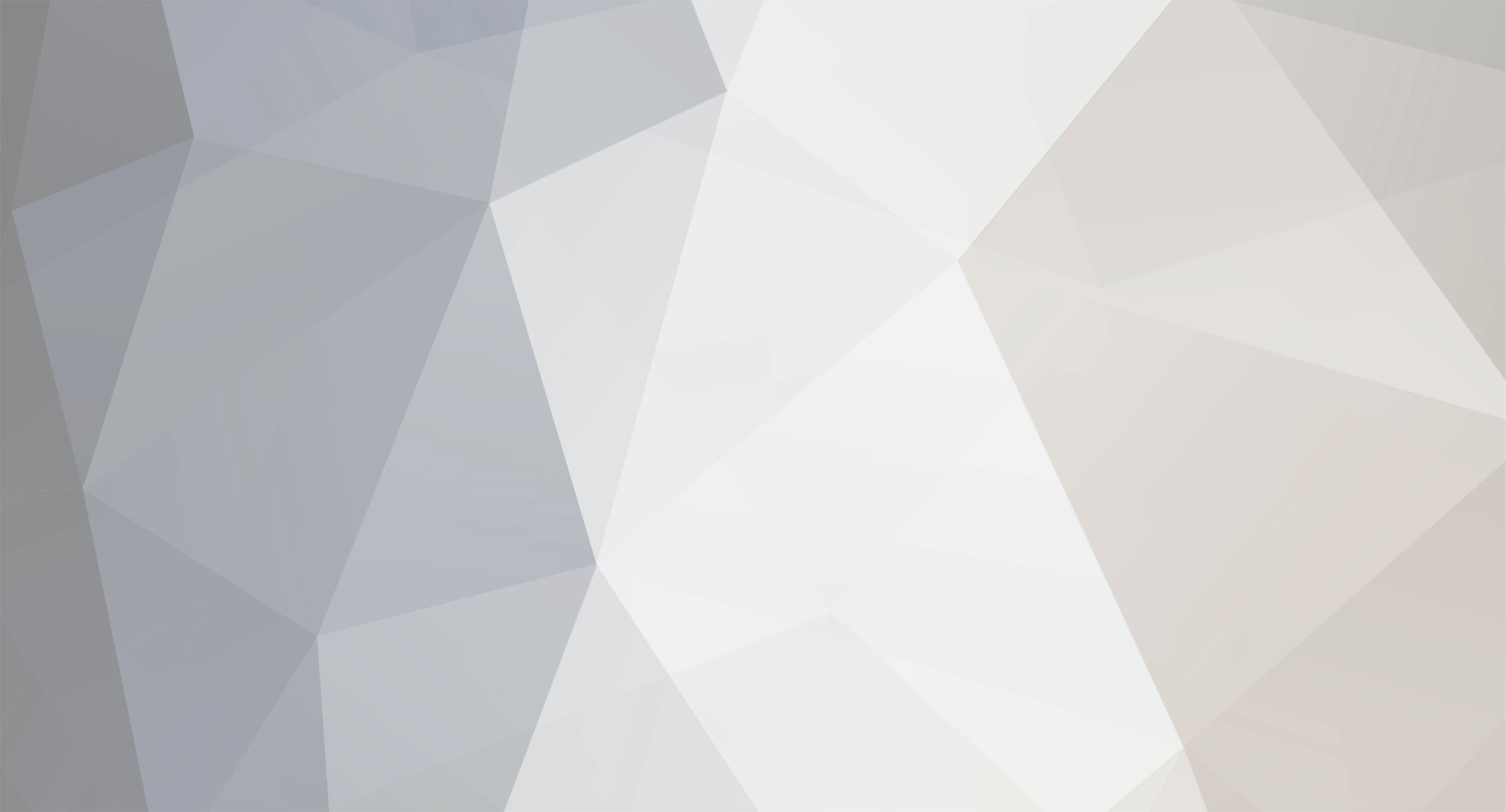
Hannah77
Members-
Posts
13 -
Joined
-
Last visited
Personal Information
-
Location
Glasgow
Recent Profile Visitors
The recent visitors block is disabled and is not being shown to other users.
Hannah77's Achievements

Member (3/5)
4
Reputation
-
De-rating cables within insulation. Best route?
Hannah77 replied to Hannah77's topic in Electrics - Other
Pretty please! 😠-
Hi, I am running the lighting and ring circuits between external studs. The holes need to be positioned in the middle of the stud depth. I am installing insulation batts in the full depth of the stud so in theory the cables will be in the middle of 140mm insulation. If I routed the cable to the rear of the stud between each hole I would increase the length of wiring but then they would be only covered by insulation on one side and next to a ventilated cavity. The build up on the outside of the stud is 11mm OSB, membrane, studs and render board. Has anyone got any advise on experince with a similar set up? Not sure about how to work out de-rating.
-
Solar PV, combi boiler and wood stove with a back boiler?
Hannah77 replied to Hannah77's topic in Photovoltaics (PV)
My combi won't take heated water. I had been advised that you could feed the thermal store with hot water from the combi when needed intsead of having an immersion for when PV not supplying enough? -
Solar PV, combi boiler and wood stove with a back boiler?
Hannah77 replied to Hannah77's topic in Photovoltaics (PV)
The south facing roof is about 3m x 10m so that less the 3 velux. Don't know what that equates to. Fire risks? -
Hi I am building an extension and want to put solar PV on the roof, with a battery and water storage tank. I want to use bthe solar to heat water in a storage tank and then direct power to a battery. I also want to use a wood stove with a back boiler to heat water in the tank. I have a combi boiler at the moment with capacity for the whole house. Installing under a wet floor heating system in the ground floor of the extension. Is there a way to integrate this system so that the combi boiler backs up the hot water system when there is not enough electricity generation from the solar PV or hot water from the stove? Are there companies that can provide a design for this kind of intergrated system? Thanks Hannah
-
Someone told me that these fix to the timber kit. Ot at least they do for render board so it might be similar to timber cladding?
-
Thanks @Mr Punter The membrane requires vertical battens first to allow for moisture to drain down face.
-
Hi, New to building timber frames! I am installing load bearing walls over several stories. The c/c of the studs are 400mm at ground level and increase to 600mm c/c for the floor above as the loads decrease. However the cladding system is render board on battens and counter battens. The render board system and the breather membrane both need battens at 400mm c/c. This means that they can fix vertically to the external wall at ground directly into the studs. But at 1st floor they will only align every second stud with two battens in between missing the studs entirely. The wall build up is just 9mm OSB on the outside face for racking. What do you do for the 600mm c/c studs? The battens need to be fixed back to studs and not OSB as the fixing strength will be insufficient for the wind loads and self weight of the cladding. Cheers Hannah
-
Distance between fixtures? Maximum window size?
Hannah77 replied to Weaf's topic in New House & Self Build Design
If you don't want to comply with the spacing between the window and doors as posted by @DevilDamo above you would need to introduce a wind post. You would need to get your structural engineer to spec that and include it as part of your building warrant application. Porches are typically classed as permitted developments so long as they don't exceed any of the required criteria. If you do have planning and want to change the window or door size then you (or your architect) may be able to submit that as a non-material variation assuming the changes aren't critical. Also need to consider lintel type and minimum bearing required. If you are going for separate lintels for the door and window minimim bearing of a robelsee type precast lintel is usually 150mm. So you would need 300mm between the window and door. You could get a larger capacity lintel and span the full distance between the window and door. Assuming you are rendering. Pretty sure Catnic style lintels for ifyou are using facing brick have a similar bearing requirement. -
Hey all I have finished the raft slab, underbuild and steel frame. About to start the joinery which is where I suspect I will need to ask questions! I had to get a build over permit from Scottish Water so if anyone has any similar issues with drainage assets within build footprint I can offer some advise or info on how my appeal process went (also a civil and structural engineer which helped!). It took a year but I got approval in the end. Doing all the work myself with the help of family and friends. Some pictures of progress to date. Taken a year to get this far from first breaking ground. A lot of digging, some type 1 compaction, even more rebar tying and a couple of massive concrete pours later! Then 3 days of craziness and a fun using a 12m tellhandler to install the steel frame here I am.... awaiting delivery of timber. Suddenly it all seems real and definitely past the point of no return. The extension includes changes to the exitsing which I have been doing as I go. New stairs into loft and loft conversion. Removed some walls and moved the back door. There will be 3 slappings through the existing gable wall into the extension, one at each level. Can't say I am looking forward to doing those. Looking forward to being part of the community. Cheers Hannah