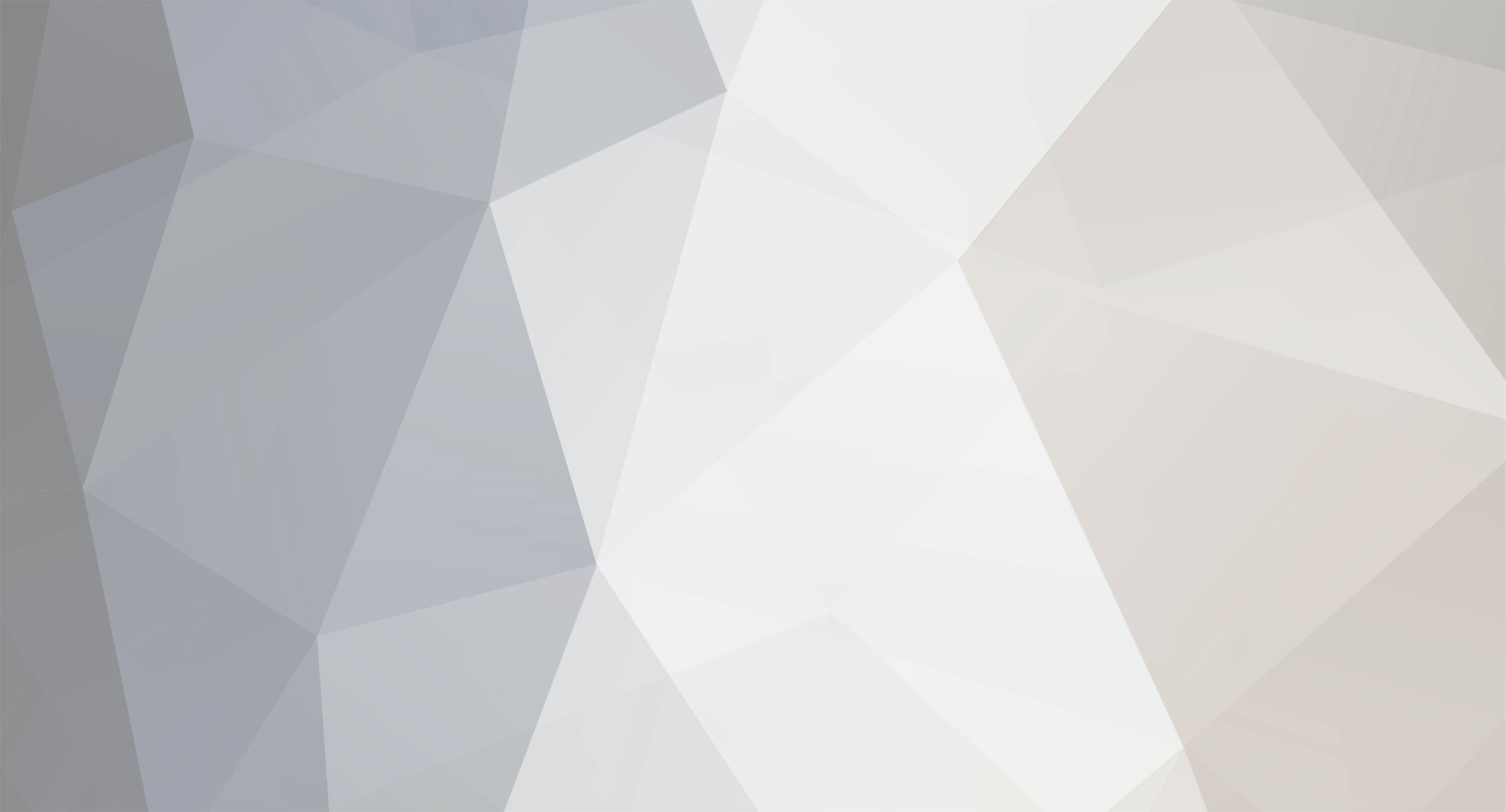
Clark Kent
Members-
Posts
22 -
Joined
-
Last visited
Personal Information
-
Location
Kent
Recent Profile Visitors
The recent visitors block is disabled and is not being shown to other users.
Clark Kent's Achievements

Member (3/5)
0
Reputation
-
it's pretty hard to see as the scale is quite small but I do have a 25mm PIR up-stand at the edge of the screed. I Guess I could bring the 50mm EPS/PIR up to/slightly higher than the sole plate. I haven't had any design drawings back from SIPCO yet but their standards don't show anything to insulate sole plates. I did wonder how these work in reality, you have a nicely insulated SIP panel just nailed to a pice of timber which is fixed to an existing outer wall. Even if you we're building an entire new build out of SIP's you would have lots of similar details like this at corner junctions and window reveals etc so I didn't think the sole plate would be a massive cold bridge. In fact, do I really need to use a Marmox block?!?
-
@Redbeard thanks for replying. There's 50mm EPS/PIR up to the Marmox black. It's un-dimensioned currently though
-
Hi Would be grateful for any feedback on these details. It's for my own extension, first time doing building detailing etc so if there are any schoolboy errors please let me know. The build is for a SIPS extension, I know it's probably very light but the proximity of neighbours tree means I've had to go deeper than standard. I've attempted to design out any thermal bridges, hence the use of a Marmox Thermoblock....hopefully this will mitigate any danger of condensation on the sole plate that I've read about. Thanks for the help in advance!
-
Solid Wood v UPVC/Composite exterior door
Clark Kent replied to Clark Kent's topic in Doors & Door Frames
I get that, I guess the point I was making is why ignore the U value of a door but not windows. So is the insulation internal? If so I assume it’s custom made. I haven’t actually searched but I didn’t think wood was a terrible insulator, they seem to use it on windows frequently. -
Sorry if I’m going over old ground, I did do a search but didn’t come up with anything conclusive so…. I’m looking to replace the street door, my wife particularly likes the doors by a company called Gileta who do some very nice designs with triple glazed stained glass. I must admit I haven’t seen a composite as attractive without paying a small fortune. The question is, will a solid wood door & frame be much much worse/colder than a composite one (providing it’s all well sealed and draught free)?. I did read a post where someone was suggesting that its such a small percentage of the exterior wall that U value isn’t important as long as it was draught free, if this is the case though then why bother with triple glazed windows? We’re looking to have a door with a window either side to maximise light as the passage is quite dark. I’m planning on making everything in the renovation as efficient as possible whilst working to a budget.
-
Thank you for the feedback @Onoff & @Iceverge, I’ve done a bit of research and am thinking of using insulated plasterboard to negate the cold bridge from the existing external wall into the new extension (Blue line on plan). Also regarding the existing house, when replacing the windows I was going to add cavity closers and insulated plasterboard for the internal reveals as per @Onoff suggested. I’m also thinking I need to do something on the ground floor where the rear extension interfaces the existing building. I’m not a huge fan of the standard detail supplied by the SIPs company for interfacing/connecting to an existing wall. It’s just a timber baton/sole plate with a DPM that the sip panel is screwed to. It’s an obviously a cold bridge. Although I guess it’s not in their remit to detail this kind of thing out.
-
@Iceverge thanks for the feedback. I’d be most interested in hearing solutions to the thermal bridge problems, or even just explain to me where they are (I’m assuming the junction between existing wall and SIPs panel for a start). I’m not gong for passive standards…probably nowhere near tbh. But, I would like to make it as efficient as possible and potentially get the bills down (or just stop them going up!) The detailing and extra work I’m doing on the drawings will hopefully mitigate some of these problems. Maybe the SIP supplier will advise? Although I rather suspect they will be more interested in banging it out as quick as possible. As for wrapping the whole house…I’d consider it but the local authority wouldn’t. It was an ache in the balls getting permission for the extensions let alone changing the appearance of the house.
-
No not yet, these drawings were submitted to the SIP supplier and they produce all the relevant building control drawings.
-
I have some drawings, still a work in progress whilst I try to iron out details/decide which way to go… I have known the builder since uni so he’s a very old friend. Which is why I’m not just dismissing his pessimism out of hand, had lots of people warn me off of ASHP but none ever had any real world experience….one even went on to have one fitted himself, by his plumber whom I’m sure probably over-specced as they generally do with a combi
-
@Iceverge Cheers for the link, was most interesting. Discussed it with my builder and he was less convinced, he’s also adamant that a heat pump is the wrong way to go though.
-
Yes it probably would, that’s something I shall do as I’d like to go down that route in the future maybe.
-
How do you lose the thickness of the IWI after 400mm? MHVR is something I have looked at and would really like to do but currently the budget wouldn’t stretch that far.
-
Thanks for linking, I’ll have a good read….
-
The wall construction is brick-cavity-brick. The cavity has been retro filled in the past with what appears to be blown mineral wool fibres, there is also a DPC. I don’t really fancy cladding internal walls as well.
-
I like this idea….definitely more viable than taking the whole floor slab out