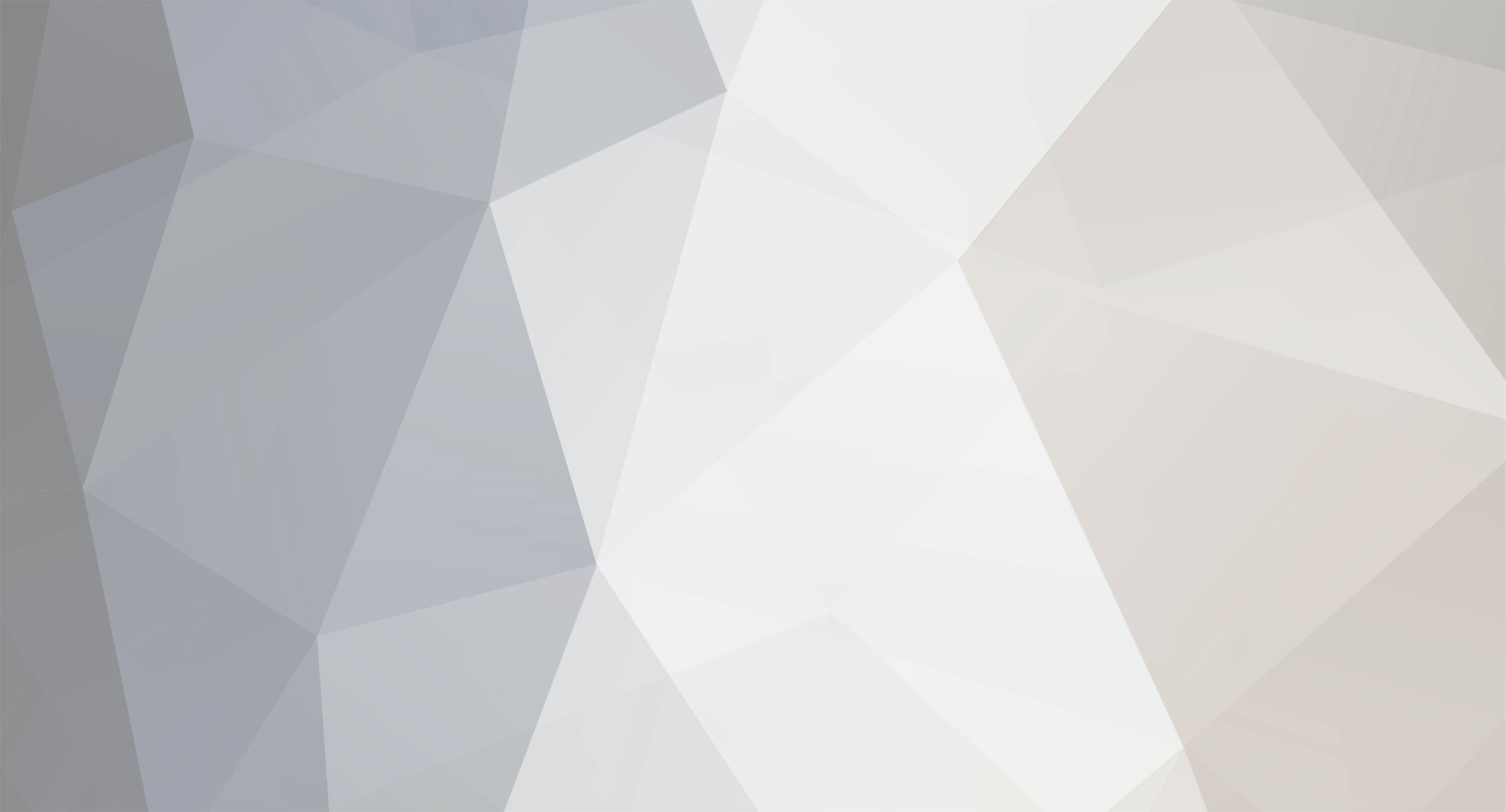
beenthere
Members-
Posts
5 -
Joined
-
Last visited
Personal Information
-
Location
Ireland
Recent Profile Visitors
The recent visitors block is disabled and is not being shown to other users.
beenthere's Achievements

New Member (2/5)
2
Reputation
-
Scandinavian timber windows - durability of recent product?
beenthere replied to beenthere's topic in Windows & Glazing
To reduce the topic to specifics. Some of the Scandinavian window makers seem to have backed away from the traditional double vacuum impregnation of slow growth pine heartwood to e.g. use of some heartwood on external surfaces (potentially a tiny amount overall), and flow coating/surface application of preservatives. Which may deliver durable timber, but could amount to an increased dependence on the paint film remaining intact, and a reduction of water resistence/stability and an increased tendency to stain and rot. i.e. be mostly be about cost reduction. Judging by the restrictive fine print and warranty conditions they're certainly not betting the farm on timber from the new (and presumably unproven) processes being bulletproof. Nordan for example still seem to use the more traditional approach. I'm wondering does this (and the possibility that it delivers more durable timber) account for the latter company's success in Scotland, or whether anybody has any standards, industry or real world based views on how the two processes compare? -
Scandinavian timber windows - durability of recent product?
beenthere replied to beenthere's topic in Windows & Glazing
Ta guys. We've looked at Rationel Dave, and at others in a similar space. Having somebody fit supply only windows is possible, but supply and fit is more the norm in this market for replacements. Unlike possibly in the UK where the opposite (?) may be the case. It's possibly that way because finding a trained and capable installer of scandinavian windows (bearing in mind that with timber windows correct installation is a huge factor in determining longevity) who will reliably work to supplier specs is likely to be a bit of a crap shoot here. Price isn't so much the issue for us either (there's competitive quotes about) - it's more that at 60 years of age we don't want to find ourselves with rotting windows in 20 years. Agree 100% that trust/reliability of the supplier and product is the point Barney - the aim is to get it done right first time as diving for the paperwork is indeed futile. It's a given that the fine print is going to be one sided, and there's probably even reasons why it needs to be so. e.g. people playing silly buggers over a final stage payment. With that in mind the core issue my original post tried to prompt some discussion on is that most of the mainstream 'scandinavian' suppliers seem recently to have deserted the double vacuum impreganted pine heartwood route in favour of flow coatings (reputedly much less penetrating) and witches brews mixing heart and other cuts of wood. One fine print I have commits only to using 'scandinavian softwood' - which theoretically could be any old mush. These presumably cost reduction driven moves may well be fine, but it's tough to establish what is likely to be delivered in practice by way of durability of the resulting timber. If nothing else it's very new, so historical data won't mean much. 80 years per brochure claims (the fine print anyway excludes brochure claims from forming a part of any contract) is a big ask. BS EN 8417 (good data or not - it claims to be based primarily on test data and experience) reportedly says that exterior window joinery (use/hazard class 3) for a 60 year service life requires at minimum timber classified as durable (class 2) in BS EN 350-1. e.g. http://www.timberinconstruction.co.uk/features/different-class The trouble with this is that the various pines (even top quality slow growth heartwood) seem to range from class 4 (slightly durable) to class 3 (moderately durable) - so highly effective impreganation or at least preservative application processes seems to be essential to get whatever is being used now up to class 2 and the claimed 60 never mind 80 years service life. The Danish makers as above claim compliance with DVC (Danish Window Control) standards, but I can't find a way to cross reference them to the BS/EN wood durability classes which at least are European/international. I mentioned Nordan because they are an option, and seem still to use the proven double vacuum impregnated pine heartwood - wondering if anybody has hands on experience with them? -
Hi all, new here and just posted an introduction. Pardon the length for a first - but it may be of interest to some. We're shaping up to buy new replacement aluclad Scandinavian pattern timber windows for our 1980s brick cavity wall self build, and finding it much less straightforward than expected. The position may be somewhat different in the UK (we're in Ireland) but we're running into two issues: 1. Highly aggressive terms and conditions, and despite the usual noises in the sales material miles of blatantly one-sided fine print. (especially from the well known large Danish guys). HIgh end pricing and premium billing doesn't seem to deliver much that's customer friendly in this regard. Payment in full is demanded before installation with no mention of standards for this work (the window companies tend to do it themselves here), the warranty is very highly constrained (12m on finishes, 3yrs on hardware, 6 yrs on the structure; 'natural' processes like knots weeping and presumably warping and/or splitting in the wood are excluded, lots of fine print about maintenance requirements), it doesn't matter what you agree with the sales guy or what’s in the brochure - it's what's in the quote that determines their specs, deliverables etc. None of this would matter terribly given a reliable product, and rock solid installation work, but…. 2. Uncertainty about likely window longevity. We may be overly cautious, and the Danish brochures in question claim very long lives (80 years in one case) with correct maintenance - but the documentation is decidedly weak on technical specification or standards information, and the fine print seems to really only commit to use of Scandinavian ‘softwood', flow coating with preservatives and water based finishes. Suggested specifiers wordings are notably toothless. The previously more or less traditional/gold standard selling points of laminated slow growth Baltic pine heartwood of specified max growth ring spacing/density, and double vacuum impregation seem to have gone by the board in their cases. (these days it's all about environmental sustainability etc. which is excellent, but what about basic functionality and longevity?) Much is made of compliance with DVC (Danish Window Control - an industry body/regulator run out of one of the technical colleges there) technical and other standards, but it’s proving hard to dig up what this means in practical and specific technical terms - and how it relates to BS 8417 window durability/life ratings. My superficial understanding is that the British Standard (anybody around with a better understanding?) at minimum requires joinery for external use (hazard/use class 3, actually 3.1 if painted - which reportedly delivers at best a 30 year life) to be from at minimum timber of durability class 3 (moderately durable). Class 2 timber (durable - and I can’t find any species of redwood/pine with this rating, even for heartwood) is reportedly required to achieve a 60 yr life. The problem is that the various pine species seem to be at best class 3 (moderately durable = heartwood of the better species), but often class 4 (slightly durable) - while the sapwood (which it seems may be be used also - if only laminated behind the heartwood) is regarded as class 5. (not durable) This suggests that highly effective and deeply penetrating (the traditional double vacuum?) preservative treatment is essential to achieve 60 year durability with even top quality pine heartwood. Trouble is it’s not by any means clear whether or not the recently adopted flow coating does that sort of job. Especially not if lesser grades of wood are mixed in. Minimisation of moisture take up to minimise movement with changes in moisture content is also a serious consideration - impregnation can it seems greatly improve stability in this regard. Then there's the question of water based coatings. There’s an industry funded body called the Wood Window Alliance that has published research into wood window longevity in the UK that suggests 30 yrs plus before maintenance for aluclad windows, but research into experience with long installed windows isn’t of much use where very recently adopted practices are concerned. Plus it's generic, and not maker specific. It’s clear that there’s been all sorts of moves recently in play to reduce the cost of the wood (mixing heart and other woods?), and to reduce manufacturing costs. (like avoidance of vacuum impregnation) The question is whether or not those using these techniques (which may well be fine, but might also seem reminiscent of how the supermarkets still tick the boxes on selling points while stripping the good out of food products) are delivering their claimed durability. The terms and conditions (see above) suggest that some of the makers may be taking no chances - may not be putting their money where their mouths are. This might seem picky, but the prospect (if this was to turn out to be a possibility) of trying to deal with rotting windows at age 80 doesn’t appeal. Never mind that claiming on warranty (at any point) sounds very much like tilting at windmills... 3. Different makers, different specs? One stand out maker may be NorDan. They seem popular in the wet and windy highlands and Isles of Scotland (could be down to effective local marketing rather than real advantages though), and there are signs that they may still use the more traditional laminated pine heartwood and vacuum impregantion construction method. Anybody with experience of and fimiliarity with Nordan? Strengths and weaknesses? Thoughts on the other topics above, especially on how the Danish DSV standard cross references to BS window durabilities? All help and input appreciated. Thanks
-
I'm new, but we have just finished installing 2mm aluminium fascia over the existing timber, and Marley Alutec extruded aluminium guttering. All powder coated in black. The job has turned out really well. The thicker aluminium makes such a difference to the look and feel of the whole deal. It was expensive, but should be a long term/rest of life solution. The site is not exposed, and there's no salt about - we have powder coated aluminium windows installed in the early 80s the finish on which is still spot on. (other than a slight matting in places) One to be careful of is the quality of the powder coating. The BS standard for architectural aluminium (or the Qualicoat process) requires the normal multi step degrease/wash/acid etch/wash/passivate/wash/powwer coat/bake process - and a decently thick >60 micron powder coating. There's been a rash of problems here (Ireland) where budget suppliers have been buying mill finish aluminium from suppliers and having it powder coated locally. They throw the powder on without the prep steps, and it often falls off a couple of years later leaving the customer high and dry...
-
Hi all from Ireland. (south of Dublin) We're struggling to bottom some issues in respect of a replacement window purchase, and will post a few questions on that topic under the windows heading. We're in self build terms at the other end of the project compared to most here. We went with a fairly large 2,000+ sq ft contemporary style brick brick bungalow on its own site back in the early 1980s, and only got finished about 17 years ago. (the main living room functioned as a store for years and years, the bathroom was jury rigged) Which seems to be about par for the course. (the lottery win never materialised) We're now into a 34 yrs later round of refurbishment - gutters, windows, better quality paving, landscaping etc. Luckily we got finished just before the bubble got going - building with direct labour was hard enough when guys were hungry for business, but must be doubly difficult now. It's turned out very well, but been a long road. The single most basic lessons it feels worth communicating are: (1) Don't borrow heavily/get into debt unless there's a clear and highly reliable way out before very long. It's tempting, and hard to wait for the money to come in - but it feels good (despite problems with illness and inability to work for long periods - we wouldn't have made it if we had taken on heavy borrowings) to have it all paid off. (just figure out how much you pay back versus the sum borrowed on a mortgage over 20 years) (2) What you do do right - wait/save until you can. Craft and broader contruction industry standards have slipped badly here (the bubble brought many untrained into construction focused only on easy money), and corner cutting on material and other specs by suppliers and trades is the norm. Training is minimal. It's really important to gain an understanding of the underlying technical issues, and to then apply these in speccing work and selecting materials hardware. Then to doubly and triply vet labour for the required skills - and the right attitude. keep on asking questions and looks at sample work/references. We went for good spec stuff, and systems which sounded way out here back in the 80s - but it's really paid off. Stuff like high levels of insulation, a zoned dual fuel heating system, masonry internal walls (the high heat storage capacity stabilises room temperatures), good quality roofing materials, tanking the bathrooms, good timber floors and tiles etc. We had hassle in one or two places where we cheap skated (like using concrete paving slabs and cheaper guttering) - but luckily nothing not relatively easily replaced. Good luck with all of your projects...
-
- 1
-