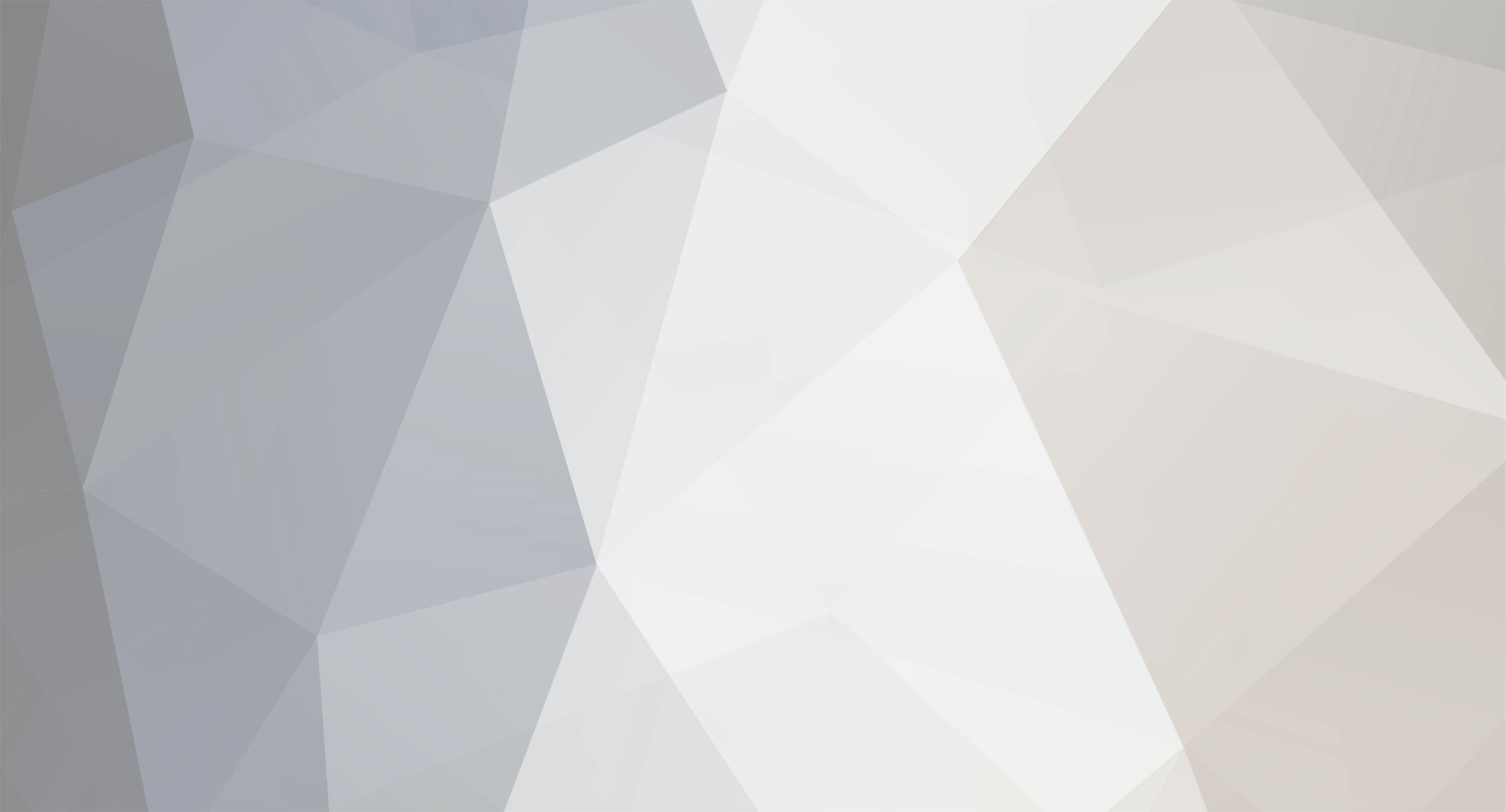
TimL
Members-
Posts
8 -
Joined
-
Last visited
Personal Information
-
Location
Greater Manchester
Recent Profile Visitors
The recent visitors block is disabled and is not being shown to other users.
TimL's Achievements

New Member (2/5)
1
Reputation
-
Reinforcing a 1st floor timber floor by adding additional joists
TimL replied to TimL's topic in Floor Structures
Thanks for the suggestion. I think our first preference would be to take the joist centres down to 300mm as this would also allow us to use a slightly thinner (and marginally lighter) subfloor, but this sounds like a reasonable alternative that we might end up using.- 13 replies
-
- floor joists
- joist hangers
-
(and 1 more)
Tagged with:
-
Reinforcing a 1st floor timber floor by adding additional joists
TimL replied to TimL's topic in Floor Structures
Do you mean to support the trimmers on hangers to be attached to the existing joists?- 13 replies
-
- floor joists
- joist hangers
-
(and 1 more)
Tagged with:
-
Reinforcing a 1st floor timber floor by adding additional joists
TimL replied to TimL's topic in Floor Structures
That's what we were hoping but the SE mentioned it would be necessary for us given the additional dead load of the upgraded stud walls and acoustic subfloor, let alone the UFH system. They also seemed to suggest that 600mm centres for C16 joists was apparently on the high end and somewhat uncommon though I'm not sure about that. We were considering the first option you suggested but given (based on a hole left in the wall from a previous owner) the external walls are hollow concrete blockwork, we're not sure whether you can get a reliable fixing into the hollow blockwork. I've seen mentions of resin based fixings but haven't found much detail on it.- 13 replies
-
- floor joists
- joist hangers
-
(and 1 more)
Tagged with:
-
Reinforcing a 1st floor timber floor by adding additional joists
TimL replied to TimL's topic in Floor Structures
Yep, full renovation. We're going after the EnerPHit retrofit standard which has a target airtightness of 1 air change per hour. Almost all the ceilings are down except for in the living room, though that's coming down too so we can seal the bottom edge of the joists that are against the party wall and external wall with airtight tape. Upstairs only has the chipboard subfloor left but that will be removed to be replaced with the floating acoustic subfloor. Planning on doing a full rewire when it comes to reinforcing as the wires going through all the joists will naturally need to come out. Radiator plumbing is all being removed as we're planning on using an overlay UFH system upstairs, the remaining plumbing we are planning on refreshing whilst we're at it. It will indeed be a very awkward job.- 13 replies
-
- floor joists
- joist hangers
-
(and 1 more)
Tagged with:
-
For the first stage we're putting in 30mm Kingspan TF70 under our floors and struggling to find someone who will do specifically party wall insulation (as opposed to cavity wall insulation which we already have). Later on when we've saved enough to afford it, we plan on putting in EWI, installing Passivhaus windows and doors and insulating the rafters to expand the thermal envelope to include the loft space. We're not sure how our local planning inspectors might feel about brick slip render on EWI since we're nowhere near that stage yet - our Passivhaus architect seemed to think this would do. I wouldn't fancy losing so much internal floor space to internal wall insulation, which I imagine is the only other way you can reach EnerPHit levels. Didn't realise what journey it would be preparing the floor for insulation. Chiselled up about 45mm of screed by hand (so the new floor level wouldn't be so high we couldn't open the doors), filled a gas pipe channel under that screed with concrete (after disconnecting the gas) and we're currently pouring a few hundred kilos of self levelling compound to try and achieve the 5mm over 3m levelness specified by Kingspan.
-
I've come across House Planning Help somewhere before and I think I subscribed to their mailing list. Though those emails got buried amongst a mountain of other stuff so I had forgotten about it. Thanks for the suggestion, I'll check it out.
-
Hello all, Our current 1st floor consists of 40x210mm joists (unstamped but assumed to be C16) spaced at nominally 600mm centres. Based on the increased dead load from removing the old paramount partitions, replacing with 38x89mm CLS studwork with some acoustic insulation, replacing the chipboard subfloor with this floating acoustic subfloor and adding an overlay underfloor heating system, a structural engineer has recommended reinforcing the floor by adding additional joists in between the existing joists by building into the external walls to bring the nominal spacing down to 300mm centres. What would be the best way of installing these new joists? The existing joists are either built into the external walls or rest on masonry joist hangers on the party wall. I was initially considering raking out the mortar joints, filling with fresh mortar with a mortar gun and installing masonry joist hangers to match the existing joist hangers but a civil engineer work colleague recommended against this. He was uneasy about there not being adequate compression of the mortar if retrofit this way. I really want to avoid building these new joists into the wall as I doubt I would be able to cut the holes at the right height and size without making a mess of it and I expect it would take a really long time. I wouldn't want to do this to the party wall anyway as it would compromise the acoustic performance of the party wall. The other solution I'm considering (pictured below) is installing ledger boards between the existing joists and installing joist hangers off those, but I'm not sure if that would be a good idea since the external walls consist of hollow concrete blockwork. From my online searches I can only seem to find American examples of fixing ledger boards to cinder blocks to build outdoor decking. Does anyone have any views on this?
- 13 replies
-
- floor joists
- joist hangers
-
(and 1 more)
Tagged with:
-
Hello all, I'm a chemical engineer working in the sustainable energy industry (who right now wishes he was a structural/civil engineer) and I'm just over one year into an EnerPHit retrofit of a three bed end terrace. I'm passionate about sustainable housing and sustainable urban design. Currently in the middle of levelling a concrete ground floor and working out how to reinforce a timber first floor of a house that has been stripped virtually back to brick. This is my first time joining a forum of any kind and I look forward to hearing advice from the community! 😃